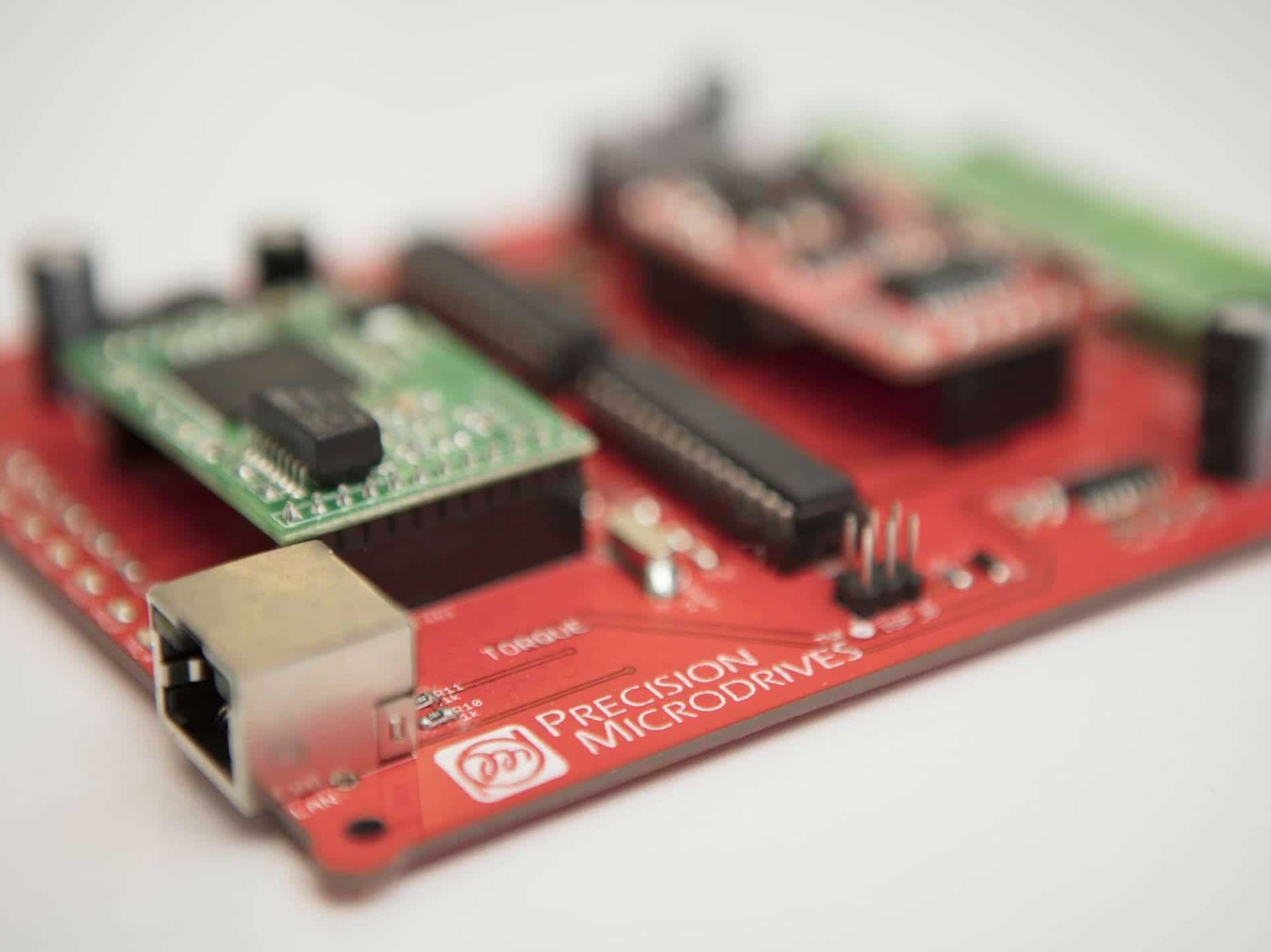
Technical resources
Articles, news and design guides
This resources section is where you can find product application notes, technical videos, design guides, news and case studies.
Search resources
Motor catalogue
Looking for our products?
Reliable, cost-effective miniature mechanisms and motors that meet your application demands.
PRECISION MICRODRIVES POSTS
Featured resources
Application notes
- AB-005: Electromagnetic Compatibility For Vibe Motors
- AB-006: Mechanical Mounting For Vibration Motors To PCBs
- AB-008: Vibration Motor Best Practices From Mobile / Cell Phones
- AB-007: Mechanical Mounting For Vibration Motors To Bulkheads
- AB-011: Electrical Techniques For Using Different Power Sources
- AB-010 : Mounting Vibration Motors To Flexible Materials & Clothing
Case studies
Technical posts
- Haptic Feedback Applications With Vibration Motors
- PCB Mounted Vibration Motors
- VAB-03: How Do LRAs Work?
- Vibration Alerting Applications
- Spur Versus Planetary (Epicyclic) Gear Types
- Positioning Actuators With DC Gearmotors
- Medical Applications With Vibration Motors
- Medical Applications For DC Gearmotors
Application notes
Case studies
Technical videos
-
VAB-02: How Do Vibration Motors Work?
This VAB introduces how ERM vibration motors work, including how they create vibrations and what determines the vibration frequency and
View Post
-
VAB-03: How Do LRAs Work?
In addition to covering the basics, we point out some of the advantages that LRAs have over their ERM counterparts
View Post
-
VAB-01: Introductory Gear Equations
The video below is based on Application Bulletin 024: Introductory Gear Equations. It covers the basics of meshed gears, including
View Post
Newsletter
Sign up to receive new blogs, case studies and resources – directly to your inbox.
