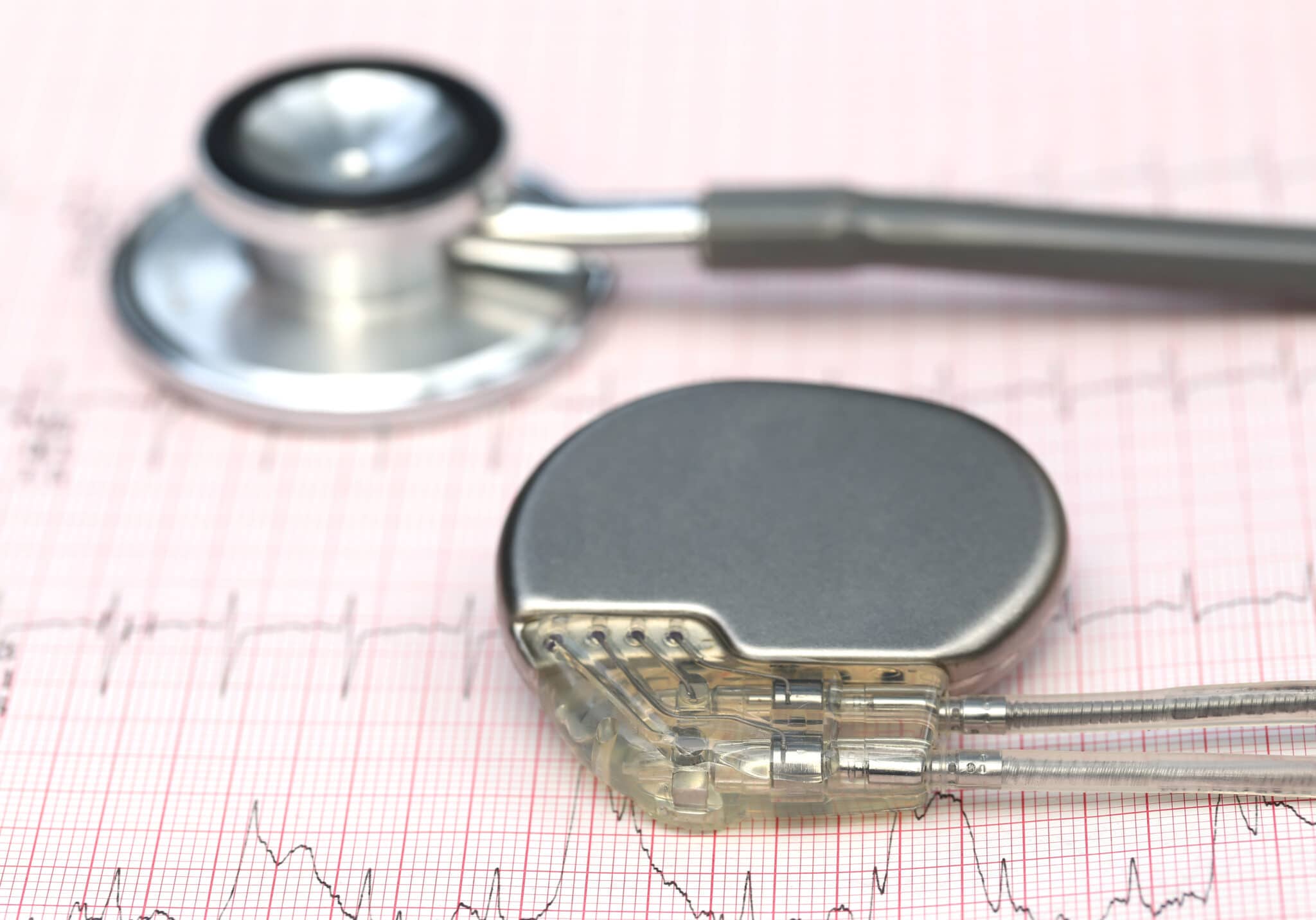
Case study
Surgically implanted pacemaker motor
- Vibration alerting for surgically implanted pacemaker.
- Ultra-reliable brushless Vibration Motor.
- FDA Class III implanted device.
Challenge
- Our customer, a large medical devices company in the US, received an end of life notification from their Japanese motor vendor.
- They had struggled to find a replacement part and were rapidly running out of time. They were very keen to minimise redesign and FDA re-submission.
- They wanted a Western partner to ease communication and who was experienced in managing the complexities of manufacturing parts for a medical implant device.
- FDA Class III required us to test, validate and certify a part for medical use that was not designed for that application.
Solution
- We took an existing brushless coin motor design and upgraded almost every sub-component.
- We also adapted the motor to contain three driving voice coils instead to two – an unusual improvement. This solved a longstanding motor starting problem experienced with the old motor.
- We built 2 custom fully-automated characterisation machines which perform an initial burn-in and then tested performance of each motor.
- The final part was similar enough to the obsolete part that only a limited FDA submission was required, expediting it’s adoption.
Results
- Our motors were left running continuously on a longevity testing machine for over a year with minimal reduction in performance.
- We prevented the customer experiencing a serious production line stop.
- The customer received a large amount of validation and testing data. In doing so we were able to spot an error that the customer themselves were doing on inbound quality control inspection.
- We went above and beyond to make sure that the parts were as reliable as could be, and they remain in use around the world today.
Project scope
Brushless vibration motor within a FDA Class III implanted medical pacemaker device
In this project our customer came to us after receiving an unexpected and abrupt end-of-life notification from a very well regarded Japense motor manufacturer. Finding a replacement on the open market was very difficult.
They engaged us to design a replacement motor that would avoid redesigns and the amount of work to re-ceritfy the device with the FDA.
The specifications were extremely difficult to fulfil, and the testing and validation requirements were significant, as were the ongoing quality checks and documentation.
We developed and manufactured a suitable motor quickly enough to prevent the customer from experiencing a production stop, and this component is found in pacemakers around the world today.
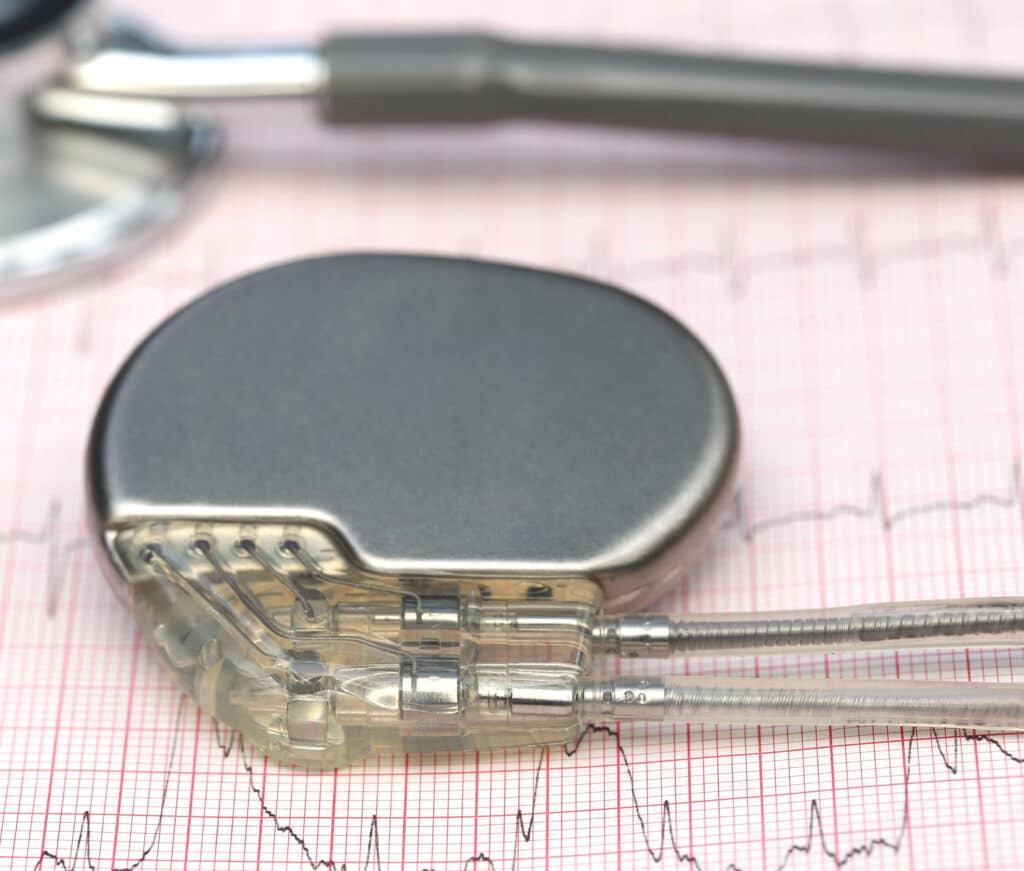
STAGE 1
Designing for application
- Our application-specific solution was a heavily modified version of an existing brushless vibration motor design.
- In addition our design contained three driving coils which fixed a start-up problem that the obsolete motor had presented.
- We supported with all the necessary documentation to enable a speedy submission to the FDA, and this prevented a production line stop for the customer’s pacemaker product line.
STAGE 2
Robust quality
- Testing, validation and very stringent quality controls, were the foundation of this project.
- We implemented extraordinary quality control and traceability of components processes.
- Full supply-chain auditing and accountability was of vital importance to our client and developed a new module in our ERP systems to meet their strict demands.
- Our advanced testing technology allowed us to thoroughly validate lifetime reliability testing.
STAGE 3
Ongoing support
- Our customer was made very confident that our motor was suitable and reliable.
- After delivering a better motor solution, on time and to spec, we provided ongoing support and communication with our customer. In doing so we improved their own product quality control processes.
- We quickly became a strong and reliable partner addressing their problems directly, and proactively managing their risk, throughout the whole project.
CASE STUDIES
We supply motor and mechanism solutions for all sorts of applications
-
Emergency services ruggedised radio
Emergency radios to withstand high temperatures, impacts, and vibrate through protective clothing
View Case Study
-
Weather balloon measurement lab
High volumes of low-cost reliable single-use motors for weather balloon measurement lab.
View Case Study
-
Bench-top pill counting machine
Bench-top medical instrument used a vibration motor to aid movement of pills through instrument pathways.
View Case Study
-
Swarm robot research linear actuator
Challenging technical and unique application for swarm robotics for a European robotic research Institution.
View Case Study
-
Medical patient simulator
Patient simulator for first-aid cardiac arrest training required a vibration motor to haptic simulate a heartbeat.
View Case Study
-
Medical laboratory DNA testing equipment
DNA Benchtop medical diagnosis machine redesign to support new commercialisation model.
View Case Study
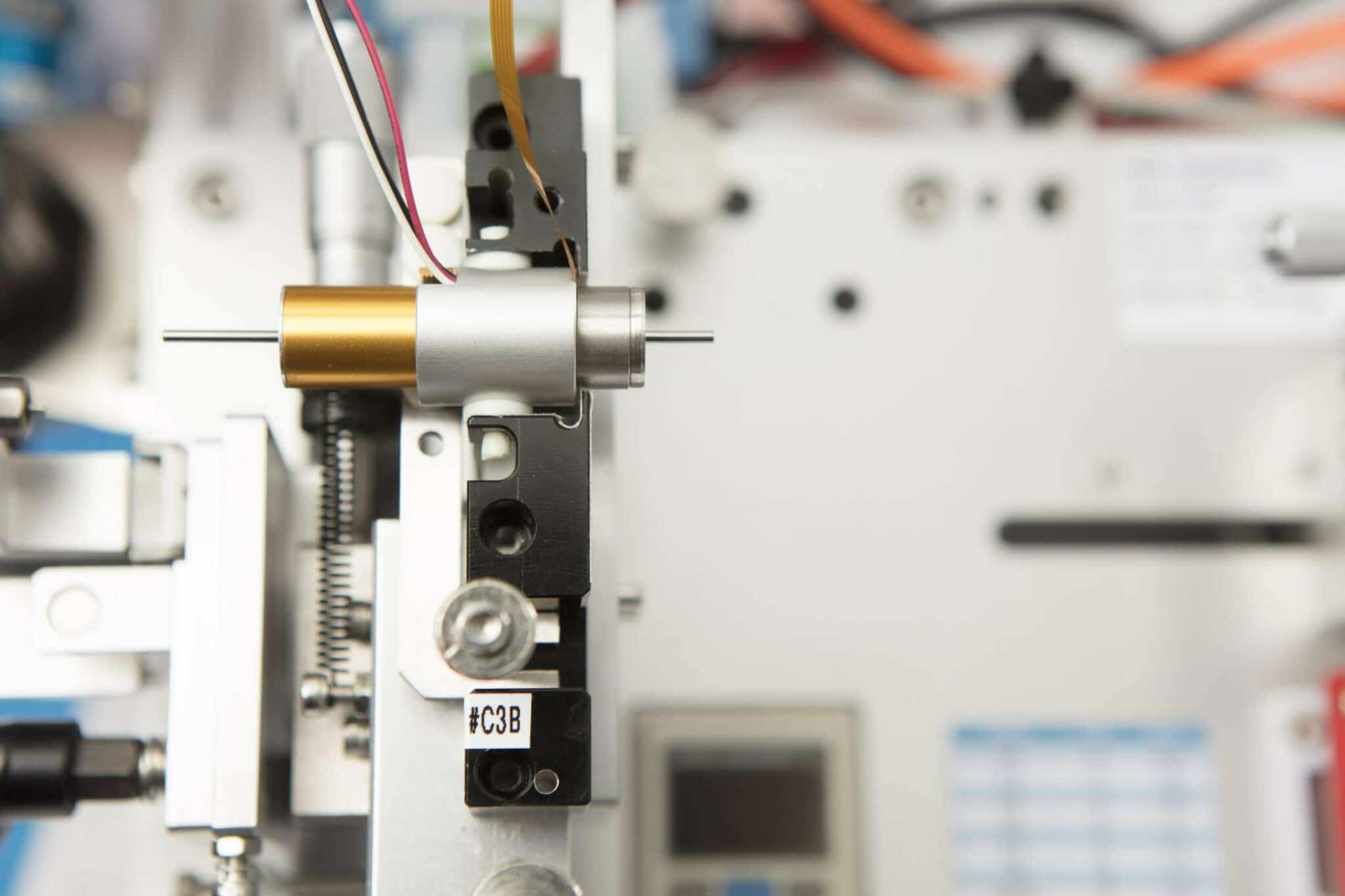
MORE THAN YOUR AVERAGE MOTOR SUPPLIER
We manage your risk
We manage your risk through optimised design and rigorous testing, protecting your application and intellectual property, fulfilling your performance requirements whilst reducing your lifecycle costs.
MOTORS & MECHANISMS
Precision products
-
DC motors
Iron-core, coreless and brushless DC motor technologies in a wide range of form factors and sizes, with off the shelf
View Page
-
DC gear motors
Building on our range of DC motors, we integrate spur and planetary gearboxes, from 6mm to 60mm frame diameters.
View Page
-
Vibration motors
With every vibration and haptic technology covered, we’ll help you select the best vibrating solution for your application.
View Page
-
Haptic feedback
Practical and reliable, low noise and high quality haptic feedback solutions for all types of application user interface.
View Page
-
Mechanisms
Custom motor assemblies designed and manufactured to your requirements. A turnkey service from design inputs to mass production.
View Page
Discover more
Resources and guides
Discover our product application notes, design guides, news and case studies
Industries served
At Precision Microdrives we design and manufacture customised electric motors and mechanisms across a number of industries.
Precision Microdrives
Whether you need a motor component, or a fully validated and tested complex mechanism – we’re here to help.