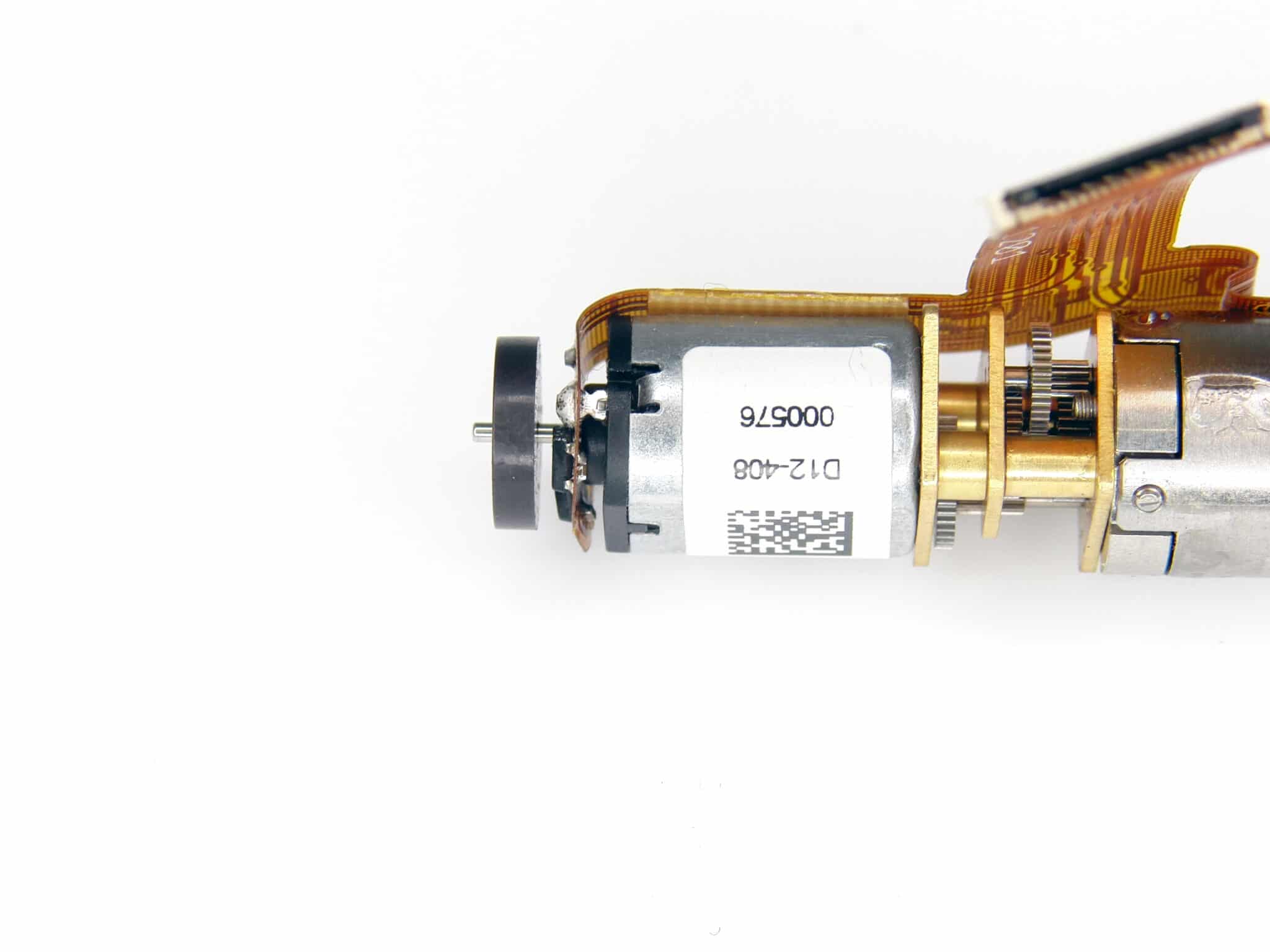
DC motors
DC brushed, coreless and brushless
Wide range of Precision DC motors with off-the-shelf sampling
Precision Microdrives designs and manufactures a wide range of high-quality, and cost effective, sub-Ø60 mm DC motors in a range of technologies. All types can be highly customised for a wide range of applications.
Speak to an engineer
Let us help you efficiently specify, validate, test, mass produce and integrate DC motors into your end product.
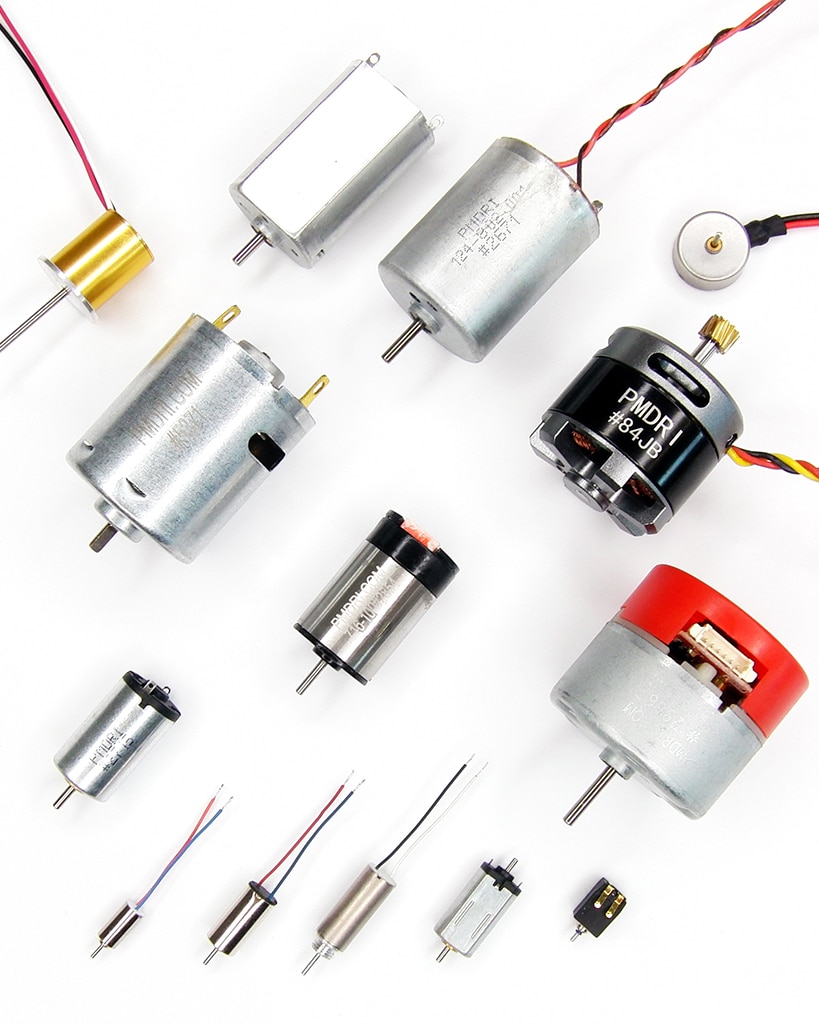
Three main DC motor technologies
Our three motor solutions are iron cored, coreless and brushless. All can be enhanced with motion control technology.
34 stocked motor form factors
We want to help get you developing quickly. So we have many off-the-shelf form factors in a variety of winding configurations available for immediate sample or purchase.
Customised for your application
Your application is unique so we expect you to need some custom features or specific performance. Work with our application engineers to design the perfect solution.
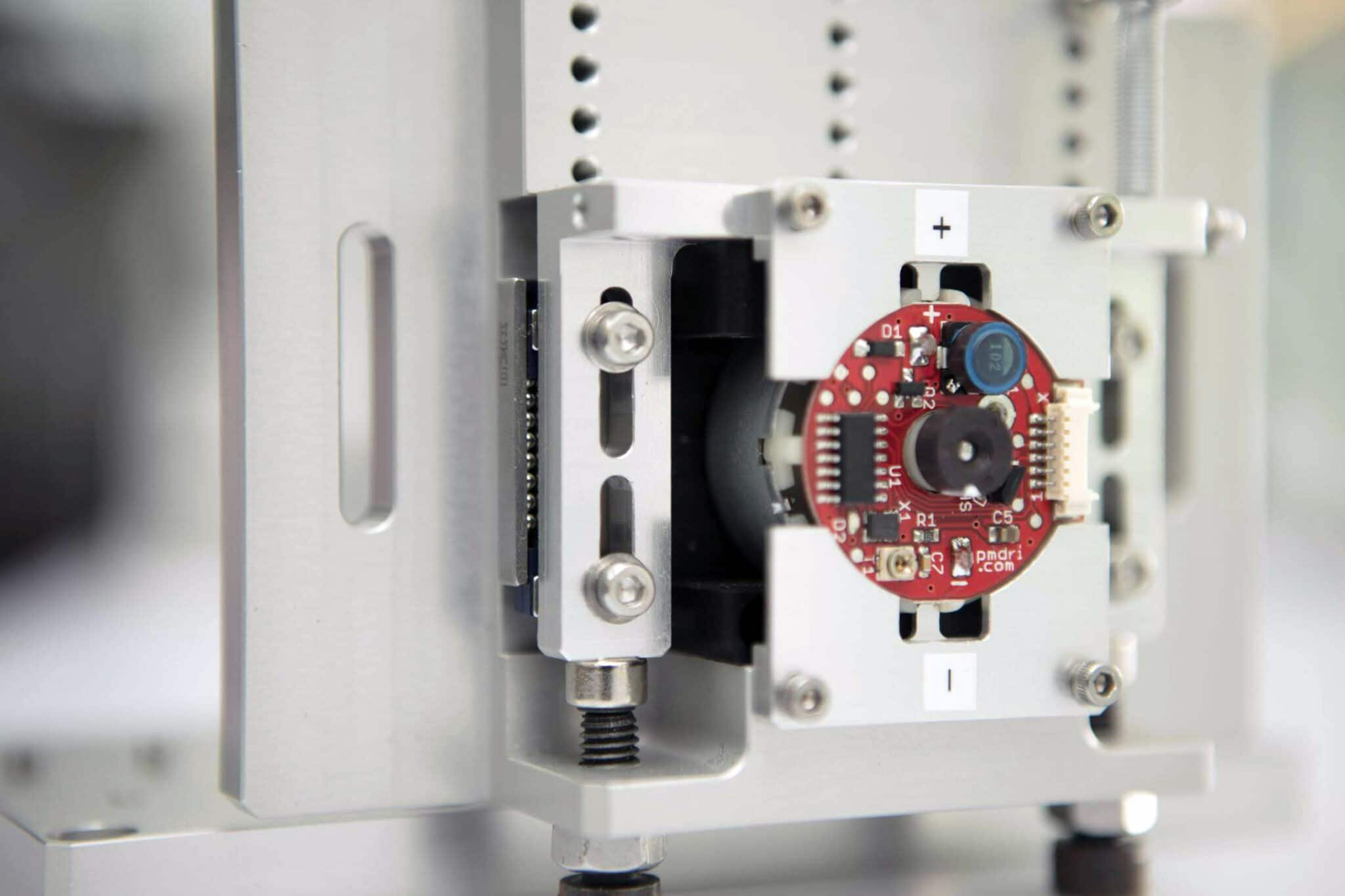
ORDER SAMPLES
Motor catalogue
Reliable, cost-effective miniature DC, Gear and Vibration motors that meet your application demands.
MOTORS & MECHANISMS
Our DC motor range
Verified and reliable precision motors, perfect for your application.
-
Vibration motors
With every vibration and haptic technology covered, we’ll help you select the best vibrating solution for your application.
View Page
-
DC gear motors
Building on our range of DC motors, we integrate spur and planetary gearboxes, from 6mm to 60mm frame diameters.
View Page
-
Haptic feedback
Practical and reliable, low noise and high quality haptic feedback solutions for all types of application user interface.
View Page
-
Linear actuators
Precise, reliable and highly customisable linear actuators designed for a wide range of industrial, commercial and medical applications.
View Page
-
Brushless Motors
We offer a comprehensive range of DC brushless motors in both slotted and slotless (high torque and negligible cogging) designs, with matching gearboxes, commutation sensors, and encoders.
View Page
-
Mechanisms
Custom motor assemblies designed and manufactured to your requirements. A turnkey service from design inputs to mass production.
View Page
DESIGN SOLUTIONS
DC motor technologies
We design and manufacture motors as components and motors within complete mechanism assemblies. In both cases, when working with DC motors, we use four different technologies:
Iron core brushed DC motors
The cheapest DC motor technology is called iron core brushed. Motors have been made using this method for over a century, although the manufacturing methods and materials used have certainly improved.
These motors are characterised by having the permanent magnets located on the inside surface of the case. The motor windings are formed around a stack of laminated iron sheets, and these form the armature which rotates to create the desired motion.
These motors can be engineered to very high standards and lifetimes, but the arrangement of their magnets and windings limits performance. Therefore for higher performance applications coreless and brushless motors are used.
The brushes mean that commutation is mechanical, and these motors can therefore be driven with a simple DC voltage. Positive for forwards, and negative for reverse.
You should be considering iron core motors if your product is cost sensitive and doesn’t require high performance in a really small package. Iron core motors are typically manufactured from 8mm diameter through to 60+mm diameters.
We have used iron core motors in a wide range of applications from consumer through to high volume medical instruments.
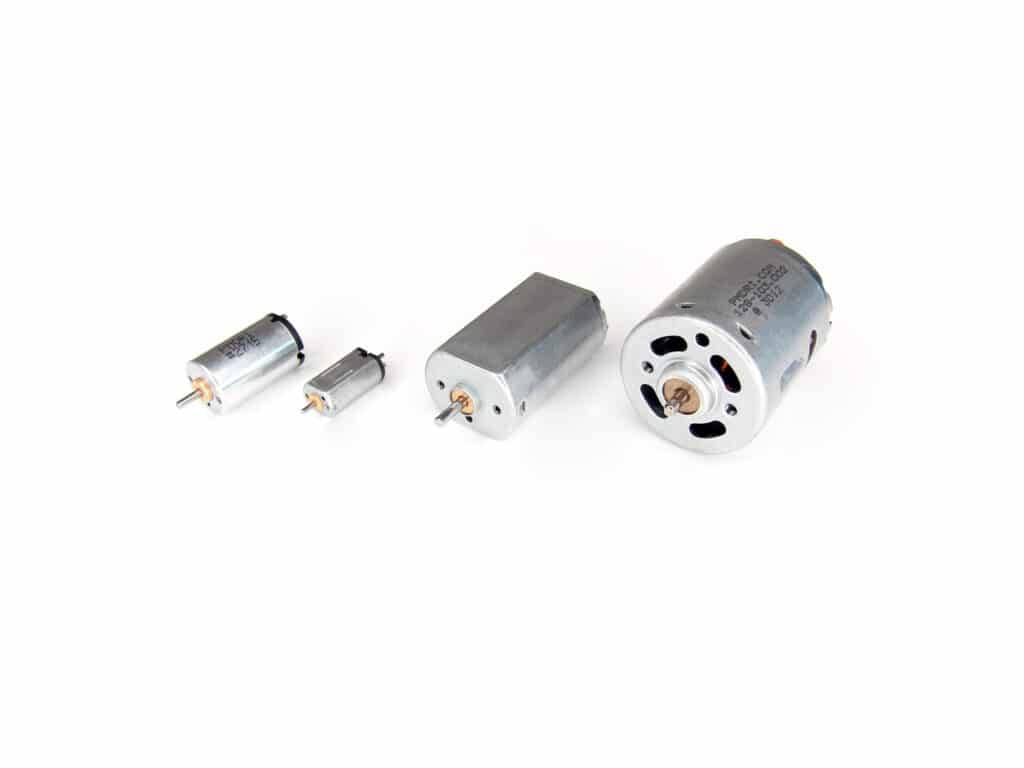
Coreless brushed DC motors
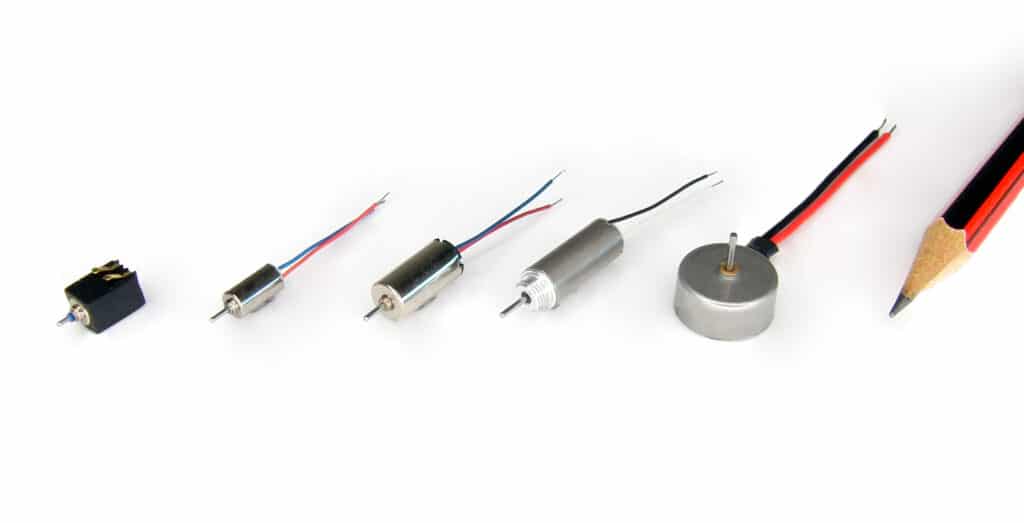
Coreless motors offer higher performance at a higher cost than iron core motors.
In this manufacturing arrangement, instead of a winding, a stationary high performance toroidal magnet makes up the core of the motor. The motor windings are still attached to the motor shaft but are laid up in a resin moulding that rotates around the magnetic core. This enables higher performance in two ways. Firstly, the efficiency of the motor is higher because magnetic losses are lower. Secondly, since the windings (the part that heats up under load) are closer to the motor case, they can radiate unwanted heat better and therefore deliver higher power.
The brushes mean that commutation is mechanical, and these motors can therefore be driven with a simple DC voltage. Positive for forwards and negative for reverse.
They are typically used in two specific design scenarios. Firstly, in sub 10mm diameter frame motors, where the only way to get usable performance is with this construction method. Secondly, in larger motors where a high performance is required and there is a preference to drive the motors with a DC voltage, rather than the more complex signals that are required when using brushless motors.
We typically use coreless motors for highly miniaturised and high performance applications, but lower volume industrial, instrument and medical applications.
Brushless (in-runner and out-runner) DC motors
Brushless motors used to be the most expensive DC motor solution, because they could only be used with a special controller to convert DC voltages into complex three-phase signals.
However, off-the-shelf single IC brushless motor controllers are becoming available at much lower costs than traditional custom designs.
In the brushless design, the windings are stationary (opposite to brushed motors) and the magnet rotates. There are two flavours of these motors.
In-runner designs see the magnet sit within the stationary windings. These are good for lower torque, higher speed applications where the motor will typically rotate faster than 5k rpm.
Out-runner designs see the magnet rotate outside the stationary windings. These are good for higher torque, lower speed applications where the rotor will spin less than 5k rpm.
One major benefit to brushless motors is that there are no brushes which tend to wear out and dictate the lifetime of a motor. Therefore brushless motors tend to last much longer than brushed motors. The downside is that they need a special driver, certain operating scenarios such as high load starts from rest and will need special attention to the design.
Find out more about our range of brushless motors here.
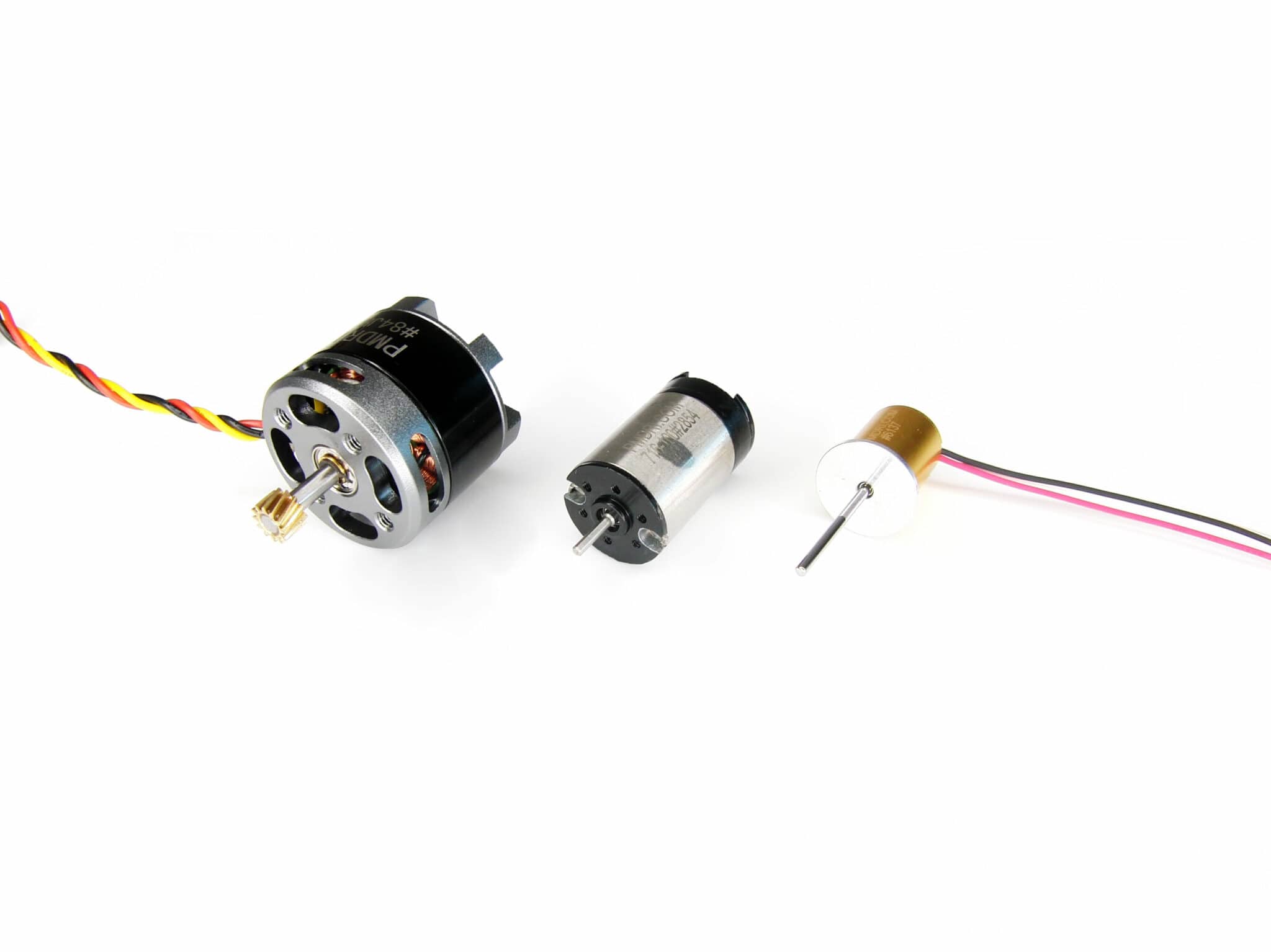
Encoders and integrated motion controllers
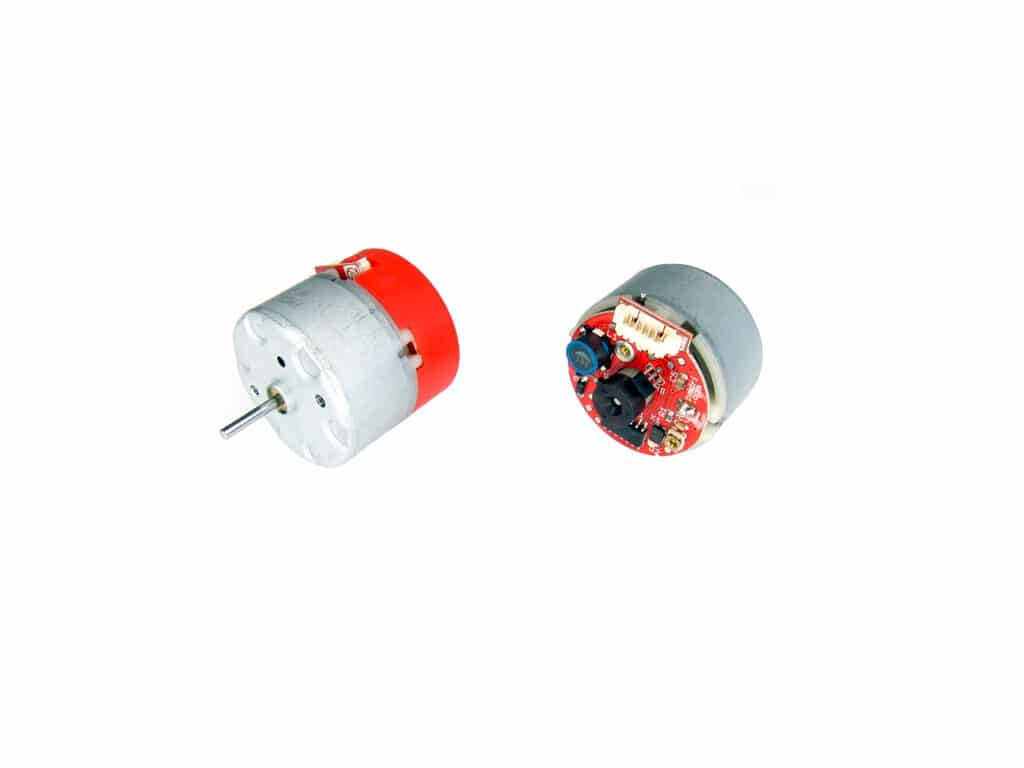
Motors are added to products and application to move something. The motor will rotate and sometimes that’s just what a design needs. In other cases, that motion may need to be more complicated and there are many mechanisms that can be fitted to the motor to convert it.
Generally the higher the voltage drive the faster the motor rotates. The higher the torque load applied to the motor the more current it will consume. Some applications don’t need anything more complex than an on/off motion such as a motor turning a fan impeller in a hairdryer.
Many applications, however, need a more precise control. This might be a specific speed such as a motor driving a pump. A more common use is a certain number of rotations such as when a motor mechanism creates a linear motion. We can use the number of rotations to know how far the linear slide is extended.
In these cases we build onto the motor an encoder (an advanced counter) and where necessary an integrated motion controller. This can receive commands from the host application such as moving a syringe plunger forward and back 10mm.
PRECISION MOTOR DESIGN
Typical DC motor form factors
Irrespective of the DC motor technology used there are some common form factors and design influences that are commonly used in applications across all industries. Below are some examples, that can be used to describe your preferred solution.
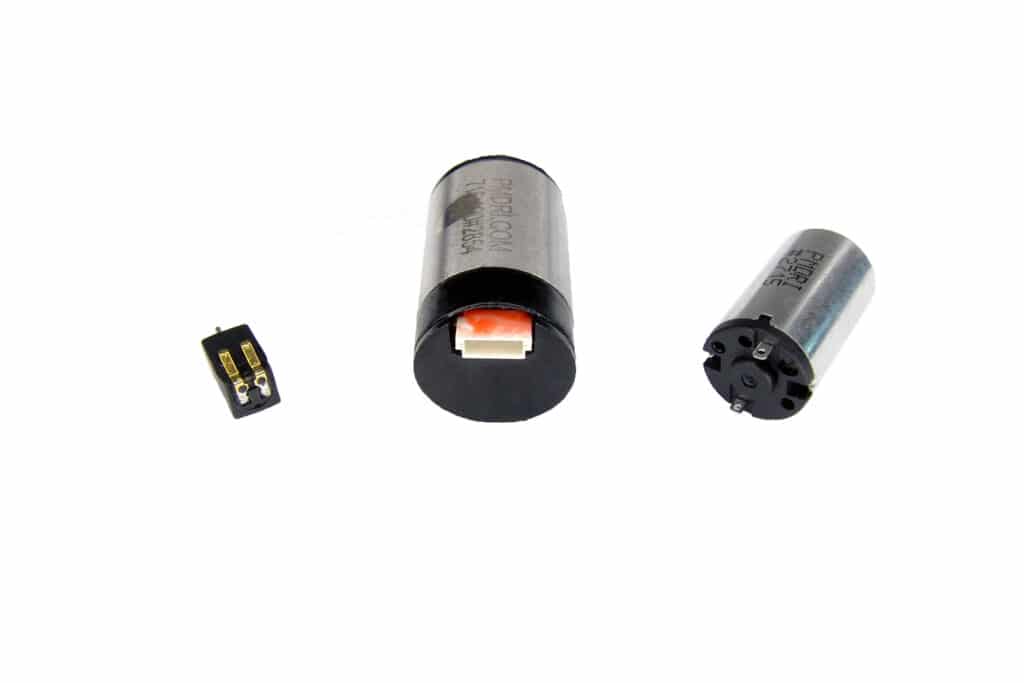
Terminals and connector pins
Connecting the motor to the application is clearly critical. We typically use soldered pins, spring pad connectors and integrated connectors.
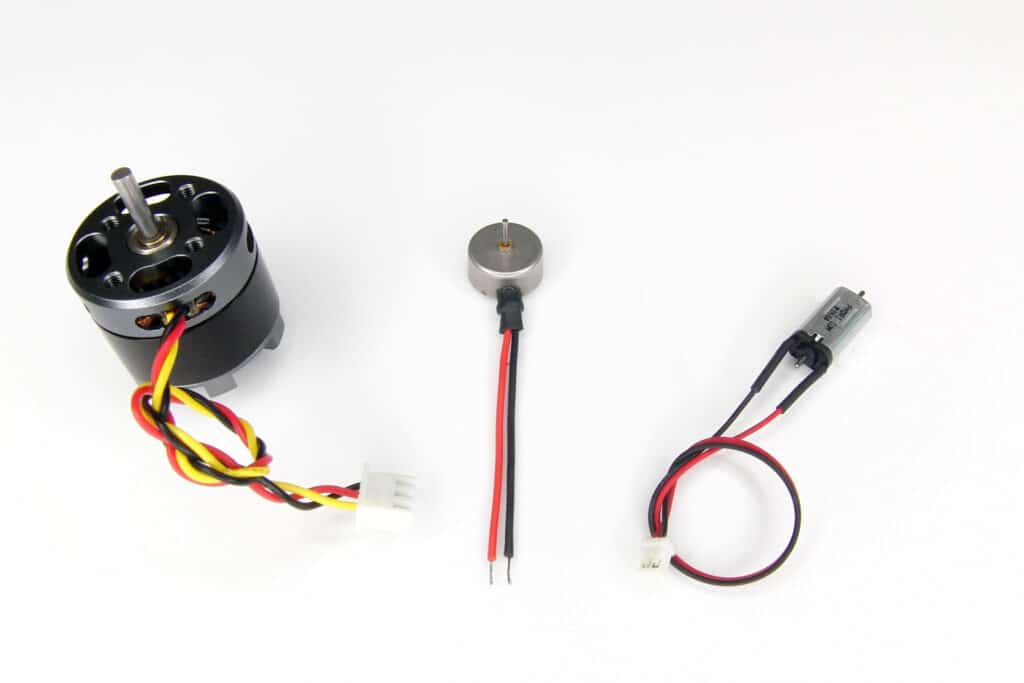
Leads and connectors
Wires and leads are frequently used to electrically connect motors in application. We offer different lengths, gauges and pre-fitted connectors.
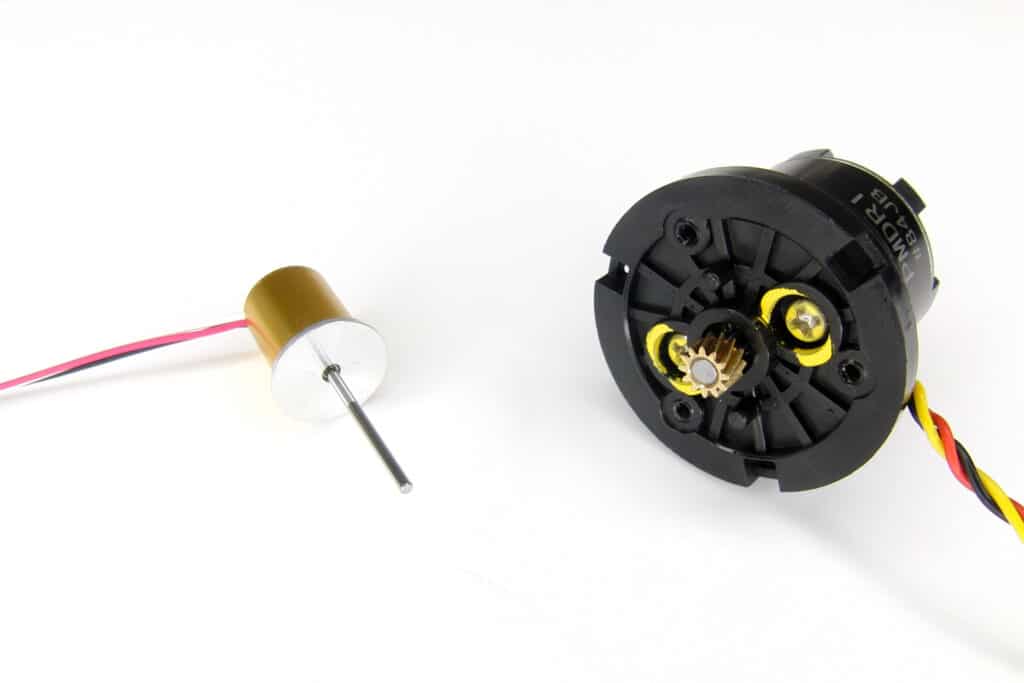
Frame modifications
Securing motor frames to your application can be done in many forms. Custom fastening points and brackets are commonly used.
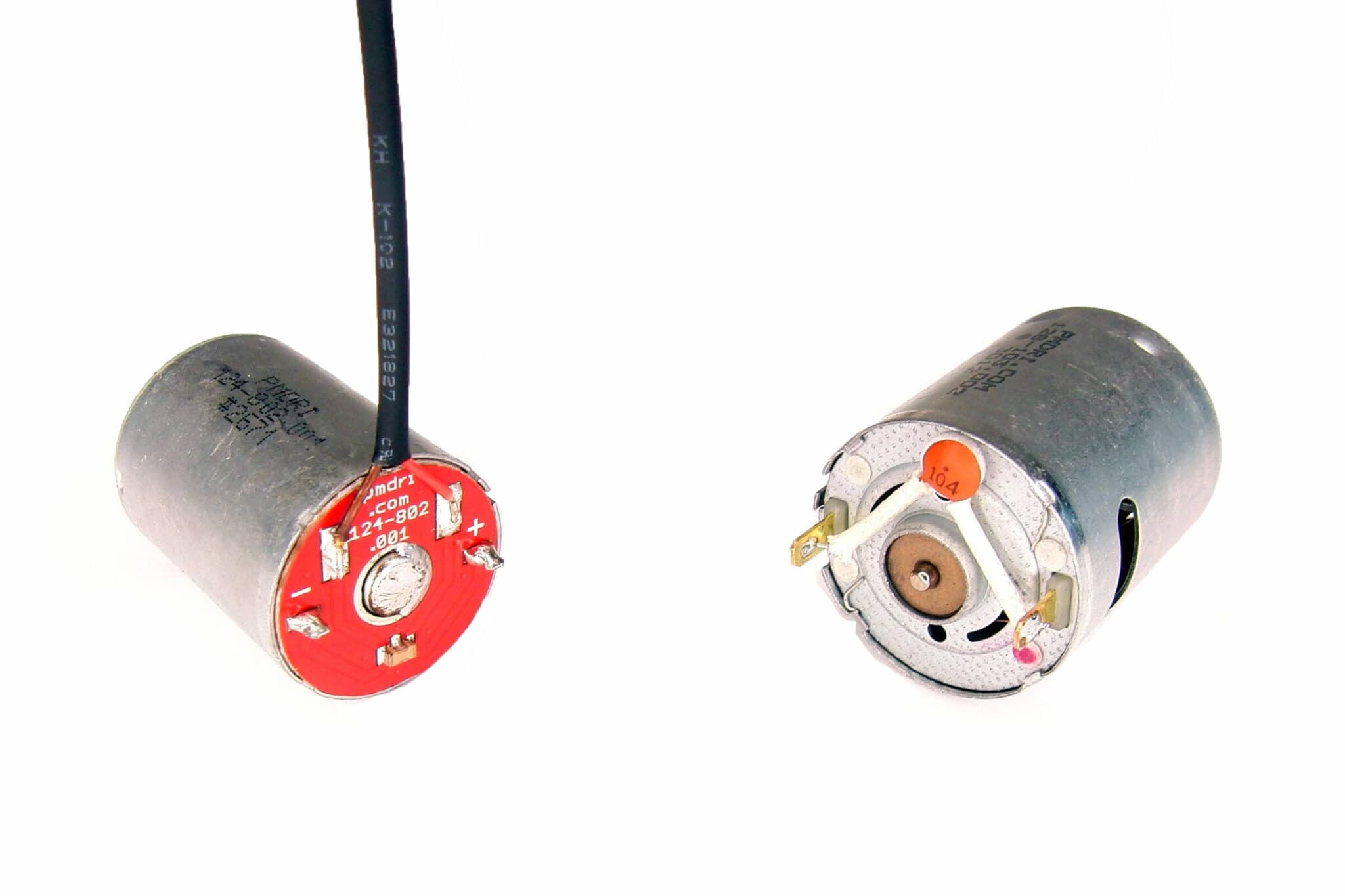
EMI filters and backpack PCBs
Operating motors produce EMI electrical noise. This can be mitigated by fitting filters that can be either PCB or wire based.
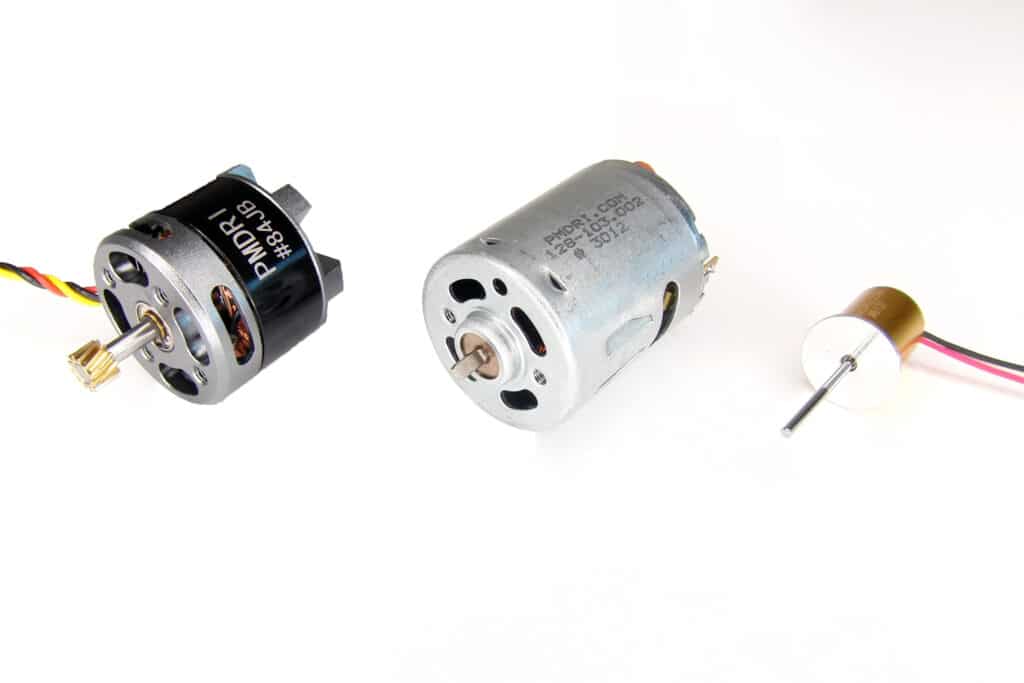
Shaft modifications
The motor needs to interface mechanically to your product. We can design custom shafts and pre-fit gears, bushes and bosses.
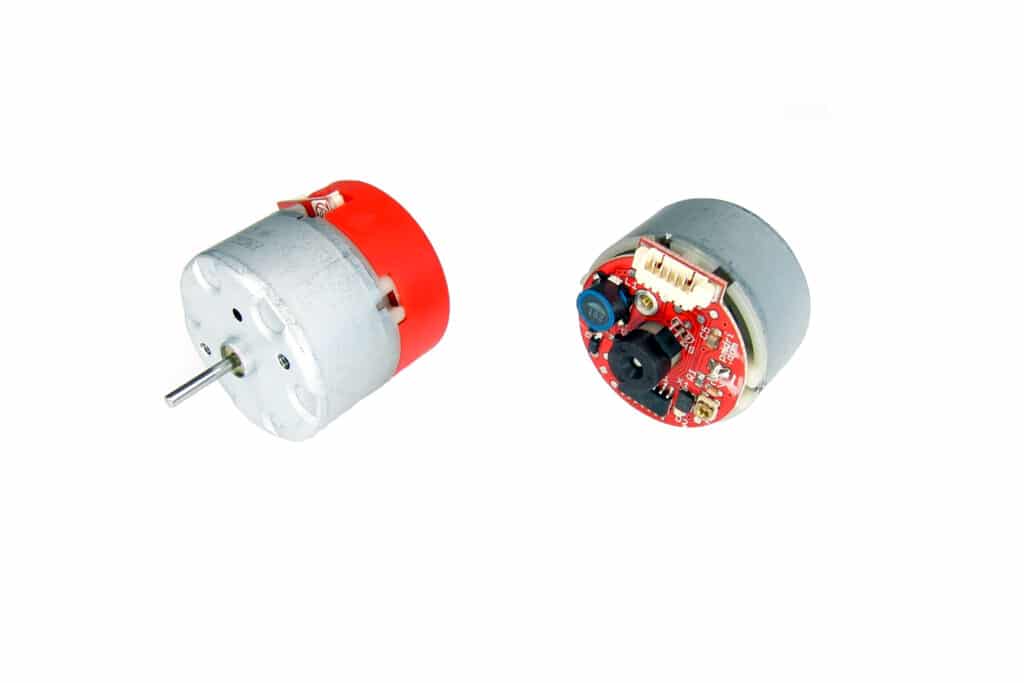
Motion controllers
A small PCB affixed to the back a DC motor can transform it into a precision servo, for a cost fraction of a similar off-the-shelf unit.
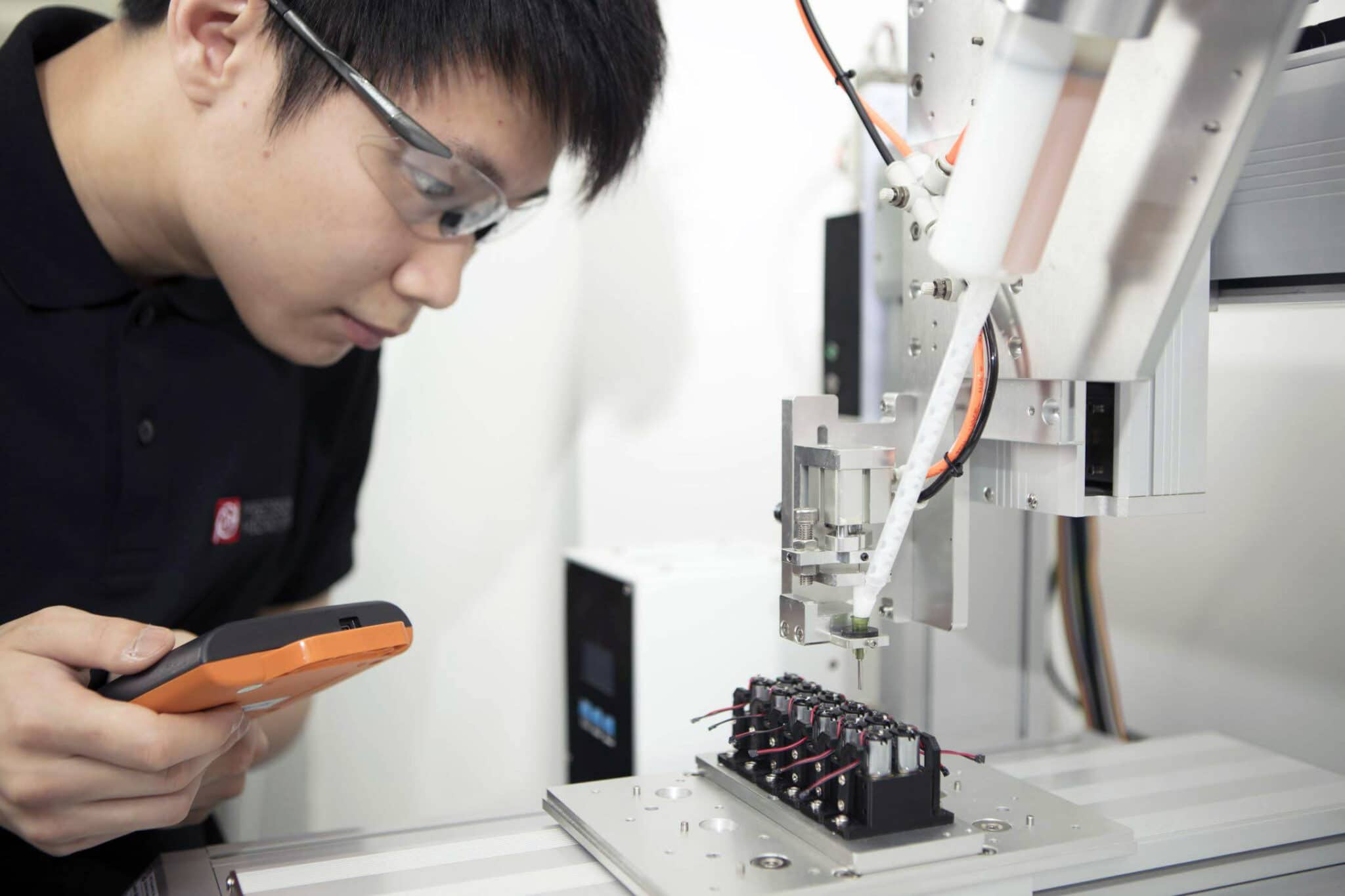
MORE THAN YOUR AVERAGE MOTOR SUPPLIER
Precision mechanisms
Innovative and optimised mechanism design for application.
Application case studies
Our DC motors are used in many applications and industries. Learn more about typical application uses and examples we have worked on.
Instruments for measuring and testing
Instruments require a high amount of accuracy and power. You can depend on our team of experienced engineers who have designed micro motor and drive solutions for high-precision measuring devices and laboratory dispensary equipment.
A partnership with us will provide you with precision products and control coupled with continued support from our team of engineers.
Case study | weather balloon
Weather balloons are used to perform all kinds of experiments in the atmosphere. The balloon is filled with enough helium to reach the target atmospheric layer and carries underneath it a small radio-controlled measurement lab.
Their single-use measurement lab was a cut-down version of a much more expensive multi-use platform and used a servo motor to drive a pump.
In this project, it was important that the motor was able to keep a constant speed. To ensure that, we designed a PID control PCB that was able to drive the motor at a constant speed. The PCB was mounted to the back of the motor and using Hall sensors, could read motors speed continuously.
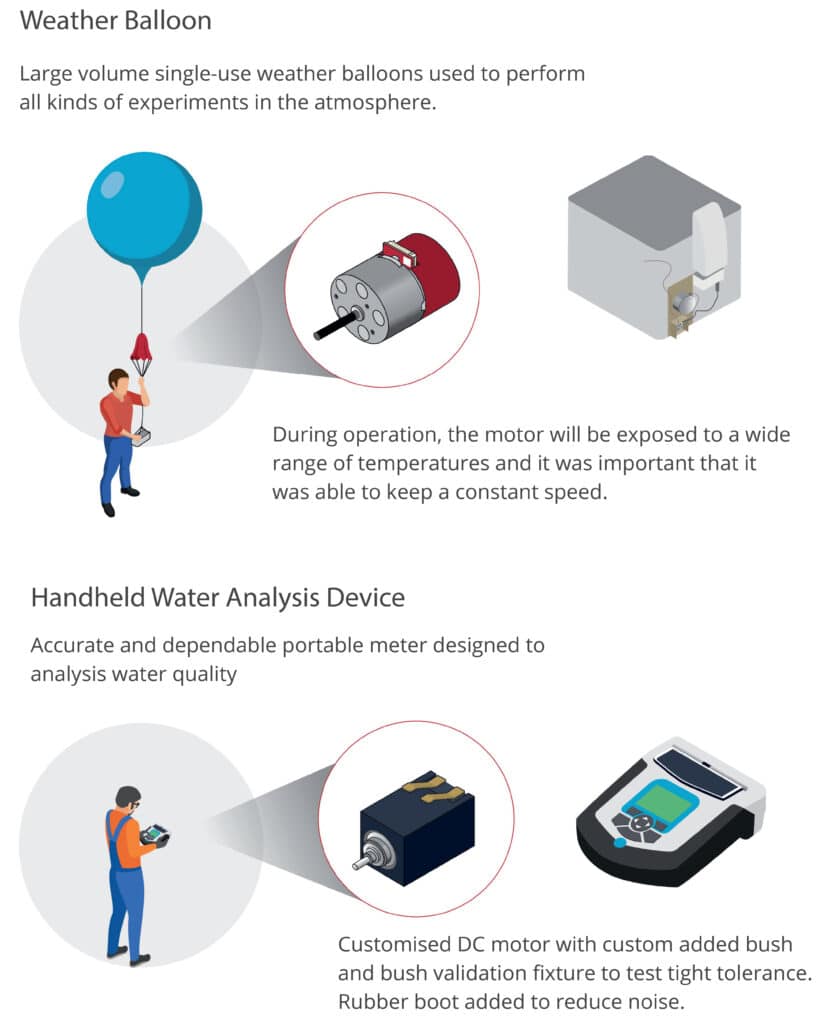
Precise medical applications
Precision Microdrives has proven capability in designing and manufacturing electro-mechanical mechanisms for medical devices.
With demand for new innovative medical devices rapidly increasing, lower device price points will make these products widely adopted, especially with diagnostic applications which are being prioritised worldwide.
Case study | Medical oral drug delivery device
Our medical device customer asked us for support in developing an innovative method of dispensing precise measures of medication, through an inhaler.
We developed two different motors for this product to be used in the same instrument. For the sake of easy assembly, we also developed a custom wireset and custom shafts.
The validation of these was very important. One of the risks identified in the application was potential damage due to radial and axial load.
We supported the customer in validating the gearbox against the expected load and provided support in design best practices to avoid longevity issues.
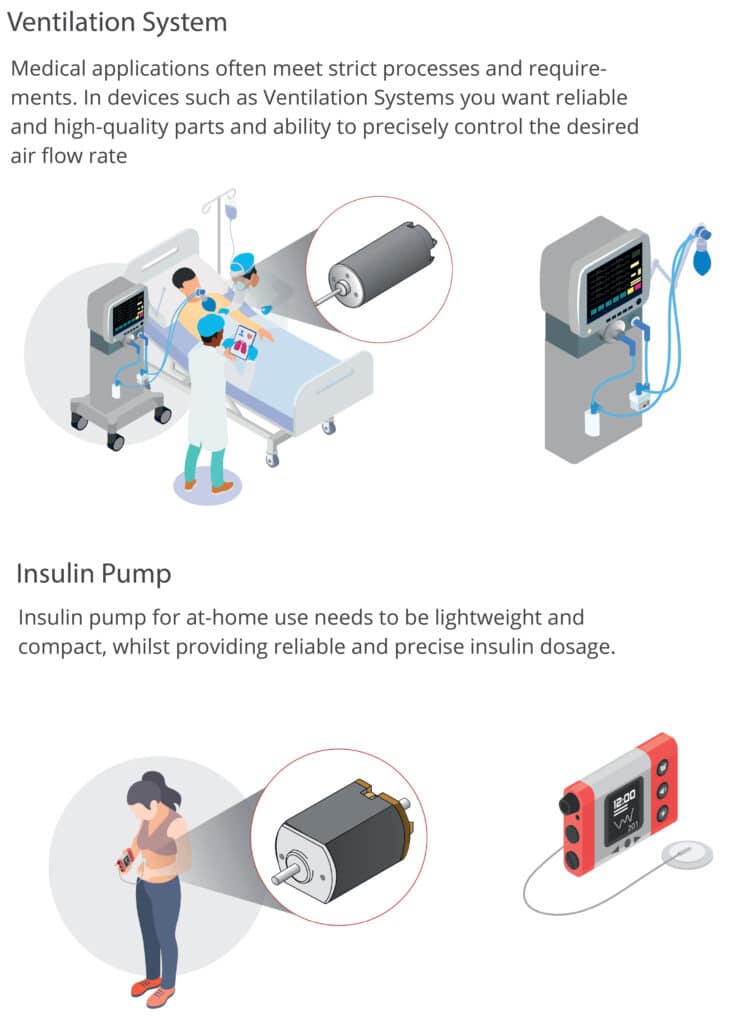
DC motors in industrial tools
Industrial products and machinery are becoming more complex in design demanding a wider range of functions than ever before. Therefore requiring higher performing parts at a fraction of the size.
Here at Precision Microdrives we design and manufacture reliable and verified micro DC, Gear and Vibration Motors with a range of customisations to give you as much choice, power and efficiency when designing your challenging industrial applications.
Case study | Gas sampling equipment
Our customer was designing a new battery powered handheld instrument to implement a new and recently patented gas analysis method.
The analysis method requires the instrument to process the collected sample using two pumps that need to remain synchronised. The sampled gas is sent via these pumps to various electronic detectors which conduct the actual tests.
We designed a brushless DC motor solution, with a customised encoder and flex PCB sealed within a grounded metal enclosure. The device passed the stringent ATEX guidelines and we have been manufacturing for this customer ever since.
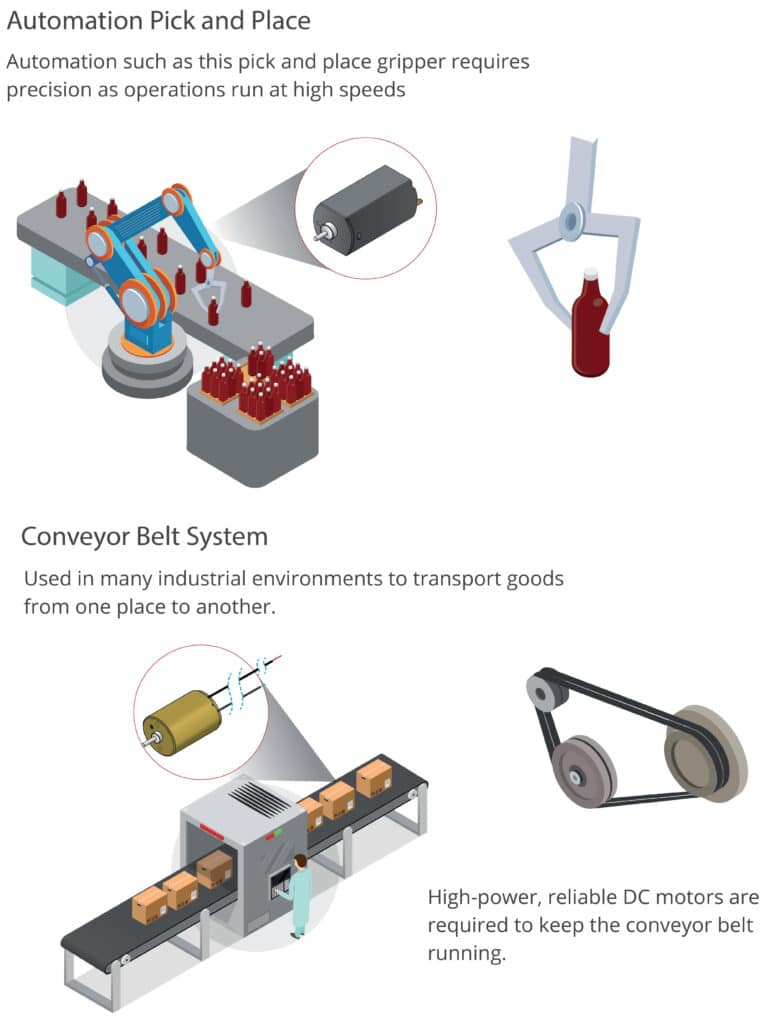
Precision products for security
Our motors and mechanisms are often used for security appliances and applications.
Products in this industry often need to meet strict requirements to make sure they are secure and provide guaranteed protection and reliable results.
Case study | electronic door lock cylinder
The customer required a like-for-like performance drop-in customised 6mm dc motor for their electronic door lock.
The lock uses a fob device, instead of a traditional key to open and close the locking mechanism for commercial buildings.
PMD manufactured a 5-Pole brushed DC motor within a sub-assembly satisfying the two-tier sourcing requirement.
The motor sub-assembly included a pinion gear on the shaft and a location point for the lock.
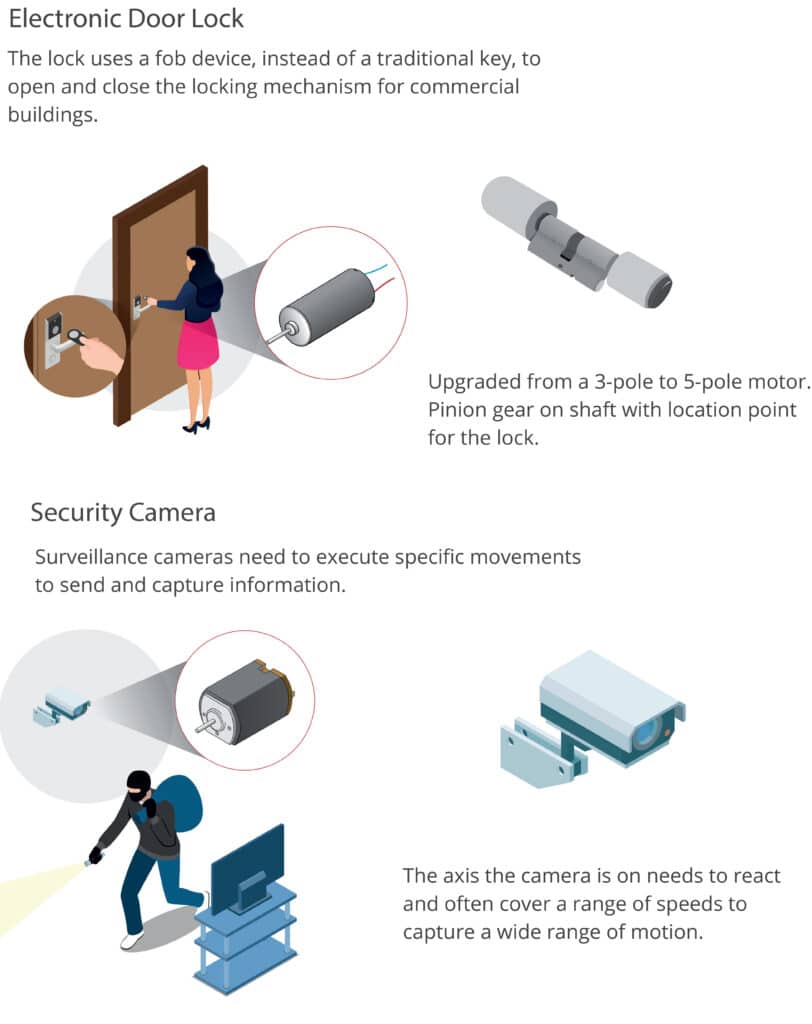
HOW CAN WE HELP?
We add value to your device through
Custom assemblies
Longevity testing
Mechanism design
Engineering confidence
In-house production
Full testing validation
PRECISION PROCESSES
Our capabilities
We can support you through the whole journey from prototype to high volume cost-effective mass production:
Discover more
Resources and guides
Discover our product application notes, design guides, news and case studies.
DC motor case studies
Explore our collection of case studies, examples of our products in a range of applications.
Precision Microdrives
Whether you need a motor component, or a fully validated and tested complex mechanism – we’re here to help. Find out more about our company.