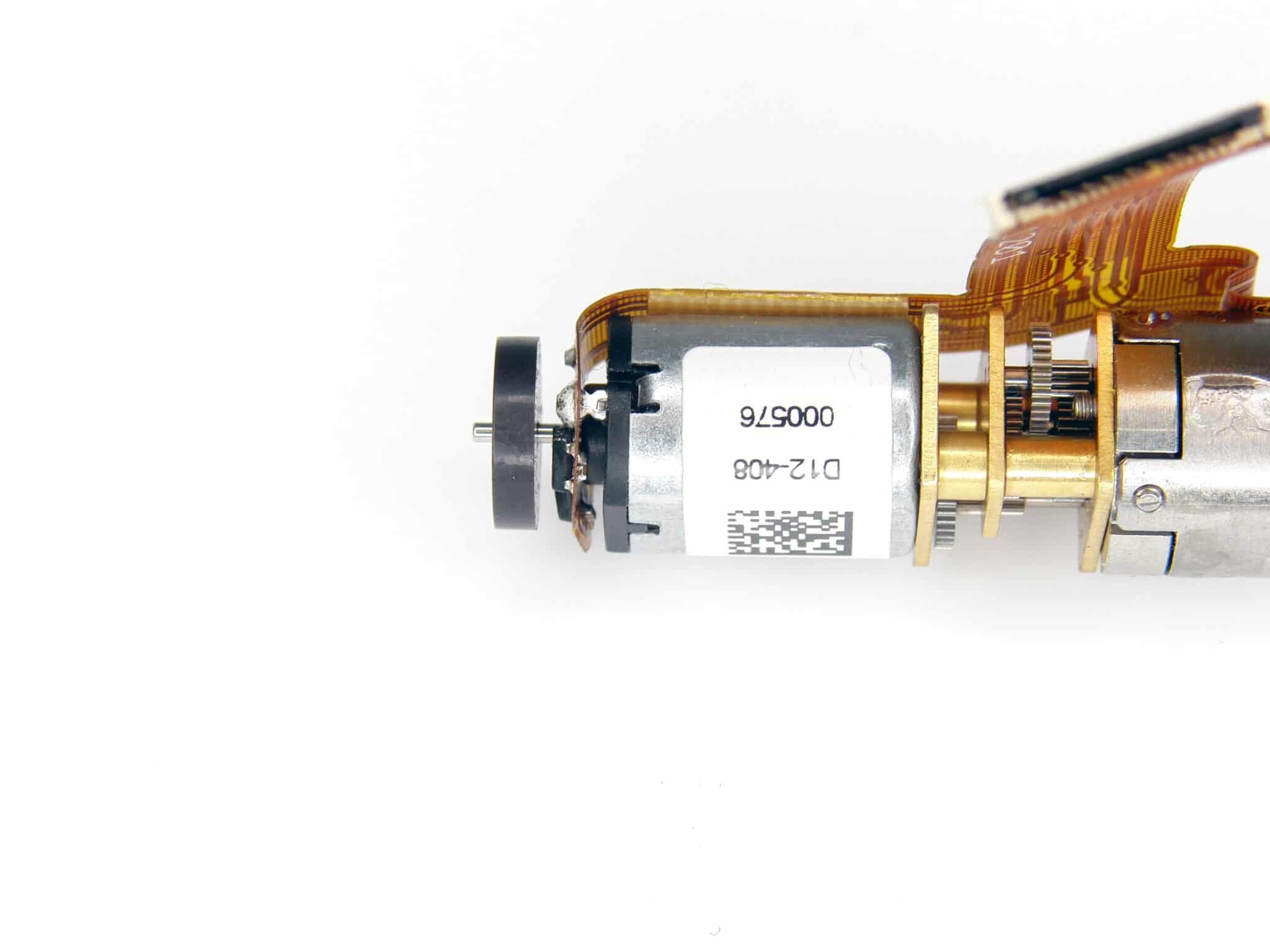
DC gear motors
DC brushed, brushless, spur and planetary
Wide range of DC gear motors with off-the-shelf sampling
Precision Microdrives designs and manufactures a wide range of high-quality, and cost-effective, sub-Ø60 mm DC motors in a range of technologies. All types can be highly customised for a wide range of applications.
Speak to an engineer
Let us help you efficiently specify, validate, test, mass produce, and integrate DC gear motors into your end product.
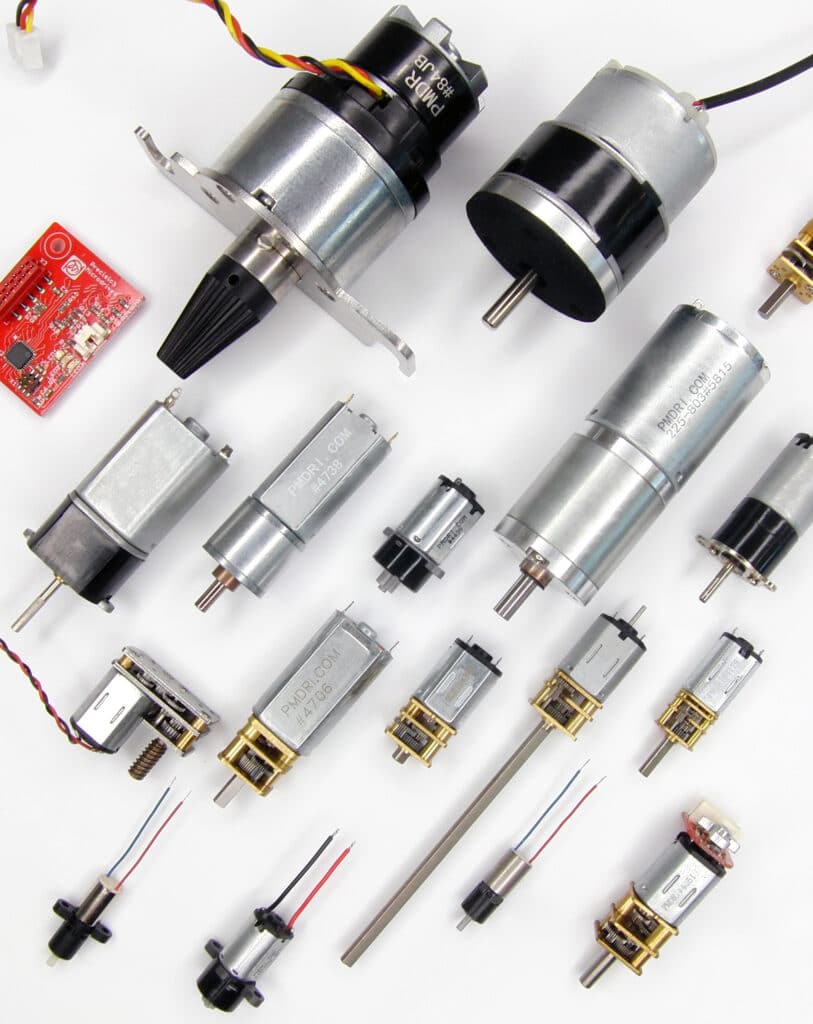
Three main DC Gear motor technologies
Our three main DC gear motor solutions use iron core, coreless and brushless technologies with two gearboxes, spur and planetary, in a variety of materials.
78 stocked motor form factors
We want to help get you developing quickly. So we have many off-the-shelf form factors with a variety of winding configurations available for immediate sample or purchase.
Customised for your application
Your application is unique so we expect you to need some custom features or specific performance. Work with our application engineers to design the perfect solution.
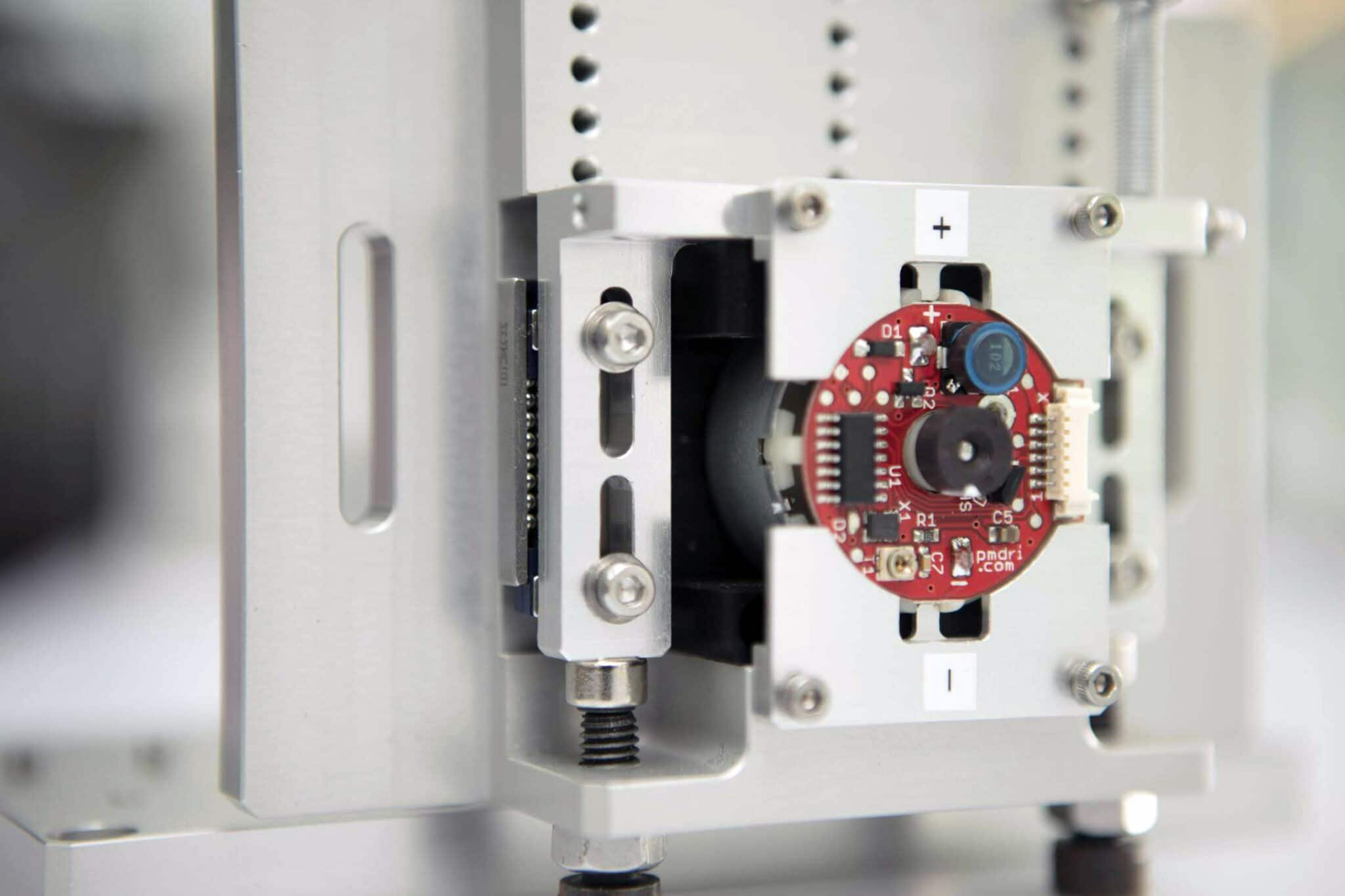
ORDER SAMPLES
Motor catalogue
Reliable, cost-effective miniature DC, gear and vibration motors that meet your application demands.
DESIGN SOLUTIONS
Gear motor technologies
We design and manufacture gear motors both as individual components, and as part of larger assemblies. In this process, we use four different categories of technology depending on the needs of the end application:
Spur geared DC motors
Gearboxes are added to motors to reduce the rotational speed and to amplify the torque. All of our spur gear boxes are constructed using steel gears to maximise strength and lifetime and can be coupled to iron core, coreless and brushless motors.
There are many designs like this on the market, but the durability and performance lies in the detail. The metallurgy of the steel has a major impact on lifetime, as does the type and application of lubricant. We have witnessed many examples of lower grade steel being used, resulting in chipped gear teeth, which near enough guarantees almost immediate gearbox destruction.
The grade of brass alloy used for the gearbox frame will impact the lifetime of the integral bearings, which in turn will affect gear concentricity and meshing. This can can dramatically affect wear and also exacerbate the risk of chipped or broken teeth.
With the right motor type, motor windings, correct gearing ratios and the right materials, our open frame spur geared DC motors can easily displace motors that cost 6x to 10x more in many applications. They therefore represent excellent value for money.
We manufacture spur gearboxes in other form factors, as applications demand, and will sometimes design in helical cut gears for higher load applications. In some applications where audible noise must be reduced, we can add gear stages from a range of engineered plastics.
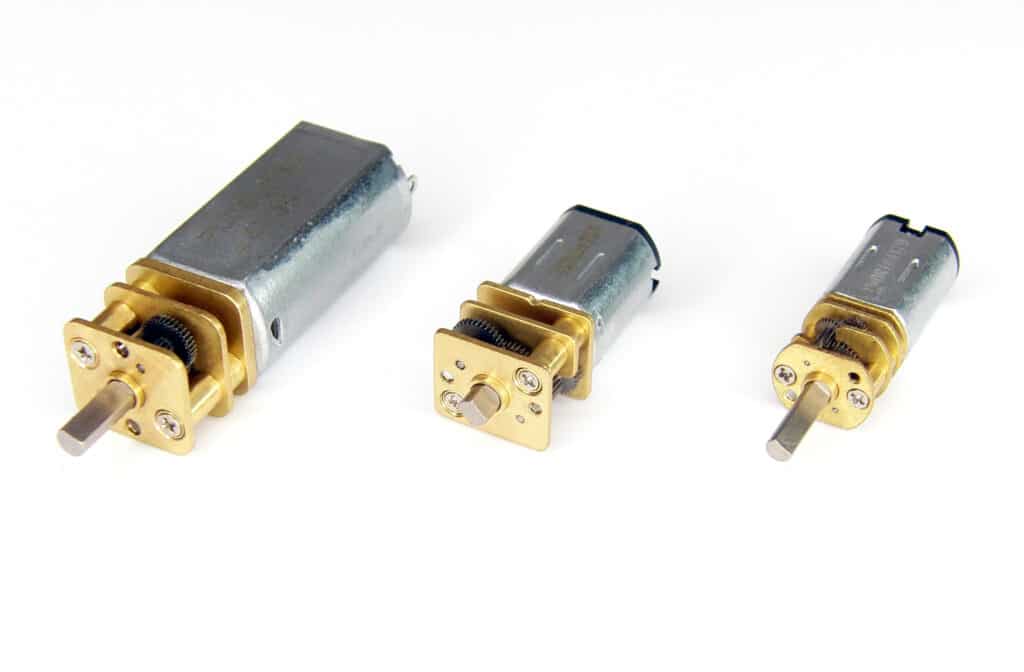
Planetary geared DC motors
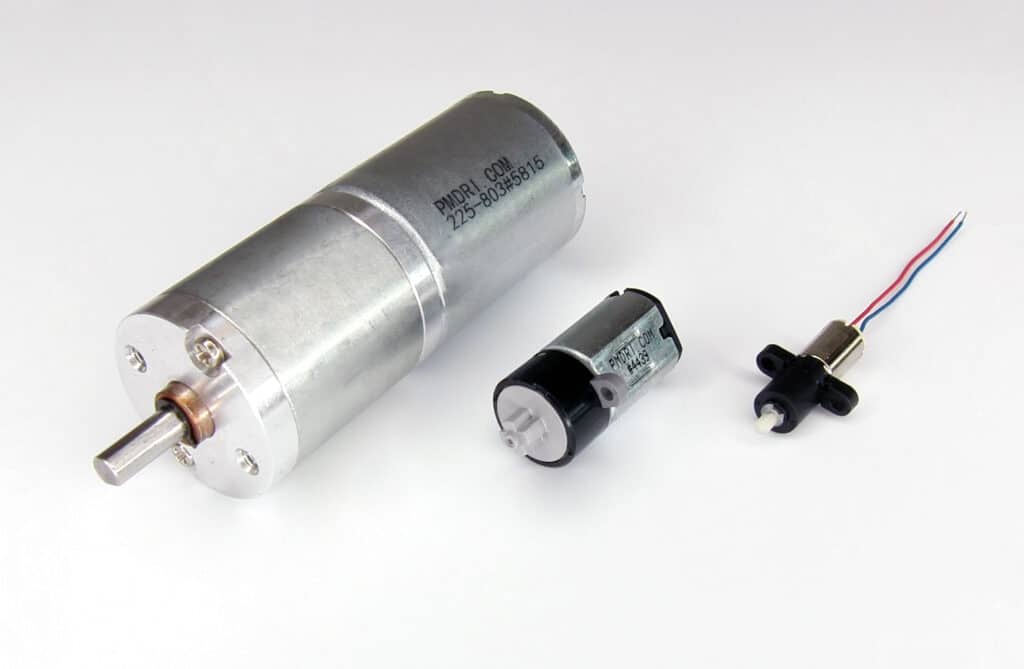
Our general approach is to use spur gearboxes where possible to optimise costs. However there are often cases where we need to optimise a design for performance or miniaturisation.
In these cases, using a planetary gearbox is more appropriate.
For sub 10mm diameter geared motors, metal gears become very expensive, requiring the adoption of gears made from injection moulded engineering plastics such as POM or LCP. To reduce gear tooth load in these designs, a planetary gearbox arrangement is preferred because there are more mesh points for each gear.
The same logic applies to larger gearboxes with higher loads. Although these larger gearboxes will use steel gears, the planetary gearbox design reduces individual gear loading. This means that the gearbox can withstand more load, and under these higher loads the gearbox will be more durable.
Planetary designs are more complex and therefore expensive than spur gearbox designs, but with the level of specification they still won’t break the bank.
Iron core, coreless and brushless construction
We can couple any of our gearbox designs to any type of motor technology. There are three motor constructions that we commonly use.
Iron core brushed designs are most cost effective and can be easily driven with a simple DC voltage. They can be engineered to high standards in terms of durability with the right sub-components, but they are limited in performance by their arrangement and construction methods. They can be used in motor designs greater than 8mm frame diameter.
Coreless brushed motor designs can also be driven by a simple DC voltage and offer higher performance in larger sizes. They are the only type of motors available in sub 8mm frame diameters. The construction method is more costly than iron core, but at the smallest scale, all that’s practically manufacturable.
Brushless motor designs are much more complex to drive, requiring a controller and driver circuit to produce the three phase drive signals. However, since they lack brushes, which are one of the components that most commonly wears, they are extremely durable. They are available in frame sizes greater than 12mm diameter and can be constructed in two ways to optimise for speed or torque.
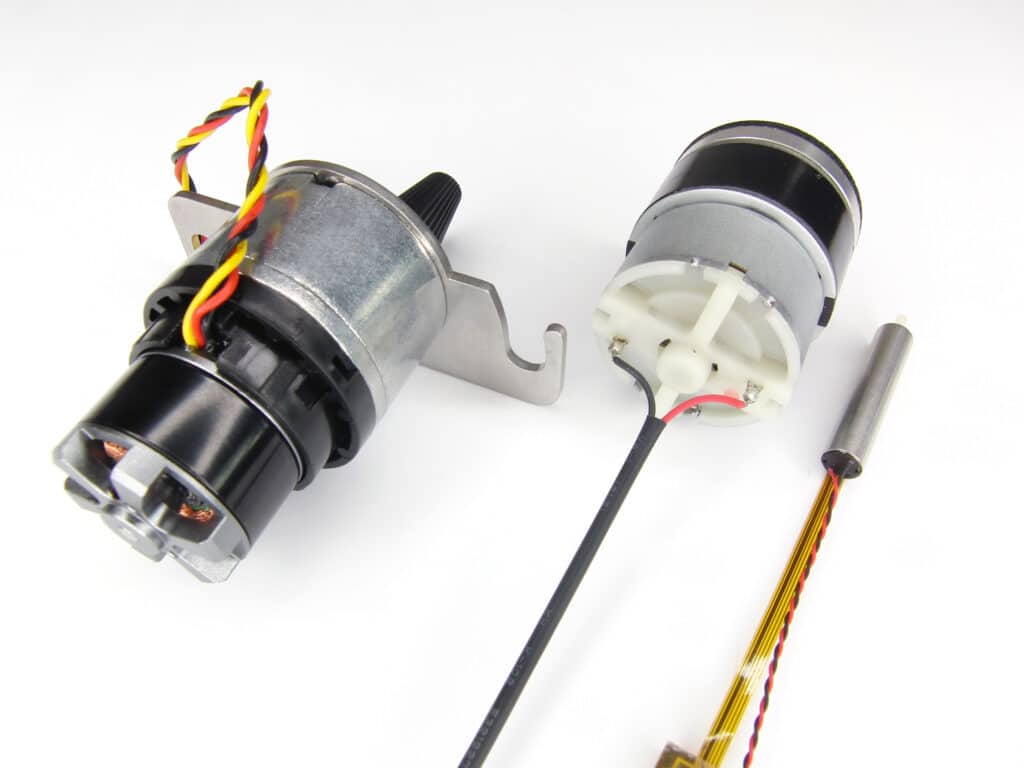
Encoders and integrated motion controllers
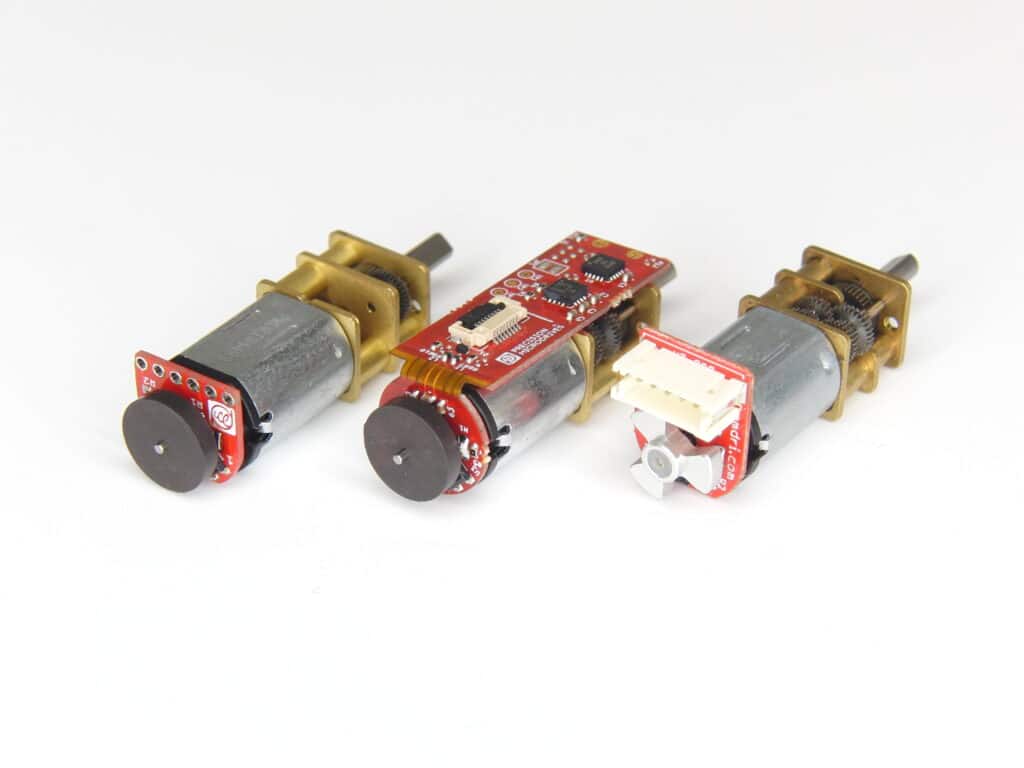
Gear motors are added to products and applications to move something. The motor will rotate and sometimes that’s exactly what a design needs. In other cases, that motion may need to be more complicated and there are many mechanisms that can be fitted to the gearbox output shaft to convert it.
Generally the higher voltage drive the faster the motor will rotate. The higher the torque load applied to the motor the more current it will consume. Some applications don’t need anything more complex than an on / off motion such as a gear motor slowly and firmly turning the blades of an ice crusher.
Many applications, however, need far more precise control. This might be a specific speed, e.g. a gear motor driving an electric screwdriver. A more common use is a certain number of rotations, such as when a motor mechanisms creates a linear motion. We can use the number of rotations to know how far the linear slide is extended.
In these cases, we build onto the motor an encoder (an advanced counter) and where necessary an integrated motion controller. This can receive commands from the host application such as to move a syringe plunger back / forward 10mm.
PRECISION MOTOR DESIGN
Typical gear motor form factors
Irrespective of the gearmotor technology adopted, there are some common form factors and design influences that are commonly used in applications across all industries. Below are some examples that can be used to describe your preferred solution.
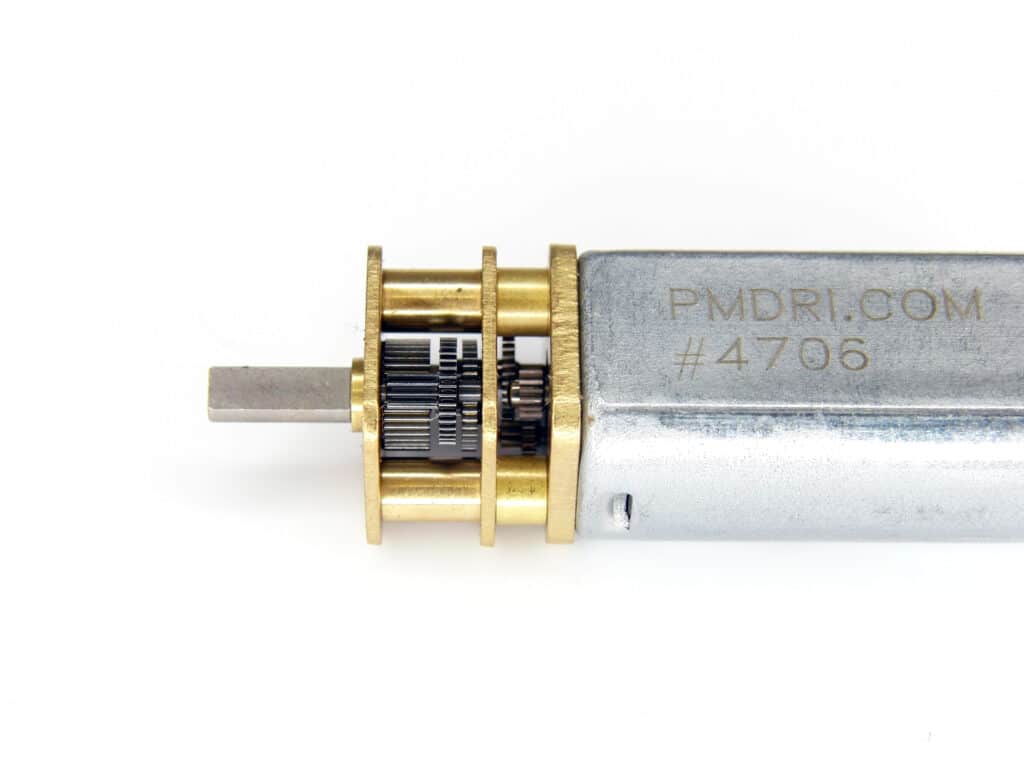
Open frame
About 1/3 of our designs use an open construction, primarily where the gearbox frame is square or rectangular.
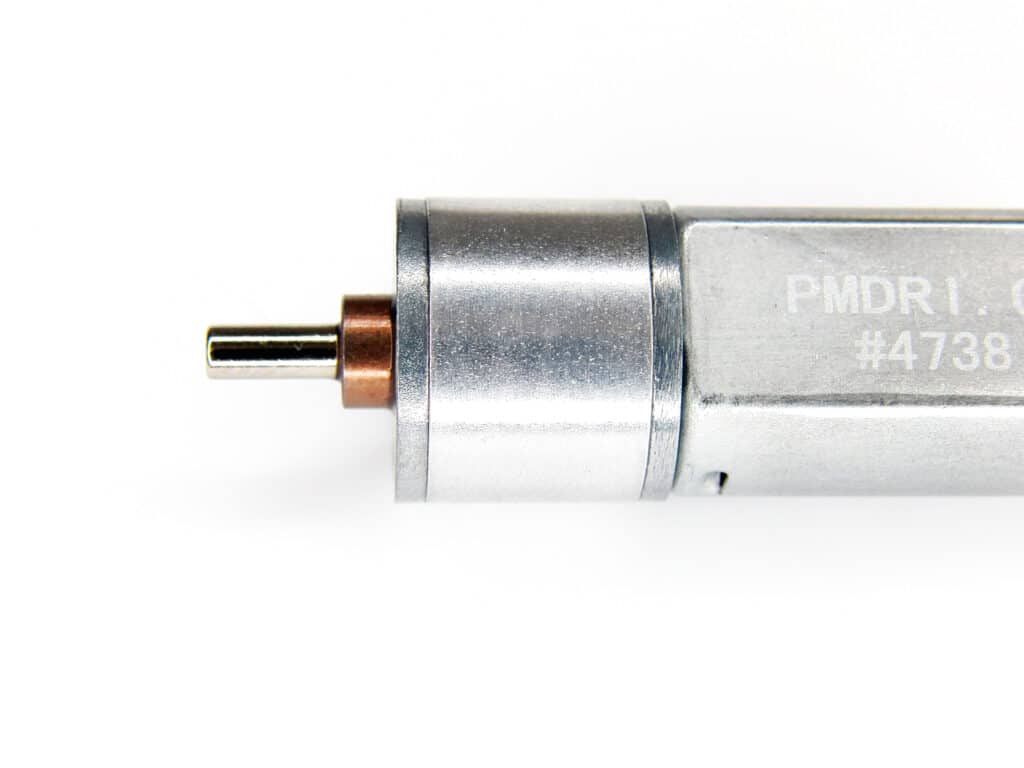
Closed frame
Other gearbox designs are circular, making it more practical to cover the gears. The main benefit is to prevent debris from entering.
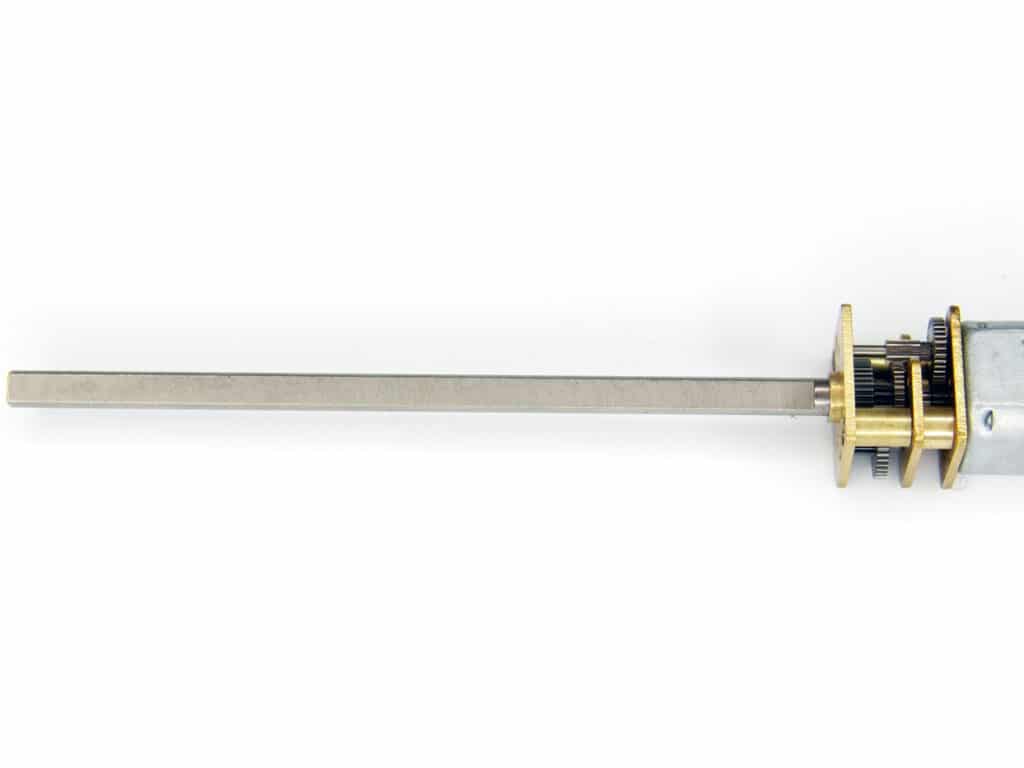
Shaft modifications
Some applications need specific shafts. Longer, shorter, d-cuts, keyway cuts, location holes and threaded shafts are all possible.
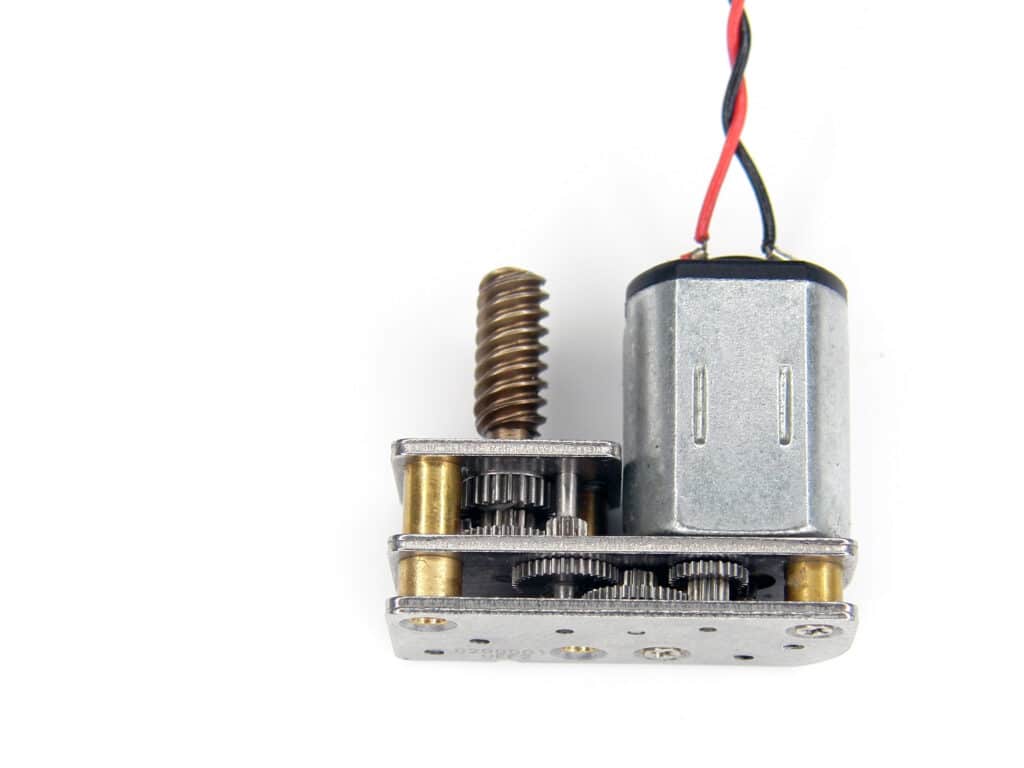
Offset and foldback gearboxes
If space is tight in the length dimension, consider a fold-back gearbox, or a non-concentric offset gearbox shaft.
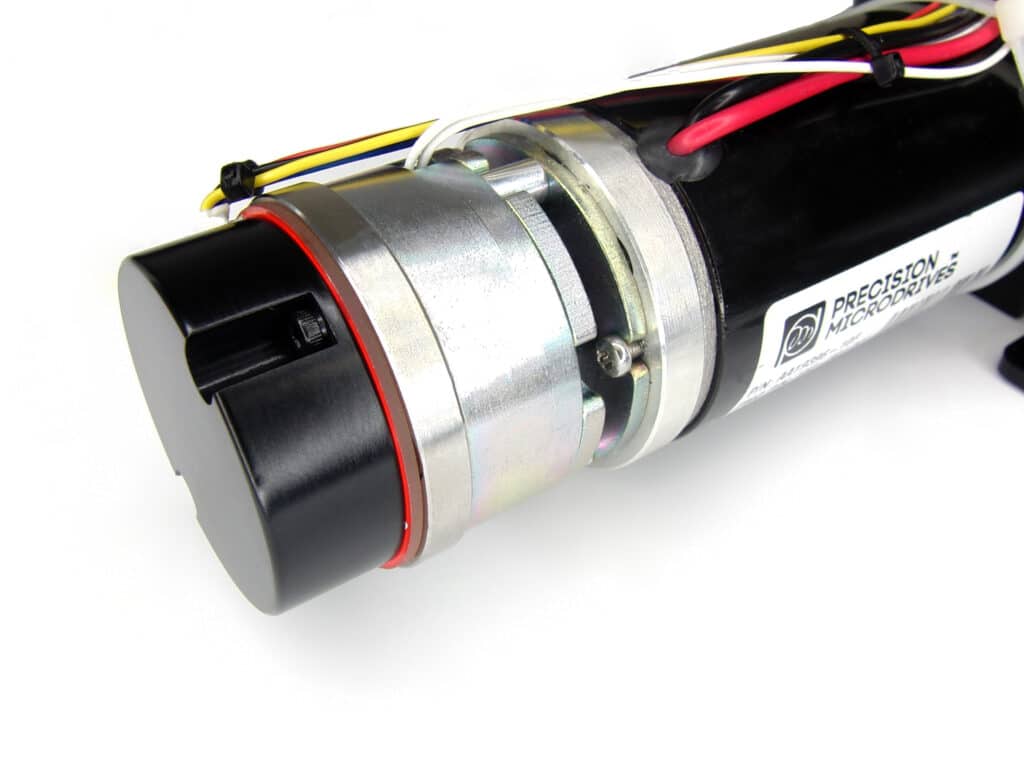
Clutches and mechanical brakes
Clutches can disengage the gearbox from the application. Mechanical brakes can lock the gearbox shaft in a ‘park’ position.
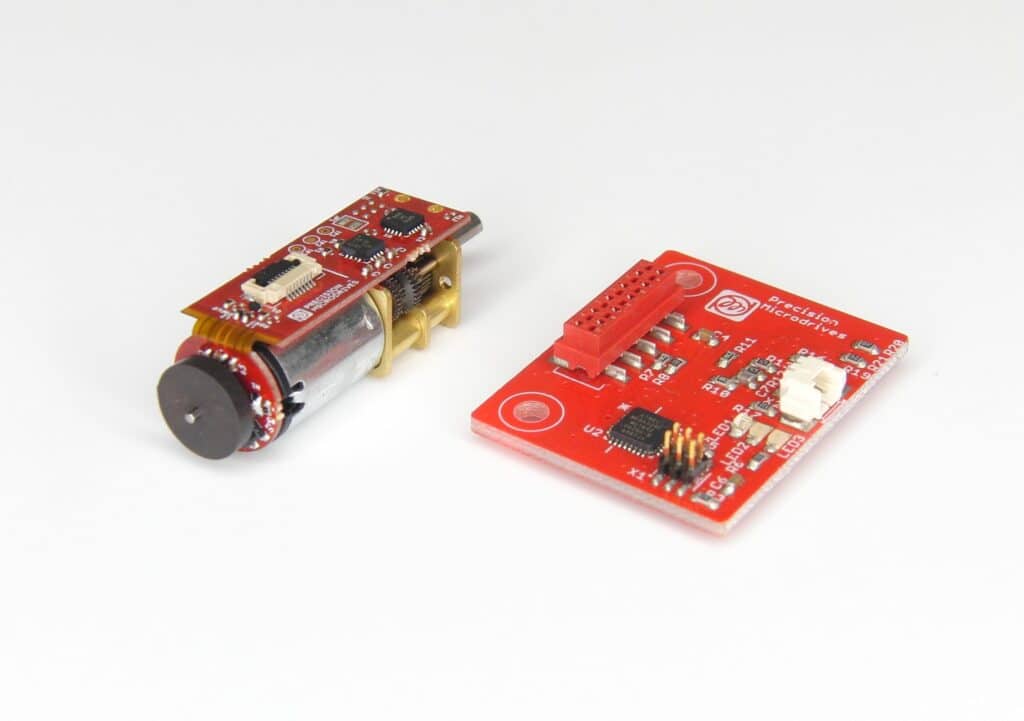
Advanced motion controllers
Precision movement is sometimes necessary, but motion controllers can also significantly extend gear motor service life.
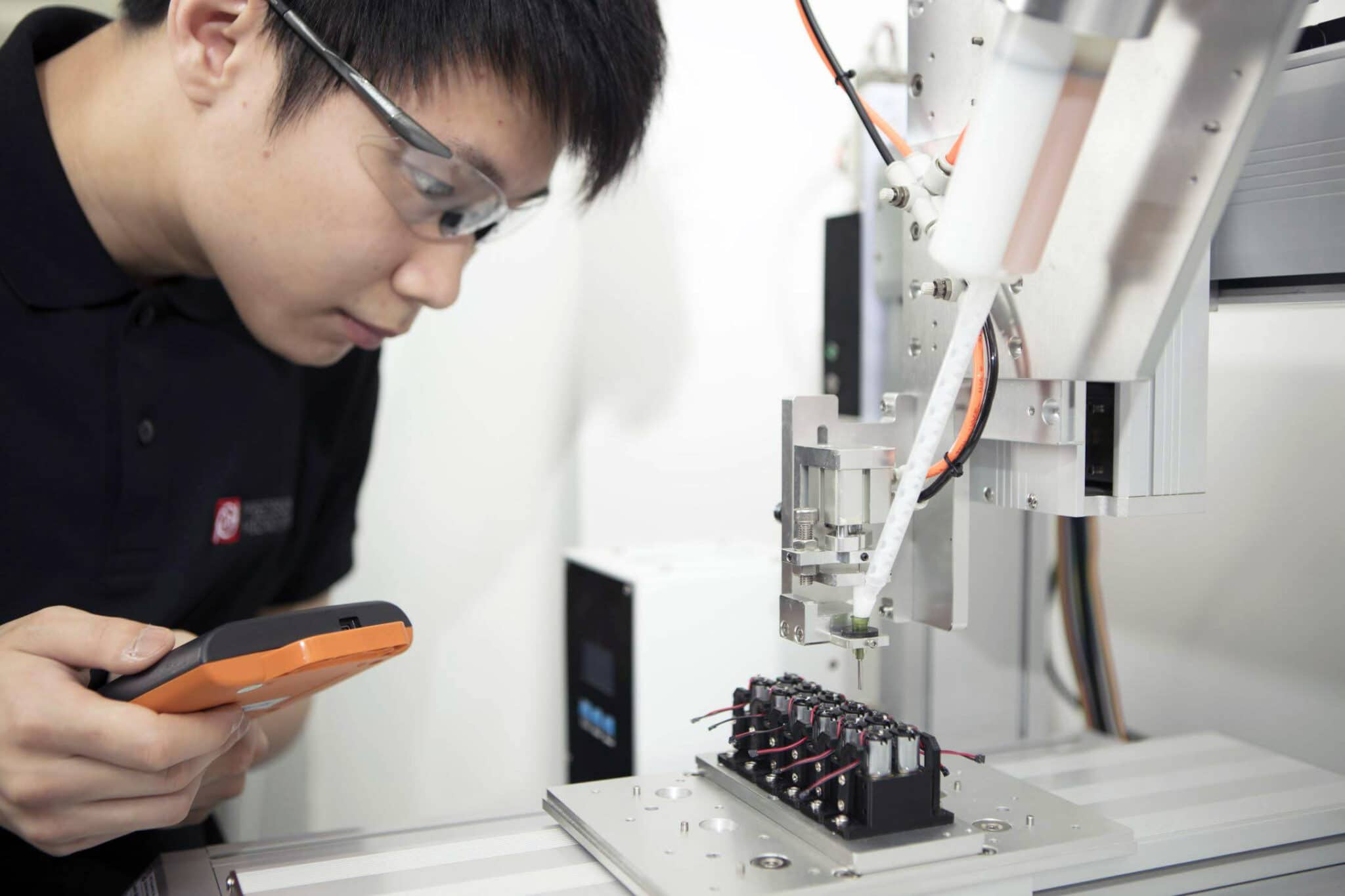
MORE THAN YOUR AVERAGE MOTOR SUPPLIER
Precision mechanisms
Innovative and optimised mechanism design for application
Application case studies
Our DC Gearmotors are used throughout many applications and industries. Learn more about typical application uses and examples we have worked on.
Accurate instruments with DC gear motors
The motors for instruments, measuring and testing equipment needs to be reliable, concise and consistent, requiring a high amount of accuracy and power.
Precision DC gearmotors can also be used for small fluid pumps, rotating trays in sterilisers and other automated laboratory functions.
Our products have the variable speed and torque control required in healthcare settings but also possess high-quality characteristics, such as reliability, ruggedness and compactness.
Case study | medical laboratory testing equipment
Our customer was challenged in designing a new Food and Drugs Administration (FDA) Class II medical laboratory testing device, requiring a new motor mechanism.
We were tasked with designing a high-precision mechanism to position a sensor within a piece of medical analysis equipment.
Our mechanism solution, capable of micron-accuracy, was based around a miniature 12mm gear motor, high accuracy encoders, and an integrated alignment motion control system.
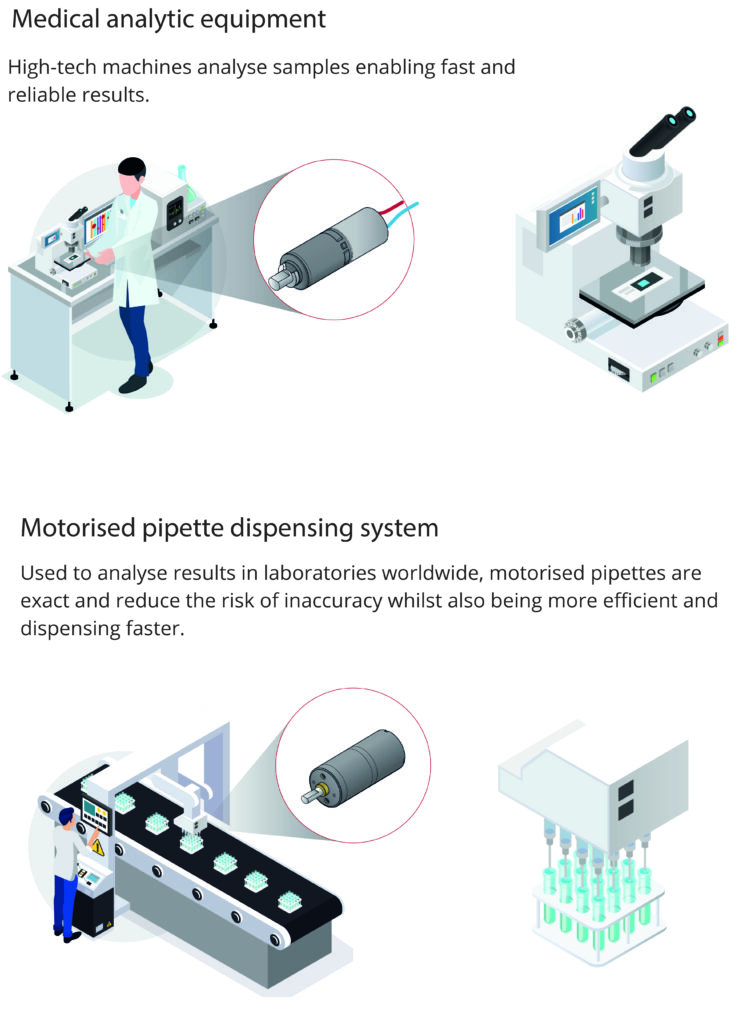
Gear motor for consumer applications
Movements controlled by motors are found in many consumer applications, making everyday living easier and more comfortable.
With more intelligent design in demand for consumer devices becoming the norm, choose a reliable design and manufacturing partner.
Case study | smart home
Our customer created an initial design for a solar-powered, smart-enabled motorised control access system for operating home devices like locks, windows and blinds.
They required a motor to drive the system but after reviewing their design, we discovered the overall concept was costly, large and over-engineered.
Our engineers designed a complete motorised mechanism solution to control window blinds. In comparison with other existing solutions in the market, we introduced a brushless option to increase the efficiency and reliability of the system.
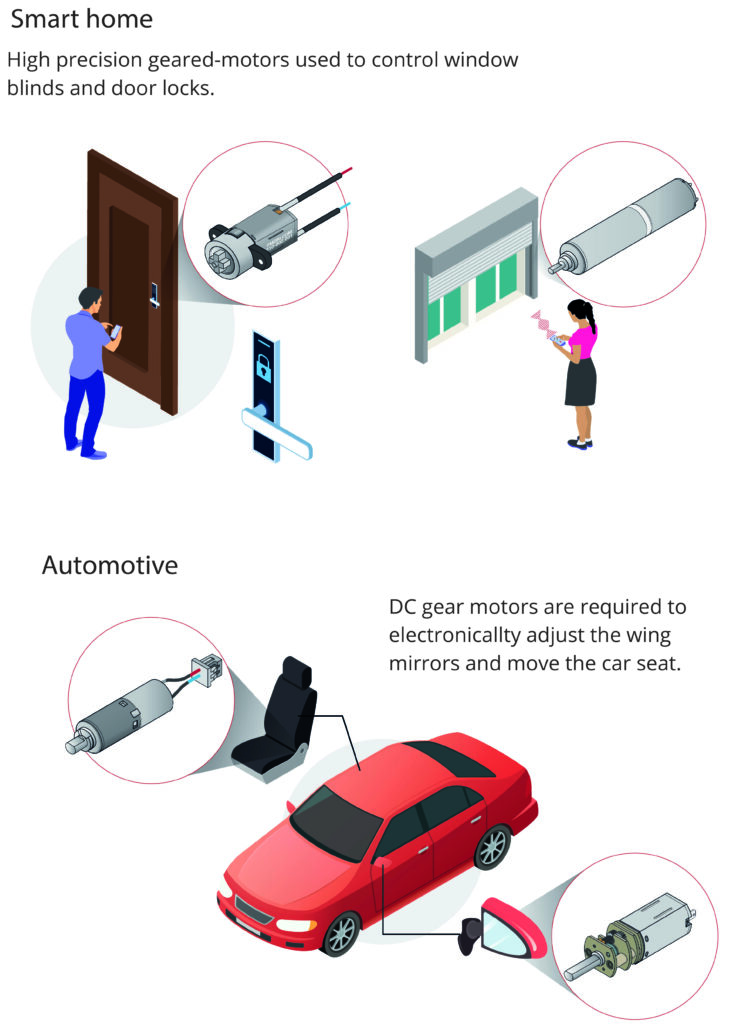
Medical and healthcare applications for DC gearmotors
Our DC gearmotors are professionally designed for use in critical medical applications, whether they are intended for surgical, clinical or laboratory settings. These geared motors are used to give applications greater accuracy and control to manoeuvre a delicate tool or an instrument with precision.
Case study | electronic inhaler
Our customer was designing a new respiratory dispensing device.
The precision gear motor solution was designed with a customised winding for 6v operation and an unusual 7.5 degree commutator advancement, to enhance the drive torque in the forward direction.
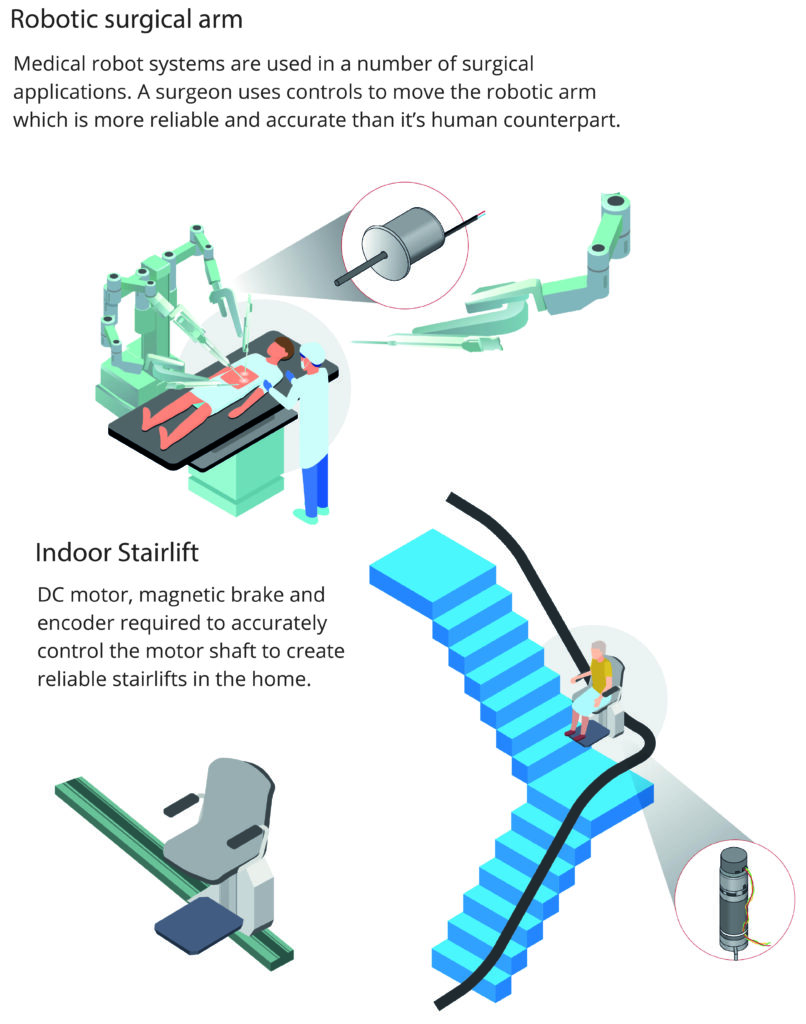
Powerful industrial applications
DC gearmotors are excellent options for power and drive applications.
Addressing the needs of power and continuous drive applications, the geared motors exert medium to high torques (for example, 500 mNm to 7000 mNm) to avoid overdriving the motor under load. The gearmotors maintain controlled speeds through continuous and periodic loading throughout the operating duty.
Typical industrial applications include mixers or stirrers, drive belts and production lines.
Case study | road traffic crossing system
The customer came to us as they wanted to reduce the cost of their existing product. We manage to reduce it by 40% and at the same time improve the product they were getting by introducing a long life brushless motor, instead of their previous brushed option.
We designed a product that could be retrofitted in their existing units, ensuring a smooth transition for the customer.
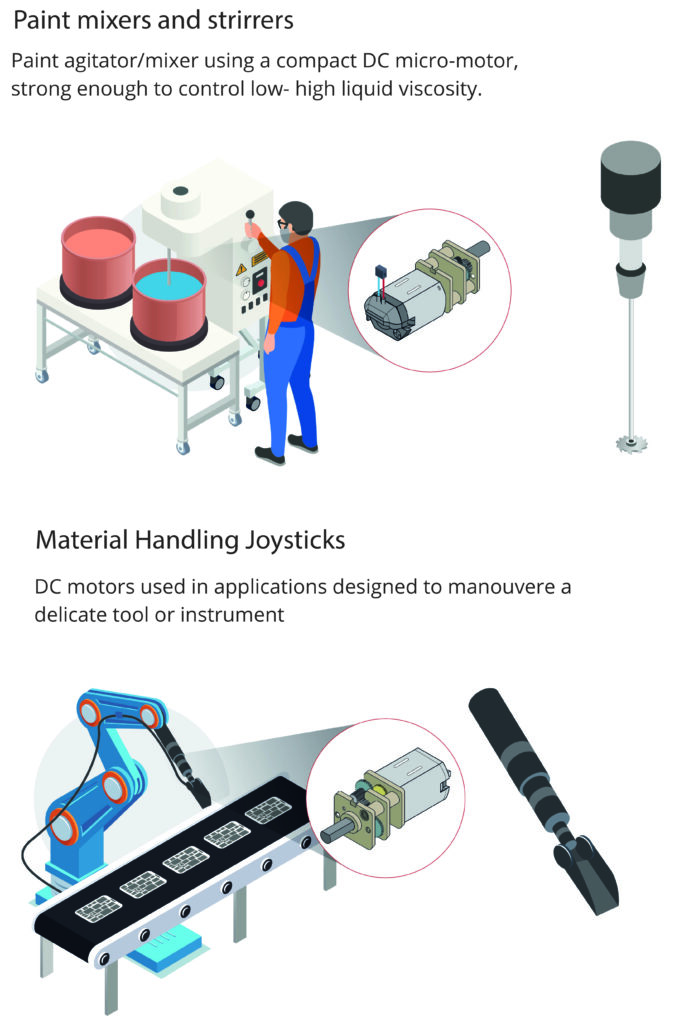
HOW CAN WE HELP?
We add value to your device through
Custom assemblies
Longevity testing
Mechanism design
Engineering confidence
In-house production
Full testing validation
PRECISION PROCESSES
Our capabilities
We can support you through the whole journey from prototype to high volume cost-effective mass production:
MOTORS & MECHANISMS
Precision products
Verified and reliable precision products perfect for your application.
-
Brushless Motors
We offer a comprehensive range of DC brushless motors in both slotted and slotless (high torque and negligible cogging) designs, with matching gearboxes, commutation sensors, and encoders.
View Page
-
Haptic feedback
Practical and reliable, low noise and high quality haptic feedback solutions for all types of application user interface.
View Page
-
Mechanisms
Custom motor assemblies designed and manufactured to your requirements. A turnkey service from design inputs to mass production.
View Page
-
DC motors
Iron-core, coreless and brushless DC motor technologies in a wide range of form factors and sizes, with off the shelf sampling.
View Page
-
Vibration motors
With every vibration and haptic technology covered, we’ll help you select the best vibrating solution for your application.
View Page
-
Linear actuators
Precise, reliable and highly customisable linear actuators designed for a wide range of industrial, commercial and medical applications.
View Page
Discover more
Resources and guides
Discover our product application notes, design guides, news and case studies.
- VAB-02: How Do Vibration Motors Work?
- AB-008: Vibration Motor Best Practices From Mobile / Cell Phones
- AB-015: Mechanical Mounting For Vibration Motors
- AB-030: Extending Vibration Theory – Displacement And Dissipation
- AB-010 : Mounting Vibration Motors To Flexible Materials & Clothing
- AB-018: Driving Brushless Long-Life Vibration Motors
Vibration motor case studies
Explore our collection of case studies, examples of our products in a range of applications.
Precision Microdrives
Whether you need a motor component, or a fully validated and tested complex mechanism – we’re here to help. Find out more about our company.