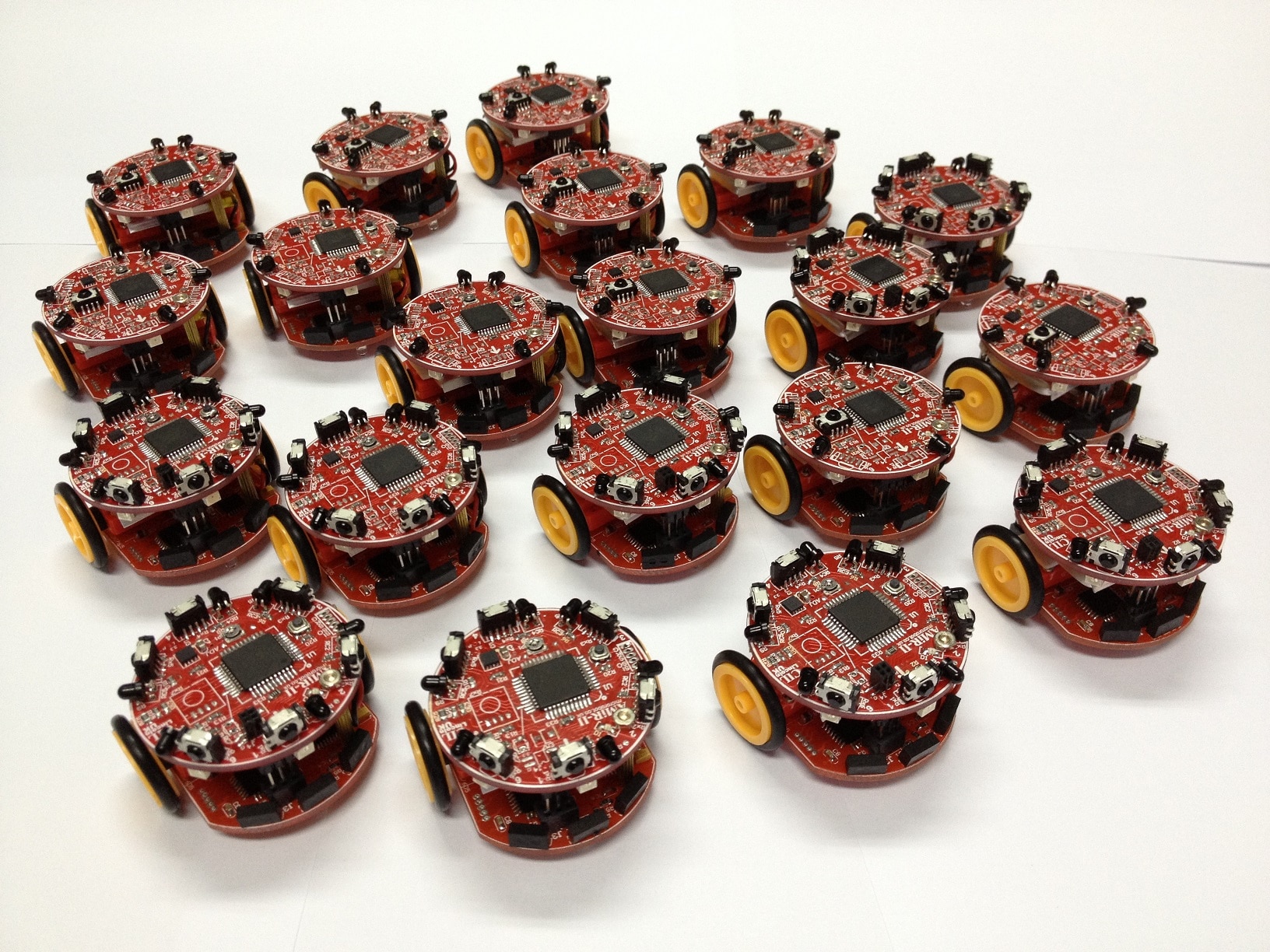
Case study
Swarm robot research linear actuator
- European robotic research Institution.
- Micro linear actuator servo.
- 7mm coreless motor with a custom lead screw and positional sensors.
Challenge
- A mass producible, highly cost-effective, miniature linear actuator with absolute positional feedback.
- The linear actuator had to be able to produce 0.25N of dynamic force, and would be used to open and close the grabbing jaws built into the front of each robot.
- Constrained by an awkward securing footprint from a much more expensive supplier’s actuator.
Solution
- Our team developed an actuator and based the design around a 7mm coreless 3v motor, with a custom D-shaft to take the pinion gear.
- Further gearing was added to amplify torque and a custom-lead screw was manufactured.
- The chassis, output arm, and pinion gears were injection moulded in engineering plastics.
- We added a very cost effective absolute positional feedback mechanism and integrated it into the chassis PCB.
Results
- Positional feedback was a real challenge, but accomplished elegantly and reliably.
- Developed an innovative solution and created an end-of-line testing station to validate and serialise each unit.
- Precision Microdrives’ testing infrastructure allowed us to assure our customer that their manufacturing risk was manged throughout.
- Every production batch was delivered on time and to spec.
Project scope
Challenging technical and unique application for swarm robotics
Current robotics research is generating some very unique applications and one particularly interesting field is ‘swarm robotics’.
These applications seek to mimic the behaviour of simple creatures such as ants where the intelligence is observable at the swarm / group level. Our customer for this project was a European research institute that required a mass-producible, highly cost-effective, miniature linear actuator with absolute positional feedback.
The linear actuator had to be able to produce 0.25N of dynamic force and would be used to open and close the grabbing jaws built into the front of each robot.
The customer’s earlier prototypes had used an alternative unit from a Swiss supplier, but this was not suitable for the final build of 5000 swarm robots due to cost and manufacturing lead-time. We designed-in a replacement to hit all of the specification targets, whilst maintaining the awkward legacy footprint of the previous actuator.
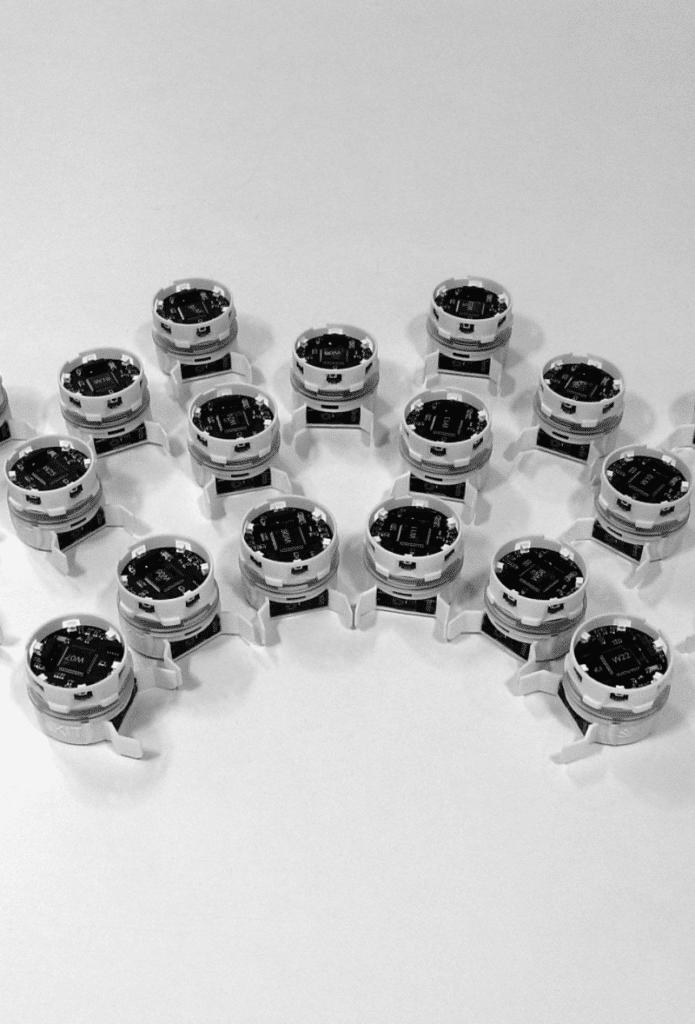
STAGE 1
Designing for application
- The application required us to push / pull a 1mm shaft and there was a requirement for manual adjustment / alignment during the final robot assembly.
- We developed our application-specific actuator in Solidworks, and based the design around a 7mm coreless 3v motor, with a custom D-shaft to take the pinion gear.
- The chassis, output arm, and pinion gears were injection moulded in engineering plastics.
- The lead-screw was based on a M2 thread, and further machined to produce a trapezoid profile to prevent sticking when higher forces were applied.
- The lead-screw was supported by miniature sintered bearings at either end of the chassis.
STAGE 2
Design for manufacture
- To offer absolute positional feedback in this package and budget, was a real challenge.
- We solved this by creating a linear potentiometer on the PCB, which also acted as a mounting base for the injection moulded frame.
- Almost half of the project hours were devoted to performing detailed DFM to reduce part-count and manufacturing costs.
- Detailed planning, lifecycle management and statistical controls allowed us to work hand-in-hand with the customer to develop – plan – produce and manufacture.
STAGE 3
Precision performance
- We also designed a driving algorithm for our customer to implement in their motion control software. This prevented lead-screw lockup.
- On the line we built an end-of-line testing station to 100% test, characterise and serialise each device for positional calibration.
- PMD’s testing infrastructure allowed us to assure our customer that the product was validated and we managing their manufacturing risk throughout.
- Every production batch was delivered on time and to spec.
CASE STUDIES
We supply motor and mechanism solutions for all sorts of applications
-
Medical patient simulator
Patient simulator for first-aid cardiac arrest training required a vibration motor to haptic simulate a heartbeat.
View Case Study
-
Bench-top pill counting machine
Bench-top medical instrument used a vibration motor to aid movement of pills through instrument pathways.
View Case Study
-
Weather balloon measurement lab
High volumes of low-cost reliable single-use motors for weather balloon measurement lab.
View Case Study
-
Emergency services ruggedised radio
Emergency radios to withstand high temperatures, impacts, and vibrate through protective clothing
View Case Study
-
Surgically implanted pacemaker motor
Brushless vibration motor within a FDA Class III implanted medical pacemaker device.
View Case Study
-
Handheld water analysis device
Handheld water spectrophotometry analysis instrument required a 4mm micro DC motor used to rotate miniature mirror plate.
View Case Study
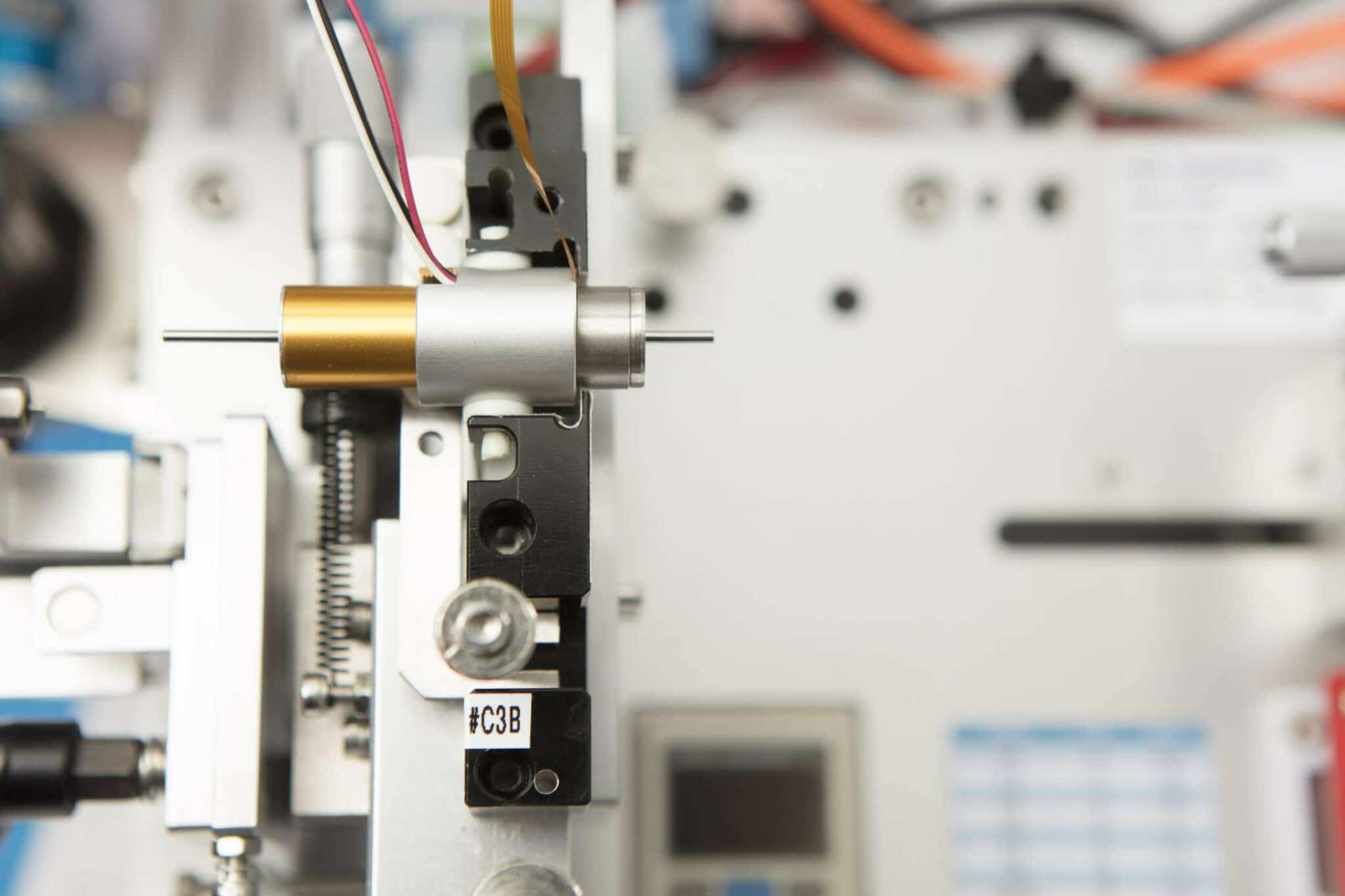
MORE THAN YOUR AVERAGE MOTOR SUPPLIER
We manage your risk
We manage your risk through optimised design and rigorous testing, protecting your application and intellectual property, fulfilling your performance requirements whilst reducing your lifecycle costs.
MOTORS & MECHANISMS
Precision products
-
DC gear motors
Building on our range of DC motors, we integrate spur and planetary gearboxes, from 6mm to 60mm frame diameters.
View Page
-
DC motors
Iron-core, coreless and brushless DC motor technologies in a wide range of form factors and sizes, with off the shelf
View Page
-
Vibration motors
With every vibration and haptic technology covered, we’ll help you select the best vibrating solution for your application.
View Page
-
Haptic feedback
Practical and reliable, low noise and high quality haptic feedback solutions for all types of application user interface.
View Page
-
Mechanisms
Custom motor assemblies designed and manufactured to your requirements. A turnkey service from design inputs to mass production.
View Page
Discover more
Resource and guides
Discover our product application notes, design guides, news and case studies
Industries we serve
At Precision Microdrives we design and manufacture customised electric motors and mechanisms across a number of industries.
About PMD
Whether you need a motor component, or a fully validated and tested complex mechanism – we’re here to help.