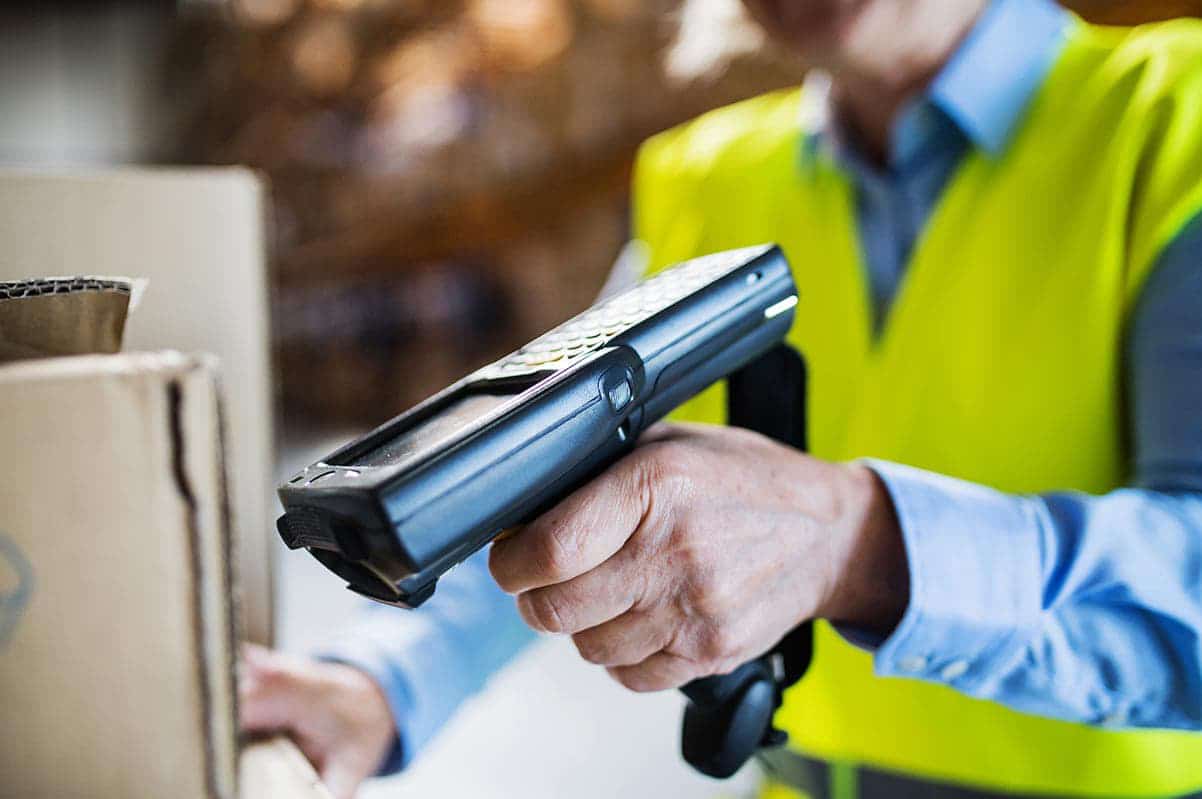
Case study
Industrial handheld barcode scanner
- Next generation, multi-purpose, handheld barcode scanner.
- Vibration motor for vibration alerting and tactile feedback.
- Custom 45mm leads with Molex connector.
Challenge
- Our customer approached us seeking a vibration motor for their handheld barcode scanner.
- They wanted to add a vibration alerting function and incorporate on-screen haptics into the device.
- They also had a strict budget, precise motor performance requirements, and needed a motor that would withstand industrial grade knocks.
- Finally they mandated an unusual specification. The motor had to be able to withstand and operate under a thermal shock, where the environmental temperature would change from +40 to -20 degs C within less than a minute.
Solution
- We designed and supplied a 7mm coreless vibration motor with 4g vibration amplitude.
- For production, this was customised with a molex connector and 45mm leads.
- Ruggedised drop testing went without problems (as expected).
- We used our thermal shock environmental chamber to validate that the motor would work as required, when subjected to the rapid change in temperatures, that the customer had specified. This requirement left our test engineers quite puzzled, until our application engineers explained the use case.
Results
- The motors were designed and fitted with a customised sintered bronze bearing, which was impregnated with a special type of lubricant.
- We entered into mass production and the customer launched their product.
- The barcode scanner has been so well received by their niche market, that the customer has been doubling their yearly orders since 2015.
- Our motors serve in the worlds first barcode scanner to be optimised and designed for used in hot climate frozen food factories!
Project scope
Vibration alerting and haptic feedback for a new handheld barcode scanner optimised for thermal shocks
Our customer approached us seeking a vibration motor, which could be designed into their next-generation, handheld barcode scanner, with a challenging set of environmental conditions.
They wanted to add a vibration alerting function and incorporate on-screen haptics into the device to reduce the risk of user input error. The scanner was to be used for shelf replenishment and inventory control. All fine, except that the scanner was to be predominantly used within frozen produce warehouses.
In hot countries the repeated transit from an outside 40°C to inside the frozen warehouse at -20°C caused many motors to fail prematurely. Firstly we discovered that the thermal cycling would draw out the grease impregnated into typical sintered bearings, leaving them unlubricated.
Secondly, condensation would form causing corrosion on the motor commutator and brushes, unless they were specifically plated.
We overcame both issues for the customer, entered into mass production, and enabled them to deliver a product optimised for a niche market.
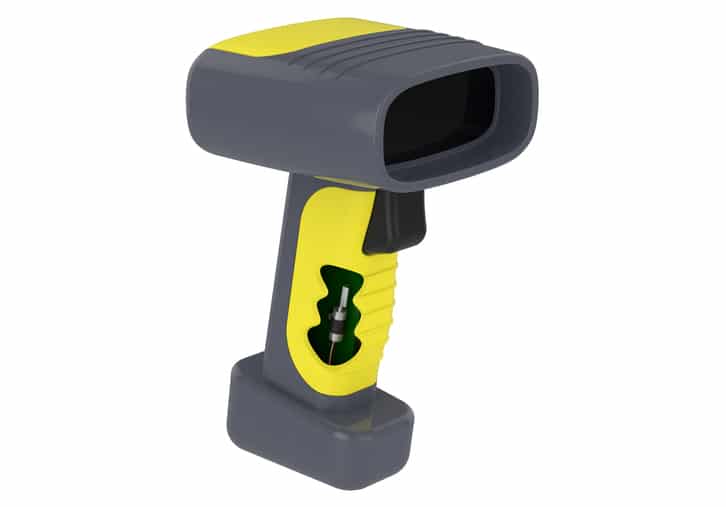
STAGE 1
Understanding the spec
- We had to understand the weight of the barcode scanner, and the motor envelope constraints.
- With those in mind, we were then able to narrow which motor frame and weight size to use.
- The thermal shock conditions were a curveball that we had not experienced, and affected the lifetime of the motor bearings.
- Whilst we understood the problem, the quickest way to solve it was to laborious cycle of trial and error testing, within our thermal shock chamber.
STAGE 2
Final design review
- We supplied them with a 7mm coreless vibration motor with 4g vibration amplitude. This was agreed with the customer to be sufficient to penetrate thermal gloves (typically worn when using this scanner).
- We customised the motor with different sintered bronze bearings with a special lubricant, gold plated brushes and a molex connector on the end of a 45mm lead.
- We supported their in-house engineering team, by allowing them to focus on other areas, whilst we solved the motor problem.
STAGE 3
Precision delivery
- When mass production started our commercial relationship changed to be with the customer’s contract manufacturer.
- We supported the contract manufacturer to resolve a few final new product introduction production issues related to the motor.
- This was of significant value to the end customer as they were able to focus on their own NPI issues, knowing that we had the vibration motor elements covered.
- The product has been so well received by their niche market, the customer has been doubling their yearly orders since 2015.
CASE STUDIES
We supply motor and mechanism solutions for all sorts of applications
-
Medical patient simulator
Patient simulator for first-aid cardiac arrest training required a vibration motor to haptic simulate a heartbeat.
View Case Study
-
Swarm robot research linear actuator
Challenging technical and unique application for swarm robotics for a European robotic research Institution.
View Case Study
-
Bench-top pill counting machine
Bench-top medical instrument used a vibration motor to aid movement of pills through instrument pathways.
View Case Study
-
Weather balloon measurement lab
High volumes of low-cost reliable single-use motors for weather balloon measurement lab.
View Case Study
-
Emergency services ruggedised radio
Emergency radios to withstand high temperatures, impacts, and vibrate through protective clothing
View Case Study
-
Surgically implanted pacemaker motor
Brushless vibration motor within a FDA Class III implanted medical pacemaker device.
View Case Study
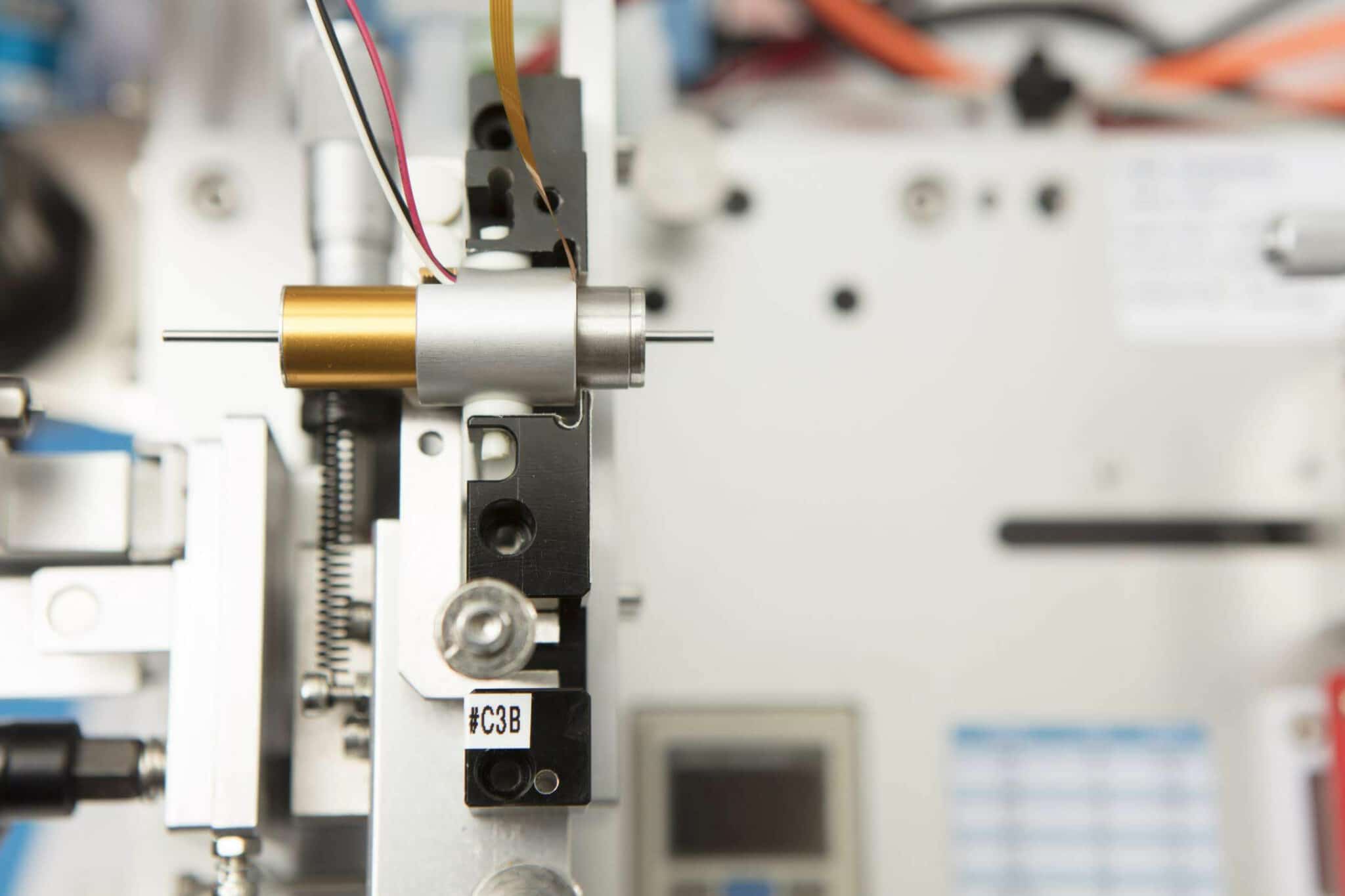
MORE THAN YOUR AVERAGE MOTOR SUPPLIER
We manage your risk
We manage your risk through optimised design and rigorous testing, protecting your application and intellectual property, and fulfilling your performance requirements, whilst reducing your lifecycle costs.
MOTORS & MECHANISMS
Precision products
From off the shelf motor components to fully validated and tested complex mechanisms, choose a motor and mechanism partner you can trust.
-
DC gear motors
Building on our range of DC motors, we integrate spur and planetary gearboxes, from 6mm to 60mm frame diameters.
View Page
-
Haptic feedback
Practical and reliable, low noise and high quality haptic feedback solutions for all types of application user interface.
View Page
-
Mechanisms
Custom motor assemblies designed and manufactured to your requirements. A turnkey service from design inputs to mass production.
View Page
-
DC motors
Iron-core, coreless and brushless DC motor technologies in a wide range of form factors and sizes, with off the shelf
View Page
-
Vibration motors
With every vibration and haptic technology covered, we’ll help you select the best vibrating solution for your application.
View Page
Discover more
Resources & guides
Discover our product application notes, design guides, news and case studies
Industries we serve
At Precision Microdrives we design and manufacture customised electric motors and mechanisms across a number of industries.
Precision Microdrives
Whether you need a motor component, or a fully validated and tested complex mechanism – we’re here to help.