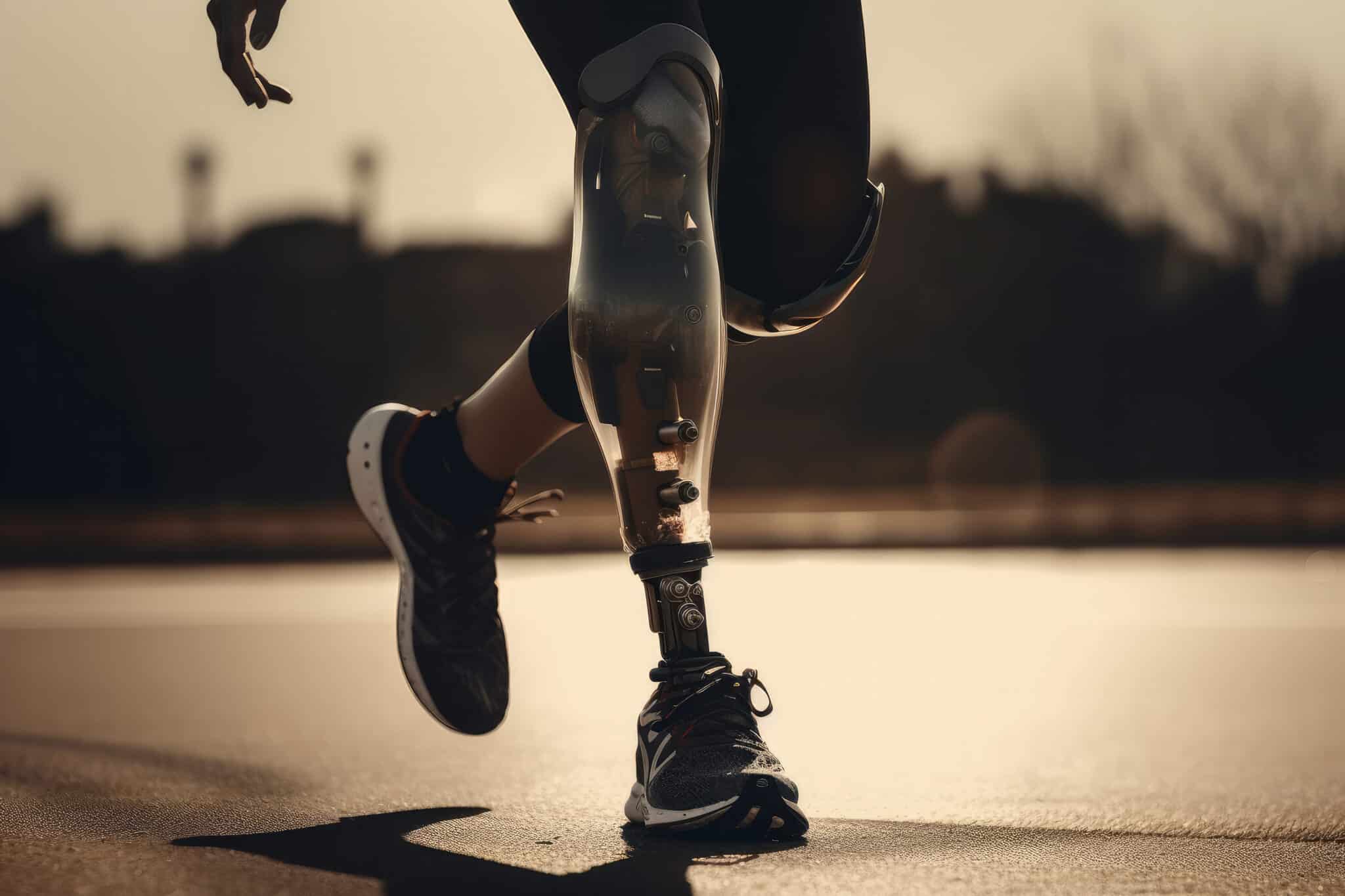
Case study
Lower limb prosthetic
- World leader in prosthetic limb technology.
- Vertically mounted vibration motors to stimulate nerve endings.
- 12mm coin vibration motor used in the lower limb replacement.
Challenge
- This customer reached out to us after they had completed the initial design work for a new concept lower limb prosthetic.
- They used the motors to stimulate nerve endings, and planned to change the orientation of the vibration motors mounted in the limb . They needed technical support, as this was the first time they had designed a limb with the motors mounted vertically, instead of in the industry standard of horizontally.
- They were also looking for a supplier who would 100% test motors against the agreed specification, and one who would share their test data ahead of sending the shipments.
Solution
- Our UK engineering team worked with the customer’s in-house engineering team to develop a detailed specification. Our Hong Kong engineering team then supported, with the motor mounting design and the motor testing protocol.
- We designed a bespoke quality control plan and supplied them with all the test data. This provided them with proof of our vibration motors’ reliability and mitigated their risk of the motors failing early.
- We designed and built a custom end-of-line tester, so that we could test every motor in the vertical orientation, ensuring that the motors would perform as specified.
Results
- The initial design stage took approximately 12 weeks to complete, and we developed and rolled out a bespoke solution to the customer’s schedule over the following 12 months. This enabled them to progress the limb into full production and on into market.
- Due to our ability to test all our motors, the customer kept us as their primary motor source and found another European company to be the second back-up supplier.
- The recipients of the new limb have been impressed with both the comfort and the realistic nerve sensations, that their prosthetic limb is now providing them with.
Project scope
Vertically mounted coin vibration motors used in a lower leg prosthetic limb
Our customer, a well-respected prosthetic limb manufacturer in the DACH region, reached out to us as they had designed and carried out some preliminary work on a new concept for a lower leg prosthetic limb.
They had tested a selection of vibration motors and decided that they wanted to use coin vibration motors with a lower than normal start voltage. They also wanted to mount the motors vertically in the prosthetic limb instead of in the standard horizontally position. They realised that their in-house engineering team needed some additional technical support, as this was a new concept in prosthetic design.
Another key requirement from the customer was their partnering supplier needed to 100% test all motors ahead of shipping them. This was to mitigate the risk of faulty motors on the production line, or early motor failure with the end limb user. 100% testing of motors, is not standard practice for the majority of vibration motor manufacturers.
Our UK engineering team spent 12 weeks supporting the customer as they worked out the limb’s specification. Our Hong Kong team then worked with their development team, and enabled the new limb to go into mass production, after a further 12 months of ramp-up. Our team also designed and built a bespoke end-of-line tester, to 100% test all our motors, ensuring they met the specification that had been agreed, for operation in the vertical orientation. Alongside the 100% testing, we developed a bespoke quality control plan, and a protocol to share all the test data.
Due to the quality of our vibration motors along with our ability to test every batch, the customer decided to make us their primary source supplier.
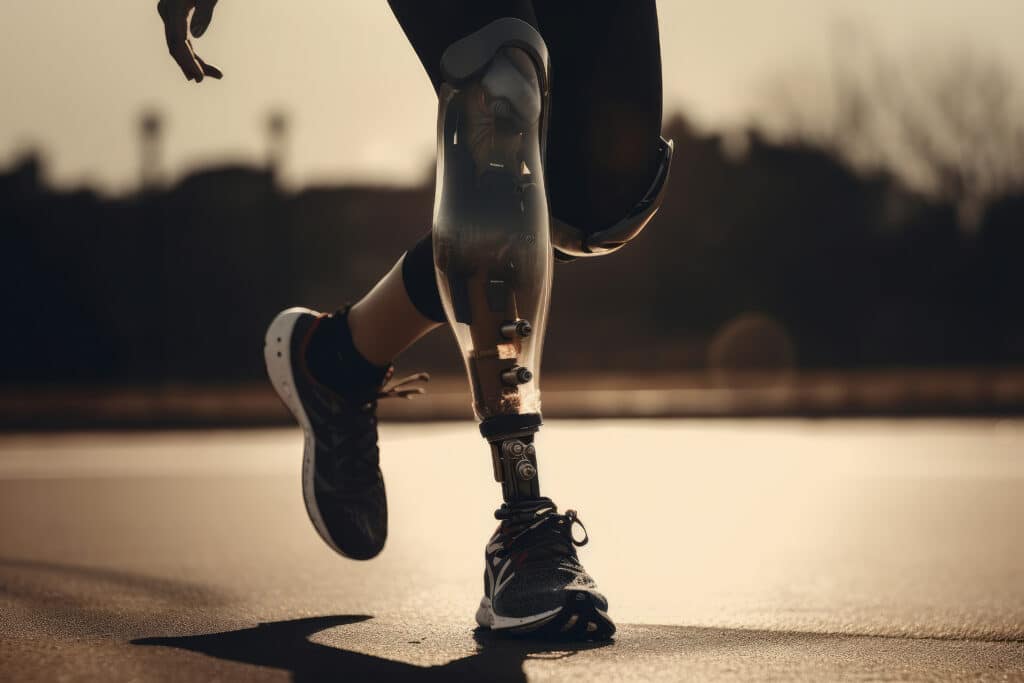
STAGE 1
Designing for application
- They were looking for technical support, to enable them to realise a new motor mounting method for lower limb prosthetics.
- The motor needed a lower than normal start voltage.
- A key requirement was having a supplier who would 100% test all motors ahead of shipping them, to guarantee that they would work as expected.
STAGE 2
Manufacturing and testing
- We built a bespoke jig so we could test 100% of the motors we were supplying, and record the test data. This was done with the motors in the vertical orientation.
- We developed a bespoke quality control plan to ensure the motors would work as specified, and we shared all the test results with the customer.
STAGE 3
Results and relationship
- The Bespoke solution took 12 weeks to design, and another 12 months to bring into mass production as defined by the customer’s timeline. At this point, the limb was launched into the prosthetic market.
- Due to the level of quality testing, we carried out they decided to make us their primary supplier, and we have been supplying them with coin vibration motors for over a decade.
CASE STUDIES
We supply motor and mechanism solutions for all sorts of applications
-
Medical patient simulator
Patient simulator for first-aid cardiac arrest training required a vibration motor to haptic simulate a heartbeat.
View Case Study
-
Swarm robot research linear actuator
Challenging technical and unique application for swarm robotics for a European robotic research Institution.
View Case Study
-
Bench-top pill counting machine
Bench-top medical instrument used a vibration motor to aid movement of pills through instrument pathways.
View Case Study
-
Weather balloon measurement lab
High volumes of low-cost reliable single-use motors for weather balloon measurement lab.
View Case Study
-
Emergency services ruggedised radio
Emergency radios to withstand high temperatures, impacts, and vibrate through protective clothing
View Case Study
-
Surgically implanted pacemaker motor
Brushless vibration motor within a FDA Class III implanted medical pacemaker device.
View Case Study
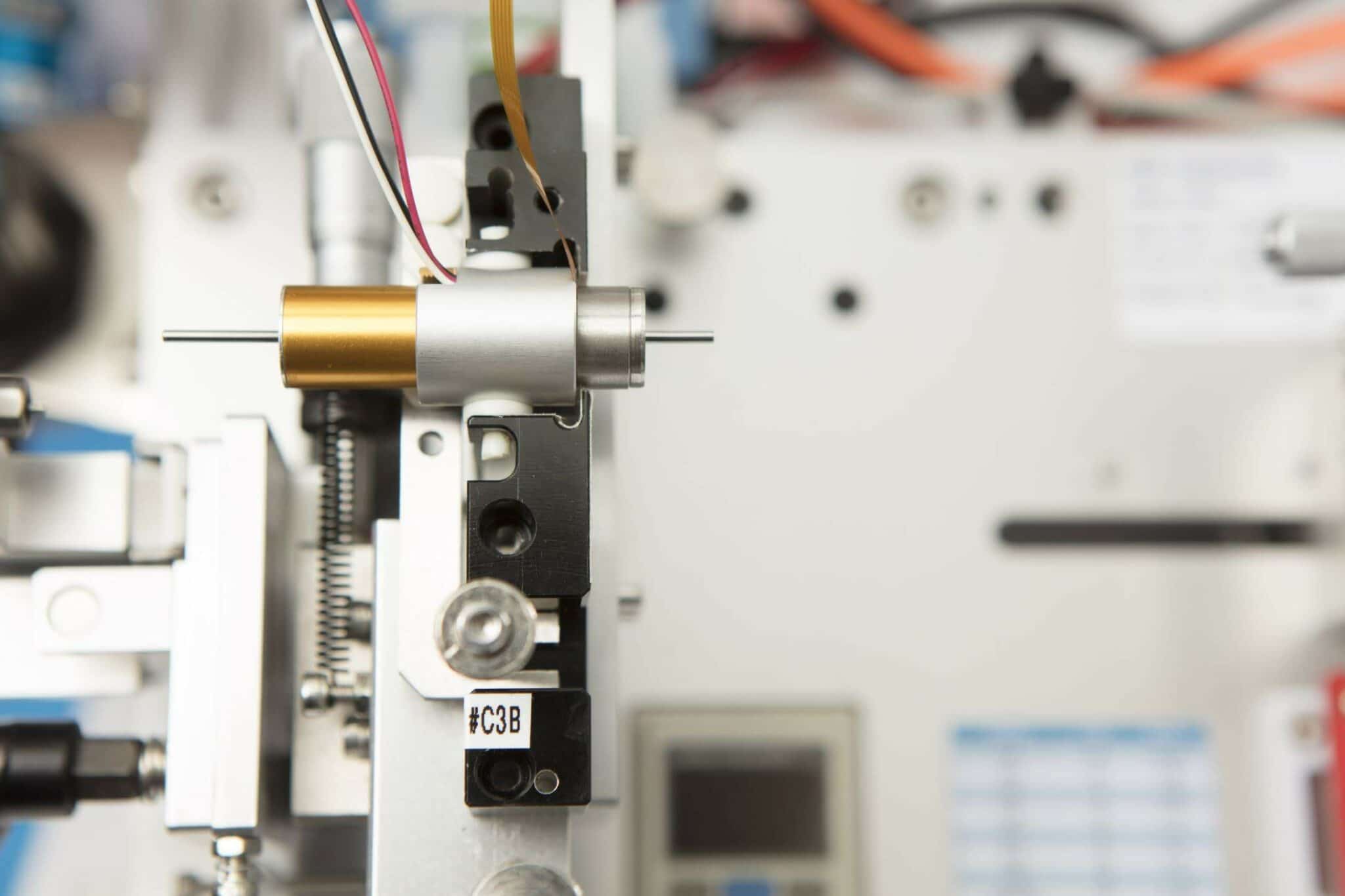
MORE THAN YOUR AVERAGE MOTOR SUPPLIER
We manage your risk
We manage your risk through optimised design and rigorous testing, protecting your application and intellectual property, and fulfilling your performance requirements, whilst reducing your lifecycle costs.
MOTORS & MECHANISMS
Precision products
From off the shelf motor components to fully validated and tested complex mechanisms, choose a motor and mechanism partner you can trust.
-
DC motors
Iron-core, coreless and brushless DC motor technologies in a wide range of form factors and sizes, with off the shelf
View Page
-
DC gear motors
Building on our range of DC motors, we integrate spur and planetary gearboxes, from 6mm to 60mm frame diameters.
View Page
-
Vibration motors
With every vibration and haptic technology covered, we’ll help you select the best vibrating solution for your application.
View Page
-
Haptic feedback
Practical and reliable, low noise and high quality haptic feedback solutions for all types of application user interface.
View Page
-
Mechanisms
Custom motor assemblies designed and manufactured to your requirements. A turnkey service from design inputs to mass production.
View Page
-
Linear actuators
Precise, reliable and highly customisable linear actuators designed for a wide range of industrial, commercial and medical applications.
View Page
Discover more
Resources and guides
Discover our product application notes, design guides, news and case studies
Industries we serve
At Precision Microdrives we design and manufacture customised electric motors and mechanisms across a number of industries.
Precision Microdrives
Whether you need a motor component, or a fully validated and tested complex mechanism – we’re here to help.