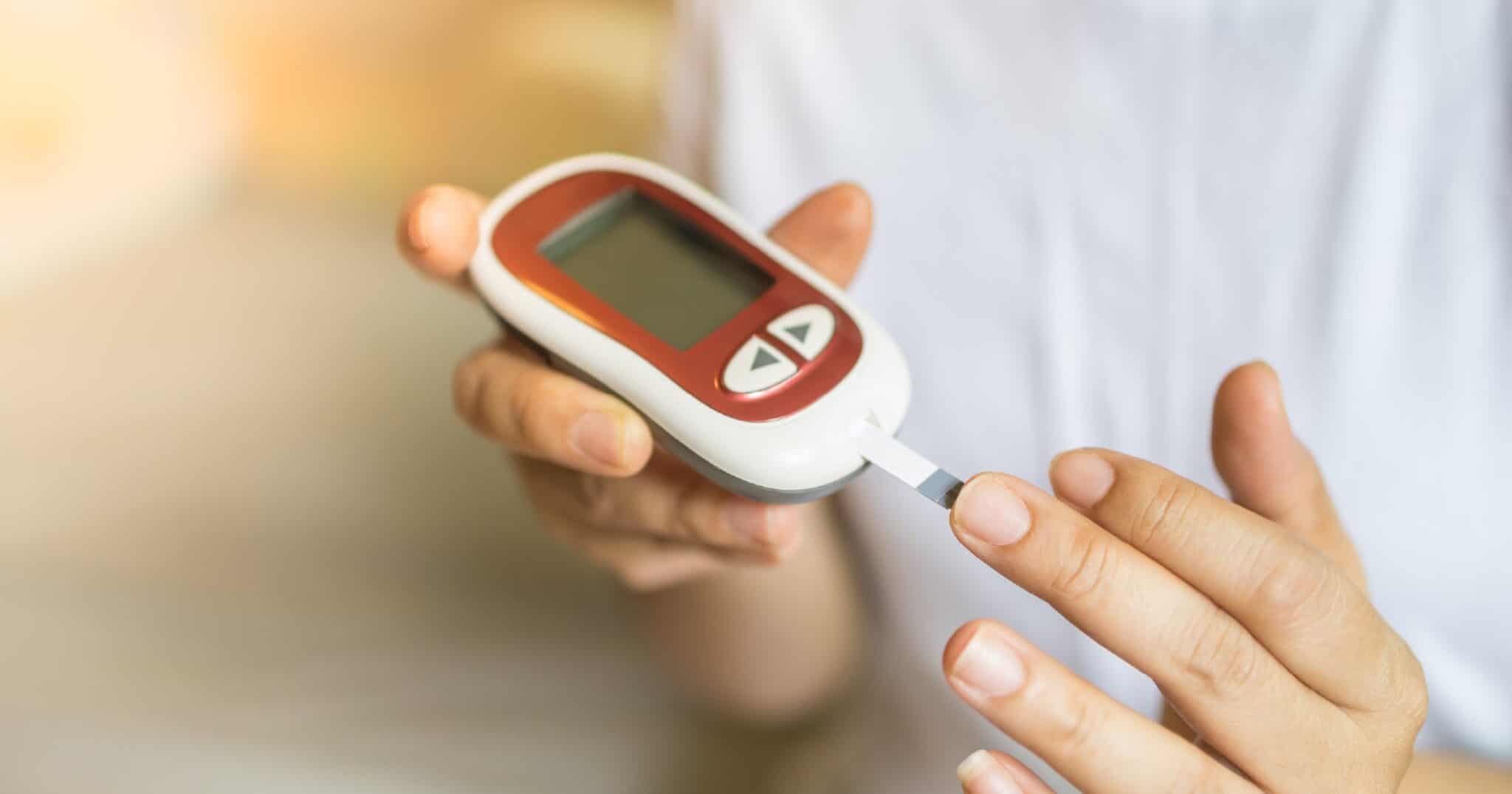
Case study
Insulin monitoring device
- FDA Class II diabetic insulin monitor already in the market, but having trouble with their existing Asian motor supplier.
- Required a bespoke vibration motor that was able to match the product’s size, performance and low current draw requirements.
- Precision Microdrives ability to design a drop-in replacement removed the need to prepare costly new FDA 510(K) paperwork.
Challenge
- Our customer approached us seeking a new vibration motor supplier, for an FDA Class II diabetic insulin monitor.
- This device, was already well established in the market, but they were experiencing an unacceptably high number of IQC motor failures, from their existing supplier.
- They also had developed a concern over the existing motor’s longevity performance, after undertaking an investigation prompted by excessive returns under warranty.
- They decided they wanted to replace the current vibration motor with one from a more robust manufacturer, and ideally a drop-in replacement.
- They revised the specifications to include a challenging longevity target.
Solution
- To deliver a drop-in replacement we had to meet a number of strict constraints. The motor had to fit the current housing as a redesign was impossible.
- The customer also had a tight constraint on current draw and vibration amplitude.
- We took an existing mechanical design and adjusted the motor’s winding to produce a bespoke vibration motor. This was able to meet their size, performance, and current draw specifications.
- We tested our proposed motor on our longevity testing machines to prove that that our solution would meet the newly specified durability requirements.
Results
- We ramped up production through a pilot and into mass manufacture. In doing so we eliminated the problems introduced by quality fade from the old supplier.
- In addition we engineered a solution to meet a more robust durability criteria, thereby greatly diminishing the number of units returned under warranty (because of motor failure) to a negligible amount.
- Because our solution was a drop-in replacement, the customer didn’t need to re-engineer any of their aluminium housings or change any of their production tools.
- Furthermore, because the drop-in replacement had an equivalent spec the customer was able to adopt the new part without a significant FDA re-submission.
Project scope
High quality, reliable vibration motor for FDA Class II diabetic insulin monitor
Our customer approached us already manufacturing a FDA Class II insulin monitor for diabetic patients. They were experiencing qualify fade from their existing supplier, as well as an unacceptable number of warranty returns, due to motor failures.
They decided to replace the current vibration motor with one sourced from a more robust manufacturer, and ideally a drop-in replacement to reduce FDA re-submission. To meet this challenge meant a number of strict constraints had to be met. The motor had to fit the current housing as a redesign was impossible. It also had to deliver an equivalent vibration amplitude, consume equivalent current, and also be proven to last longer than the old motor.
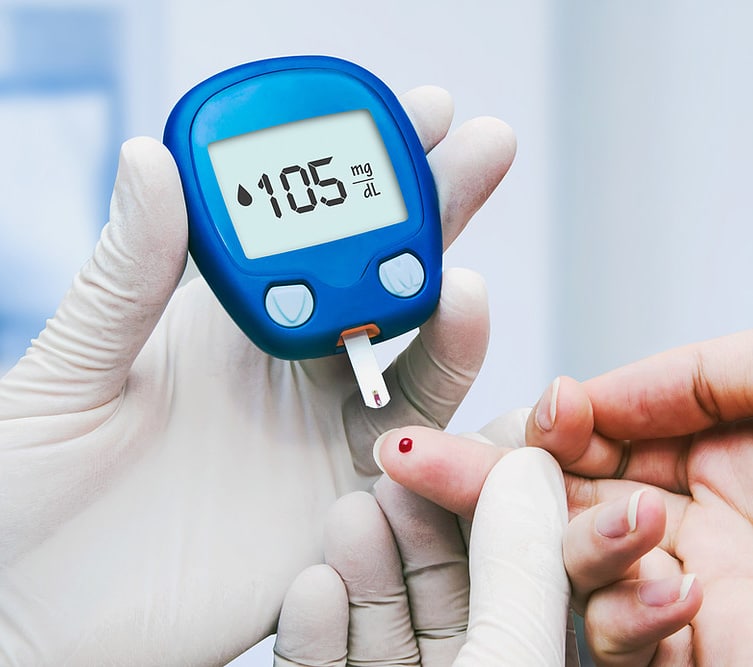
STAGE 1
Designing for application
- After analysing the device, our engineers adapted an existing motor design with a bespoke winding. We were able to manufacture a custom vibration motor that exactly matched the size, performance, and current draw specifications.
- This meant that our motor would fit directly into the existing housing and production tooling without any redesign.
- We worked with the customer to develop a suitable test profile to simulate application usage. Motors were then tested in this way for durability on our longevity testing machines.
STAGE 2
Testing and validation
- Our motor engineering expertise combined with our technical diligence, meant that our replacement solution worked far better than the original motor.
- Our client was able to use existing enclosures and tools without any modification, reducing their wastage and production costs.
- We saved the customer time and money by avoiding a resubmission to the FDA for a 510(K) clearance, which would have been costly, time consuming, and may have caused a production stop.
STAGE 3
Results and relationship
- The high number of motor failures has been eliminated, and no devices are being returned under motor failure warranty with our solution.
- All our motors are diligently quality controlled, to ensure no risk of quality fade.
- The customer was able to seamlessly transition over to our motor without any production changes.
- Overall our risk management helped them avoid an adverse impact to their brand.
CASE STUDIES
We supply motor and mechanism solutions for all sorts of applications
-
Medical inhaled medication delivery device
Intelligent medical inhaler device, which was FDA Class III approved, required a gear motor mechanism to provide precise
View Case Study
-
Medical patient simulator
Patient simulator for first-aid cardiac arrest training required a vibration motor to haptic simulate a heartbeat.
View Case Study
-
Swarm robot research linear actuator
Challenging technical and unique application for swarm robotics for a European robotic research Institution.
View Case Study
-
Bench-top pill counting machine
Bench-top medical instrument used a vibration motor to aid movement of pills through instrument pathways.
View Case Study
-
Weather balloon measurement lab
High volumes of low-cost reliable single-use motors for weather balloon measurement lab.
View Case Study
-
Surgically implanted pacemaker motor
Brushless vibration motor within a FDA Class III implanted medical pacemaker device.
View Case Study
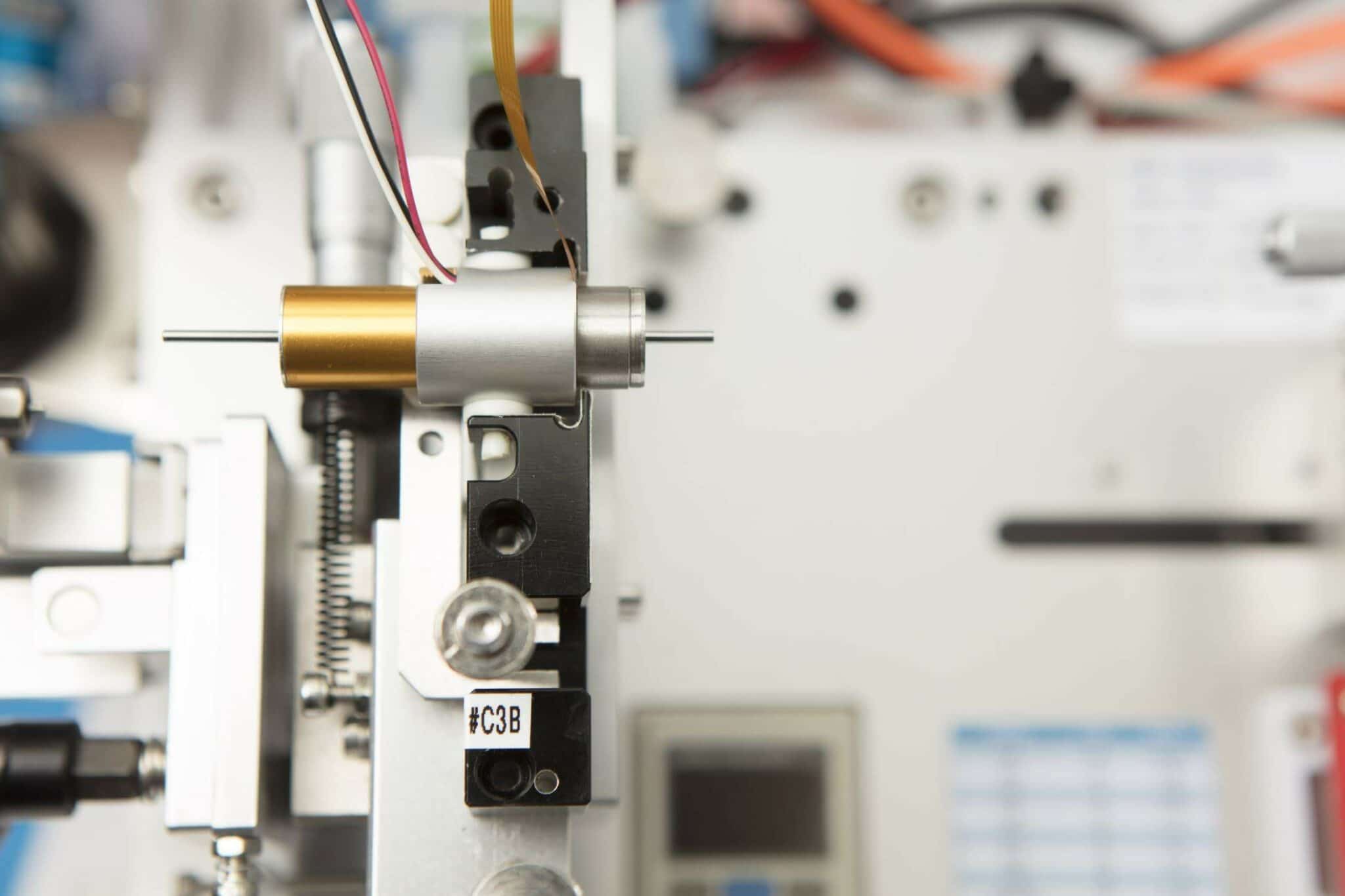
More than your average motor supplier
We manage your risk
We manage your risk through optimised design and rigorous testing, protecting your application and intellectual property, fulfilling your performance requirements, whilst reducing your lifecycle costs.
MOTORS & MECHANISMS
Precision products
-
DC motors
Iron-core, coreless and brushless DC motor technologies in a wide range of form factors and sizes, with off the shelf
View Page
-
DC gear motors
Building on our range of DC motors, we integrate spur and planetary gearboxes, from 6mm to 60mm frame diameters.
View Page
-
Vibration motors
With every vibration and haptic technology covered, we’ll help you select the best vibrating solution for your application.
View Page
-
Haptic feedback
Practical and reliable, low noise and high quality haptic feedback solutions for all types of application user interface.
View Page
-
Mechanisms
Custom motor assemblies designed and manufactured to your requirements. A turnkey service from design inputs to mass production.
View Page
Discover more
Resources and guides
Discover our product application notes, design guides, news and case studies
Industries we serve
At Precision Microdrives we design and manufacture customised electric motors and mechanisms across a number of industries.
About PMD
Whether you need a motor component, or a fully validated and tested complex mechanism – we’re here to help.