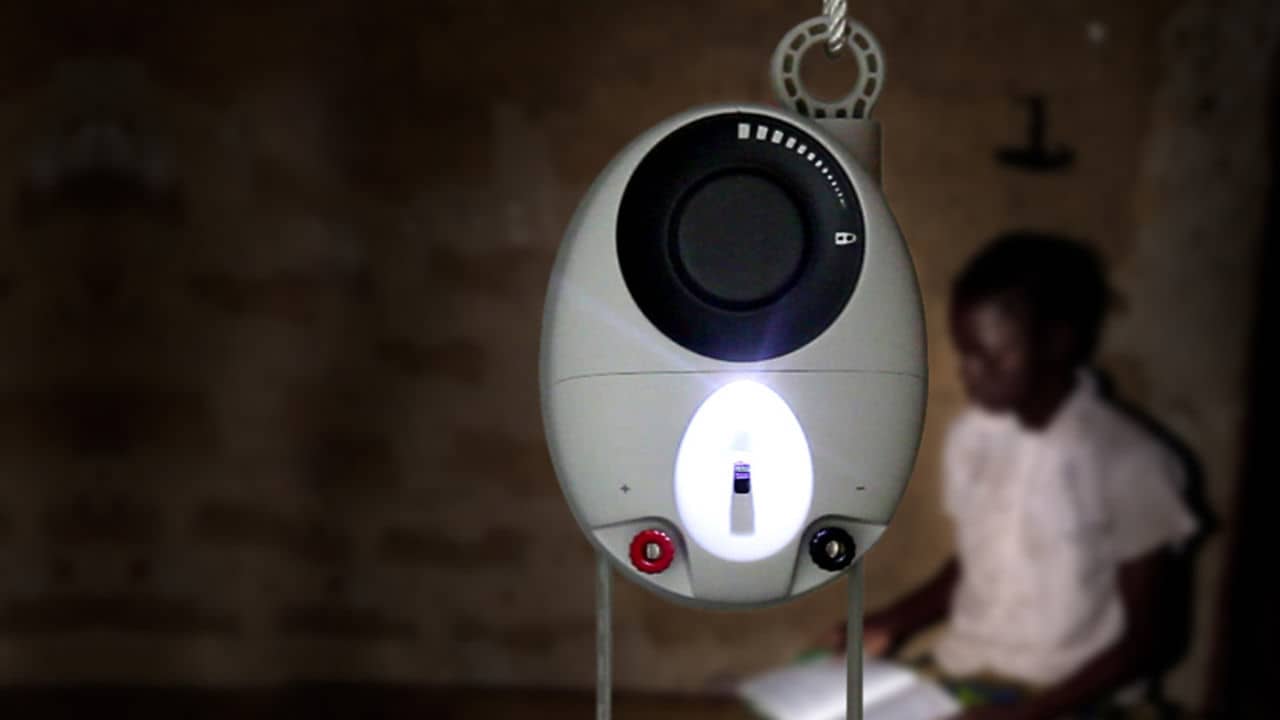
Case study
GravityLight
- New technology to provide an alternative light source to Kerosene lamps in the developing world.
- DC motor driven as a generator – our customer wanted to optimise for the best energy generation.
- Our team of engineers worked closely with the customer evaluating a unique technical challenge.
Challenge
- Kerosene lamps are still commonly used in the developing world despite the numerous financial, health, and environmental repercussions, and GravityLight is a lamp powered by the energy in a falling mass.
- Conducting a rigorous and thorough design process, GravityLight asked if Precision Microdrives could assist them in their attempts to fully characterise their prototype DC motor. After this, we worked together to optimise the performance further.
Solution
- Our team of application engineers worked with the client and performed a number of very detailed tests to characterise the DC motor used in early prototypes.
- We then redesigned the motor core and magnetic circuit, to deliver, after further dynamometer testing, an improved 32mm DC Motor which was installed in Gravity Light’s own testing equipment.
Results
- After rigorous testing, our engineering team delivered an improved motor in the same form factor, but with a higher electrical generating capacity.
- This design went into production and formed the core of their patented gravity light drive.
- With future revisions of the product, we adjusted the motor parameters yet further to support a changing load point.
Project scope
An alternative, safer and environmentally friendly lighting system for developing countries.
Our customer came to us to advise on a project they were working on: GravityLight. Kerosene lamps are still commonly used in the developing world despite the numerous financial, health and environmental repercussions, and GravityLight wanted to offer off-grid lighting in a novel way.
The concept of the GravityLight is elegantly simple. A weight is manually raised and as it falls slowly back to earth, it turns the shaft of an electric motor via a gearbox. The driving of the electric motor in reverse creates electrical energy which is then used to power an LED light and charge other items via USB. Each straightforward lift of a bag containing earth or rocks, provides the system with enough potential energy to provide approximately 30 minutes of lighting.
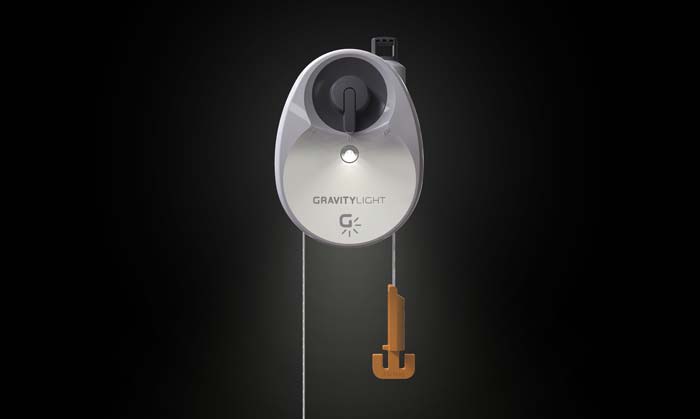
STAGE 1
Designing for application
- The first step was to fully characterise the motors used in the prototype Gravity Light units.
- The industry standard for characterising electric motors is typically to take measurements at a no-load condition and a nominal loading greater than the rated load.
- However, at Precision Microdrives we have a range of in-house dynamometers with electronically controlled loads. These create dynamic torque loadings at a range of load points. Using these we were able to prepare a very detailed spec as a target starting point.
STAGE 2
Testing
- For this project, we also created a specific one-off testing jig for driving the motors in reverse at very precise speeds and powers.
- This enabled us to understand the optimal load points of maximum electrical power generation.
- We then redesigned the core of the motor, to better match the optimal load point for generation with the available power from the gearbox unit.
- We manufactured a sample run of 32mm motors with a revised core configuration and tested. They worked very well as generators, with 24% more power output.
STAGE 3
Results and relationship
- The output power of the GravityLight might be relatively low (you would need over 20 million of them on the highest power setting to produce the same amount of power as a 2MW wind turbine!) but it’s important to remember it is being used to light only a single room. It does this at a fraction of the cost of a kerosene lamp, with no harmful fumes, and with no cost of fuel.
- That said, every little helps, and the 24% extra power our motor was able to deliver enabled the LED light to shine brighter, or for the the system to run a bit longer between re-lifting the weight.
CASE STUDIES
We supply motor and mechanism solutions for all sorts of applications
-
Medical inhaled medication delivery device
Intelligent medical inhaler device, which was FDA Class III approved, required a gear motor mechanism to provide precise
View Case Study
-
Medical patient simulator
Patient simulator for first-aid cardiac arrest training required a vibration motor to haptic simulate a heartbeat.
View Case Study
-
Swarm robot research linear actuator
Challenging technical and unique application for swarm robotics for a European robotic research Institution.
View Case Study
-
Bench-top pill counting machine
Bench-top medical instrument used a vibration motor to aid movement of pills through instrument pathways.
View Case Study
-
Weather balloon measurement lab
High volumes of low-cost reliable single-use motors for weather balloon measurement lab.
View Case Study
-
Surgically implanted pacemaker motor
Brushless vibration motor within a FDA Class III implanted medical pacemaker device.
View Case Study
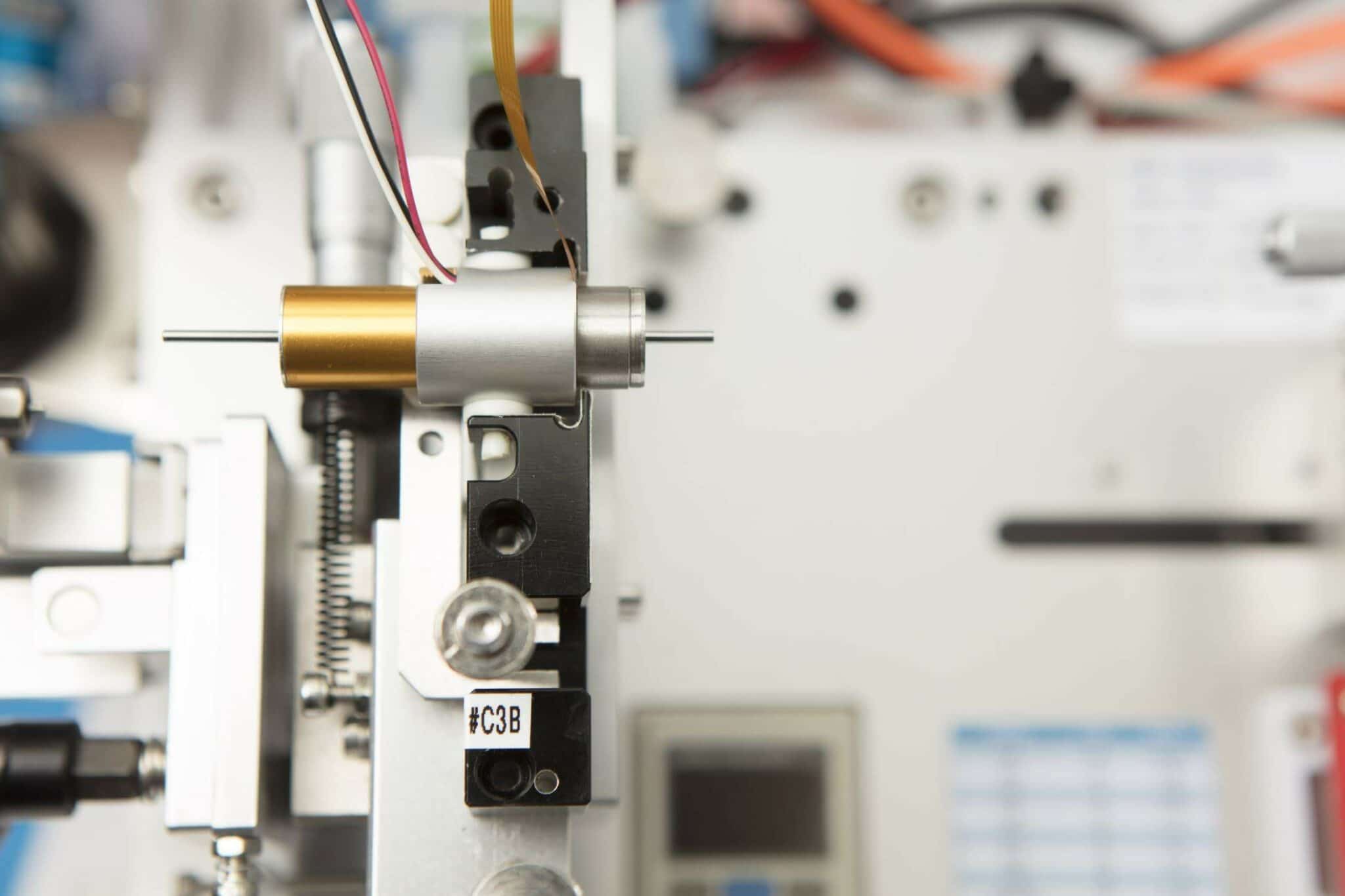
More than your average motor supplier
We manage your risk
We manage your risk through optimised design and rigorous testing, protecting your application and intellectual property, fulfilling your performance requirements, whilst reducing your lifecycle costs.
MOTORS & MECHANISMS
Precision products
-
DC motors
Iron-core, coreless and brushless DC motor technologies in a wide range of form factors and sizes, with off the shelf
View Page
-
DC gear motors
Building on our range of DC motors, we integrate spur and planetary gearboxes, from 6mm to 60mm frame diameters.
View Page
-
Vibration motors
With every vibration and haptic technology covered, we’ll help you select the best vibrating solution for your application.
View Page
-
Haptic feedback
Practical and reliable, low noise and high quality haptic feedback solutions for all types of application user interface.
View Page
-
Mechanisms
Custom motor assemblies designed and manufactured to your requirements. A turnkey service from design inputs to mass production.
View Page
Discover more
Resources and guides
Discover our product application notes, design guides, news and case studies
Industries we serve
At Precision Microdrives we design and manufacture customised electric motors and mechanisms across a number of industries.
About PMD
Whether you need a motor component, or a fully validated and tested complex mechanism – we’re here to help.