Understanding How Vibrations Are Transferred
So how does a vibration motor cause an entire object to vibrate? For eccentric rotating mass vibration motors, the unbalanced force created causes the motor to displace. The displacement is very small because the motor rotates so fast (the direction of the force changes as the mass rotates). Linear resonant actuators use the same principle of an unbalanced force, but achieve it by moving a magnetic mass on a spring.
When mounted to another object, for example, soldered to a PCB, the vibration motor now tries to move that object too. This is due to Newton’s second law:
The acceleration of a body is directly proportional to, and in the same direction as, the net force acting on the body, and inversely proportional to its mass.
$$F = ma $$
This means the PCB will be subject to the same unbalanced force as the motor’s body. They can now be considered as part of the same system. If the PCB is then housed in a plastic casing we can consider the motor, PCB, and plastic housing as a single system. Any movement in the motor’s body will be equal to the movement in the plastic housing:
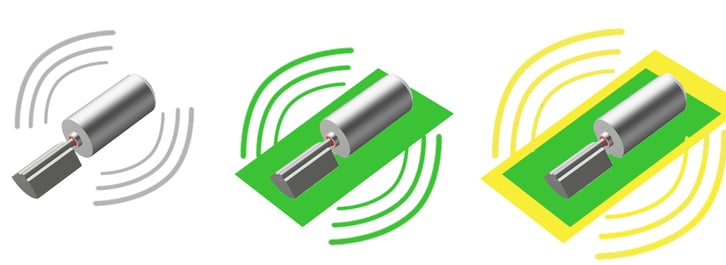
This means for a product like a mobile phone the capacitive touchscreen, battery, casing, internal PCB and every other component will be displaced by the vibration motor. Obviously heavier objects require a greater force to cause the same displacement or vibration amplitude (which is measured in G and a unit of acceleration). This is why when using a tool like our Quick Vib Estimator you need to supply the ‘Target Mass’ to calculate the output.
Of course, this only considers rigid materials with secure mounting, what happens if we mount the motor to something flexible like foam? Well if the material can compress, some of the displacement is absorbed and the full displacement from the motor is not transferred:

This makes the vibration strength feel weaker. Similar effects can be experienced if using a large PCB that is only supported at the sides, the flexibility in the middle will absorb some of the movement.
However, this is not always a negative effect. Using softer materials can aid performance by removing audible noise, caused by movement between the motor and a rigid surface.
It also leads to the theory of mechanical isolation. Say you are looking to vibrate a particular section of a system, but not the whole thing. For example a user interface on a car dashboard – but not the entire car, or a chute/hopper – but not the entire machine. We can isolate the sections we want to vibrate by using softer materials, like silicon or rubber, to separate them from the rest of the system. With the localised vibrations, we no longer need to account for the entire system in our target mass.
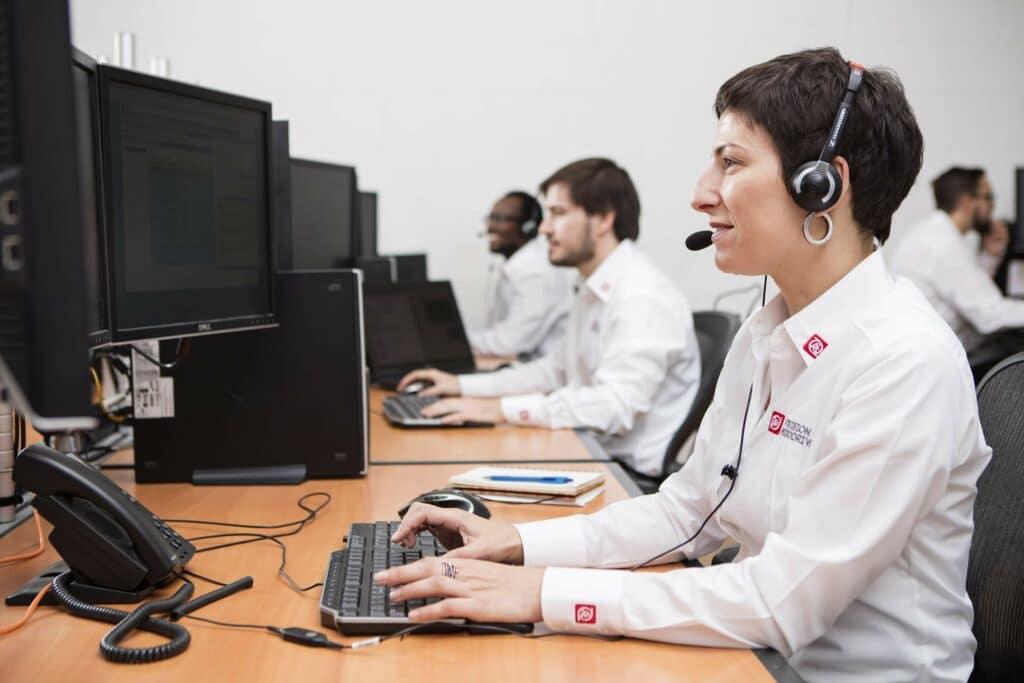
Get in touch
Speak to a member of our team.
Motor catalogue
Looking for our products?
Reliable, cost-effective miniature mechanisms and motors that meet your application demands.
Discover more
Resources and guides
Discover our product application notes, design guides, news and case studies.
Case studies
Explore our collection of case studies, examples of our products in a range of applications.
Precision Microdrives
Whether you need a motor component, or a fully validated and tested complex mechanism – we’re here to help. Find out more about our company.