Using BLDC Motors with Positioning Control
The main complexity of BLDC motors is the need for specialised drivers to handle the electronic commutation, but is there a hidden advantage?
BLDC motors have many plus points, including high endurance and a higher power-to-volume ratio than their brushed DC motor counterparts. However, some regard the need for additional drivers as a drawback – but with advanced driver ICs the user complexity is greatly reduced, and we can use them for relatively precise positioning control.
Stepper motors are commonly used in high precision applications, some even offer a positioning accuracy of less than 1°. In truth, stepper motors are a specially designed brushless motor. Whilst your normal BLDC motor is designed with a high-speed continuous rotation in mind, stepper motors use a more specialist internal construction to offer greater control over the shaft position via the introduction of steps.
The main difference is the number of poles and phases. A common BLDC motor might use 3 phases (the minimum would be 2 poles and 3 slots), whereas a stepper motor might use as many as 5 phases and many more poles to offer up to 500 steps per revolution. The more slots and more poles, the closer a motor resembles a stepper motor.
As an example, we can look at the simpler and more common 3-phase BLDC motor. Normally, the communication is handled by a driver that powers two phases to turn the rotor, whilst the third phase is used for sensing back EMF. Knowing which phases to power at the right time is often achieved through a Hall sensor or “zero-crossing detection”.
This setup gives us a 6 step sequence positioning:
Step | Phase A | Phase B | Phase C |
---|---|---|---|
1 | +V | GND | NC |
2 | +V | NC | GND |
3 | NC | +V | GND |
4 | GND | +V | NC |
5 | GND | NC | +V |
6 | NC | GND | +V |
Depending on the number of poles and slots, a motor may have made a full rotation or a half rotation after this sequence (repeating the sequence would complete a full rotation if required). As a result, the minimum angle of rotation the motor makes with each step is determined by the number of poles and slots.
To improve this accuracy we can use a three-phase sine wave as the motor supply. Motor drivers can be used to generate three-phase sinusoidal waves, each with a 120° phase shift from the other two waves.
As a caveat, in this mode the motor works without any positional feedback – so the load torque must always be lower than the motor’s rated load.
In general, most BLDC motors can work in this method – including the 712-100 from Precision Microdrives which has only two poles (so the motor shaft will make one full revolution per six steps, as discussed above). This means that the resolution of positioning is lower compared to a higher poled motor, but has the advantage that the position of the shaft is always uniquely defined.
This means the two poles motor is more suitable for applications like mechanical gauges, speedometers, and tachometers – where the shaft will always be in the same position after step #1.
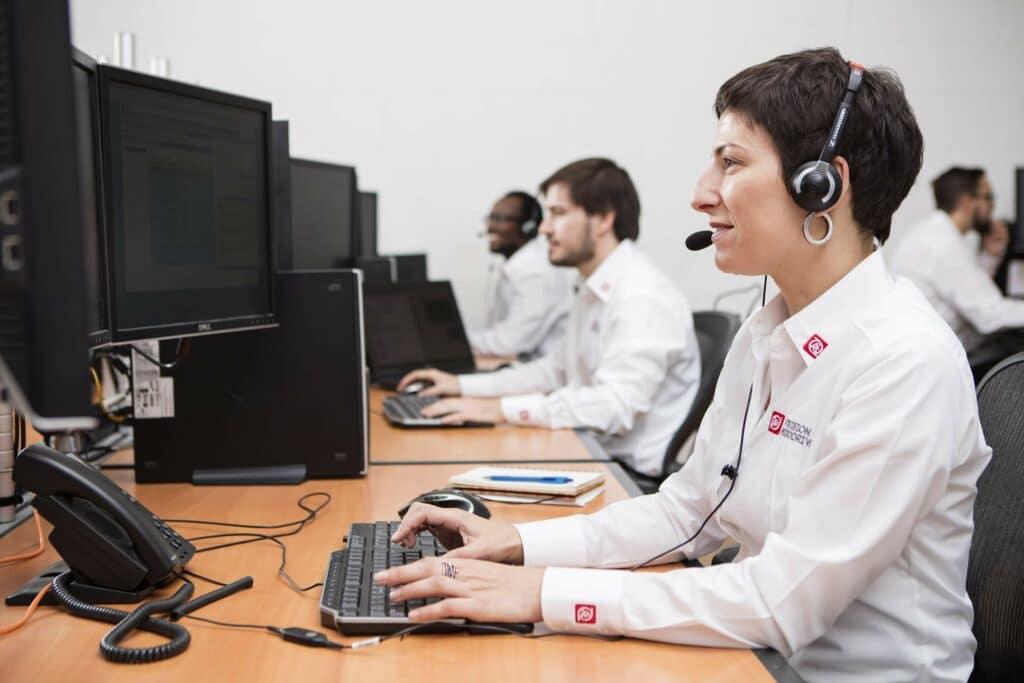
Get in touch
Speak to a member of our team.
Motor catalogue
Looking for our products?
Reliable, cost-effective miniature mechanisms and motors that meet your application demands.
Discover more
Resources and guides
Discover our product application notes, design guides, news and case studies.
Case studies
Explore our collection of case studies, examples of our products in a range of applications.
Precision Microdrives
Whether you need a motor component, or a fully validated and tested complex mechanism – we’re here to help. Find out more about our company.