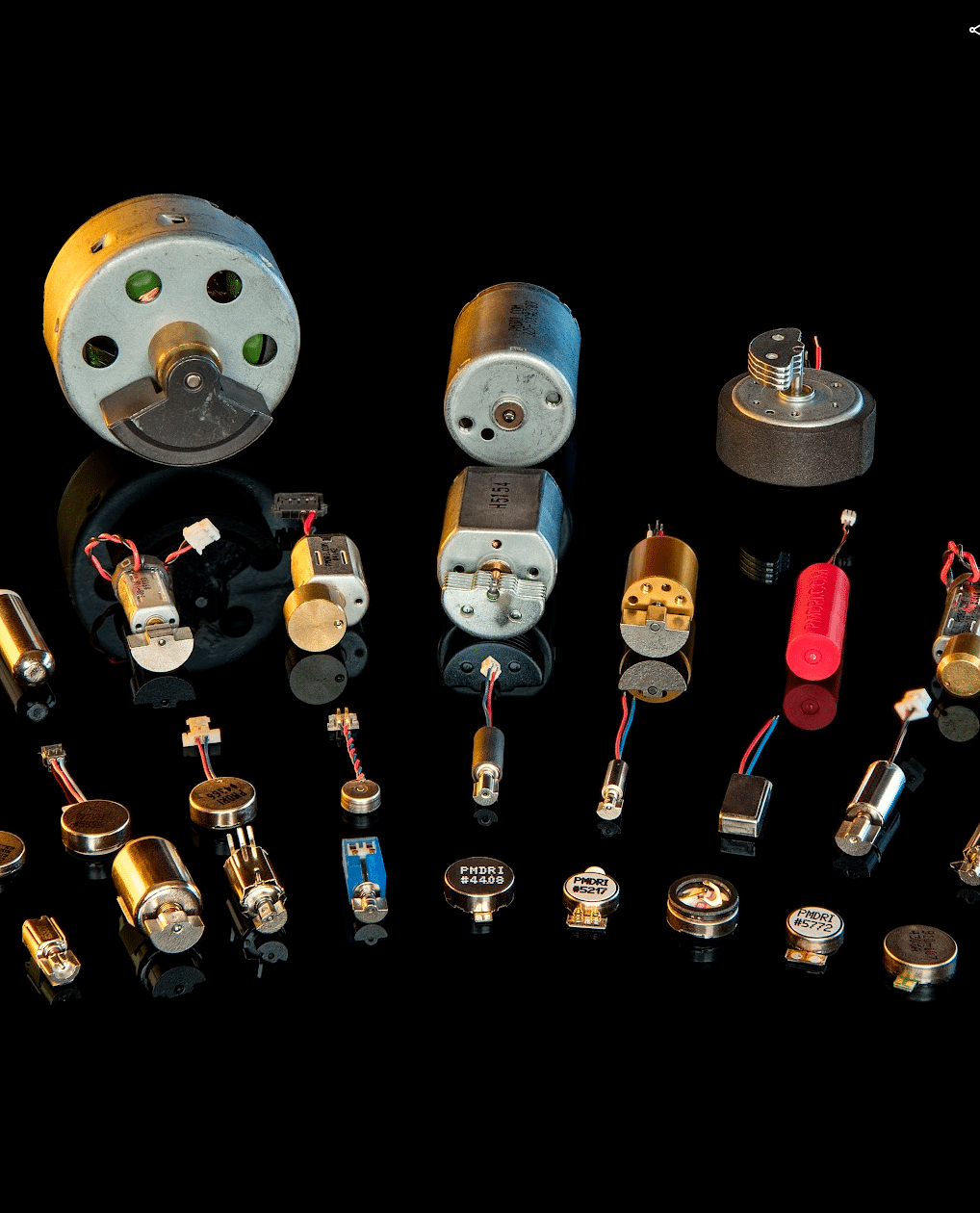
Vibration motors
Eccentric rotating mass (ERM), LRA, and solenoid
Wide range of DC vibration motors with off-the-shelf sampling
Precision Microdrives designs and manufactures a wide range of high-quality, and cost-effective, sub-Ø60 mm DC motors in a range of technologies. All types can be highly customised for a wide range of applications.
Speak to an engineer
Let us help you efficiently specify, validate, test, mass produce, and integrate DC vibration motors into your end product.
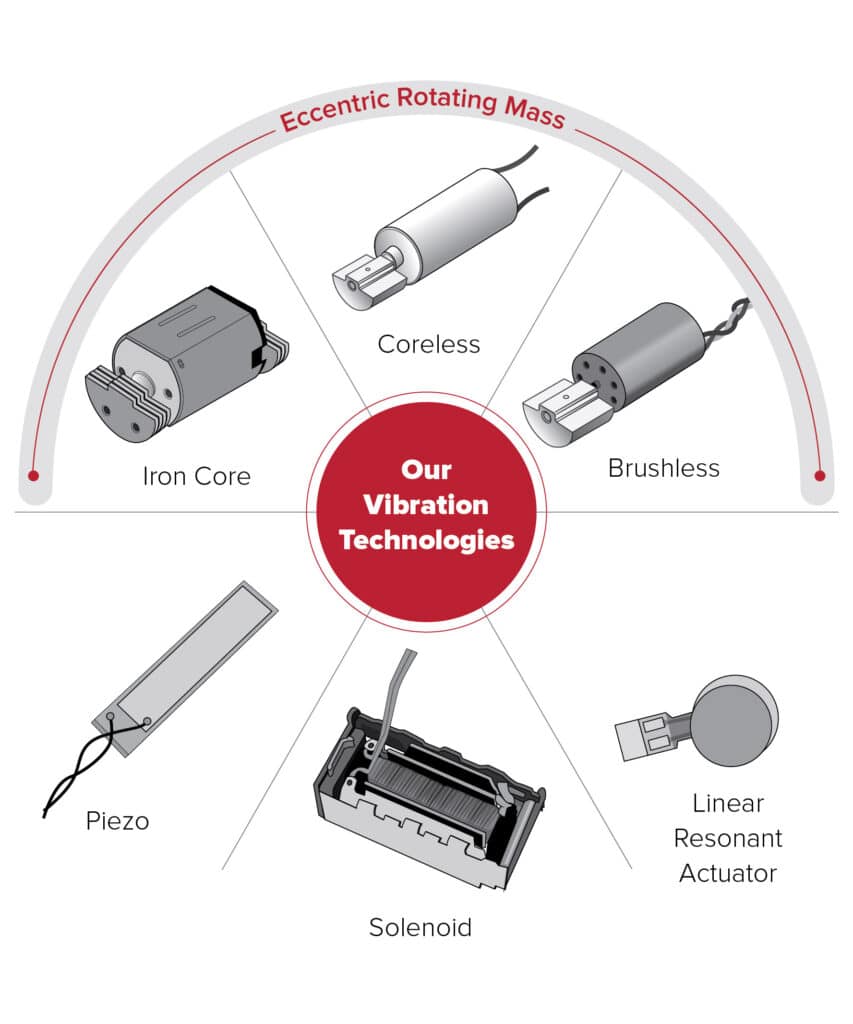
Six vibration motor technologies
There are a lot of ways to vibrate something! With every vibration and haptic technology covered, we’ll help you select the best tech for your application.
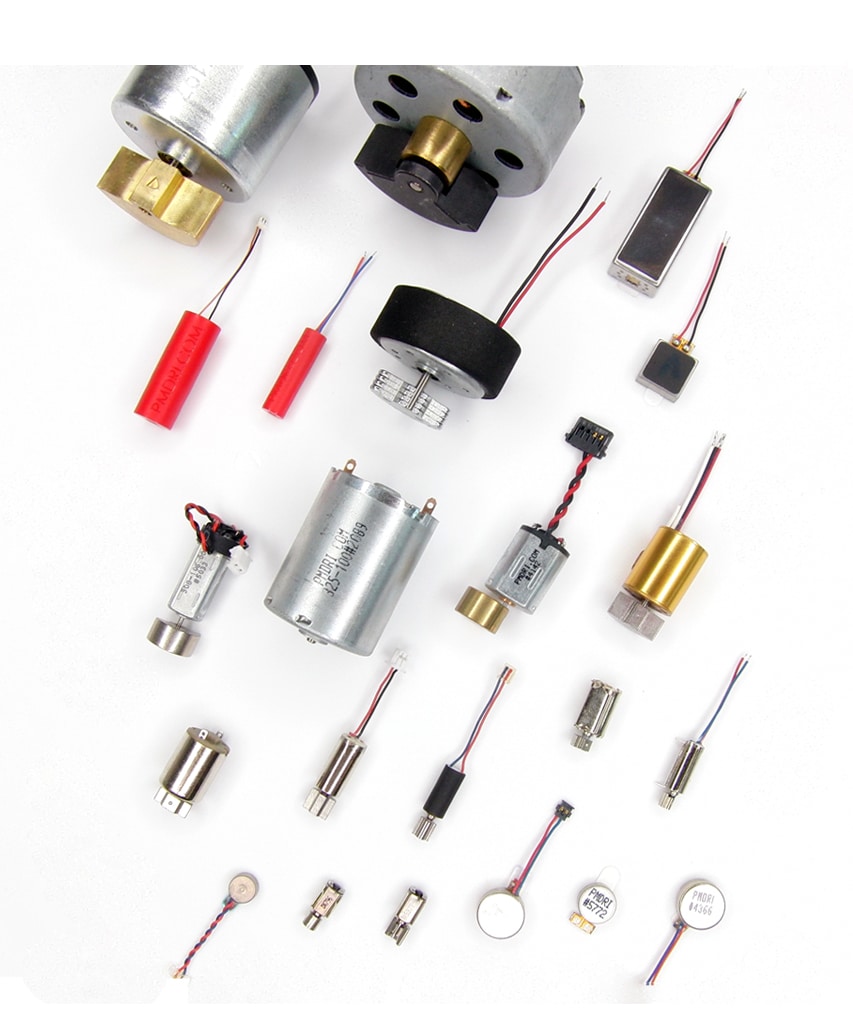
57 stocked motor form factors
We want to help get you developing quickly. So we have many off-the-shelf form factors in a variety of winding configurations available for sample or purchase.
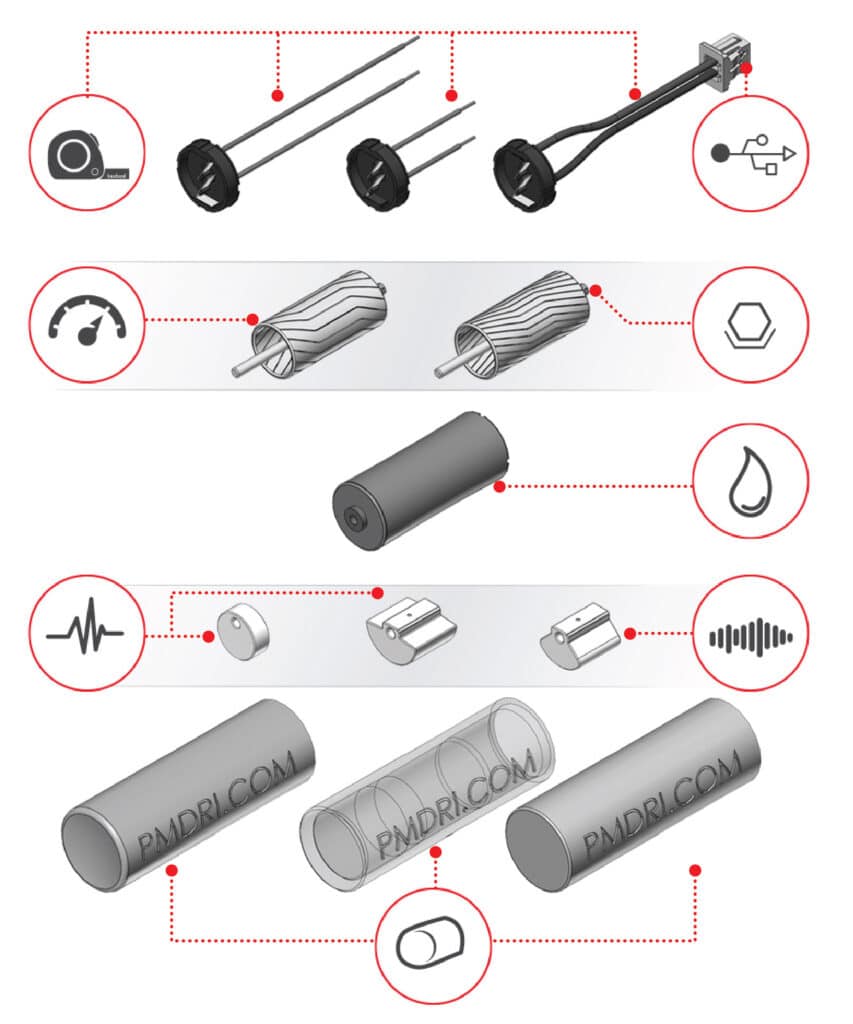
Customised for your application
Your application is unique so we expect you to want some level of custom features or performance. Work with our application engineers to design the perfect solution.
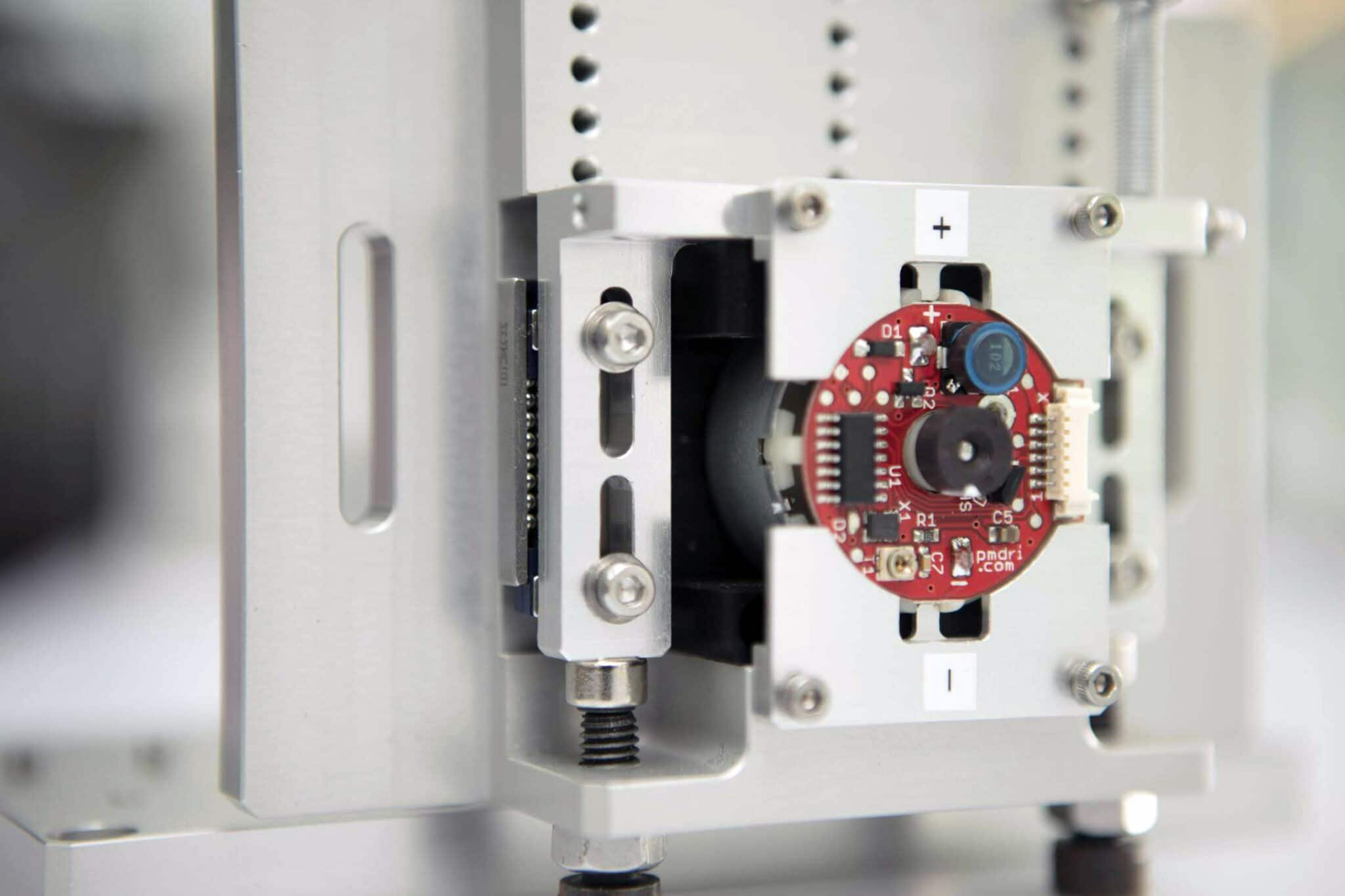
ORDER SAMPLES
Motor catalogue
Reliable, cost-effective miniature DC, Gear and Vibration motors that meet your application demands
DESIGN SOLUTIONS
Vibration motor technologies
Our application engineers design vibration and haptic feedback solutions using six distinct motor technologies. Each come with their own characteristics, benefits and compromises.
Eccentric rotating mass (ERM) vibration motors
Eccentric Rotating Mass (ERM) motors represent the original technology for generating vibration. They are simple to use and are available in a wide range of sizes. That translates to a wide range of vibration amplitudes and frequencies to match any application. They can be found in everything from the smallest smart watch to truck steering wheels.
We can design and manufacture these type of vibration motors using a range of motor technologies, including iron core, coreless and brushless, in both cylinder and coin form factors.
Benefits are that the motors are simple to use and understand. DC motors in particular are easy to control and if long life is necessary, then brushless vibration motors can be used.
Compromises are that the amplitude is tied geometrically to the frequency and the speed, for example it’s not possible to alter the amplitude and frequency independently.
We produce these motors with three different motor constructions and technologies. Iron core for lower cost, coreless for medium cost and medium performance and brushless for the highest performance and longest life.
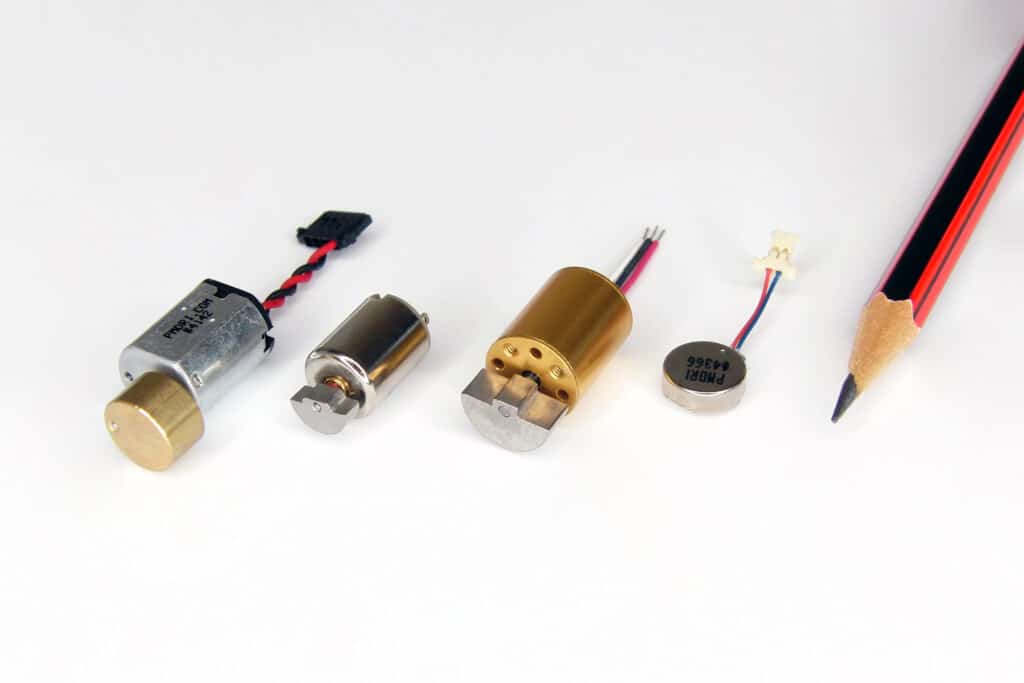
Linear resonant actuators (LRAs)
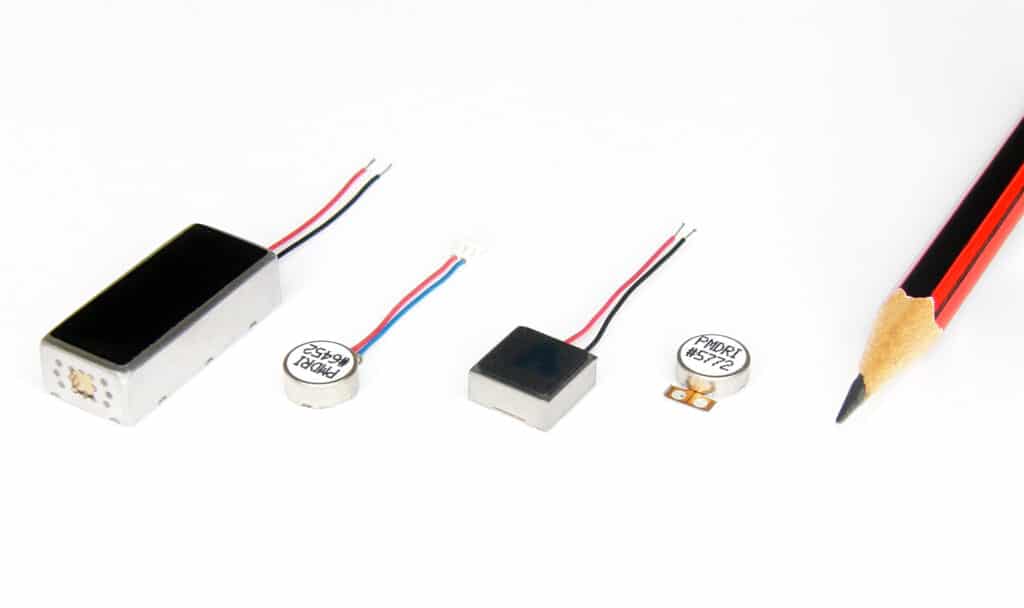
Linear resonant actuators work more like a loud speaker than a traditional ‘motor’. Instead of a cone there is a mass which is moved back and forth by a voice coil and a spring.
This means that LRAs have a resonant frequency at which the amplitude is maximised. Trying to make them vibrate even a few hertz either side of this resonant frequency will lead to a significant loss of vibration amplitude and energy.
Due to small manufacturing variations, each LRA will have a slightly different resonant frequency and therefore a special driver IC is required. This automatically tunes the drive signals to make each specific LRA resonate at their own resonant frequency.
LRAs are commonly used in smartphones and small touch / tracker pads and other sub 200g handheld devices. They are available in two specific form factors – coin and bar – with a few square designs. The axis of vibration varies depending on the form factor, but is always in one axis (whereas ERMs vibrate in two axis).
Our range is quickly evolving to match the latest / specific customer needs. If you’re considering an LRA, it would be well worth discussing this with one of our application design engineers.
Solenoid actuators
Solenoid actuators are similar to LRAs but are typically much larger. With a construction similar to a solenoid, a large coil is formed though which a mass can slide.
In some cases the mass is tied at each end by springs that prevent it from hitting the outer case or end stop. This construction arrangement is therefore similar to a large LRA.
In other designs it is intended that the inner mass will hit and end stop built into the motor enclosure which will create more of an impact.
A third type of solenoid actuator is attached via a lever to a touch surface which is suspended via haptic suspension mounts. This solenoid is used to jog the surface when touched which the brain interprets as a button push.
Solenoids actuators require a custom driver to control them and so are a more expensive alternative to ERMs. The use cases for solenoids are quite specific and often ERMs are a more reasonable and worthy substitute.
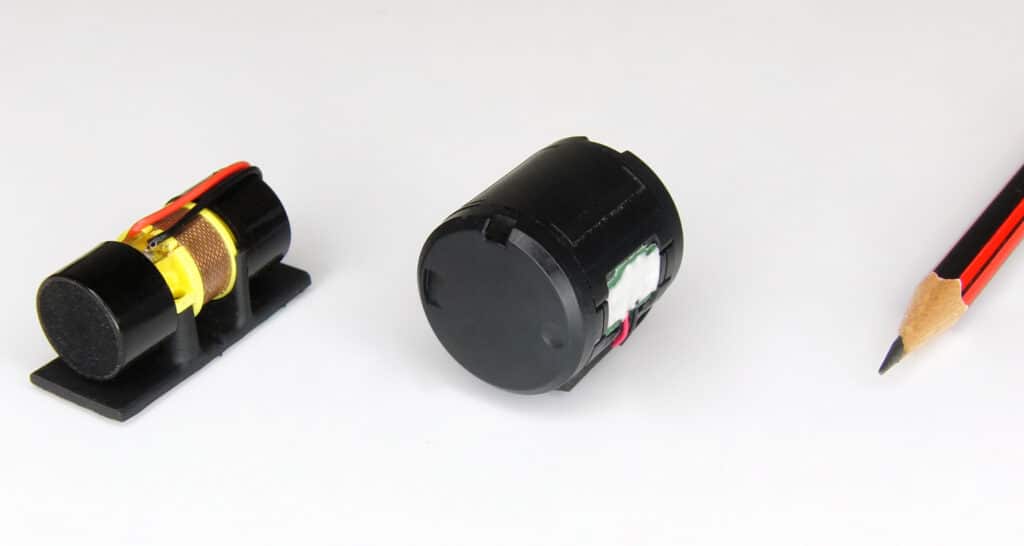
PRECISION MOTOR DESIGN
Typical vibration motor form factors
Irrespective of the vibration motor technology used, there are some common form factors and design influences (largely around the electrical connection interface) that are commonly used in applications across all industries. Below are some of these that can be used to describe your preferred solution.
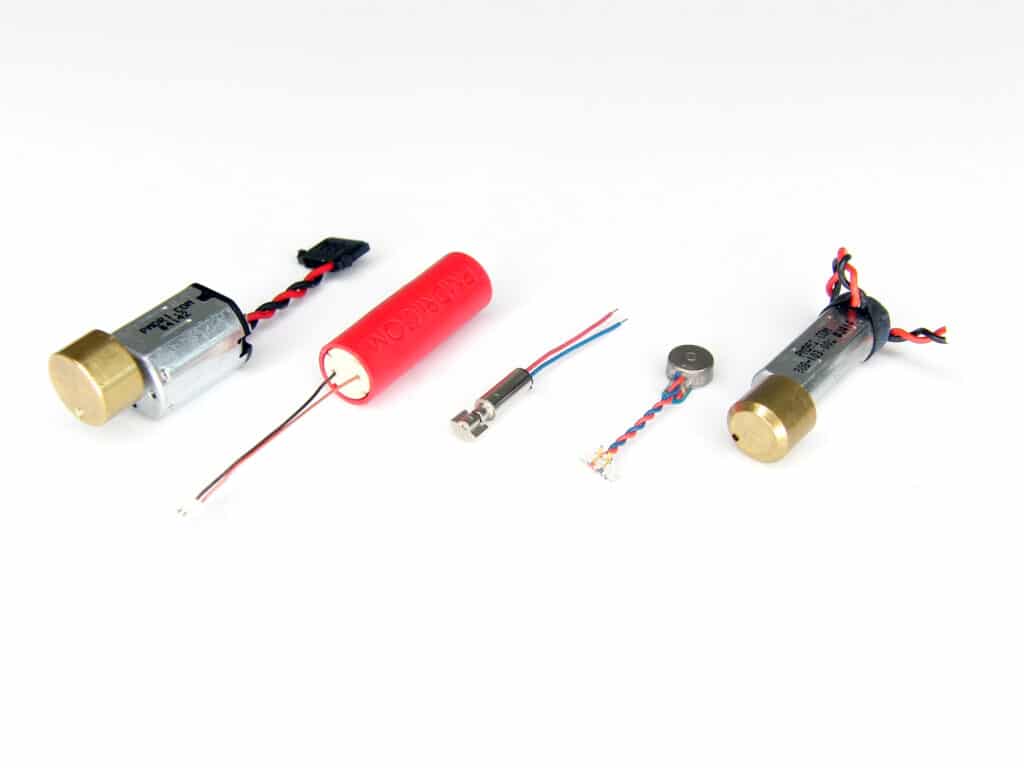
Leaded vibration motors
Most vibration motors come with pre-fitted wires / leads that can be modified to length and fitted with a wide range of connectors.
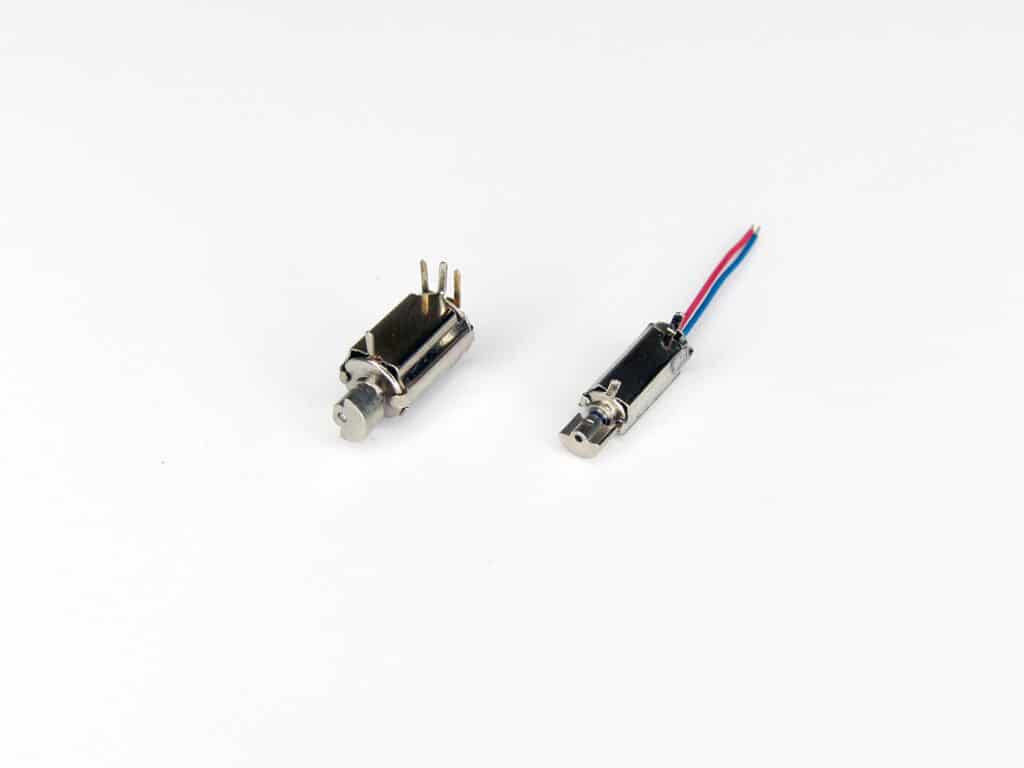
Through hole PCB vibration motors
Some vibration motors can be through-hole PCB mounted, and within this category, we can send power through pins or wires / leads
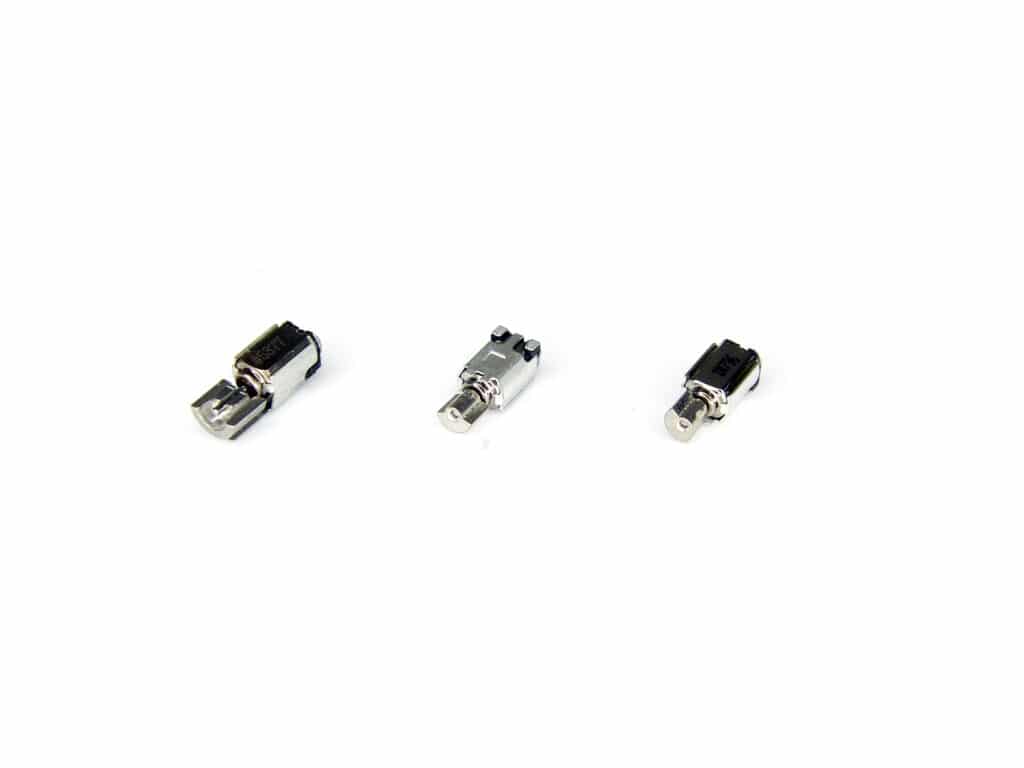
SMD reflow vibration motors
We offer a wide range of SMD reflowable vibration motors that are supplied on SMD pick and place reels.
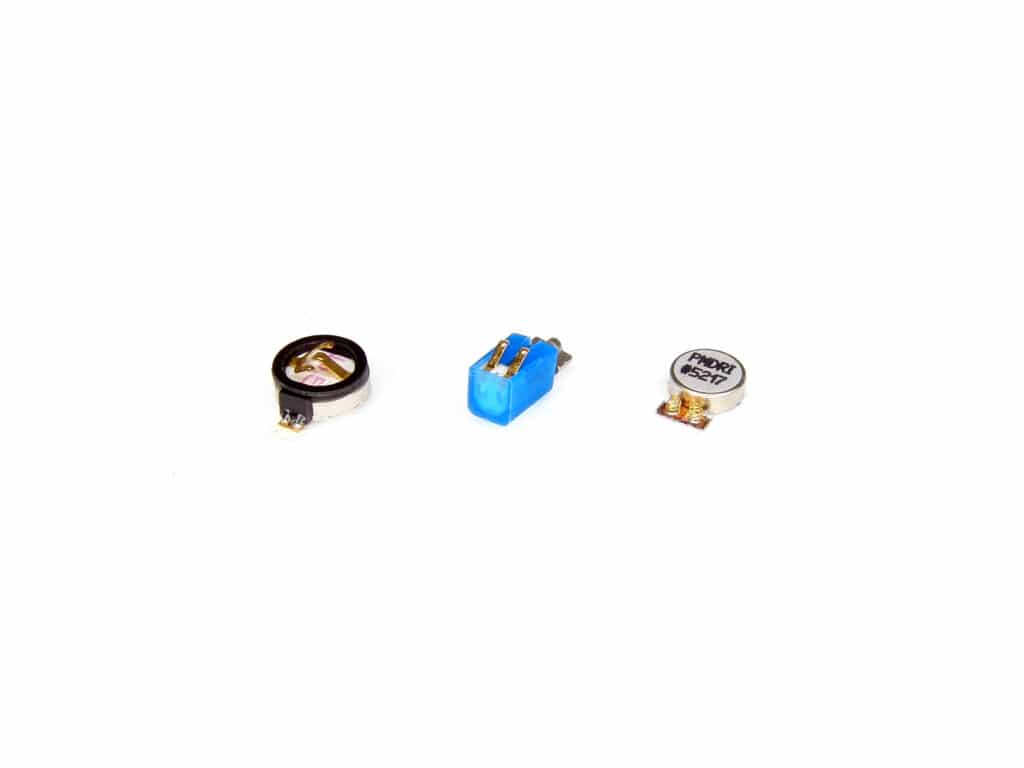
Spring pad vibration motors
For cases where the motor should be integrated into the case, rather than PCB, spring pad motor designs are a good choice.
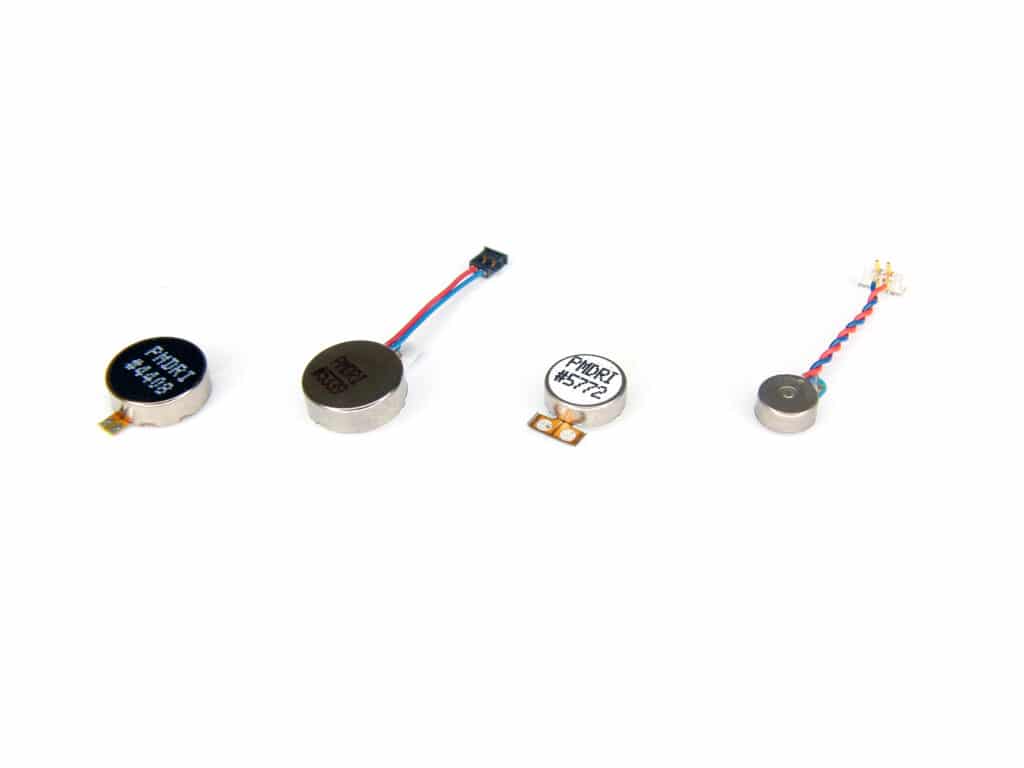
Coin and pancake vibration motors
We carry a wide range of ERM and LRA motors in both coin or ‘pancake’ designs. These can be leaded or fitted with pad springs.
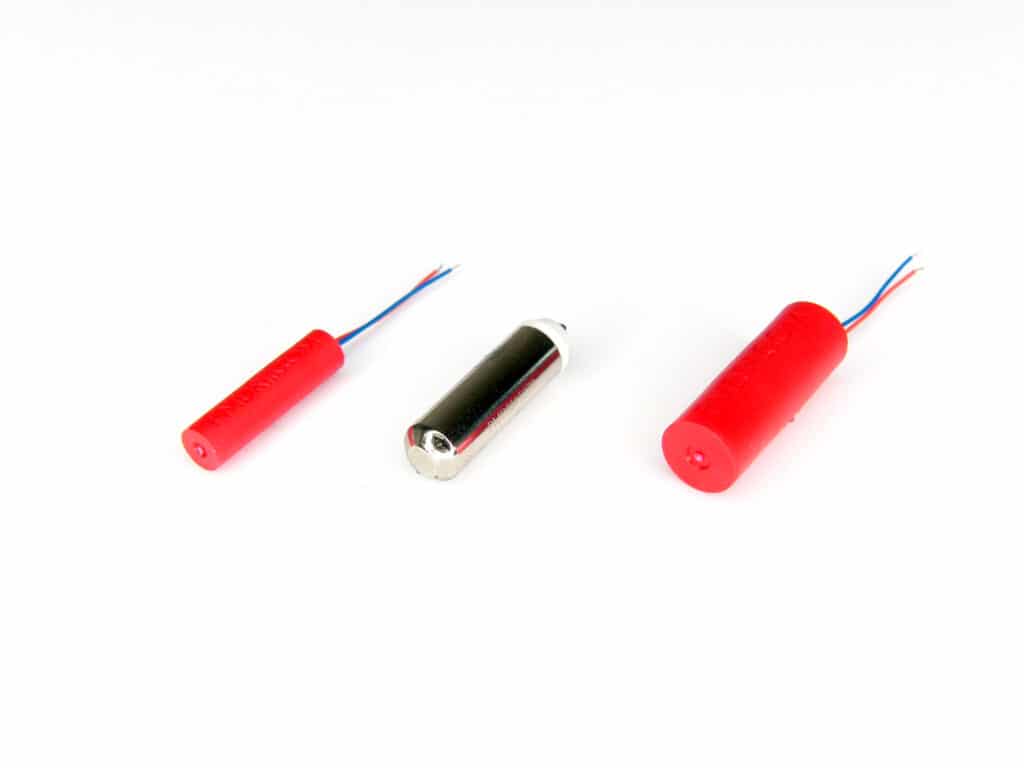
Encapsulated vibration motors
If ERM clearance is an issue, or over-moulding is desired, try our range of encapsulated vibration motors.
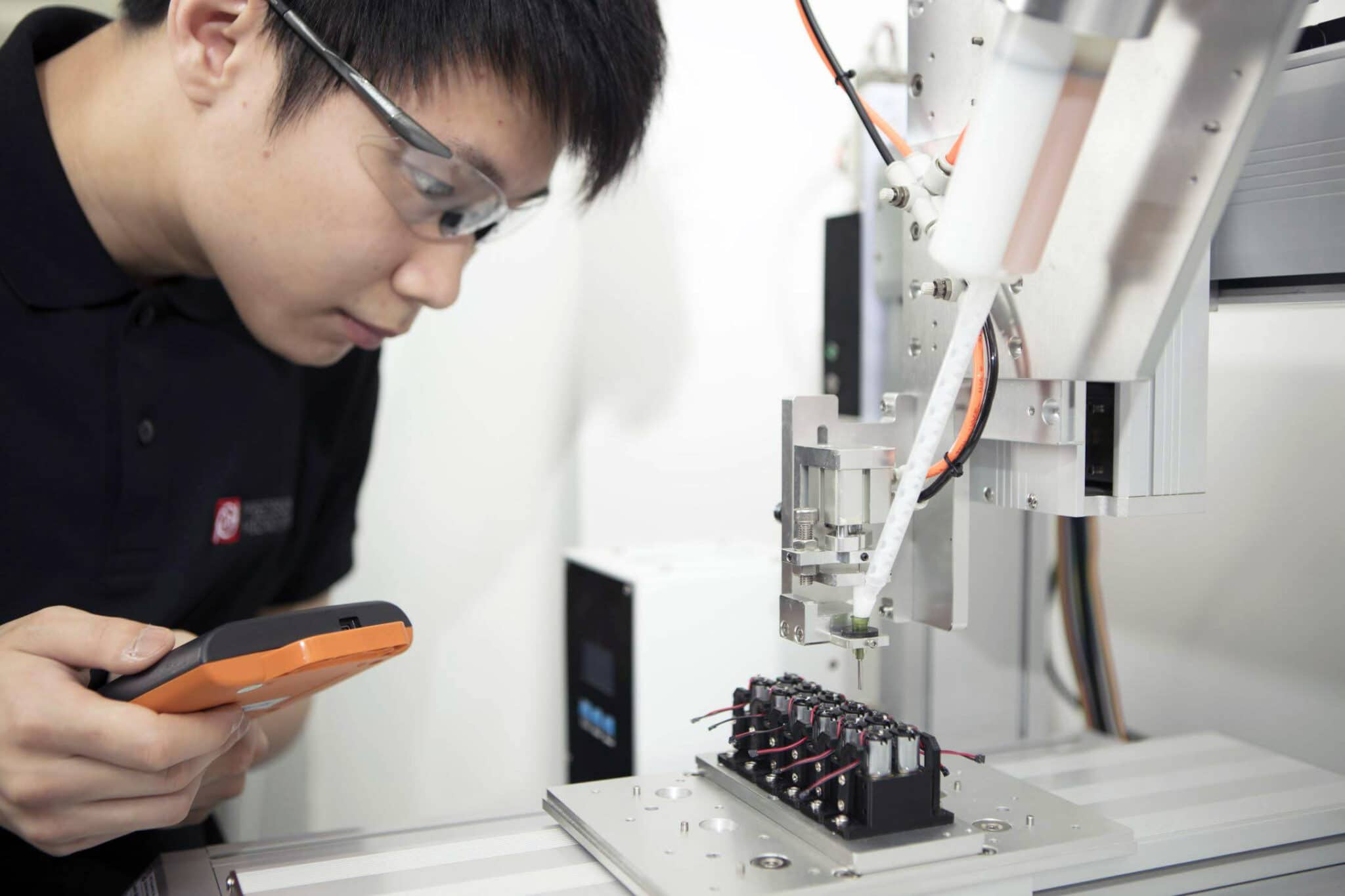
MORE THAN YOUR AVERAGE MOTOR SUPPLIER
Precision mechanisms
Innovative and optimised mechanism design for application
DESIGNING FOR YOUR APPLICATION
Example vibration motor customisations
We routinely re-design and customise all types of vibration motors for customer applications. The interactive hot-spot graphic below shows some of the typical customisations we make for brushed DC vibration motors. We do the same for brushless, LRA, solenoid and piezo technologies.
-
Eccentric mass modification
Adjust the size, material, shape and number of eccentric mass(es) to tune the working range of both vibration frequency and amplitude.
-
Encapsulation
Cover the rotating mass is useful in certain applications. The motor can also be fully sealed in an extra step, to protect against the ingress of fluids.
-
Winding customisation
We design the motor windings for off-the-shelf motors to cover a spectrum of performance requirements. Windings can of course be tailored to an application. Custom windings will deliver a custom performance load point which can be set in conjunction with an appropriate eccentric mass. This will yield the correct amplitude and frequency requirements for the application.
-
Lead customisation
Lead lengths and in some cases wire gauges can be customised to work with application requirements as well as particular connectors. Wires are typically crimped directly to the commutators within the motors, so there are design-for-manufacture considerations to bear in mind. Naturally we will advise.
-
Connector customisation
Customised wiresets including all manner of connectors from JST, Hirose, AMP, Molex, AVX, and Kyocera can be added to any motor that we produce. We can also incorporate PCB ‘backpacks’ to the rear of some motor to suppression EMI locally or add additional circuit features.
-
Brushes and commutator
The brushes and commutator are the heart of every DC motor. The plating type and method used on the components can have a huge effect on the longevity of the motor, as can the type of commutator polishing and lubricant used. Long life brushes are more expensive, but cheaper than using brushless technology.
-
Bearings and lubricants
We use a selection of bearings and lubricants in our motor designs, adapted to the application environment. In larger vibration motors, the bearing is usually the first component to wear, due to the centrifugal force originating from spinning an eccentric mass. We will advise against an application specification.
-
Resonant frequency
All devices have a resonant frequency at which the vibration amplitude will be highest. Vibration motors will tend to ‘lock’ in to this frequency when driven at neighbouring frequencies and we can help optimise that for your application.
-
Click on the blue dots to expand customisation details
SOLVING YOUR PROBLEMS
How we can help
At face value, using vibration motors in your application seems easy, but trust us – getting reliably to mass production can be harder than it looks.
Have you considered the following?
- Appropriate vibration amplitude and frequency
- Tuning the motor windings to your power source
- Audible noise
- Motor longevity
- Haptic response characteristics
- EMI / EMC electrical noise suppression
- Integrating the motors into your enclosure
- Unwanted resonant frequencies and harmonics
- Electrical connections to aid mass assembly
- Batch to batch quality consistency
We have done the design for application, design for manufacture and ramp up into mass production process thousands of times.
Why not let us handle this part with all our experience so that you can focus on the parts of your application that add the most value.
Let us design for your application
Design is at the heart of what we do at Precision Microdrives.
We understand the challenges motors present and enjoy providing solutions, whilst reducing cost and risk, through innovative and optimised design.
Let us determine the best motor for your product based on our technical expertise and extensive experience.
Design yourself with our sampling catalogue
Reliable, cost-effective miniature mechanisms and motors that meet your application demands. Also motors.
CASE STUDIES
Example vibration motor applications
Vibration motors find their way into a surprising number of applications. We’ve covered the main types of use below:
Vibration alerting
Vibration alerting is used to interrupt a users attention with a tactile alert. A pager or phone vibrating to indicate an incoming message.
A fireman’s radio indicating an incoming call. A respiratory aid indicating that it’s filter needs changing, and a pace-maker indicating that it’s battery needs changing, are all examples of using vibration to augment or replace sound or visual-based indicators or warnings.
Case study | pacemaker patient notifier
Our customer required an ultra reliable vibration alerting motor for their implantable pacemaker.
They also called upon us to perform all the value-add engineering and quality control services required, to reliably produce a class III FDA approved medical product.
Over the past decade, we have delivered over 1 million brushless vibration motors with very high quality and performance consistency.
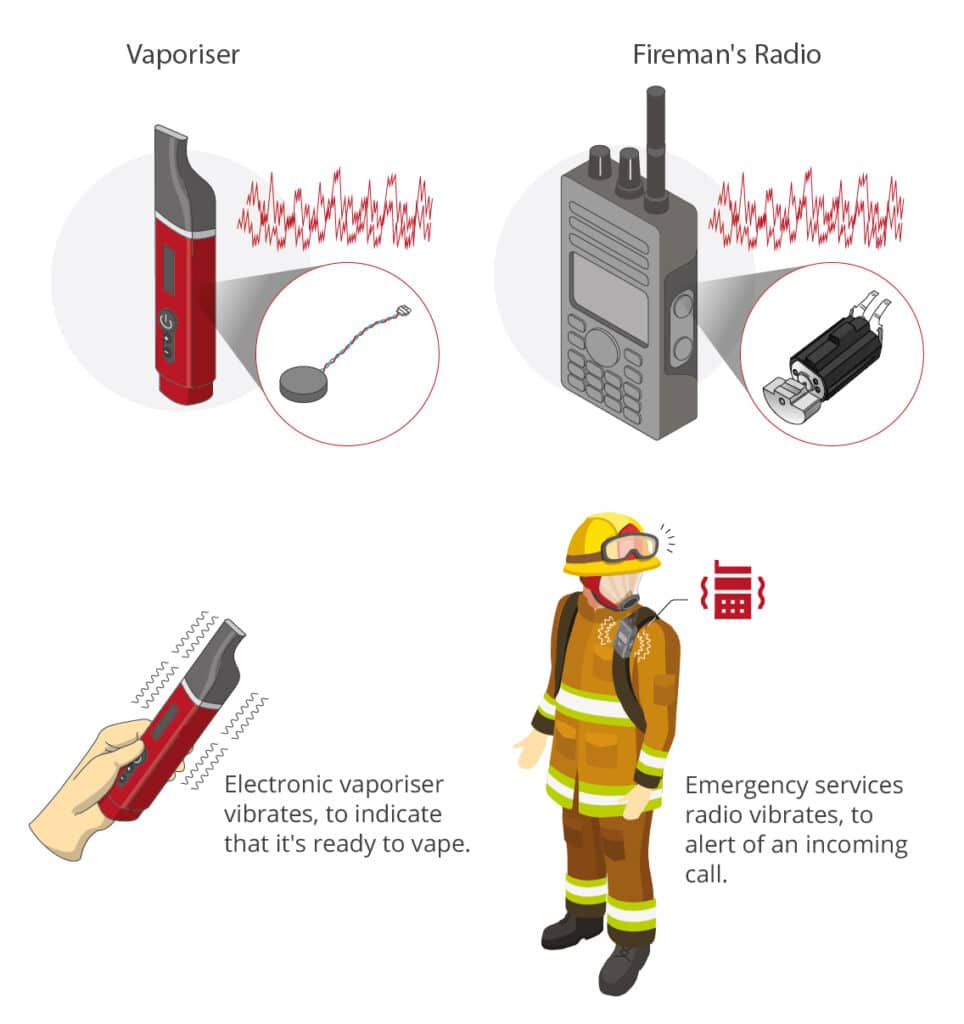
Touch screen haptics
Screen haptics is where a vibration motor is used to simulate the tactility of a push-button when a user presses a flat screen.
Signals from the screen’s touch sensors trigger a haptics driver that sends impulse drive signals to the vibration motor(s) attached to the screen. The motors operate vibrating the screen so that the user feels the sensation of pressing a physical button.
We have a wide range of vibration motors and Linear Resonant Actuators optimised for screen haptics applications. We also have a new range of heavy-duty haptic actuators designed for larger screen (such as point of sale) haptics.
Case study | thermal imaging camera
Our customer was updating their range of thermal imaging cameras by integrating touch screens, to enable more complicated user-interfaces without increasing physical button count.
We produced a linear resonant actuator (LRA) solution that provided crisp haptic feedback to the screen, despite a ruggedised enclosure.
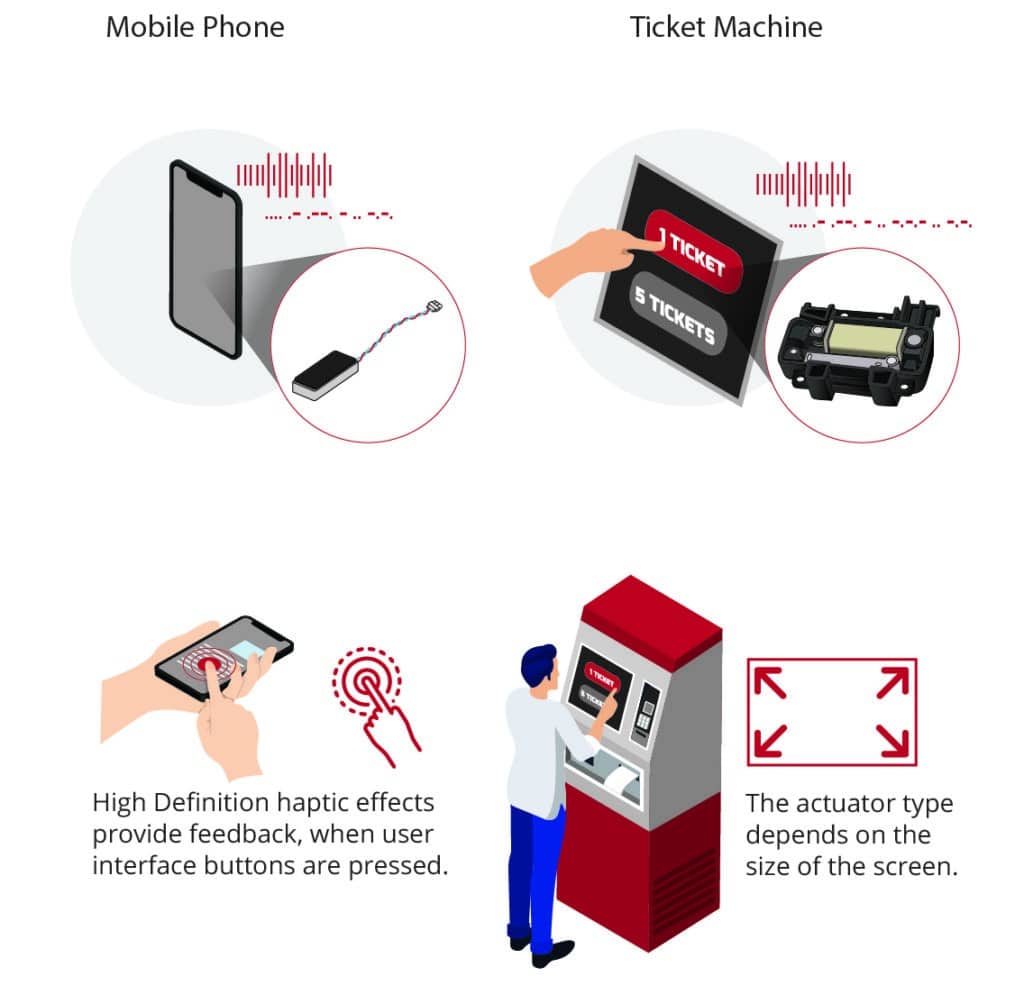
Haptics for user interfaces
Precision Microdrives vibration motors can also be used to add haptics to non-screen user interfaces. These include capacitive touch-surfaces which do not have a screen (e.g. capacitive switch panels), and other user-interfaces such as machine control sticks / levers. Information can be fed instinctively back to the machine operator by vibration motors embedded into the control columns / handles. This is a more refined version of Vibration Alerting, where more information than just an alert needs to be conveyed to the user.
Many items can be turned into haptic user interfaces, for example, shoes that vibrate directions to one foot at a crossroads, or steering wheels that vibrate as part of a lane departure warning system.
Case study | industrial barcode reader
Our customer was designing a ruggedised barcode reader for use in a food distribution warehouse.
The scanner would regularly see very rapid temperature changes between ambient and sub-zero (frozen foods) sections. We designed and manufactured a motor that could withstand these environmental challenges as well as deliver long-life, crisp, haptic feedback to the scanner handle.
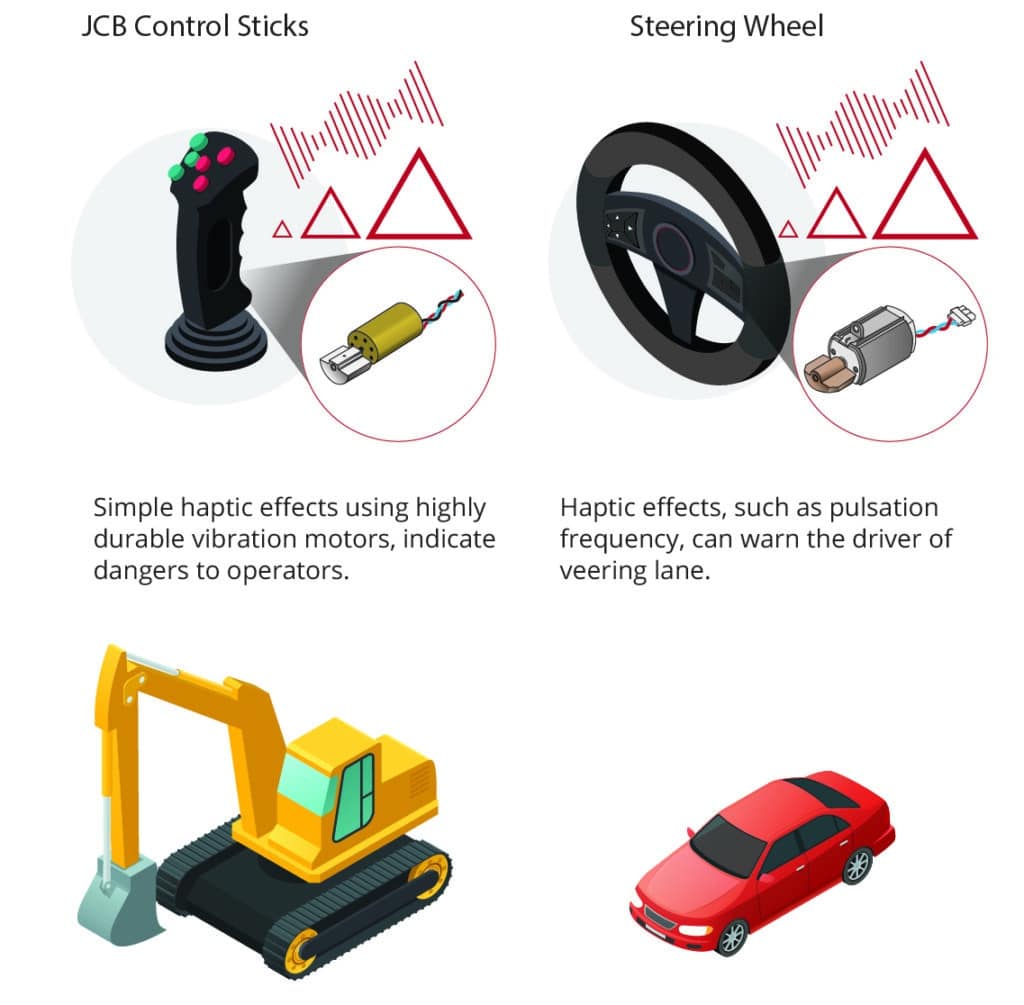
Vibration for industrial mechanical aid
Vibration is used in industrial processes, vending machines and lab equipment to aid the movement of materials through a process.
For example, ice-cubes through the chute of a crusher, wires through the hopper of a wire crimping machine, or the mixing / emulsification of fluids and powders.
If you have powders, small items, wires, or other materials that are prone to getting stuck or won’t mix, try freeing them with a source of vibration. We offer a wide range of motors for this application, including super-long-life brushless vibration motors for constant operation.
Case study | vibrating hopper for automated wire crimping
Our customer manufactures complex automatic wire crimping machines. In one of their processes, they required pre-cut wires to be fed through the machine, and found that they needed to vibrate the wire hopper to reliably funnel the wiresets which were sticking.
Our solution was a brushless vibration motor with a precise speed controller set to the hopper resonant frequency.
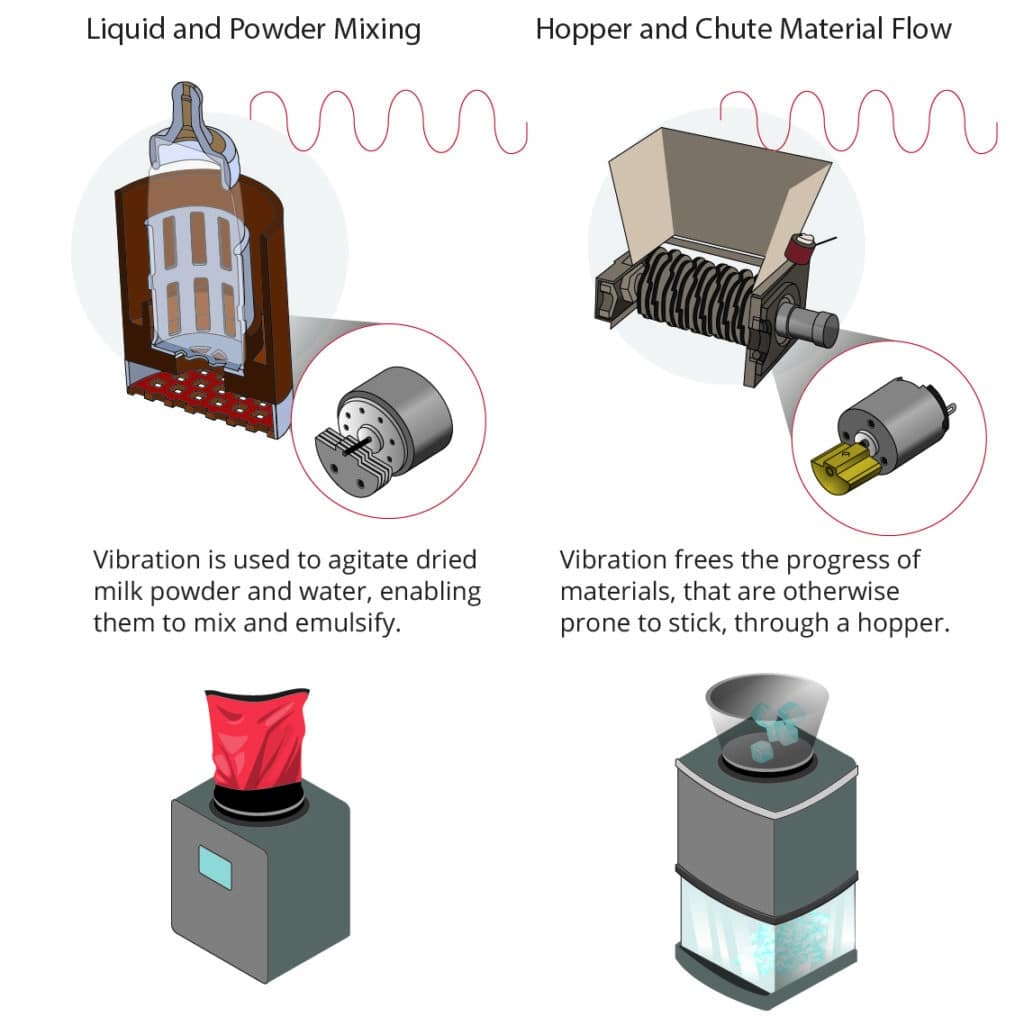
Vibration for material analysis instruments
A more unusual use of our vibration motors is within instrumentation and material analysis markets. Some seismometers and vibration monitoring sensors integrate our vibration motors to operate as part of their self-testing algorithms.
This reduces the chances of false-negative readings within the instruments. Also, some instruments deliberately send vibration through a material under test, measuring how the vibration signals propagate through the medium. We can customise our range of vibration motors to precisely target a specific frequency range or amplitude.
Case study | portable medical instrument
Our customer was designing a new portable neurothesiometer instrument, that could be used to quick-test for type II diabetes in patients.
The requirements were for a very precise frequency output of 128 Hz. Since the frequency had to be controlled and longevity was critical, we chose a brushless vibration motor solution with a customised controller that ran the motor at a precise 7680 (+/- 10) RPM.
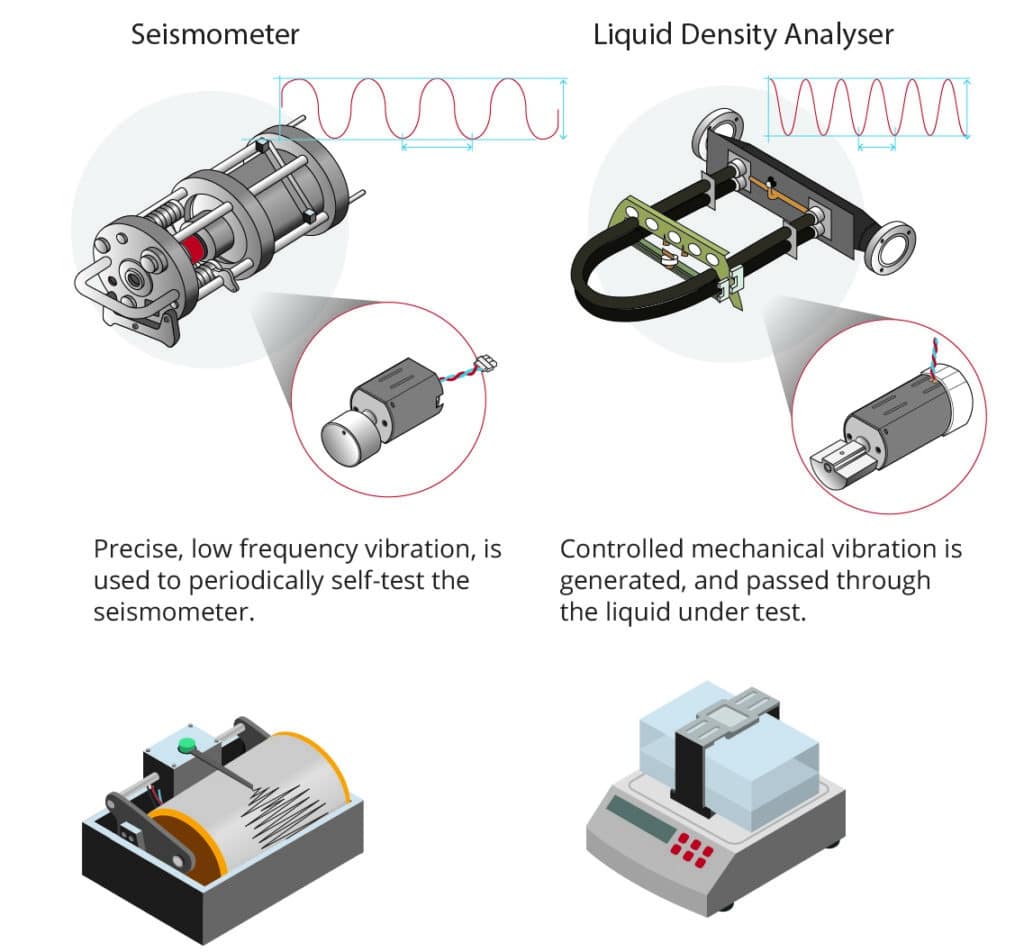
Vibration for healthcare
An obvious use of vibration motors is in the application of ‘good vibrations’ for adult toys and consumer massager applications.
However, vibration motors are also used in the application of pain relief to sore joints and the trigger-point release of fatigued and overtrained muscles.
For healthcare applications, the precise application of frequency and amplitude is often required. At Precision Microdrives we can tailor the performance characteristics of our motors to deliver an exact vibration, as well as tuning vibration systems to take advantage of or avoid completely system resonant frequencies.
Case study | tennis elbow vibration therapy pain relief
Our customer designed a new consumer healthcare device to offer pain relief to ‘tennis elbow’ injuries.
The product was launched with an aggressive pricing strategy but required a precise vibration frequency and amplitude profile.
We designed a cost-effective iron core vibration motor and improved the product’s accuracy by individually calibrating and marking each motor during manufacture.
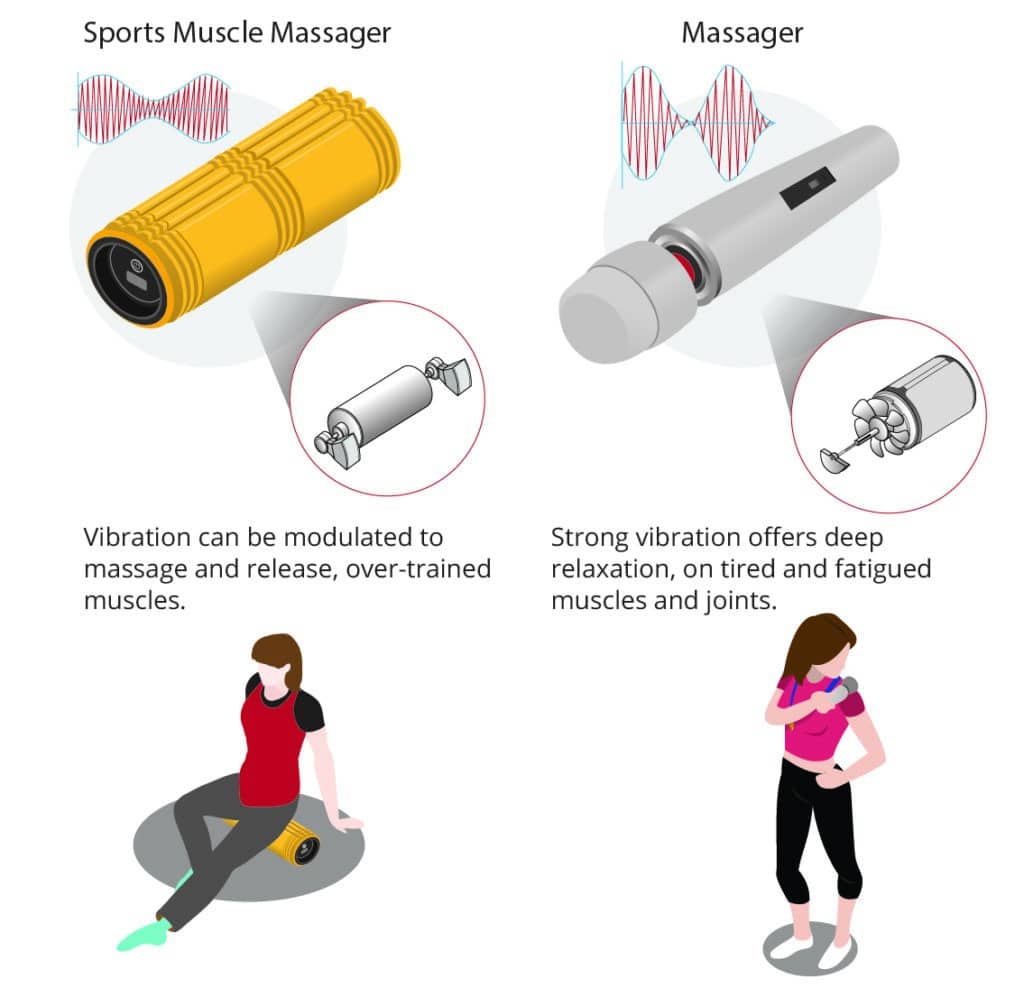
HOW CAN WE HELP?
We add value to your device through
Custom assemblies
Longevity testing
Mechanism design
Engineering confidence
In-house production
Full testing validation
PRECISION PROCESSES
Our capabilities
We can support you through the whole journey from prototype to high volume cost-effective mass production:
MOTORS & MECHANISMS
Precision products
Verified and reliable precision motors, perfect for your application
-
Brushless Motors
We offer a comprehensive range of DC brushless motors in both slotted and slotless (high torque and negligible cogging) designs,
View Page
-
DC motors
Iron-core, coreless and brushless DC motor technologies in a wide range of form factors and sizes, with off the shelf
View Page
-
DC gear motors
Building on our range of DC motors, we integrate spur and planetary gearboxes, from 6mm to 60mm frame diameters.
View Page
-
Haptic feedback
Practical and reliable, low noise and high quality haptic feedback solutions for all types of application user interface.
View Page
-
Mechanisms
Custom motor assemblies designed and manufactured to your requirements. A turnkey service from design inputs to mass production.
View Page
-
Linear actuators
Precise, reliable and highly customisable linear actuators designed for a wide range of industrial, commercial and medical applications.
View Page
Discover more
Resources and guides
Discover our product application notes, design guides, news and case studies.
- VAB-02: How Do Vibration Motors Work?
- AB-008: Vibration Motor Best Practices From Mobile / Cell Phones
- AB-015: Mechanical Mounting For Vibration Motors
- AB-030: Extending Vibration Theory – Displacement And Dissipation
- AB-010 : Mounting Vibration Motors To Flexible Materials & Clothing
- AB-018: Driving Brushless Long-Life Vibration Motors
Vibration motor case studies
Explore our collection of case studies, examples of our products in a range of applications.
Precision Microdrives
Whether you need a motor component, or a fully validated and tested complex mechanism – we’re here to help. Find out more about our company.