Vibration Frequency vs Vibration Occurrence
In this article, we’ll clear up a confusing difference in terminology and attempt to create a common language surrounding vibration frequencies.
The problem arises because in normal conversation we might refer to a single vibration effect as ‘a vibration’. For example, you might say your mobile phone vibrated when you received a text, or a touchscreen plays a short ‘vibration’ when pressed and ‘two vibrations’ to confirm a long press. In reality, there were hundreds of displacement cycles played in a single effect.
It is important to understand that vibrations are essentially a repeated and cyclical displacement. In Eccentric Rotating Mass vibration motor (ERMs) this is angular as the mass rotates, and in Linear Resonant Actuators (LRAs) it is (as the name suggests) linear as the mass moves back and forth on a spring. Therefore, these devices have a vibration frequency that refers to the oscillating nature of the displacement.
As an example, we can look at the graph below which shows the output from a single axis of an accelerometer that is attached to a vibrating actuator. The resulting waveform shows the acceleration as a wave, and we can measure the frequency by looking at the period of the waveform, either as it crosses the x-axis or between two peaks:
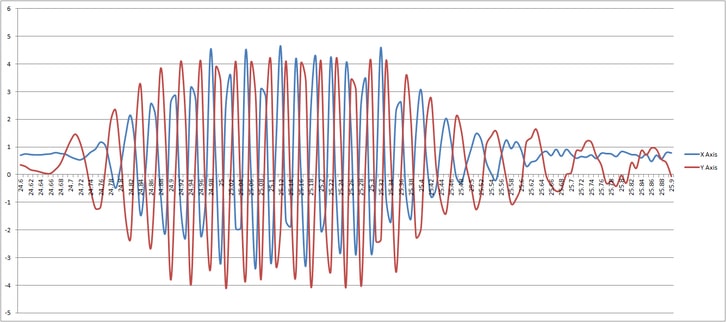
In the example above of a touchscreen with a single or double click, there’s little confusion – it’s clear that the actuator should play one or two effects depending on the touch duration – but many applications require vibration effects repeated at a specific timing interval. In this instance, someone in the development meeting might say “we need the device to vibrate 10 times every second”, which might be translated to a “vibration frequency” of 10 Hz.
However, the vibration frequency refers to the rate of displacement cycles of the actuator, not the number of effects played in a second.
Defining the Terms
Vibration frequency is expressed in Hz and refers to either the speed of the motor in RPM divided by 60 (for ERMs) or the resonant frequency on the datasheet (for LRAs).
It is actuators (ERMs and LRAs) that have vibration frequencies, derived from their speed and construction.
Vibration occurrence is the number of times a vibration effect is played over a specific time period. Therefore, it could be expressed as effects per second, per minute, per day, etc.
It is applications that have vibration occurrences, where a vibration effect might be played at specific time intervals. We explore this in the next section.
Why Are They Important?
Quite simply, the terms are not interchangeable and there are limitations to the range of vibration frequencies available, as explained in this article.
Let’s take an example application where we want to simulate a person’s pulse. We will vibrate our actuator every time there is a heartbeat, in addition, we want to be able to adjust the heart rate between 60 and 150 beats per minute (bpm). This equates to a vibration occurrence of 1 effect every second to 2.5 effects every second (60/60 = 1 and 150/60 = 2.5).
However, the formula for vibration frequency of an ERM is:
$$Vibration Frequency (Hz) = frac{RPM}{60}$$
So, if you were to specify that your application needed a vibration frequency of 1 to 2.5 Hz, this would equate to a motor speed of 60 to 150 RPM. Our slowest motor, the 324-102, has a rated speed of 2,800 RPM – almost 20 times the value in the specification.
A vibration frequency of 2.5 Hz is clearly too slow to achieve, but we show below that 1 – 2.5 vibration occurrences every second is possible (with good actuator selection) and fairly simple.
How to Vary and Achieve Specific Vibration Frequency
Aside from the limitations, varying the vibration frequency is very simple and covered in more depth in this AB-029 Vibration Motors Voltage vs Frequency vs Amplitude.
Simply put:
- The vibration frequency directly relates to the speed of the motor, which in turn relates to the applied voltage
- To increase (or decrease) the vibration frequency, increase (or decrease) the applied voltage
- As the applied voltage is limited by the start voltage and the rated voltage (or maximum rated voltage for short periods), the vibration frequency is also limited
- Different vibration motors have different profiles, based on the design of motor’s torque output and eccentric mass – see the datasheets for more information
- The vibration amplitude is also dependant upon the speed of the motor, therefore you cannot vary vibration frequency and amplitude independently
- The above applies to ERMs, LRAs have a fixed vibration frequency known as their Resonant Frequency
From the above points, we can see that achieving a specific vibration frequency is the same as driving the motor at a specific speed. This raises two points for discussion.
First, setting an exact speed can be problematic due to the manufacturing tolerance and ageing in miniature motors. Even in a single batch, there can be tiny differences in the motor’s parts that lead to slight variations in speed. A vibration motor’s Rated Speed and tolerance are both provided on the datasheet. Fortunately, every 1 RPM of variation is reflected as only 1/60 Hz, so for a window of ± 20 Hz, the equivalent motor speed tolerance is ± 1,200 RPM.
Secondly, achieving a specific vibration frequency is only a realistic goal in a steady-state vibration or during effects that are long enough to reach steady-state. A constant vibration frequency will only be achieved when the speed of the motor is constant, so during the startup and stopping periods, as the mass accelerates and decelerates the vibration frequency will change. Extremely short effects like ‘clicks’ spend virtually no time in steady-state, so it’s not feasible to hit an exact frequency.
Instead, for applications like haptic feedback, you may wish to consider comparing the ‘frequency window’ between the start voltage and rated voltage of different actuators – i.e. the range of vibration frequencies an ERM will fluctuate over as it performs the effect. See this performance on the Typical Performance Characteristics graph on our datasheets.
Nevertheless, if you are looking to mainly operate at steady-state and can accept the small variation in speed, then there are a few methods for attempting to control the vibration frequency. At the core, there needs to be some form of feedback from the motor, so that we can tell how fast it is turning:
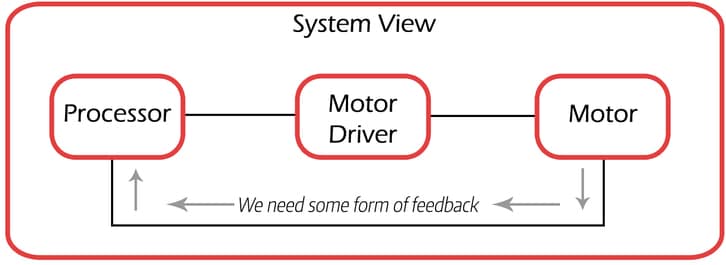
There are two good methods for measuring the current frequency, one is back EMF and the other is the actual vibration frequency. From here we can adjust our drive voltage, creating a control loop. You can read our full application bulletin on how to control the speed of a DC motor using the back EMF.
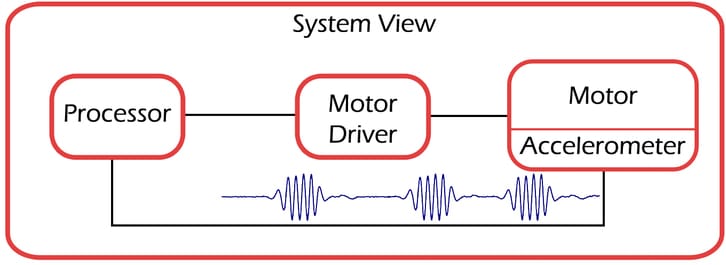
Alternatively, an accelerometer can measure the vibration output, which gives a direct reading of the vibration frequency. Note that some level of signal processing is required to translate this output into an actual drive voltage:
How to Vary Vibration Occurrence
This is best covered in our previous article “Simple Timing Code for Motors”. We talk about the extra components you need to a circuit that produces vibrations at regular intervals.
However, one aspect that the article doesn’t discuss is the upper limit of vibration occurrences. Playing an effect takes time, to have a discernable period between effects there is going to be a limit of how quickly you can play the effects back to back.
Compare the ‘ERM click’ and ‘ERM click-bounce’ waveforms from the DRV2605 datasheet:
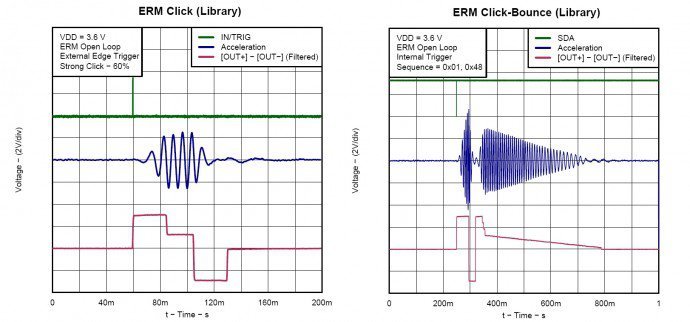
The click lasts only ~80ms but the click-bounce lasts ~500ms. So whilst we could play ~12.5 click effects in a second, we could only play the click-bounce twice. For our example application of heart rate simulation, we needed an effect every 2.5 seconds – so we could use the click effect but would struggle with the click-bounce.
We also need to consider actuator performance. Some ERMs start slower than others, typically when the DC motor is underpowered compared to the mass. We characterise the start and stop times with the Typical Haptic Characteristics.
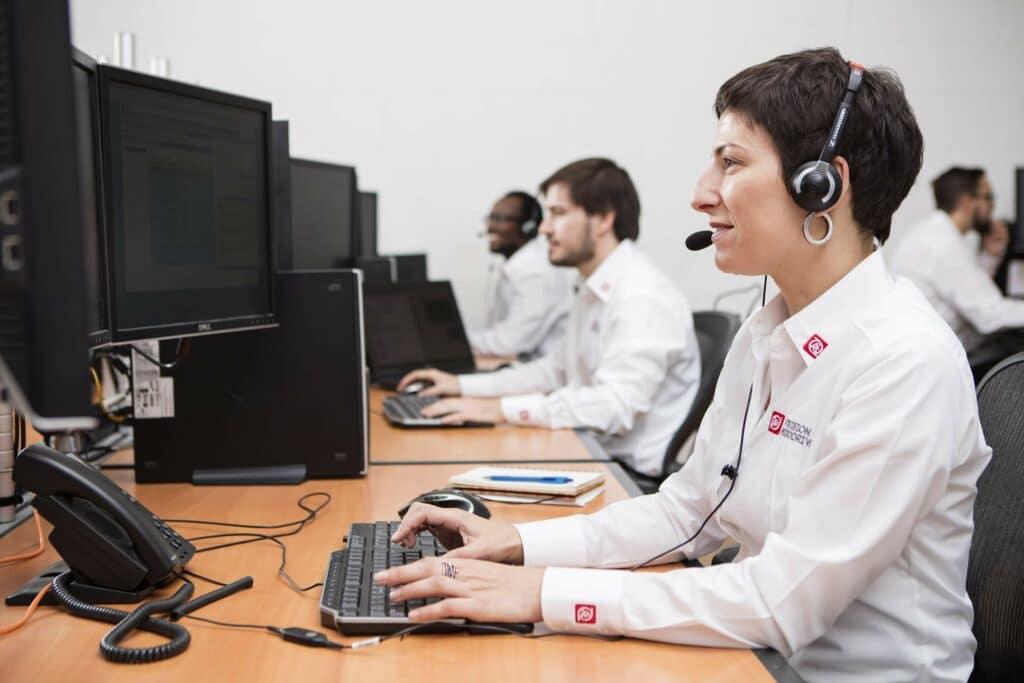
Get in touch
Speak to a member of our team.
Motor catalogue
Looking for our products?
Reliable, cost-effective miniature mechanisms and motors that meet your application demands.
Discover more
Resources and guides
Discover our product application notes, design guides, news and case studies.
Case studies
Explore our collection of case studies, examples of our products in a range of applications.
Precision Microdrives
Whether you need a motor component, or a fully validated and tested complex mechanism – we’re here to help. Find out more about our company.