Using The Hall Effect to Drive Brushless Motors
What gives brushless vibration motors a long life? The clue’s in the title!
The precious metal brushes are typically the most common source of failure that limits the lifetime of normal DC motors. They are integral to the operation of our eccentric rotating mass vibration motors in the ‘Vibration Motor’ section of our Product Catalogue.
Whilst our recent Application Bulletin demonstrated our miniature vibrating motors are achieving an MTTF in the region of 1,500 – 2,000 hours some applications demand even longer performance.
So to improve life the solution seems simple, find a replacement for the brushes! This is quite complicated, the job of the brushes was to reverse the direction of the current through the internal metal windings (this ensures a constant direction of rotation of the shaft).
This is achieved by sensing the position of the internal windings and electrically changing the direction of the current at exactly the right time. To do this, we use the Hall Effect to calculate the position of the motor and change the drive signal accordingly. For more information on this, see Application Bulletin 018: Driving Brushless Vibration Motors.
Instead, with this blog post, we wanted to share an interesting infographic found on spingarage.com. Those interested in seeing exactly how the drive signal changes with the output from the Hall Effect sensors can study the image below.
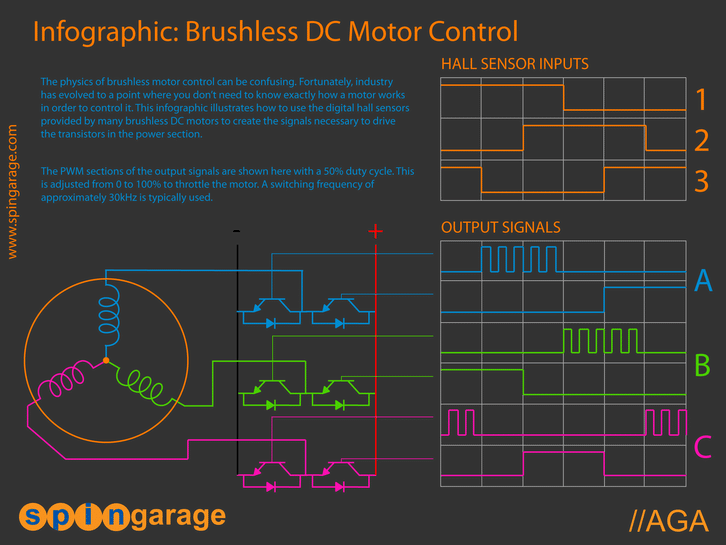
Thankfully if you find the graphics confusing, you don’t need to fully understand them. Our 910-101 has an integrated driver chip that handles the communication automatically, and we have a suggested circuit for the 912-101 that you can easily implement.
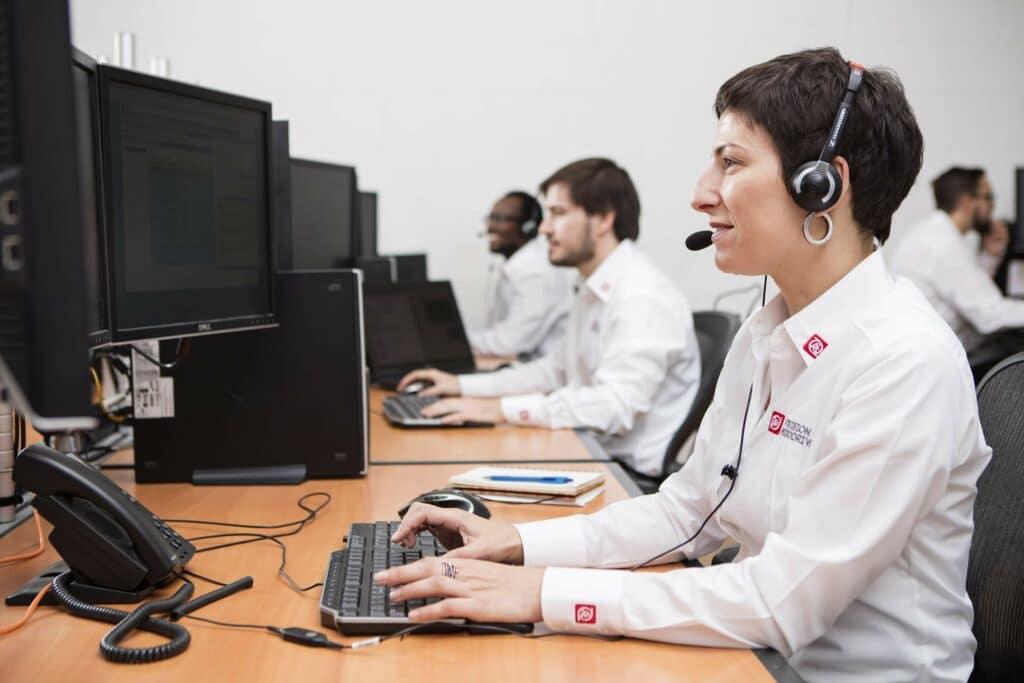
Get in touch
Speak to a member of our team.
Motor catalogue
Looking for our products?
Reliable, cost-effective miniature mechanisms and motors that meet your application demands.
Discover more
Resources and guides
Discover our product application notes, design guides, news and case studies.
Case studies
Explore our collection of case studies, examples of our products in a range of applications.
Precision Microdrives
Whether you need a motor component, or a fully validated and tested complex mechanism – we’re here to help. Find out more about our company.