Risks of using under-powered batteries in haptics
Looking for our Haptics range? View our main Haptics hub here.
Many haptic applications, in particular, wearables, face severe trade-offs in overcoming limitations in power supplies. A battery’s volume is directly related to a host of other desirable specifications, such as voltage, current, or capacity. For many designers, squeezing as much life out of their battery is one of their greatest challenges.
In this blog post, we’ll look at each of these limitations in turn before discussing one of the most common, but often unsuitable, battery choices.
Challenges Faced
Limited Voltage
One of the great features of a DC motor is that its output speed can be easily controlled by varying the voltage. Quite simply, limiting the voltage to a vibration motor reduces the speed and therefore the vibration amplitude.
As an example, using a common AA battery (1.5V) to drive the 307-103 would create an amplitude of ~2.5 G, instead of its rated 7 G. Two AA batteries in series would address the shortage in voltage, but perfectly highlights our volume/voltage trade-off.
If the voltage is severely limited, the motor will not even start – which is an even greater issue for those looking to take advantage of low-profile coin motors as they often have a higher start voltage (due to their short length).
It should be noted that a battery’s quoted voltage is not constant for all levels of charge – as a battery depletes, its output voltage drops. So, those looking to use a low voltage battery that only just meets a motor’s start voltage should seriously reconsider their battery or motor choices.
Limited Current
In practice, limiting the current will have the same effect as limiting the voltage: the motor will either turn slower or fail to start.
However, motors don’t draw a constant current. Instead, as the motor accelerates to its rated speed (assuming the Rated Voltage is applied) it draws a greater current. With a limited current the motor will take longer to reach its target speed, which can have performance implications for haptic applications. If you’re looking to generate a simulated “click”, or a similar effect that relies on a sharp rise time, a limited current will greatly reduce the crispness of the haptic effect – quick stop-start functions like double clicks will be most affected.
In addition, the current from the battery is not dedicated to the motor – it must be shared across all the components. For digital electronics like drivers or microcontrollers, this is a real issue. If the motor draws excessive current which causes the controller to reset, the product may become unfunctional every time the motor plays an effect. Capacitors can be used to provide extra current as required but will drain the battery quicker as they store energy (which potentially may not be used).
Again, using our example of the AA battery above, the trade-off with battery volume is visible when we place a second battery in parallel. This would keep the output voltage (from the batteries) at 1.5V, but with two batteries from which to draw the peak current is doubled.
This touches on a final challenge with batteries and their output current – many have a peak output current on their datasheets. For extremely low-profile batteries, this peak is far below the motor’s Maximum Start Voltage. Always check the datasheet of the battery and compare it with your proposed motors.
Limited Capacity
Battery capacities are quoted in milliamp hours, which can be interpreted as how many hours the battery can provide 1mA of current at its rated voltage or how many milliamps it can provide for 1 hour (see “How Long Will It Last?” here). However, calculating how long a battery might last with a specific vibration motor is challenging for two reasons.
First of all, it can be extremely difficult to measure how much current a vibration motor plays across a specific effect. If your application makes use of lots of different effects, you might have to estimate expected user behaviour (to verify the frequency of each effect) and the average current draw across each effect. An alternative method would be to simply test your chosen battery and motor by repeatedly playing the effect and counting how many you can produce from a single charge.
Secondly, the two interpretations of mAh are simply guidelines. In actual fact, batteries discharge much quicker with higher current draws, as shown below. Instead, a battery’s datasheet or manufacturer should be able to provide detailed figures about how test conditions under which they measure the capacity. Again, check the peak output current to see if this is a recommendation (that you shouldn’t exceed or it voids the datasheet values) or an actual limit of the battery (that it cannot reach).
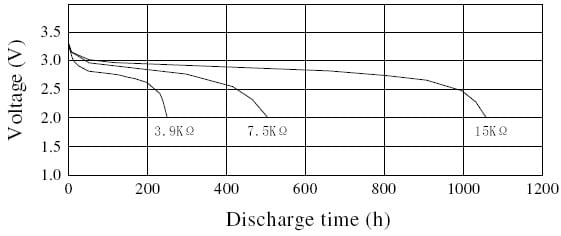
The CR2032 and coin cell batteries
This CR2032 battery is one of the first considerations that comes to mind for many of those first venturing into prototypes, however, it suffers from many of the limitations listed above.
Naturally, its low profile makes it attractive for fitting into space-restricted housing, however, this comes with a limited voltage, peak output current, and capacity. At first blush, the 3V output might also appear to be suitable for many motors. However, even a 30mA current draw would be considered extremely high as these batteries are designed to give an average current of 0.2mA. This is far below even our lowest current intensive 3V vibration motor, the 304-121.
In fact, looking at a list of coin batteries with standard discharge currents, the highest value is typically 0.2 mA – even the CR2450 which is billed as being designed for high current devices suggests a value of 3 mA.
In addition, the CR2032 and many other off-the-shelf coin batteries are typically non-rechargeable. For many users of wearable haptics, it is common to recharge their device rather than replace the battery as it reduces ongoing running costs and is generally more manageable (not to mention environmentally sustainable).
Instead, at Precision Microdrives we would recommend using batteries that are specifically designed for haptic applications.
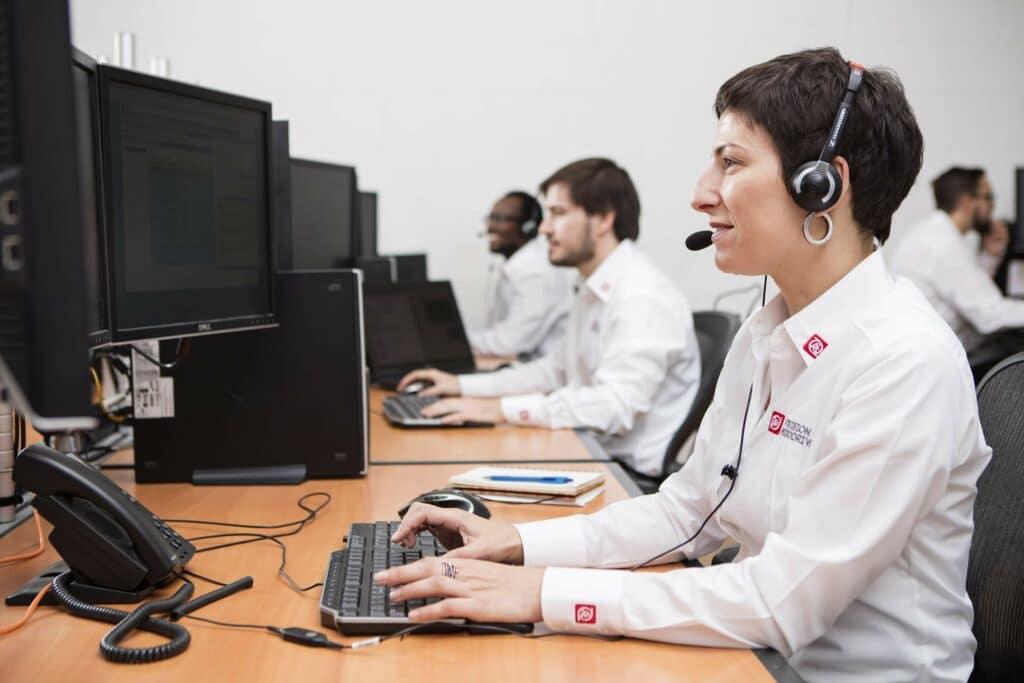
Get in touch
Speak to a member of our team.
Motor catalogue
Looking for our products?
Reliable, cost-effective miniature mechanisms and motors that meet your application demands.
Newsletter
Sign up to receive new blogs, case studies and resources – directly to your inbox.

Sign up
Discover more
Resources and guides
Discover our product application notes, design guides, news and case studies.
Case studies
Explore our collection of case studies, examples of our products in a range of applications.
Precision Microdrives
Whether you need a motor component, or a fully validated and tested complex mechanism – we’re here to help. Find out more about our company.