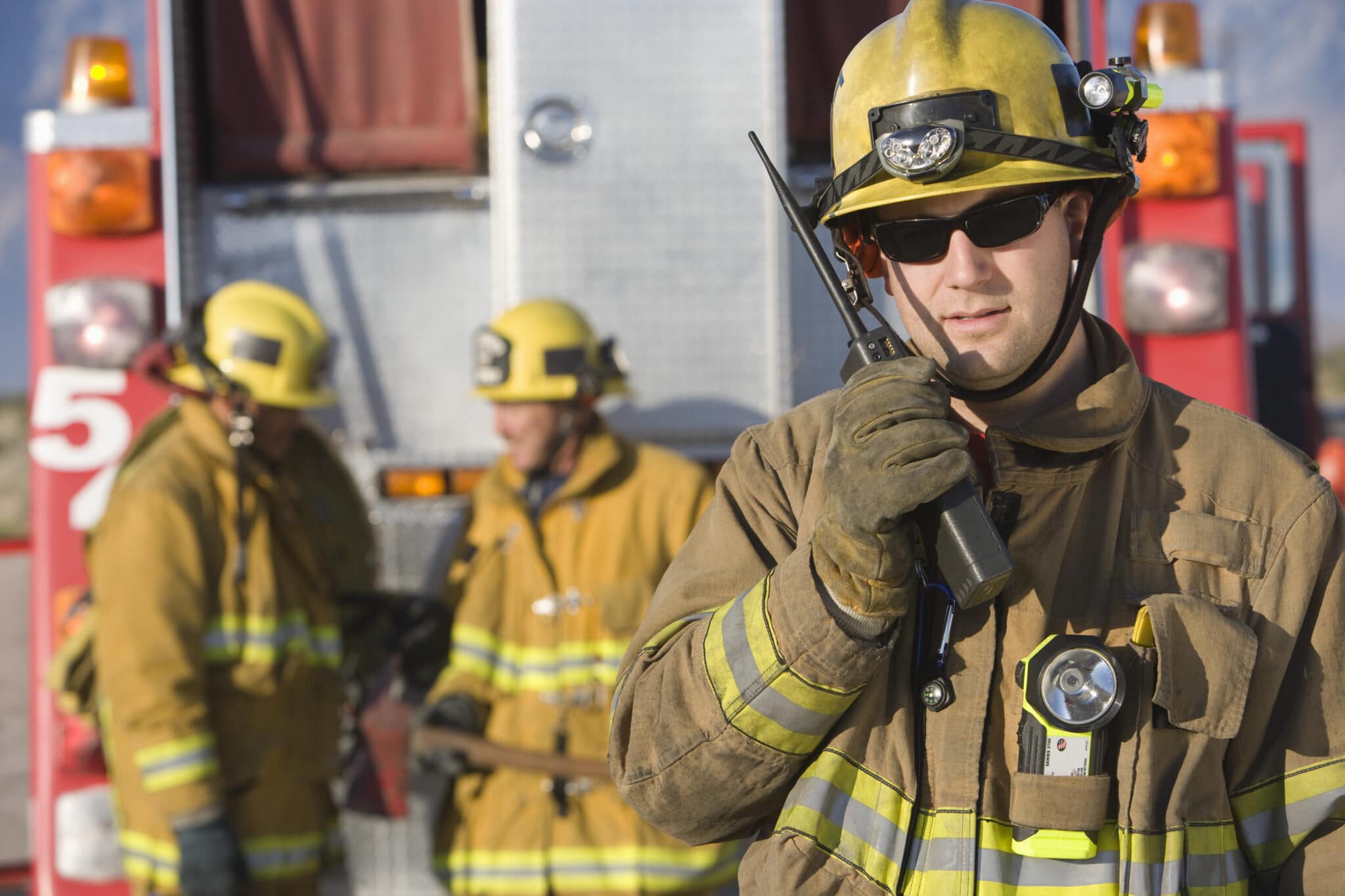
Case study
Emergency services ruggedised radio
- Ruggedised handheld radio for emergency services.
- Vibration Alerting to indicate incoming message or call.
- High performance ruggedised vibration motor with PCB backpack interface.
Challenge
- The customer was updating a well established emergency services radio. The previous generation radio had experienced multiple issues with the vibration alert feature.
- They wanted to upgrade the vibration intensity and address reliability issues that had plagued the previous model. This meant finding a new supplier.
- The radio needed to withstand extreme temperatures, a profile of ‘active’ and ‘rough’ use, as well as penetrate a new generation of more protective fire fighting clothing.
Solution
- We were lucky enough to enter this project with a clear list of improvements required for the next generation radio.
- Our engineers uprated the motor windings, bearings and eccentric mass.
- We upgraded the motor shaft and added / enclosed the motor with a rubber suspension cover. This reduced audible noise from the motor and enabled it to withstand accelerated drop tests.
- We undertook a design for manufacture review with the customer’s manufacturing engineers. This resulted in a PCB backpack with gold plated connection springs to speed up assembly.
Results
- The new generation radio was released with a long list of improvements that had been requested by the worldwide emergency services user community.
- Firefighters were pleased with the new radio’s ability to penetrate protective clothing when the radio was secured to chest and hip belts.
- Police and security forces appreciated the new radio’s ability to withstand repeated drops and continue functioning.
- Our customer’s production line staff were able to assemble radio’s quicker because of our assembly optimised features.
Project Scope
Emergency radios to withstand high temperatures, impacts, and vibrate through protective clothing
Vibration alerting is a key feature for many applications. This is especially true when communication can mean life or death, such as this emergency services radio, which was widely used throughout the world.
Our customer had built a loyal following, but there were some issues around the vibration motor in a previous generation (and from another motor supplier) radio that needed to be addressed.
The customer engaged us at the start of a redesign on the next generation radio, and helpfully had a very specific list of the problems affecting the previous design and motor. We methodically worked through each problem to find an solution. The result was a more expensive motor assembly, but one which worked much better, and was far more robust.
The new radio can now alert fire fighters when fully suited, and take a lot more abuse than the previous generation. The end customer is able to manufacture quicker to thanks to features built into the motor to aid end product assembly.
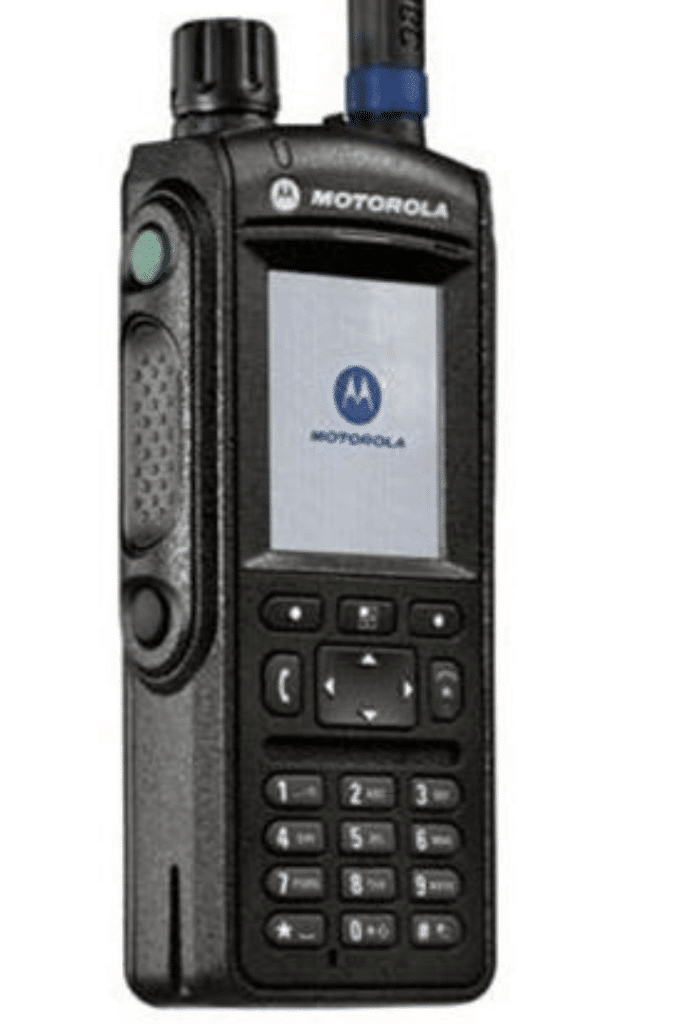
STAGE 1
Designing for application
- Following a number of tests on a customer vibration analysis machine, we made changes to the motor’s windings and eccentric mass.
- We also uprated the shaft and designed a rubber suspension cover to withstand impacts.
- We worked with their manufacturing engineers to implement a spring / pad electrical connection method, to simplify end assembly.
STAGE 2
Testing and validation
- We designed a new Tungsten weight with raw materials sourced in compliance with necessary Dodd-Frank anti-conflict minerals regulations.
- On initial prototypes the vibration performance was great, but longevity suffered. We used our testing validation process to find a more suitable load point for the motor and adjust the windings accordingly.
- We built a customised accelerated drop test to validate the ruggedness of the new design.
STAGE 3
Mass production
- We replaced leads and connectors with a PCB back-pack carrying gold plated surface mounted springs.
- This reduced the radio assembly time by 20 seconds per radio.
- It also eliminated a common failure mode identified at the start of our design review – vibration fatigued wire joints.
- Our dedication to quality consistency, focus on improved performance and continued commitment to investing in advanced testing technology, means radios with our motors, continue to serve with strength.
CASE STUDIES
We supply motor and mechanism solutions for all sorts of applications
-
Gas sampling equipment
Designing a new battery powered handheld instrument to implement a patented gas analysis method.
View Case Study
-
Medical patient simulator
Patient simulator for first-aid cardiac arrest training required a vibration motor to haptic simulate a heartbeat.
View Case Study
-
Swarm robot research linear actuator
Challenging technical and unique application for swarm robotics for a European robotic research Institution.
View Case Study
-
Bench-top pill counting machine
Bench-top medical instrument used a vibration motor to aid movement of pills through instrument pathways.
View Case Study
-
Weather balloon measurement lab
High volumes of low-cost reliable single-use motors for weather balloon measurement lab.
View Case Study
-
Surgically implanted pacemaker motor
Brushless vibration motor within a FDA Class III implanted medical pacemaker device.
View Case Study
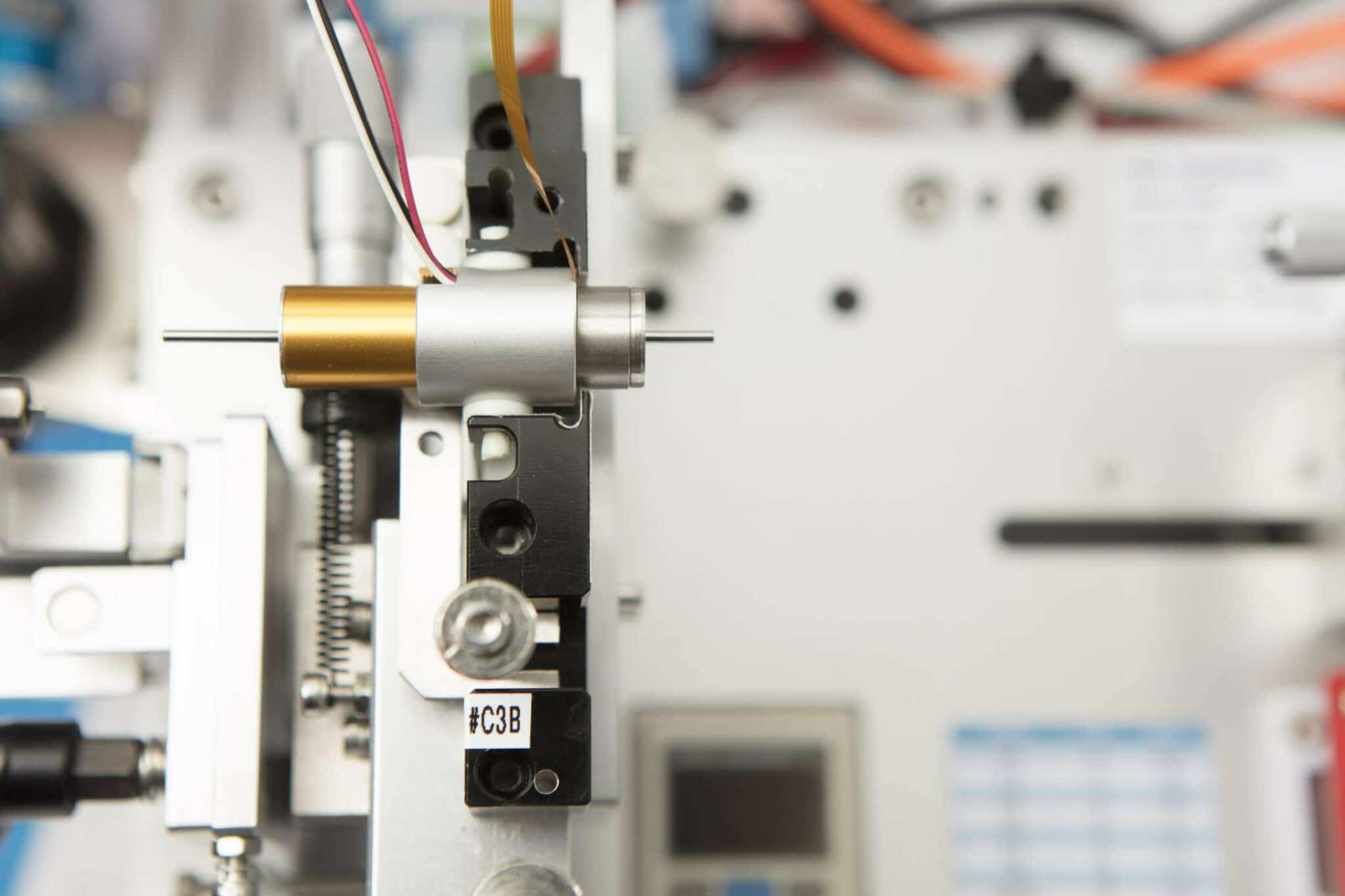
MORE THAN YOUR AVERAGE MOTOR SUPPLIER
We manage your risk
We manage your risk through optimised design and rigorous testing, protecting your application and intellectual property, fulfilling your performance requirements, whilst reducing your lifecycle costs.
MOTORS & MECHANISMS
Precision products
-
DC motors
Iron-core, coreless and brushless DC motor technologies in a wide range of form factors and sizes, with off the shelf
View Page
-
DC gear motors
Building on our range of DC motors, we integrate spur and planetary gearboxes, from 6mm to 60mm frame diameters.
View Page
-
Vibration motors
With every vibration and haptic technology covered, we’ll help you select the best vibrating solution for your application.
View Page
-
Haptic feedback
Practical and reliable, low noise and high quality haptic feedback solutions for all types of application user interface.
View Page
-
Mechanisms
Custom motor assemblies designed and manufactured to your requirements. A turnkey service from design inputs to mass production.
View Page
Discover more
Resources and guides
Discover our product application notes, design guides, news and case studies
Industries we serve
At Precision Microdrives we design and manufacture customised electric motors and mechanisms across a number of industries.
About PMD
Whether you need a motor component, or a fully validated and tested complex mechanism – we’re here to help.