Linear Resonant Actuator Vibration Analysis with Pulse Width Modulated Signals
Introduction
We were delighted to be contacted by Nick Inoue who has been researching our C10-100 Linear Resonant Actuator for Cardiff University School of Engineering. He offered some great analysis of our LRA and was kind enough to provide us with a detailed report on his findings.
The main focus of the project was to look at how the vibration strength of the LRA varied with pulse width modulated (PWM) signals of different duty cycles. We have excerpted a section of his research into this blog post and offered a couple of conclusions based on his findings.
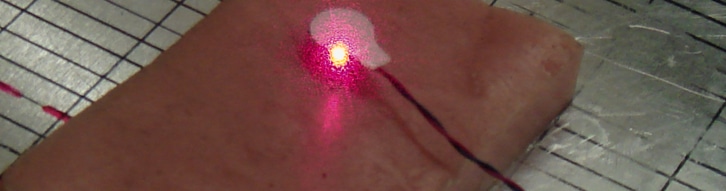
LASER Vibrometer
The laser vibrometer works by splitting a laser beam and directing one beam onto the vibrating object, in our case an LRA. The LRA reflects the laser back, and this reflected beam is then joined to the original split beam. The reflected LRA beam and original laser beam are then both measured by the photon detector. See the diagram to the left for a better understanding.
This enables the use of the Doppler Effect to measure the displacement, and therefore vibration strength, of the LRA. The reflected beam’s frequency increases as the LRA moves towards the laser vibrometer and decreases as it moves away. When combined with the original reference beam, a beating frequency is created which the photon detector can measure. For more information on how the Doppler Effect works see this article.
The LRA can now be measured with great accuracy, providing excellent quantitative data about vibration strengths. Using this setup, the team then looked into how the LRA performs with a variety of duty cycles.
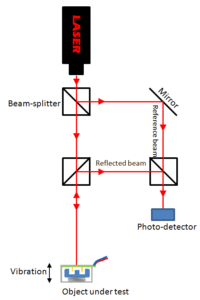
Vibration Testing with the LASER Vibrometer
To simulate direct contact with a human, the LRA was placed on a realistic skin substitute. Living skin could not be used as any movement by the person would skew the results.
The laser vibrometer used in the experiment is a Polytec PSV-400 scanning head. It can scan multiple points of reference to see the vibration modes over a surface. This feature was used to check the LRA was indeed only vibrating in one direction, unlike our eccentric rotating mass vibration motors.
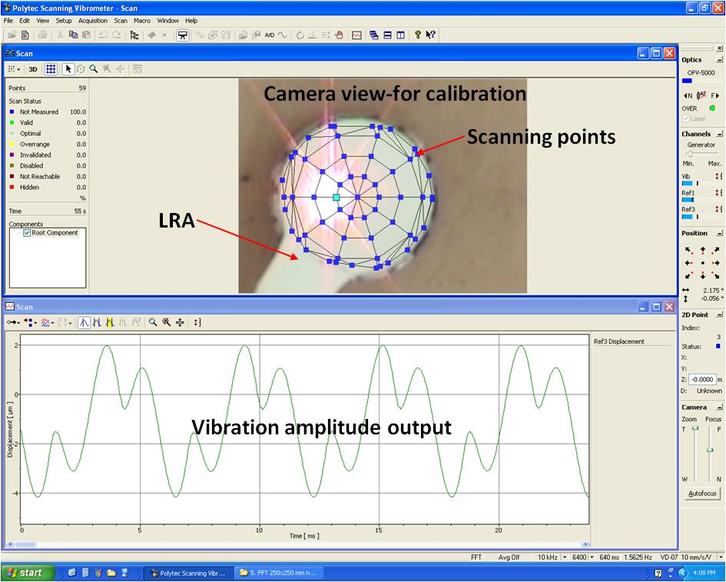
After confirming the LRA moved in one direction, further analysis could take place with measuring only one point on the LRA.
The team at Cardiff University then measured the displacement amplitude of the vibration motor when driven with PWM signals of varying duty cycles. It is worth mentioning that the PWM signal was generated in the software of the microcontroller. This means that varying the duty cycle can impact on the resulting frequency, this is because the exact processing time of each software command is difficult to ensure with high-level languages.
LRAs are very sensitive to fluctuations in frequency and must be driven very close to their resonant frequency for maximum vibration amplitude. Thankfully the measured frequency at each duty cycle was close to constant around 173 Hz.
The results were interesting. Below is a plot of the displacement of the LRA at 5 different duty cycles:
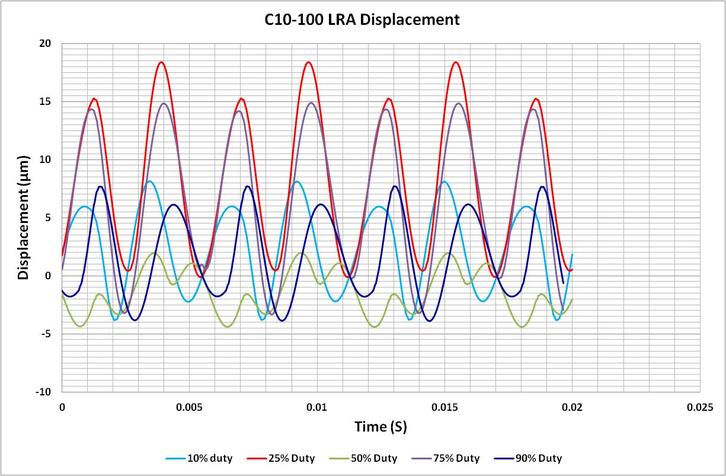
From the graph above we can see that the 25% and 75% duty cycles produced the greatest displacement. Most would have expected the 50% duty cycle to result in greater vibrations as it is the waveform that closest resembles the LRA’s normal sine wave input.
The following graph is an FFT of the results of each duty cycle.
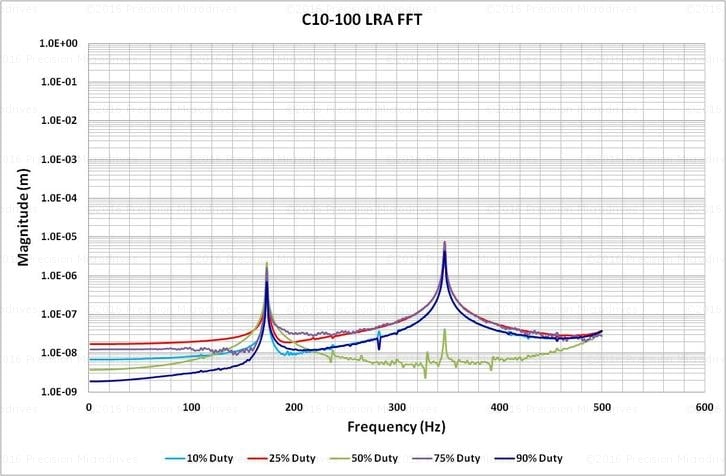
Here we see the fundamental at 175 Hz and a harmonic at 350 Hz. This is to be expected, however, there is another surprise in the harmonic has greater displacement than the fundamental.
Another interesting note is that when Nick performed a subjective test by placing his finger on the LRA he found that the 50% duty cycle resulted in the strongest vibrations. This was in contradiction to the test results of the laser vibrometer.
Discussion of Results
At first glance, the results can easily seem erroneous. However, we believe we can explain the project’s findings.
The research appears to draw three conclusions, the third contradicting the first two:
- The LRA produces stronger vibrations at the second harmonic 350 Hz
- The LRA produces stronger vibrations with 25% or 75% PWM duty cycles
- The LRA produces stronger vibrations with 50% duty cycle when measured by human touch
Whilst one could conclude that humans are simply more sensitive to vibrations at 175 Hz than 350 Hz, we believe that the first two statements derive from a combination of the nature of driving PWM signals and the synthetic skin.
First, an important feature of pulse signals (such as the PWM) is that the FFT of 25% and 75% duty cycles shows us the second harmonic is very close or equal to the fundamental. Below we have included screenshots taken from a quick hookup up of a signal generator and an oscilloscope in our lab. They show the PWM signal at the top and the corresponding FFT below:
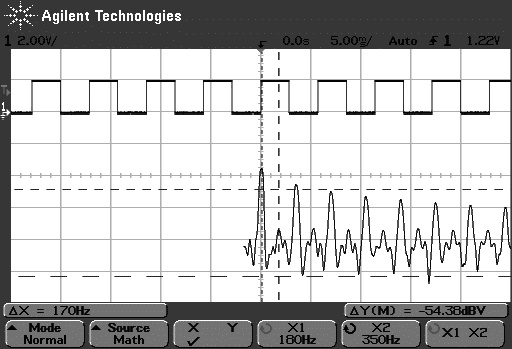
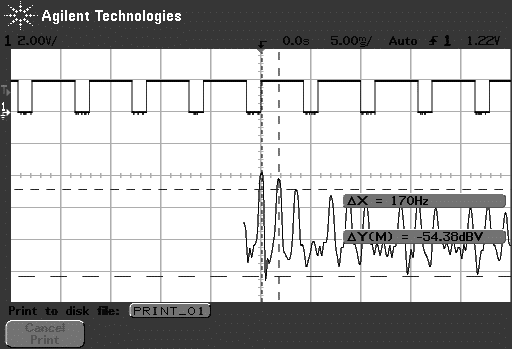
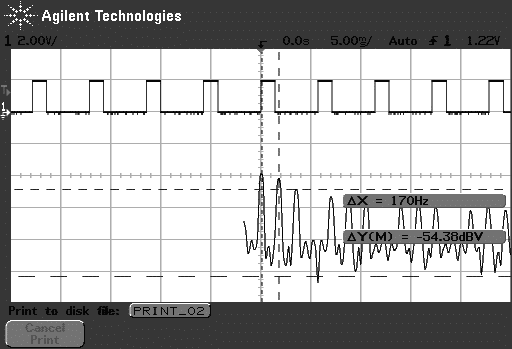
Secondly, once the LRA is placed in contact with the artificial skin, the resonant frequency of the system changes. This is because the skin is now considered part of the system, similarly how a mobile phone’s casing becomes part of the vibration system once it is attached to the vibrating motor.
It is likely that the skin has a resonant frequency closer to the second harmonic 350 Hz, and because there is little difference between the fundamental and second harmonic of 25% and 75% duty cycle signals the vibration amplitudes are greater at 350 Hz.
Finally, we can explain the results of the human touch with some understanding of the human skin. The mechanoreceptors in our fingers are much better at responding to lower frequencies of vibration, usually less than 300 Hz. The vibrations of the LRA, therefore, feel stronger at the fundamental harmonic, where the FFT of the vibration analysis shows us a 50% duty cycle produces the greatest vibration magnitude.
Conclusion
Driving an LRA with a PWM signal can be extremely difficult. Many microcontrollers have accurate PWM generators, however, these are often at a frequency much higher than the resonant frequency of the LRA. If you are not inclined to divide the clock of the microcontroller to a suitable frequency, then the other option is to generate the PWM signal manually in software using loops. However, this is often unpredictable and ties the microcontroller to the single task of constructing the PWM when required.
The simplest method of overcoming this is to use a dedicated chip for driving the LRA, preferably one with an auto-resonance function. This enables the LRA to be driven at the correct resonant frequency without any change in the microcontroller’s software. Instead, the microcontroller can concentrate on other tasks, for example developing advanced haptic feedback waveforms.
You can see a summary of various LRA driving chips in this Application Bulletin.
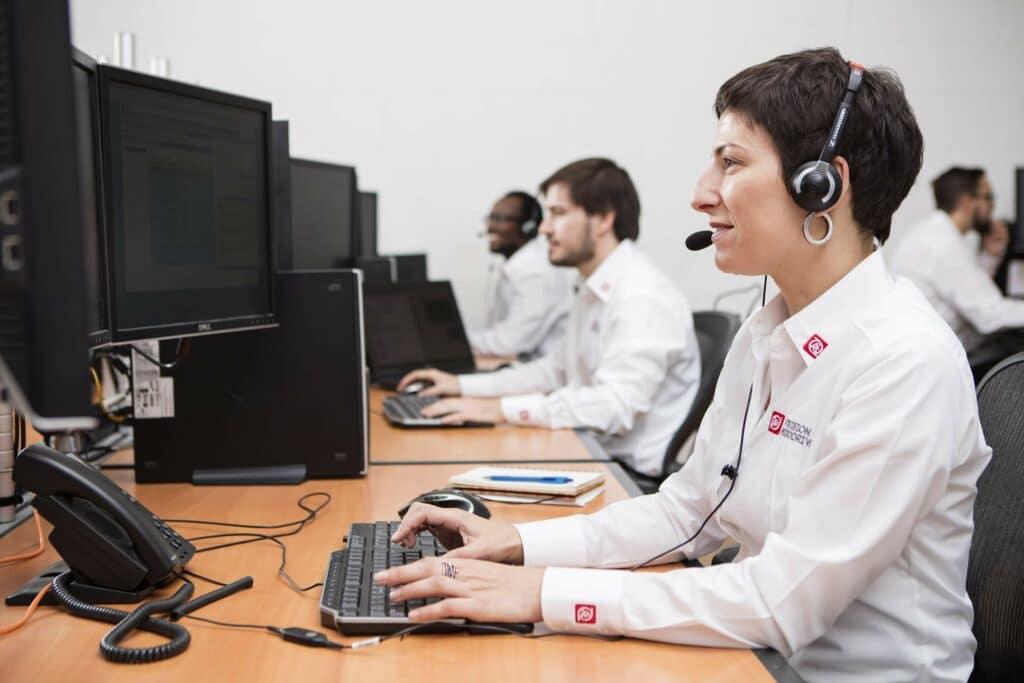
Get in touch
Speak to a member of our team.
Motor catalogue
Looking for our products?
Reliable, cost-effective miniature mechanisms and motors that meet your application demands.
Newsletter
Sign up to receive new blogs, case studies and resources – directly to your inbox.

Sign up
Discover more
Resources and guides
Discover our product application notes, design guides, news and case studies.
Case studies
Explore our collection of case studies, examples of our products in a range of applications.
Precision Microdrives
Whether you need a motor component, or a fully validated and tested complex mechanism – we’re here to help. Find out more about our company.