Gear Motor Integration and Customisations
12mm Spur Gear Motors
For your design flexibility, Precision Microdrives provides a range of 12 mm spur gear motors.
Your decision in selecting an appropriate 12 mm spur geared motor for your application and integrating and customising it will depend on the technical requirements of your application, and meeting safety and other operational requirements. First, consider the following 12 mm spur geared motors and evaluate their capabilities for your application requirements.
Our 12 mm spur geared motors, where 12 mm denotes the body diameter, offer a wide choice of parameters, from a technical specification point of view. Precision Microdrives 12 mm spur geared motors are available in two input voltages: 12 Volt and 3 Volt. These geared motors also have a wide range of gear ratios (for example, 29.5:1 for model 212-107 or 297.9:1 for model 212-103), varying speeds (for example, 125 rpm for model 212-106, or 22 rpm for model 212-103) and rated torques (for example, 5 mNm for model 212-106 or 40 mNm for model 212-103).
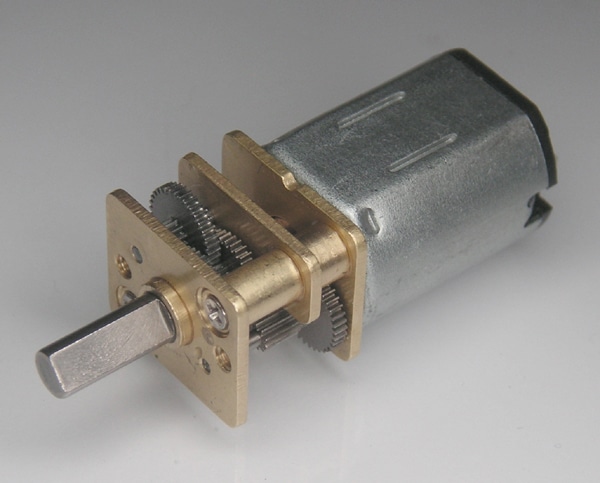
You should focus on other technical characteristics and operational features as well. A few 12 mm geared motors (for example model 212-113) have a double flat extended shaft,19 mm from the gear side. You can mount actuation arms or rollers on this shaft. There is another shaft that protrudes on the other end from the motor case, use this component for mounting encoders or other drive components for feedback control or actuation.
As a designer, you need to prevent the overheating of the end-cap terminals. This is possible when the terminals are rigidly connected to the commutator brush. Overheating can lead to a shift in the position of the brush, resulting in shorting and premature failure. You can prevent this by using geared motors that are supplied with leads and connectors pre-fitted, or with a PCB electrical integration.
Precision Microdrives geared motors are also suitable for operating in reverse. To accomplish this, you can mount precious metal brushes in the direction of the designated rotation. Do not do this with a carbon brush! You can also drive and operate the motors electrically in both directions with similar performance, assuming that the motor end-caps are not directionally biased. As a precautionary measure, you should run the motor with a lower rotor speed to minimise the reversing stress on the commutator brush.
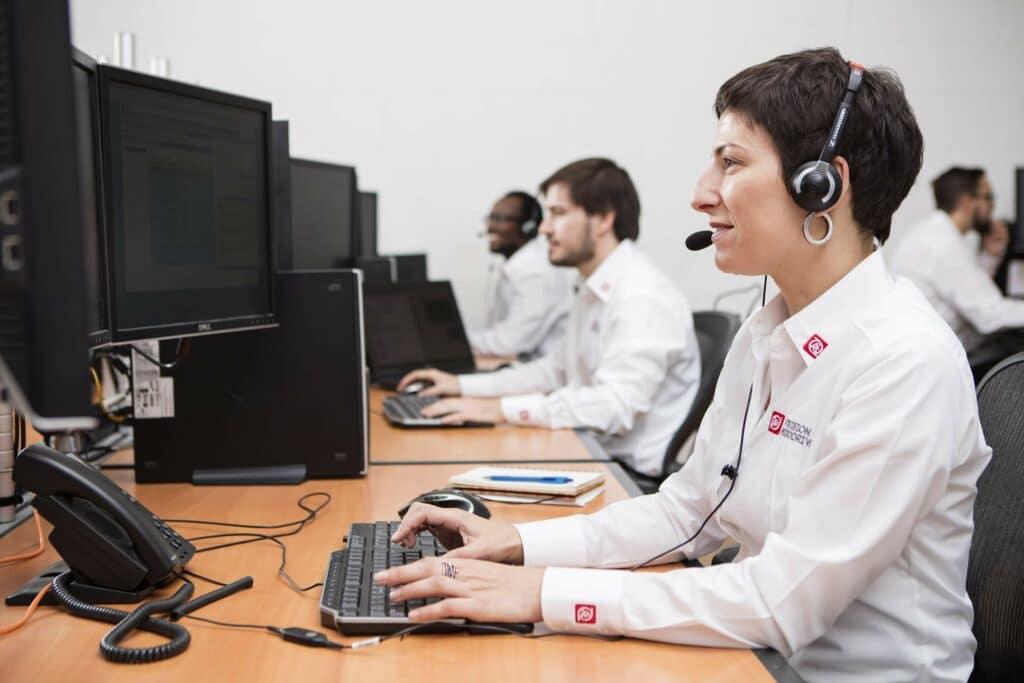
Get in touch
Speak to a member of our team.
Motor catalogue
Looking for our products?
Reliable, cost-effective miniature mechanisms and motors that meet your application demands.
Discover more
Resources and guides
Discover our product application notes, design guides, news and case studies.
Case studies
Explore our collection of case studies, examples of our products in a range of applications.
Precision Microdrives
Whether you need a motor component, or a fully validated and tested complex mechanism – we’re here to help. Find out more about our company.