Benefits of PCB Backpacks
Our larger DC motors commonly have terminal power pins, as opposed to SMD motors or ones with power leads. Whilst in some applications this can be a drawback, others appreciate the flexibility offered – bear in mind that larger motors have a much wider range of mounting considerations rather than simple surface mounting on PCBs or bulkheads. Often, motors are mounted in custom moulded plastics, which can be in locations relatively remote to the control circuit. In these instances, highly customisable lead orientations, lengths, and thicknesses can be an advantage.
However, simply running long leads between the motor and drive circuit isn’t always the best solution. Larger motors, in particular, can be (electrically) noisy and we recommend the use of capacitors or other dedicated filters to help with the suppression of EMI. It is best practice to place these components as close to the motor terminals as possible.
This is where products like “PCB backpacks” offer fantastic advantages. These small, custom-designed PCBs take advantage of the DC motor’s large, rigid terminals to mount circuit boards directly onto the motor themselves.
We can see from the photo above that a capacitor has been placed as close to the terminals as possible, whilst keeping the motor itself unmodified (which helps reduce design costs and lead times, and keeps MOQs down).
Whilst an extremely simple and cheap solution is to solder a capacitor directly to the terminals (as shown below), the PCB has some additional benefits.
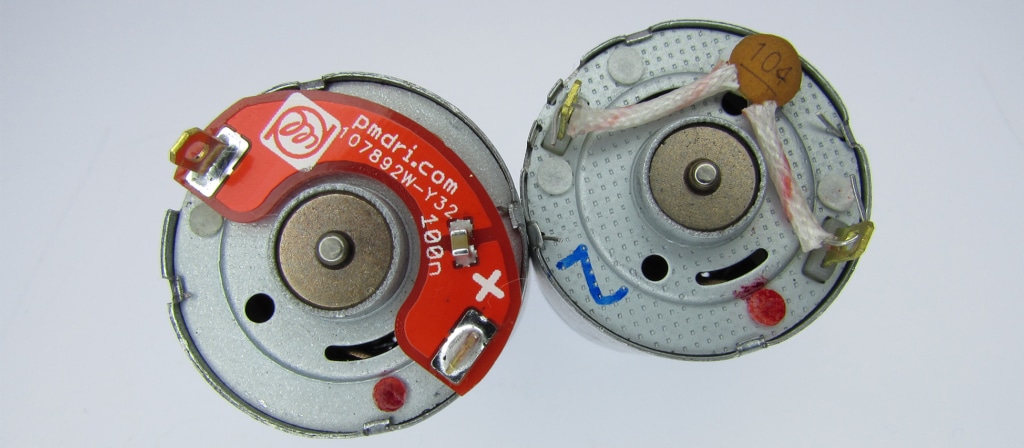
With a PCB, you can add in more components as required, such as a variable resistor. Below is an image of the 132-100, described in our AB-026: Sensorless Speed Stabiliser for a DC Motor.
PCBs also offer greater flexibility in electrical connectors for power leads. Using PCB Molex headers allow wires to be easily disconnected to help make remote boards and motors more serviceable.
Of course, there are limitations to the components that can be placed on this circuit board. For one, there is a clear restriction on space – you would not be able to place a great volume of components or ones that carried particularly high footprints / physical volumes.
In addition, components like capacitors at motor’s terminals aid electromagnetic interference suppression – not elimination. There is still enough noise generated to affect sensitive components, such as oscillators or other discrete digital chips. For example, you might find a simple timing circuit with a crystal oscillator and 555 timer would not perform very well on a PCB backpack and would be better kept on a separate control board.
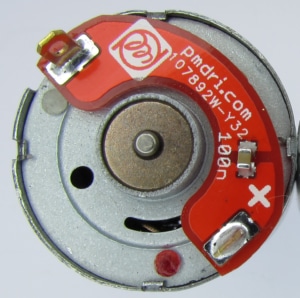
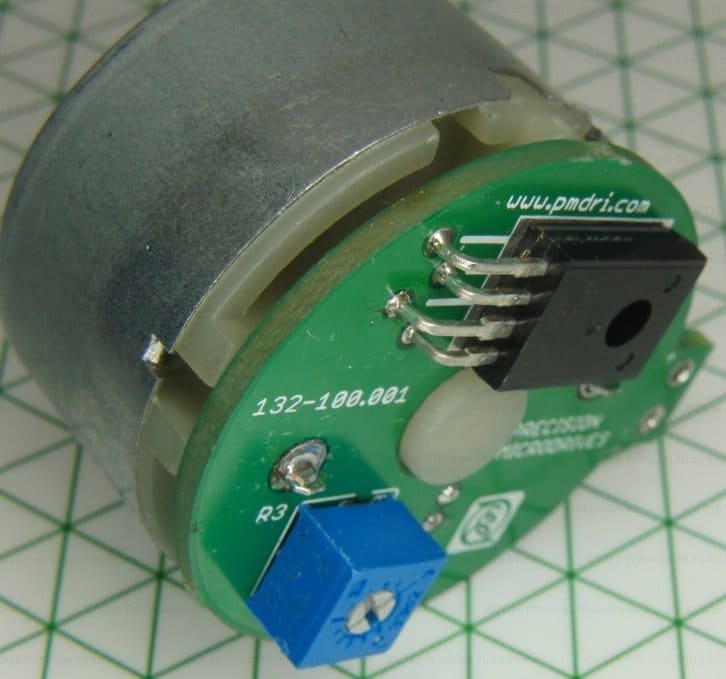
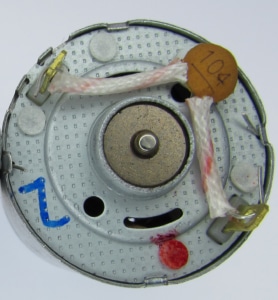
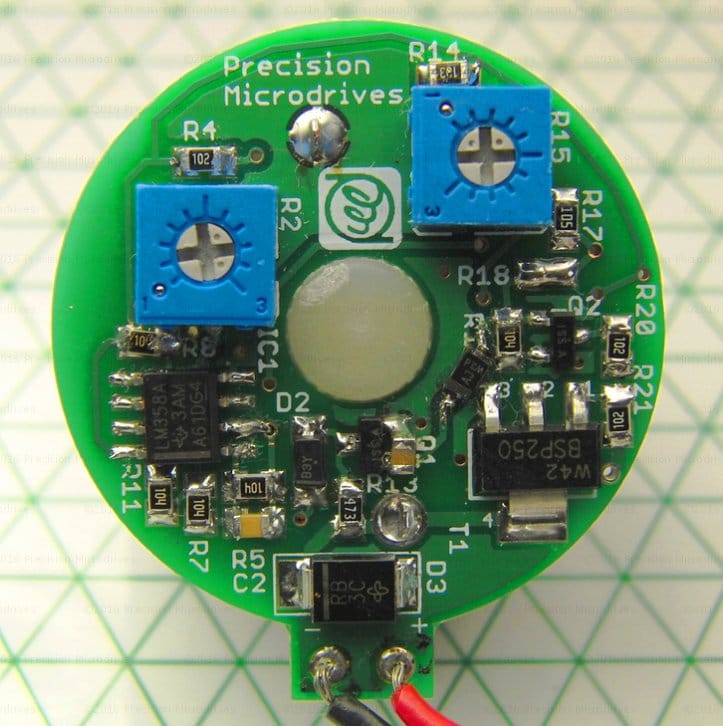
Despite these two small limitations, PMD has helped many companies design, manufacture, test, and supply DC motors with custom-made PCB backpacks. The images above show our 132-100 with a 100nF capacitor – but it is possible to develop much more complicated PCB backpacks, such as this analogue switching mode speed controller: If you have an application that might benefit from a custom made PCB, we can advise on the types of components and designs that are suitable for PCB backpacks and offer alternative solutions if they’re not. Simply contact our engineers at [email protected] and we’d be happy to discuss your application with you.
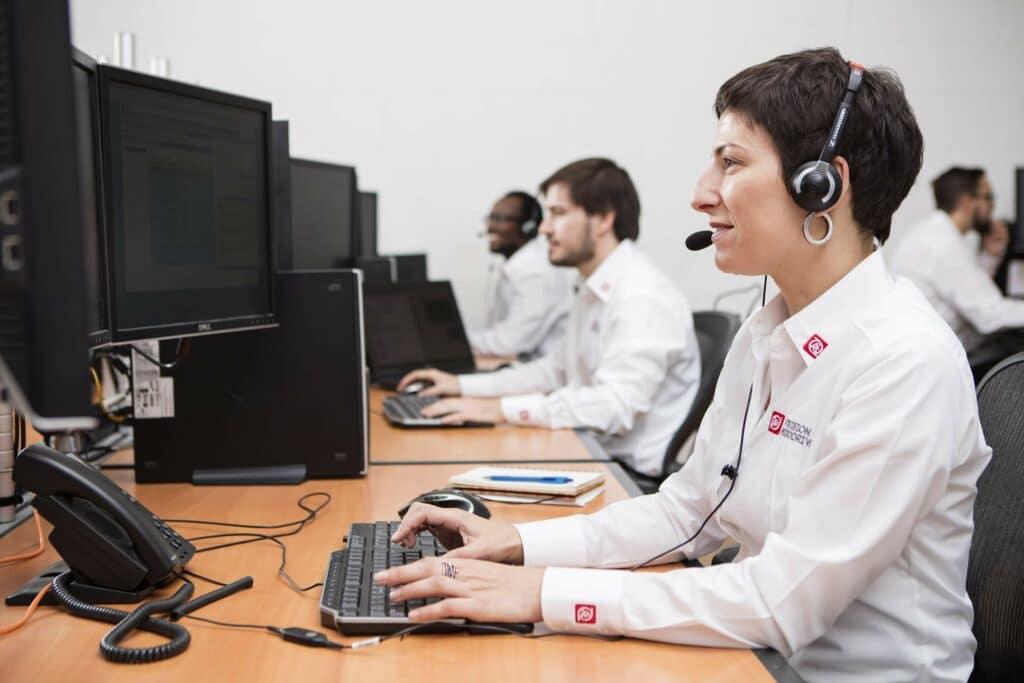
Get in touch
Speak to a member of our team.
Motor catalogue
Looking for our products?
Reliable, cost-effective miniature mechanisms and motors that meet your application demands.
Newsletter
Sign up to receive new blogs, case studies and resources – directly to your inbox.

Sign up
Discover more
Resources and guides
Discover our product application notes, design guides, news and case studies.
Case studies
Explore our collection of case studies, examples of our products in a range of applications.
Precision Microdrives
Whether you need a motor component, or a fully validated and tested complex mechanism – we’re here to help. Find out more about our company.