AB-004
Understanding ERM vibration motor characteristics
Overview
The Eccentric Rotating Mass vibration motor, or ERM, also known as a pager motor is a DC motor with an offset (non-symmetric) mass attached to the shaft.
As the ERM rotates, the centripetal force of the offset mass is asymmetric, resulting in a net centrifugal force, and this causes a displacement of the motor. With a high number of revolutions per minute, the motor is constantly being displaced and moved by these asymmetric forces. It is this repeated displacement that is perceived as a vibration.
Many mechanical engineering textbooks discuss the characteristics of ERMs, as a ‘rotating unbalance’, and do so in a negative context. Often engineers are trying to minimise the source of vibration from rotating machinery because it generates noise and causes excessive machine wear and fatigue. As a result, there is little literature on the theory of maximising the amplitude of vibration in applications.
This Application Bulletin has been made into a Video Application Bulletin which you can access on the Precision Microdrives website or directly on Vimeo. Click here to see VAB-02: How Do Vibration Motors Work?
Theory of creating vibrations with ERM vibration motors
Modelling Vibration Motors As A Mechanical System
The vibration produced by ERMs is an example of “Driven Harmonic Vibration”. This means there is an external driving force causing the system to vibrate, and this is also sometimes called forced vibration. The term ‘harmonic’ means that the system is forced to vibrate at the frequency of the excitation.
It is important to remember that in the case of the ERM model, the excitation input is not the DC voltage applied to the motor. Instead, it is the rotation of the mass around the central motor shaft. The mass’ movement can be modelled as a sinusoidal wave, shown below:
Here the function 𝐴𝑠𝑖𝑛(𝜔𝑡) is the excitation input, and the frequency of this sine wave is the frequency at which the ERM vibrates. In the real world, the DC voltage controls the speed of the motor (the two are directly proportional) and therefore the frequency, however, when modelling the ERM as a system, we will refer to the sinusoid as the input.
To analyse the behaviour of the ERM, we will approximate the system to having one degree-of-freedom (DOF). This means that the vibration will only manifest itself in one direction, and it makes the maths a lot simpler. We can accept this simplification because when dealing with small DC vibration motors, the displacement of the motor in other DOFs is sufficiently small that they are negligible.
The one DOF vibration model can be shown as a mass, connected to a spring, with a damping factor (drawn in the diagram as a dashpot). The equation of motion is built from the forces of these three components and the input force.
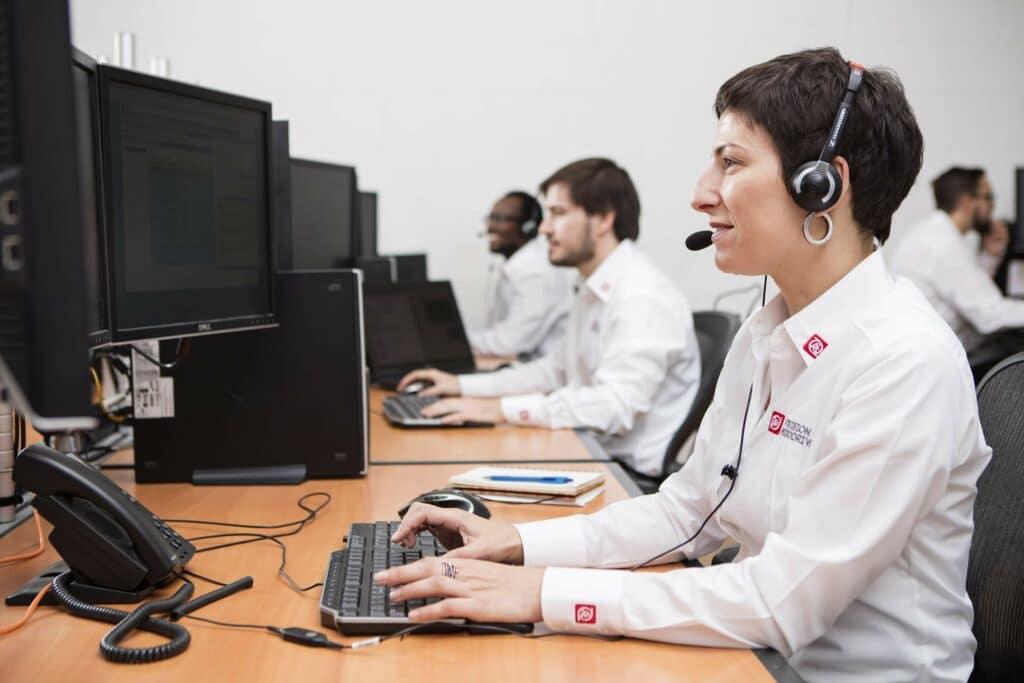
Get in touch
Speak to a member of our team.
Motor catalogue
Looking for our products?
Reliable, cost-effective miniature mechanisms and motors that meet your application demands.
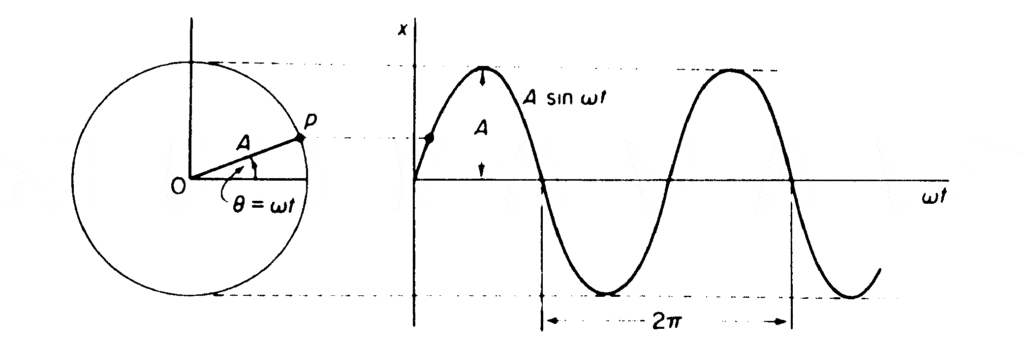
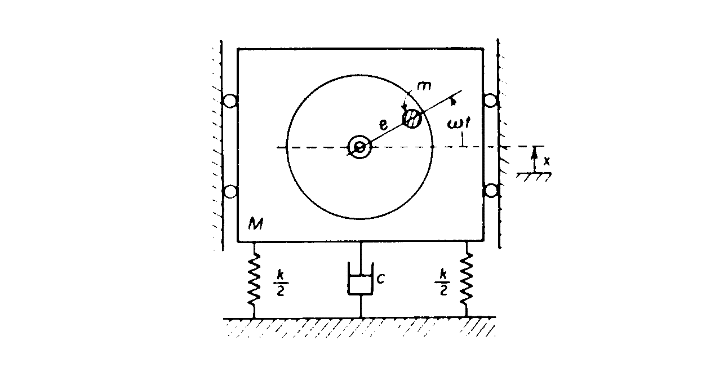
In the equations below, 𝑥 is the displacement of the eccentric mass.
The diagram above has two separate springs, each with stiffness 𝑘2 representing an overall stiffness 𝑘. This can be considered as one single spring with stiffness k which follows Hooke’s law, where 𝐹=𝑘𝑥.
The viscous damping is proportional to the velocity of the mass 𝐹=𝑐𝑑𝑥𝑑𝑡 (velocity is the derivative of displacement).
The mass of the ERM (excluding the eccentric mass) follows Newton’s second law of motion 𝐹=(𝑀–𝑚)𝑑2𝑥𝑑𝑡2 .
The sum of these three forces is equal to the input 𝐹=𝐹0sin(𝜔𝑡).
In which 𝐹0 is the centripetal force of the eccentric mass 𝐹=𝑚𝑟𝜔2.
Here, 𝑚 is the mass of the eccentric mass and is the distance from the motor shaft to the centre of the eccentric mass. This is sometimes called the eccentricity and referred to as,
such as in the diagram above. 𝜔 is the angular velocity of the motor.
We now have the equation of motion for the system:(𝑀–𝑚)𝑑2𝑥𝑑𝑡2+𝑐𝑑𝑥𝑑𝑡+𝑘𝑥=𝐹0sin(𝜔𝑡)
For electrical engineers this will appear familiar as it is similar to an RLC circuit in which the displacement is analogous to the electrical charge, the velocity to the current, and the force to the voltage:
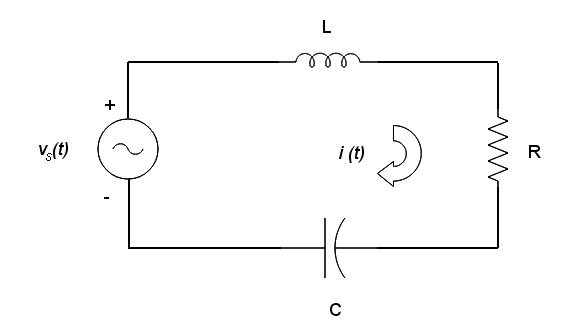
𝑑2𝑖(𝑡)𝑑𝑡2+2𝛼𝑑𝑖(𝑡)𝑑𝑡+𝑤20𝑖(𝑡)=𝑓(𝑡)
where :𝛼=𝑅2𝐿, 𝑤0=1𝐿𝐶√ , and f is the forcing function 𝑓(𝑡)=1𝐿𝑑𝑣𝑠(𝑡)𝑑𝑡.
Solving second order homogeneous equations is well documented but beyond the scope of this bulletin. Instead, these equations are presented as the foundations for modelling an ERM vibration motor as a mechanical system.
ERM As A Circuit Component
Equivalent Circuit
The equivalent circuit of a series connected DC motor, from which an ERM is built, is shown below.
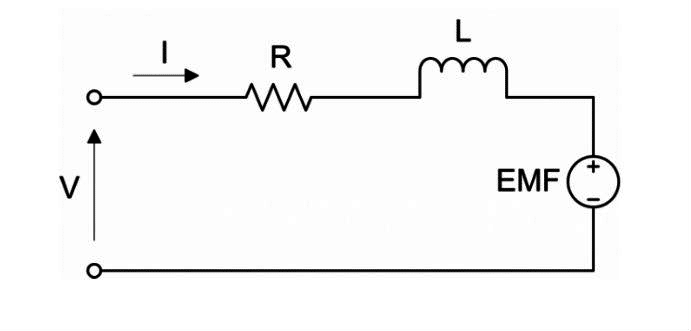
The winding inductance 𝐿 is a result of the mechanical design of the armature. It is an adverse factor for the motor since it works against the reversal of current flow in the armature. Coreless or coin motors are less susceptible to winding inductance because the smaller mass of these motors improves their dynamic performance. However, winding inductance can be used to store current in pulse-width modulation drive systems.
The winding resistance 𝑅 is a purely parasitic element that is responsible for the majority of losses in the motor. As the current increases, the loss from 𝑅 increases, and the motor efficiency reduces.
If the motor has leads, these will add to the total resistance and inductance seen at the terminals, and these values will increase with the length of the wires.
The Electromotive Force (EMF), also called back EMF, is the voltage that appears at the brush terminals when the shaft is rotating. The EMF has an internal resistance of zero. The voltage amplitude is strictly proportional to the shaft speed and its polarity depends on the direction of rotation. The linear proportionality between EMF and speed is defined as the motor voltage constant, 𝐾𝐸. which is typically expressed in 𝑣𝑜𝑙𝑡𝑠𝑘𝑟𝑝𝑚. As the EMF is proportional to the shaft speed, its voltage can be given:𝐸𝑀𝐹=𝐾𝐸𝜔
Where is the rotational speed of the motor measured in krpm.
We can easily see the linear relationship between speed and voltage in the equation for the equivalent circuit in steady-state:𝑉=𝑅𝐼+𝐸𝑀𝐹=𝑅𝐼+𝐾𝐸𝜔
In a permanent magnet DC motor the current in the circuit is proportional to the torque of 𝑇:𝐼=𝑇𝐾𝑇
Where 𝐾𝑇 is the motor torque constant, usually expressed in 𝑁𝑒𝑤𝑡𝑜𝑛𝑀𝑒𝑡𝑒𝑟𝑠𝐴𝑚𝑝 and 𝑁𝑒𝑤𝑡𝑜𝑛𝑀𝑒𝑡𝑒𝑟𝑠𝐴𝑚𝑝≈0.00706×𝑂𝑢𝑛𝑐𝑒𝐼𝑛𝑐ℎ𝑒𝑠𝐴𝑚𝑝.
The chart below shows how speed and current are related to the torque. Four parameters fully describe these relations: no-load current and stall current, and no-load speed and stall torque. The values will then be different for every motor.
Basic Control
The simplest way to drive an ERM motor is to connect the terminals / leads to a constant voltage DC source, at the motor’s rated voltage. A constant voltage will drive the motor at a constant speed, and hence constant frequency and vibration amplitude until the supply is switched off.
ERMs will work over a range of voltages, but note that we quote a ‘start voltage’ which must be observed in order to guarantee that the vibration motor will start every time. As the applied voltage is increased, the vibration frequency increases proportionally, and vibration amplitude will all increase as with a square; remember that 𝐹0, the amplitude of the centrifugal force, equals 𝑚𝑟𝜔2. The ERM current is proportional to the torque ‘load’ seen by the motor. As vibration energy is taken out of the ERM system, the torque required to continue spinning the eccentric mass will increase, and so too will the current.
This explains why the current draw of a loosely held vibration motor is greater than the current draw when the same motor is clamped tightly. In the latter case, less vibration energy is being removed from the ERM system.
These phenomena are represented below in a Typical Performance Chart taken from the datasheet for our 304-109 ERM Vibration Motor (part has since been depreciated).
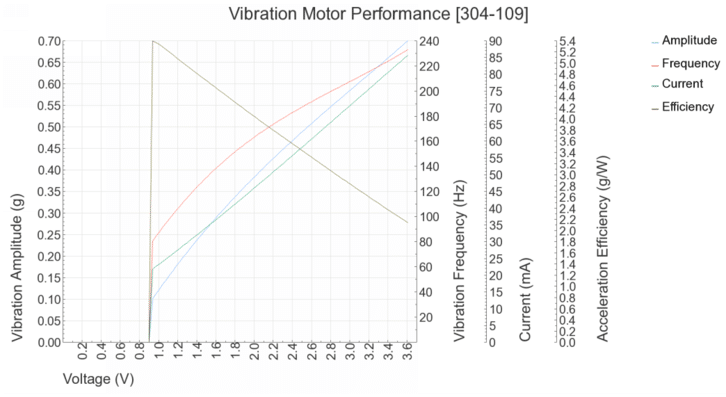
There are many vibration motor driver ICs available on the market, with some specifically designed for vibration or haptic feedback solutions. A simpler solution is to use a single transistor, and a more complex topology for increasing motor control is an H-Bridge. The H-bridge allows the user to easily change the polarity of the voltage applied to the motor, and therefore control the direction of the motor rotation.
Whilst the direction of the motor rotation may not be important for the user it does introduce the concept of ‘active braking’, which reduces the time taken to stop the eccentric mass; this is particularly useful for haptic feedback applications. The circuitry of the H-Bridge is explained in the previous article App-Bulletin 002: Discrete H-bridge Circuit For Enhanced Vibration Motor Control.
Conclusion
We have derived the equation of motion for an ERM vibration motor with one degree of freedom. Looking at the components of this equation, we can see that the strength of vibration produced by the motor is affected by the mass of the eccentric weight, the distance between the eccentric mass and motor shaft, and the speed of rotation. The motor itself and what it’s built into will also affect the equivalent values for stiffness of spring, the dampening characteristics, and mass of the ERM, which in turn will impact the level of vibration.
Fortunately, for our customers’ sanity, we offer typical ‘nominal vibration’ values for all of our motors on datasheets. These figures which are expressed in units of G (acceleration relative to 9.8 m/s2) relative to a 100g mass, remove the need for complex modelling. They are a pragmatic reflection of how the motor would perform in a typical hand-held application (e.g. a mobile phone), and can also be used to compare the vibration amplitudes of all our motors relative to each other.
When considering an ERM within a circuit design, we have provided an equivalent circuit and explained which performance parameters are linked and how they may vary in the application. We have also suggested further reading for the more advanced driving techniques.
Newsletter
Sign up to receive new blogs, case studies and resources – directly to your inbox.

Sign up
Discover more
Resources and guides
Discover our product application notes, design guides, news and case studies.
Case studies
Explore our collection of case studies, examples of our products in a range of applications.
Precision Microdrives
Whether you need a motor component, or a fully validated and tested complex mechanism – we’re here to help. Find out more about our company.