PCB Mounted Vibration Motors
Precision Microdrives offers a range of Printed Circuit Board mountable vibration motors that make mounting easy, reduce the design-in time, and allow for fully automated assembly. These motors are part of our Pico Vibe™ range and are ideal for haptics. Popular application areas include medical products, industrial tools, portable instruments, telecoms devices, and RFID / barcode scanners.
Our PCB motors are available in Ø4mm, Ø6mm cylinder types, and Ø10mm coin vibrator motor sizes. Vibration motors with flying leads are also available.
Thru-hole PCB vibration motors and SMT vibrator motors are perfect for retro-fitting vibration motors for vibration alerting or haptics as they often don’t require changes to the product’s enclosure and can avoid expensive tooling and redesign.
The securing pads of PCB mounted vibration motors can also be tied to ground which will make a small improvement to the EMC / EMI radiation produced by the motor.
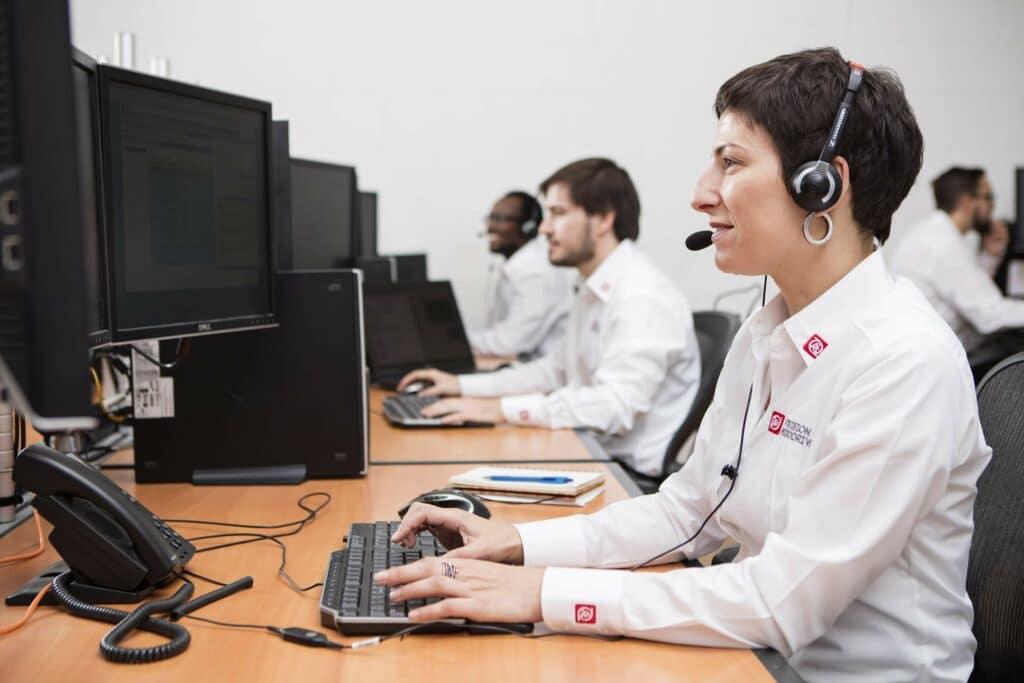
Get in touch
Speak to a member of our team.
PCB Vibration Motor Design & Mounting
Our PCB vibration motors are all Eccentric Rotating Mass (ERM) motors, and come in either cylindrical or coin motor form factors. We offer three different mounting designs, each with different advantages:
Through-hole vibration motors have protruding metal pins and are designed to be placed through holes on the PCB and soldered in place. This creates a strong mechanical anchor between the motor and board, particularly if the board is plated-through-hole (PTH). Through-hole PCB vibration motors have connectors to secure the vibrating motor, and separate connections for the drive signal – either pins or flying leads (with/without connector).
Surface mount vibrating motors are secured and connected via PCB pads and reflow soldering. Surface mount technology (SMT) is a popular way for mounting electronic components onto a PCB. Due to smaller foot-prints, they can save valuable PCB real-estate in complex applications. Also, components can be automatically assembled to boards with rapid pick and place machines.
Spring PCB vibrator motors have spring-loaded fingers on the motor which mat with pads on the PCB. This makes assembly easier for applications where it’s desired to have the motor mounted to the enclosure. Also, higher frequency harmonics are absorbed and reduced by rubber ‘boots’ that enclose these kinds of motors.
Application
The reduced size requirements of PCB vibrating motors mean that they are ideal for applications where space is at a premium, such as hand-held products. We have a guide to PCB vibration motor best practices, which contains design tips when using these kinds of motors. Examples of the kind of devices and applications these vibration motors have been used in are:
- Handheld medical equipment
- Industrial tools and portable instruments
- Telecommunications devices
- Mobile consumer products, such as cell phones or tablet PCs
- RFID / barcode scanners
- Automotive dashboards and controls
Useful resources
- Through-Hole Vibration Motors
- Surface Mount (SMD / SMT) Vibration Pager Motors
- Spring Mount Vibration Motors
- Best Practice Design for PCB Vibration Motors
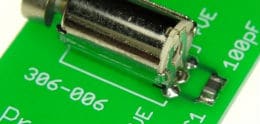
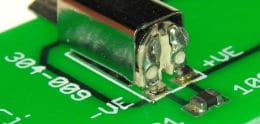
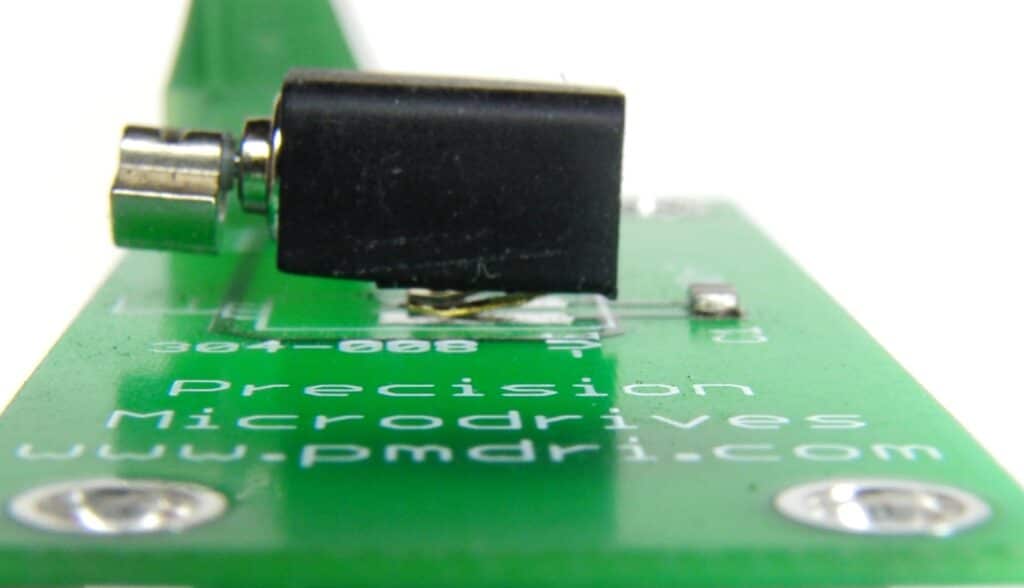
Discover More
Resources & Guides
Discover our product application notes, design guides, news and case studies.
Case Studies
Explore our collection of case studies, examples of our products in a range of applications.
Precision Microdrives
Whether you need a motor component, or a fully validated and tested complex mechanism – we’re here to help. Find out more about our company.