PID Controllers
With DC Gearmotors
There is always the challenge of ensuring that the chosen DC gearmotor delivers optimum performance according to its technical specifications. For a DC geared motor, the deviation from its optimum performance can happen for many reasons for example backlash. A PID (Proportional Integral Derivative) controller, when working in conjunction with a DC gear motor, implements a closed-loop system and due to its ability to increase accuracy, it has found wide acceptance in industrial, positioning and consumer applications.
Using a PID controller to improve the positioning performance of a DC gearmotor is a smart design choice. A PID controller provides a feedback mechanism for a gear motor’s parameter, for example, the positioning accuracy. A designer, working on a geared motor application, finds a lack of positioning accuracy due to backlash. Without any control system, the application gets reduced stability or becomes sluggish.
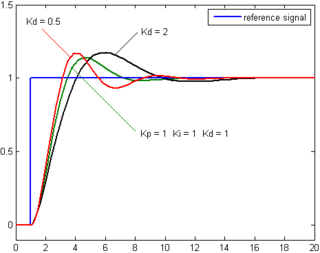
How Does A PID Controller Provide Positioning Accuracy?
A PID controller implements a closed-loop control system. Output measurement is calibrated in order to control the input. In a closed-loop control system, the following is defined:
Output = (Input − Output) × Gain
For the design requirements:
Use the PID controller to regulate the gain
Consider other factors in feedback to adjust the PID algorithms
The PID controller opens up the possibility of changing the dynamics with a larger number of options. This helps the designer in practical applications. PID controllers are viewed as three terms: a proportional term, an integral term and a derivative term. These are added together. As a designer, use a PID controller that has well-tuned parameters for your application.
Note: High acceleration or shock on the output gear shreds gear teeth. To prevent this, the designer can also use pre-gearhead (rear shaft) encoding feedback to improve positioning control. This control can be about 1 (one) revolution on the rear shift per degree of gearhead output. This ensures slow start and slow stop, avoiding high stress on one of the teeth
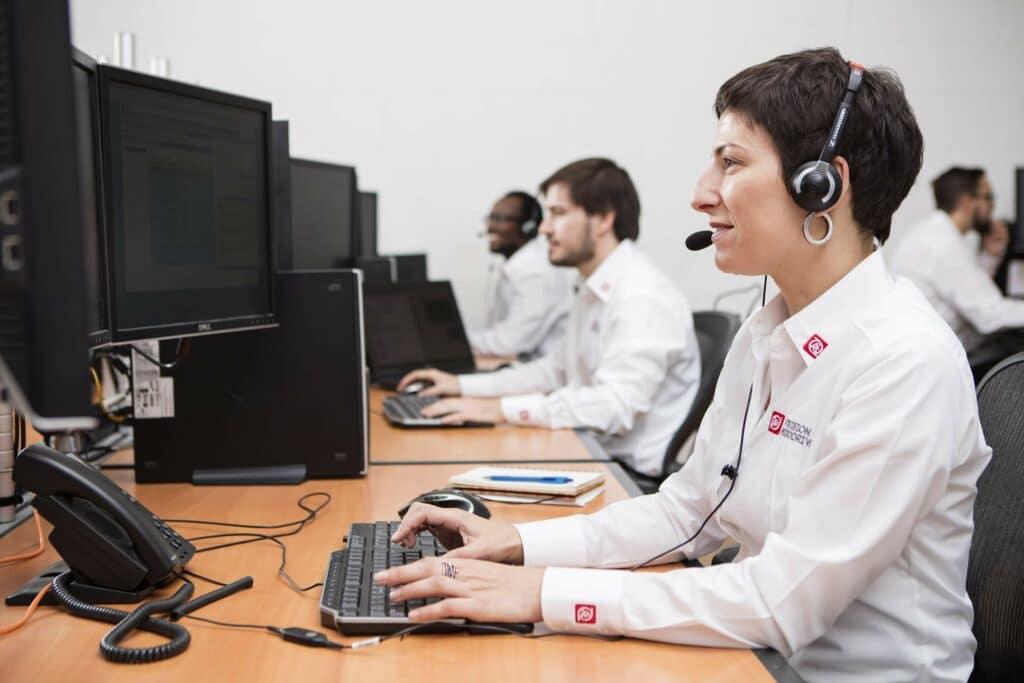
Get in touch
Speak to a member of our team.
Motor catalogue
Looking for our products?
Reliable, cost-effective miniature mechanisms and motors that meet your application demands.
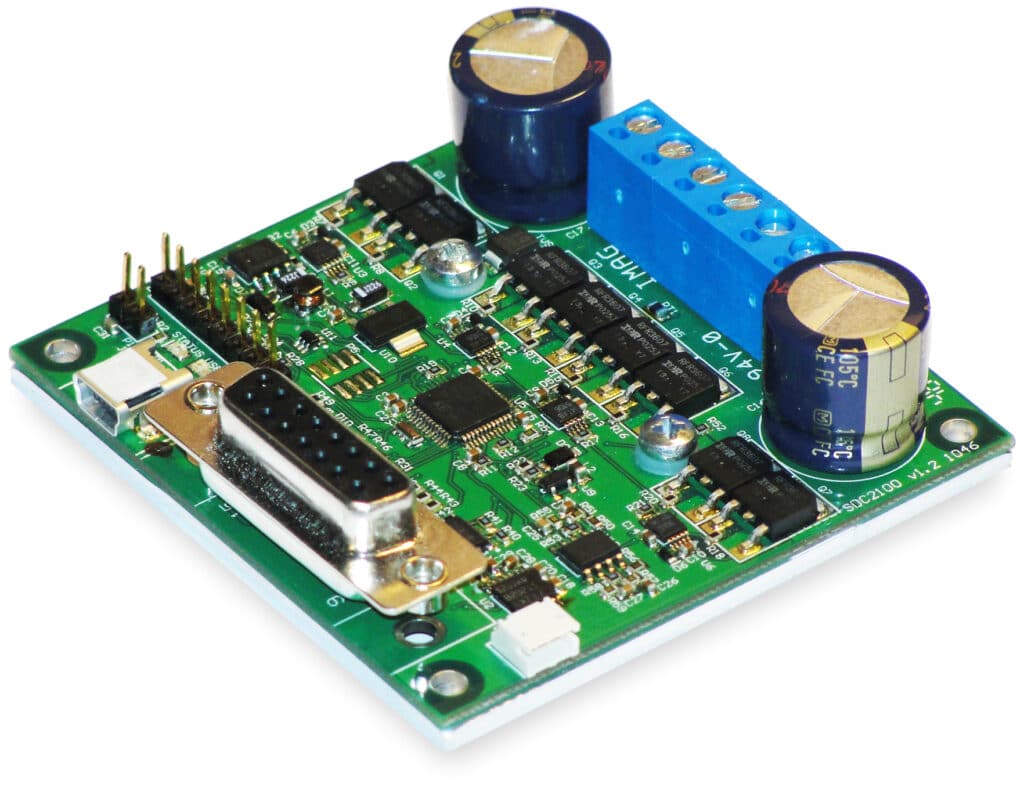
Discover more
Resources and guides
Discover our product application notes, design guides, news and case studies.
Case studies
Explore our collection of case studies, examples of our products in a range of applications.
Precision Microdrives
Whether you need a motor component, or a fully validated and tested complex mechanism – we’re here to help. Find out more about our company.