DC Motor and Gearmotor Lifetime and main sources of failure
Introduction
We’re commonly asked for information such as MTTF (Mean Time To Failure), FIT (Failure In Time) or the total number of “cycles” that our DC motors and gearmotors will reach. This is a difficult question to answer as there are a variety of parameters to be considered, most of which are application dependent. MTTF and FIT concepts are broadly explained in the application bulletin AB-19
With this blog post, we will discuss lifetime units, common failure modes, difficulties with lifetime approximation and ultimately, methods of preserving lifetime with your motors.
We’ve also previously looked at brushless DC motors and how a greater lifetime can be achieved with these parts. For vibration motors, the lifetime can be calculated in an easier way by fixing the supply voltage. See MTTF test for some of our more demanded vibration motors has been recently published.
Failure Modes
In order to discuss the lifetime of our DC motors and gearmotors, we feel it is first necessary to briefly mention some of the most common failure modes, their common causes and suggestions on how to avoid them. As might be expected the addition of the gearhead in a gearmotor will add another possible source of failure.
Damaged Gears in Gearmotors
This is usually provoked by one of the following causes:
- Gearmotor stalling due to overloading
- Shock loading from hard stops
- General wear
- Debris in the gear chain
- Prolonged periods of high loads/speeds
In order to help prevent these failures, we recommend adding limit switches or current sensors that could cut the power before a hard stop/stall is reached. Another method to alleviate this could be using a belt drive to avoid shocks in the gears.
Take care with the housing method to prevent debris or dirt ingress.
Match the specification and duty cycle of the gearmotor carefully to the application.
Brush/Commutator Wear
This is another common source of failure for all DC motors, including vibration motors. In the particular case of DC motors and gearmotors, this is exacerbated due to the potential exposure to high loads.
The common causes are:
- General wear (inevitable under any circumstances)
- Increased wear due to high speed/over-driving
- Excessive arcing due to overdriving
In this case, if a motor fails after a few hours of operation, for the above reasons, we could assume that the motor is either overdriven or overloaded. The motor needs to be used within its rated conditions. This type of failure could, therefore, indicate that the motor might not be the best solution for the application.
Brush/Commutator Contamination
Contamination from various sources can potentially enter inside of the motors and affect the electrical contact between the brushes and commutator.
The main common causes we see are:
- Over-moulding compound ingress
- Blooming of super glues
- Operation in dirty or dusty atmospheres
These issues are easily targeted by avoiding adhesives that tend to bloom (eg. Cyanoacrylate based super glues), using viscous mounting adhesive or potting compounds, or providing protection from the environment.
Bearing Wear
This is actually more common than we would think. Gearmotors are not designed to withstand axial or radial loads.
Common sources of failure are:
- Excessive radial or axial loading during operation/assembly
- Insufficient axial play
This can be avoided by reducing any radial or axial loading on the shaft in the assembly or by adding a thrust bearing to help relieve the axial loads.
Difficulties with Lifetime Approximation for Gearmotors or DC motors
We’re in the process of completing extensive lifetime testing (application-notes/ab-019-lifetime-of-dc-vibration-motors-mttf-fit) across our range of vibration motors. These values are published on the datasheets in the form of MTTF and FIT. In short, this data can be recorded and presented accurately because our vibration motors are commonly operated at their rated voltages (so the rotational speed/brush wear is largely consistent between applications) with the same eccentric mass (so the torque loading and bearing load is largely fixed).
Unfortunately, testing the lifetime of our DC motors/gearmotors is not quite so simple and for this reason, it is unlikely that you will find this specification on the datasheets. Different driving voltages combined with dynamic loads are particular characteristics for each application. However, this is a service that we can and we have provided to our customers. Lifetime tests using elements like magnetic brakes to simulate loads and replicate the customer environment is something that we can do for you.
Conclusion
When approaching a project that will require the use of a DC gearmotor, there are several variables that need to be considered in order to not compromise the lifetime of the actuator. At Precision Microdrives we have extensive experience working with this type of motor and we know how to prevent the main sources of failure. We encourage you to contact us as soon as possible to avoid the inherent problems that appear in projects where a gearmotor is needed.
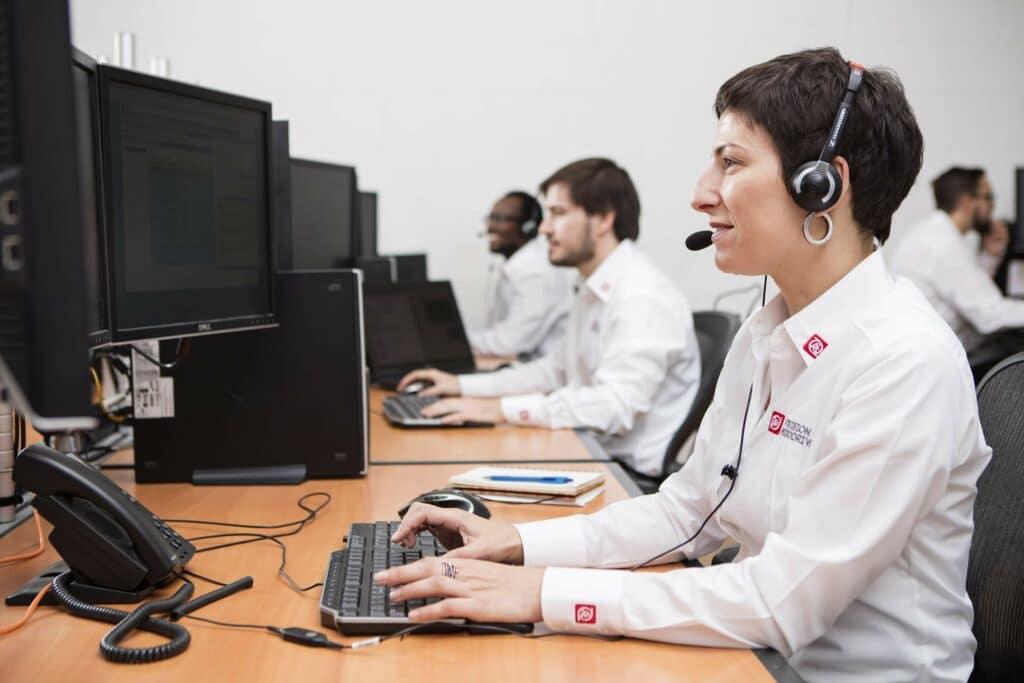
Get in touch
Speak to a member of our team.
Motor catalogue
Looking for our products?
Reliable, cost-effective miniature mechanisms and motors that meet your application demands.
Newsletter
Sign up to receive new blogs, case studies and resources – directly to your inbox.

Sign up
Discover more
Resources and guides
Discover our product application notes, design guides, news and case studies.
Case studies
Explore our collection of case studies, examples of our products in a range of applications.
Precision Microdrives
Whether you need a motor component, or a fully validated and tested complex mechanism – we’re here to help. Find out more about our company.