Choosing an NTC for a current limited battery powered motor applications
Introduction
On our last blog post, we talked about motor surge protection in battery-powered systems. One of the suggested methods was adding a Negative Temperature Coefficient (NTC) thermistor, but we didn’t explain how to choose an NTC for a project that includes miniature motors.
The first two main problems that we should take into account when designing a battery-powered application are the short circuit and the over-discharge.
Fortunately, many batteries have an internal electronic protection circuit which prevents the battery from short circuit and under-voltage. A short circuit can lead to a battery fire, and discharging under minimal operating (mostly about 2,75V) voltage can permanently damage the battery or, at the very least, reduces its lifetime.
Once we have chosen a battery appropriate for the motor power demands, it is time to think about protecting the battery from over-current.
The starting current of DC motors could be a few times greater than steady-state current. When we first power the motor, it tends to draw a current nearly equal to the stall current. This current is reduced as the motor gains speed, due to the back-EMF generated by the motor.
Current spikes may also occur when we suddenly accelerate the motor by increasing the voltage. This is a typical application in devices, for example, performing haptic feedback.
As we have mentioned these current spikes can result in permanent damage to the battery.
Case study
We will consider the use of the enclosed vibration motor 325-100 together with a battery. This motor has a rated voltage of 3V and a rated current consumption of 190mA. However, the maximum start current of the motor is 2,500mA.
The battery characteristics for this example can be found in the table below:
Capacity | 450mAh @ 90mA (0.2C) |
Max discharge current | 450mA (1C) |
Power off voltage | 2.75V |
The start current of the motor is 5 times the rated max discharge current of the battery. However, this does not mean that the battery cannot be used with this motor. We will just have to incorporate a protection method. The battery can deliver the steady-state current requested by the motor and it’s only the current spikes in the start-up what we should have to prevent.
In this case, we are going to include an NTC thermistor to our circuit to prevent the overcurrent problem.
We would need the NTC thermistor to cut the initial current spike to a maximum of 450mA. Having a terminal resistance on this motor equal to 1.3Ω, we would have:
$$V = IR_{T} => R_{T}= \frac{V}{I}$$
At this point, when including the NTC in our system, we can assume that the total resistance will be obtained adding the terminal resistance of the motor RM and the NTC resistance RNTC
$$R_{M}+R_{NTC}=\frac{V}{I} => R_{NTC} = \frac{V}{I} – R_{M} = \frac{3V}{0.45A} – 1.3Ω = 5.36Ω$$
Choosing an NTC thermistor from this website, we would choose a safe value of 10Ω as the initial resistance. Thanks to this, we would protect the battery from overcurrent in the start-up of the motor.
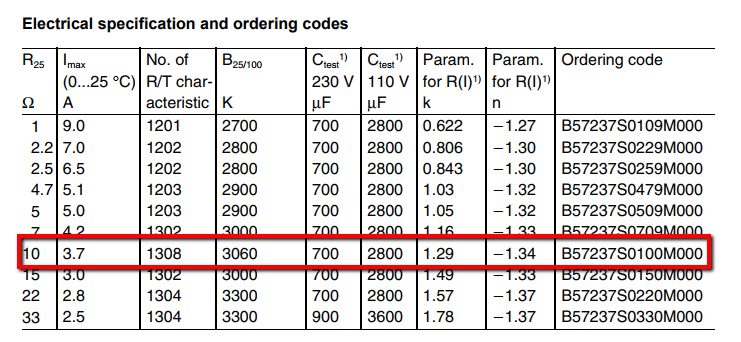
Below there is a proposed circuit diagram implement an NTC.
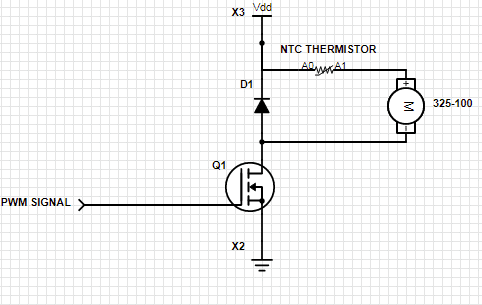
One last point to consider is the thermal inertia of thermistors. During the start-up, the NTC will warm up and we will need to allow a certain amount of time for this heat to dissipate, so the resistance decreases to the initial value. Therefore, this solution will be only valid in applications where the cycle allows enough time between on and off times.
We can help!
We have supported several customers on this topic as part of our design-for-application and design-for-manufacture services. We have also discovered problems on customer’s behalf and alerted them, as part of our engineering due diligence when reviewing motors for their application.
If you’re thinking of using some miniature motors of any kind, we always recommend reaching out to us for a friendly chat. Our application design engineers see a lot of applications pass through their desks, and are familiar with a lot of the pitfalls that may not otherwise be so obvious.
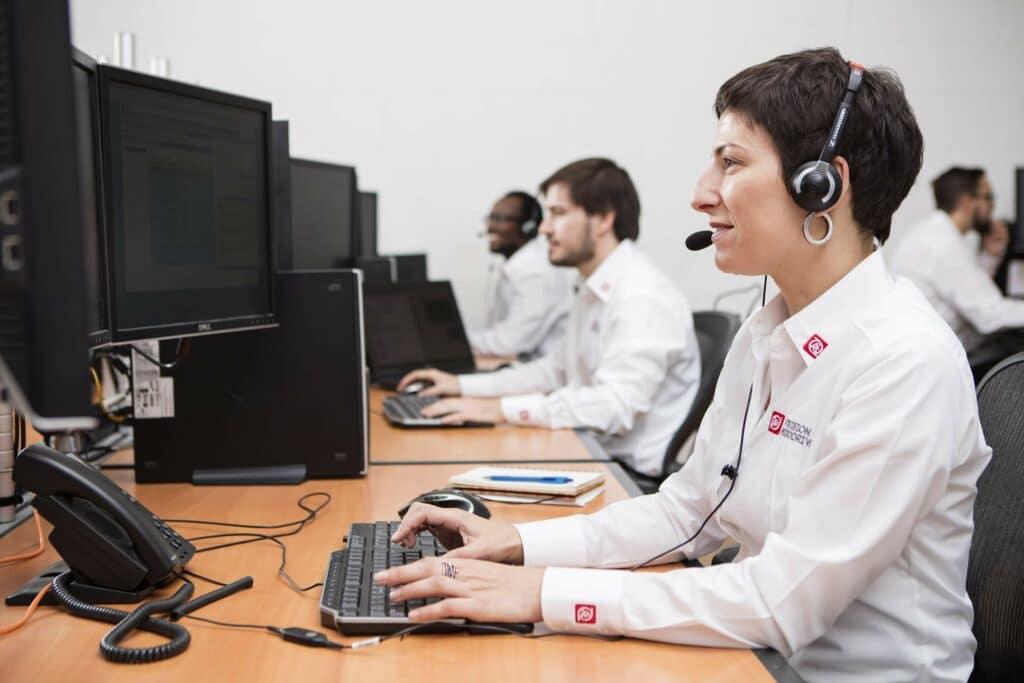
Get in touch
Speak to a member of our team.
Motor catalogue
Looking for our products?
Reliable, cost-effective miniature mechanisms and motors that meet your application demands.
Newsletter
Sign up to receive new blogs, case studies and resources – directly to your inbox.

Sign up
Discover more
Resources and guides
Discover our product application notes, design guides, news and case studies.
Case studies
Explore our collection of case studies, examples of our products in a range of applications.
Precision Microdrives
Whether you need a motor component, or a fully validated and tested complex mechanism – we’re here to help. Find out more about our company.