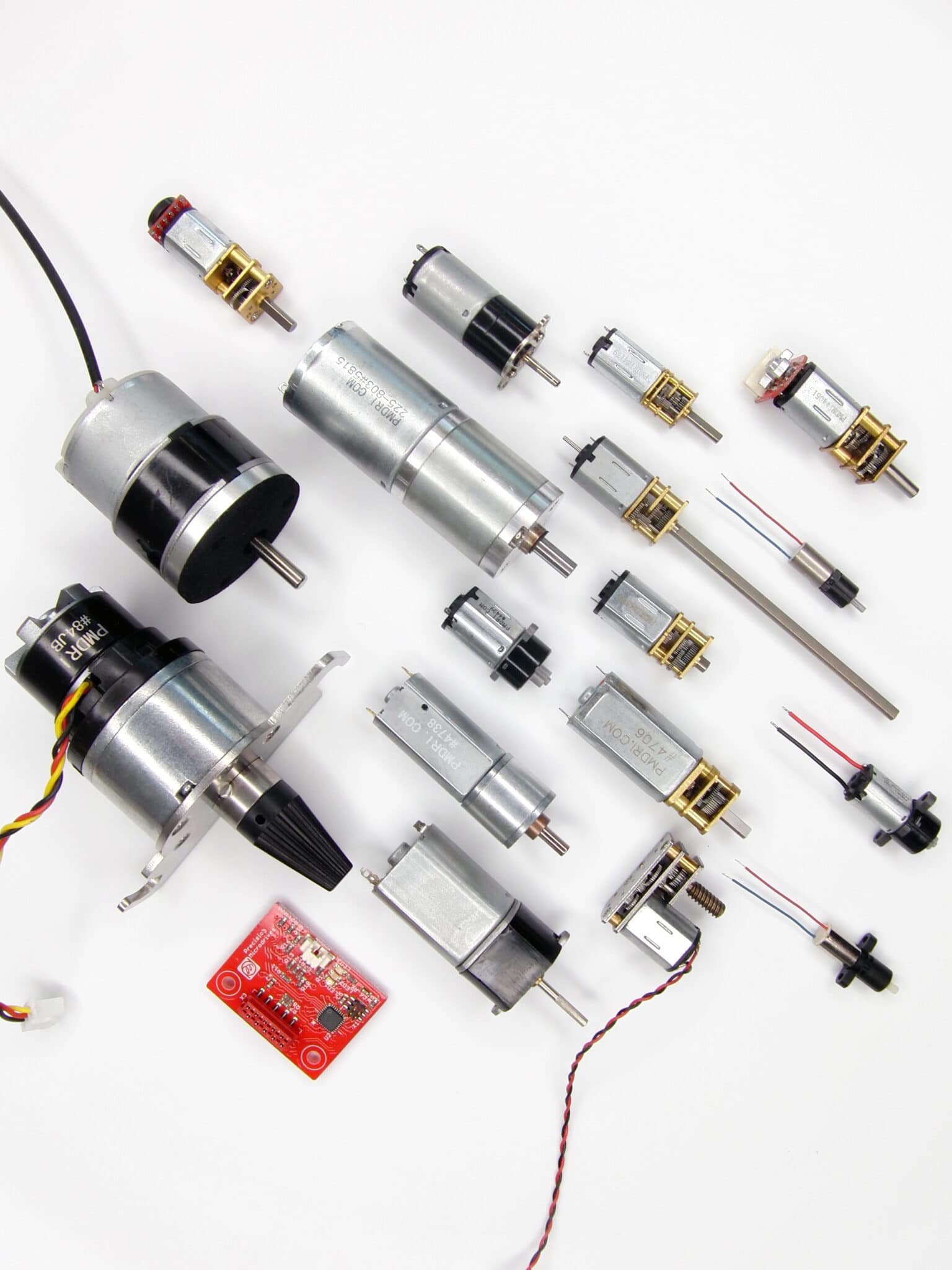
Precision Microdrives DC Gear Motors
Wide range of customised DC gear motors with off-the-shelf sampling
We design and manufacture a wide range of high-quality, and cost-effective, sub-Ø60 mm DC motors in a range of technologies.
Three main DC Gear motor technologies
Our three main DC gear motor solutions use iron core, coreless and brushless technologies with two gearboxes, spur and planetary, in a variety of materials.
78 stocked motor form factors
We want to help get you developing quickly. So we have many off-the-shelf form factors with a variety of winding configurations available for immediate sample or purchase.
Customised for your application
Your application is unique so we expect you to need some custom features or specific performance. Work with our application engineers to design the perfect solution.
Speak to an engineer
DESIGN SOLUTIONS
Gear motor technologies
We design and manufacture gear motors both as individual components, and as part of larger assemblies. In this process, we use four different categories of technology depending on the needs of the end application:
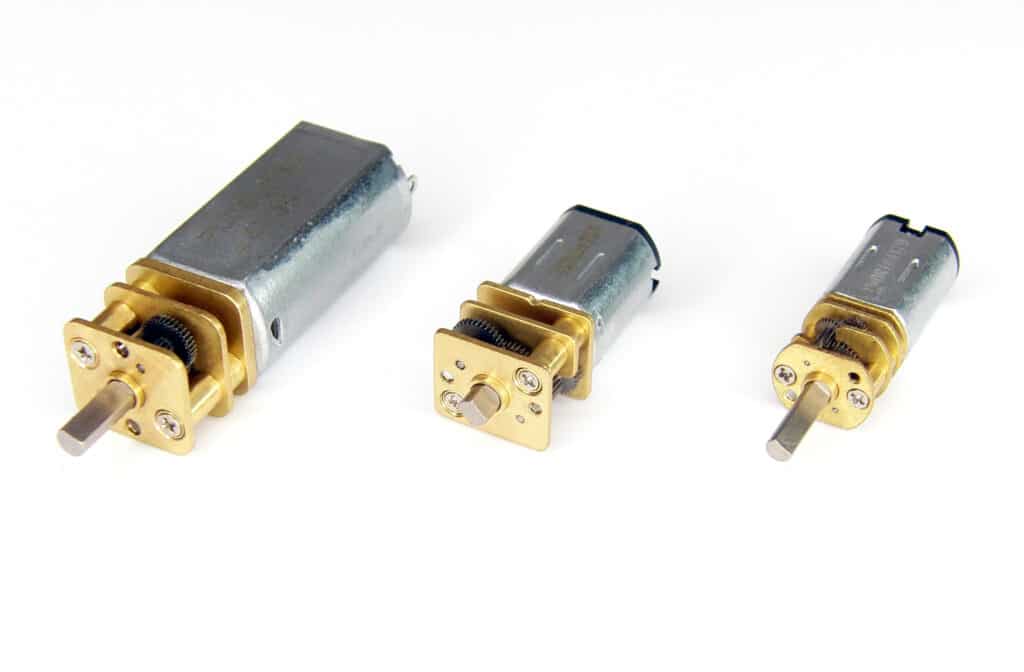
Spur geared DC motors
Gearboxes are added to motors to reduce the rotational speed and to amplify the torque.
All of our spur gear boxes are constructed using steel gears to maximise strength and lifetime and can be coupled to iron core, coreless and brushless motors.
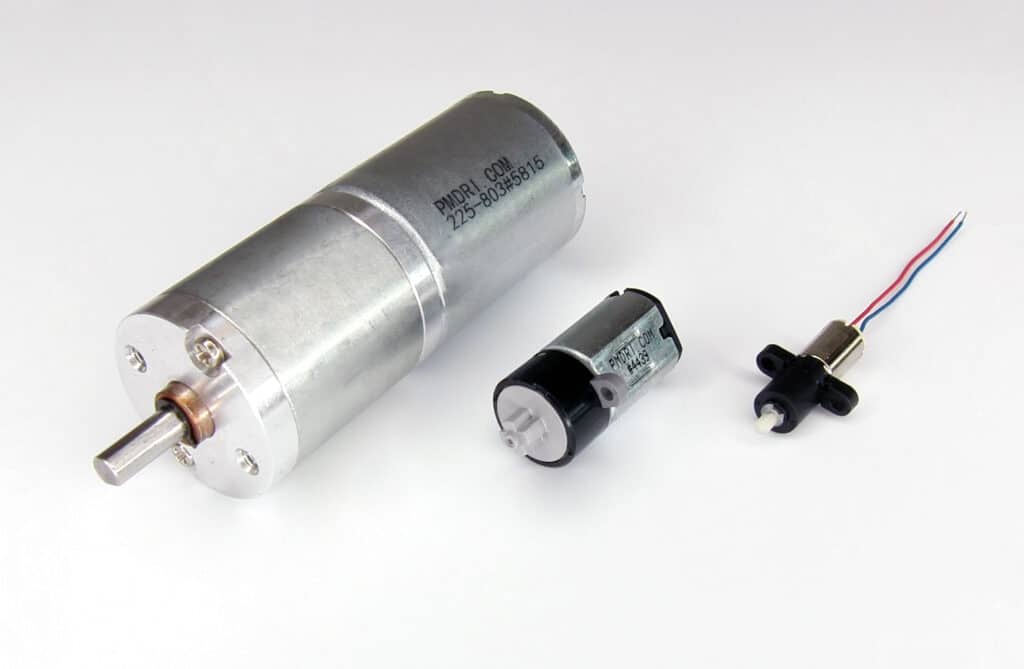
Planetary geared DC motors
For sub 10mm diameter geared motors, metal gears become very expensive, requiring the adoption of gears made from injection moulded engineering plastics such as POM or LCP.
To reduce gear tooth load in these designs, a planetary gearbox arrangement is preferred because there are more mesh points for each gear.
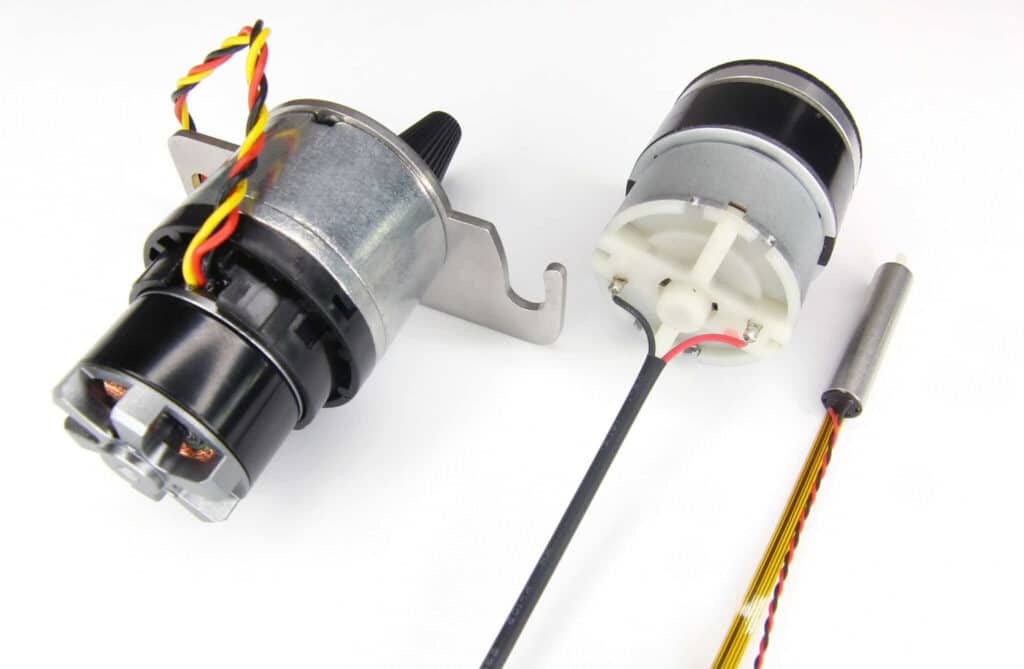
Iron core, coreless and brushless construction
We can couple any of our gearbox designs to any type of motor technology. There are three motor constructions that we commonly use:
Iron core brushed
Coreless brushed
Brushless motor designs
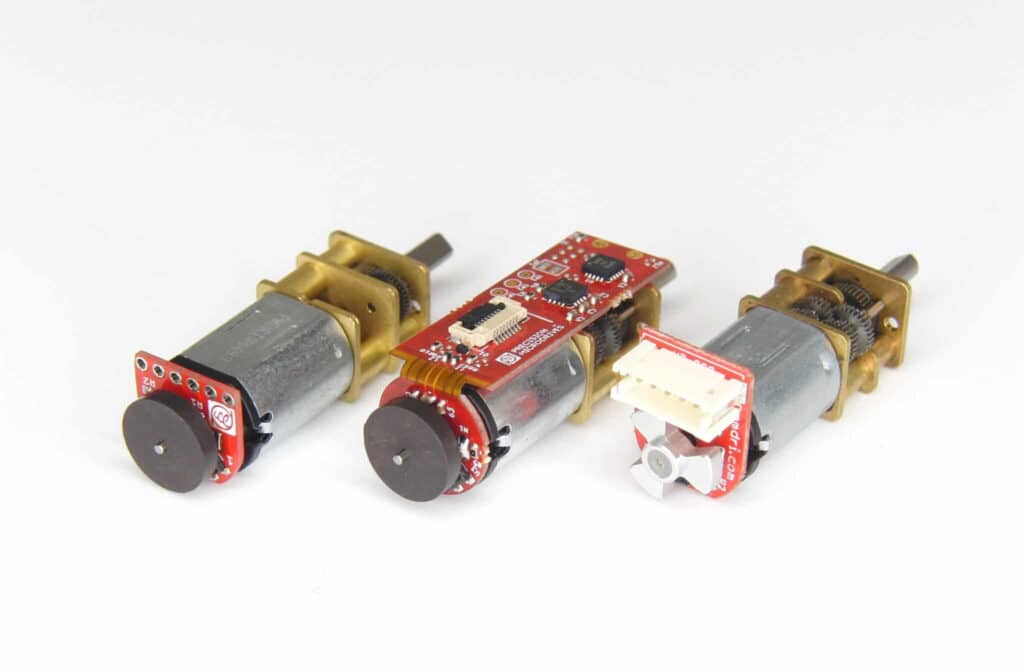
Encoders and integrated motion controllers
For more precise control we build onto the motor an encoder (an advanced counter) and where necessary an integrated motion controller.
This can receive commands from the host application such as to move a syringe plunger back / forward 10mm.
Typical gear motor form factors
Irrespective of the gearmotor technology adopted, there are some common form factors and design influences that are commonly used in applications across all industries. Below are some examples that can be used to describe your preferred solution.
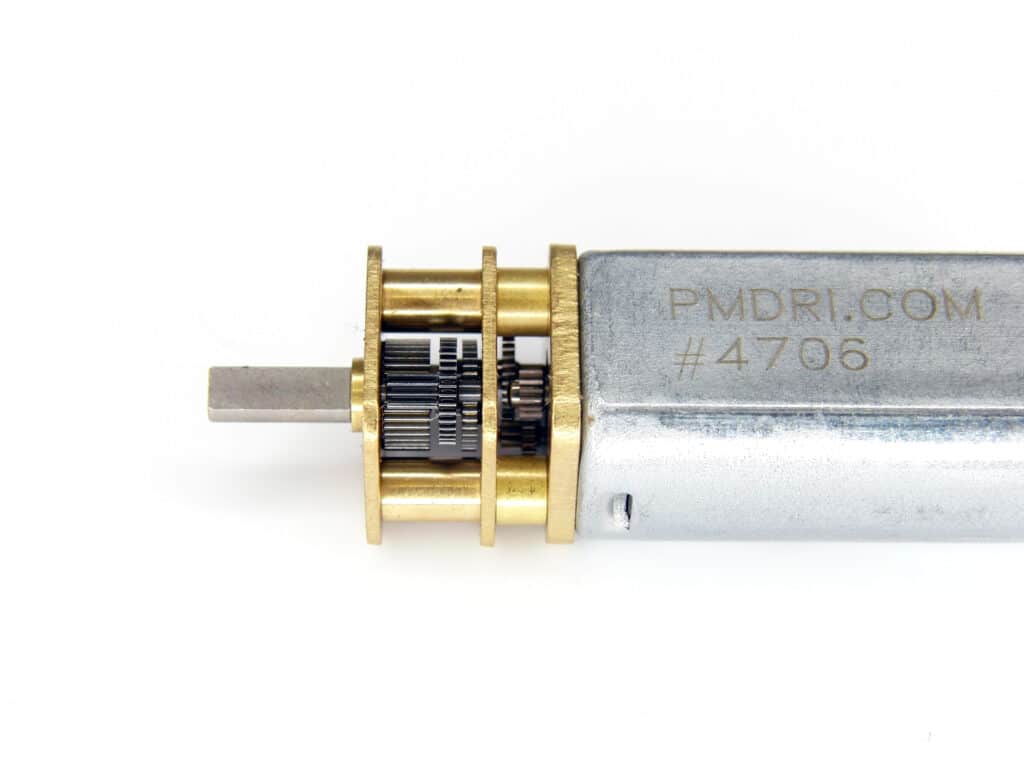
Open frame
About 1/3 of our designs use an open construction, primarily where the gearbox frame is square or rectangular.
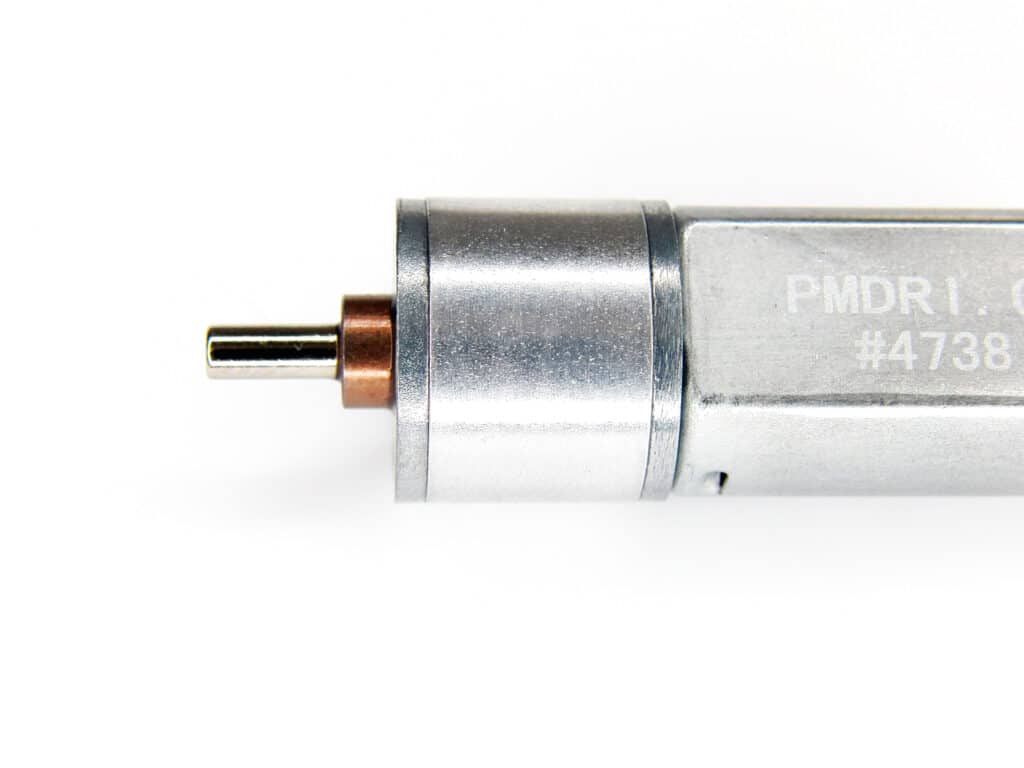
Closed frame
Other gearbox designs are circular, making it more practical to cover the gears. The main benefit is to prevent debris from entering.
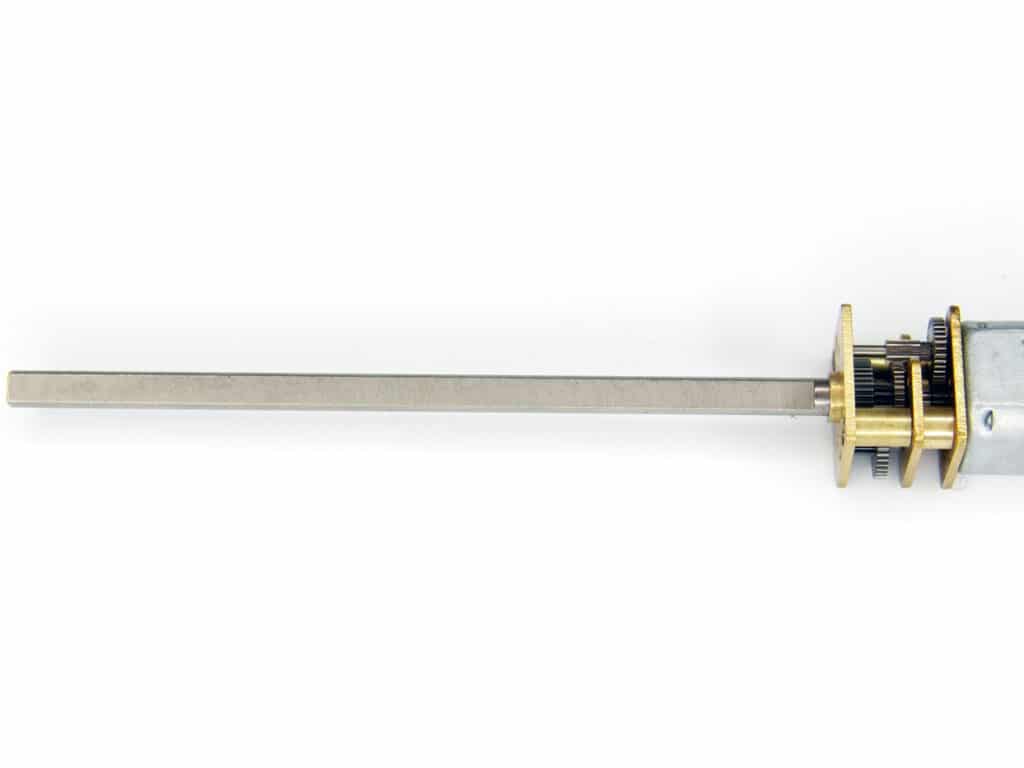
Shaft modifications
Some applications need specific shafts. Longer, shorter, d-cuts, keyway cuts, location holes and threaded shafts are all possible.
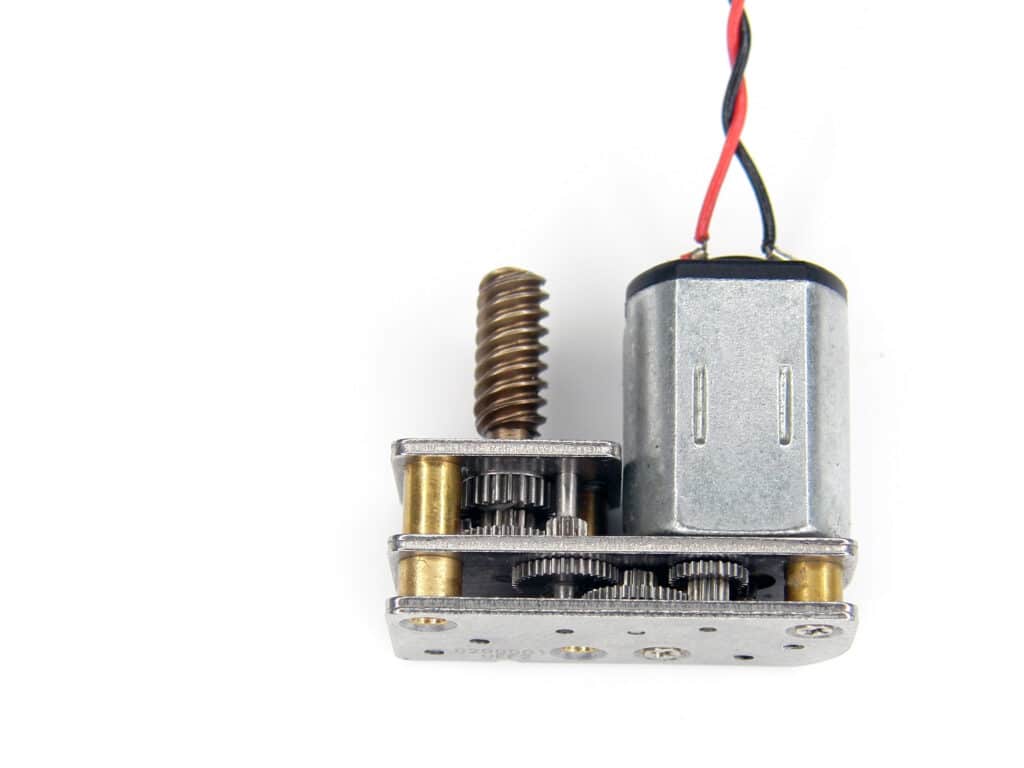
Offset and foldback gearboxes
If space is tight in the length dimension, consider a fold-back gearbox, or a non-concentric offset gearbox shaft.
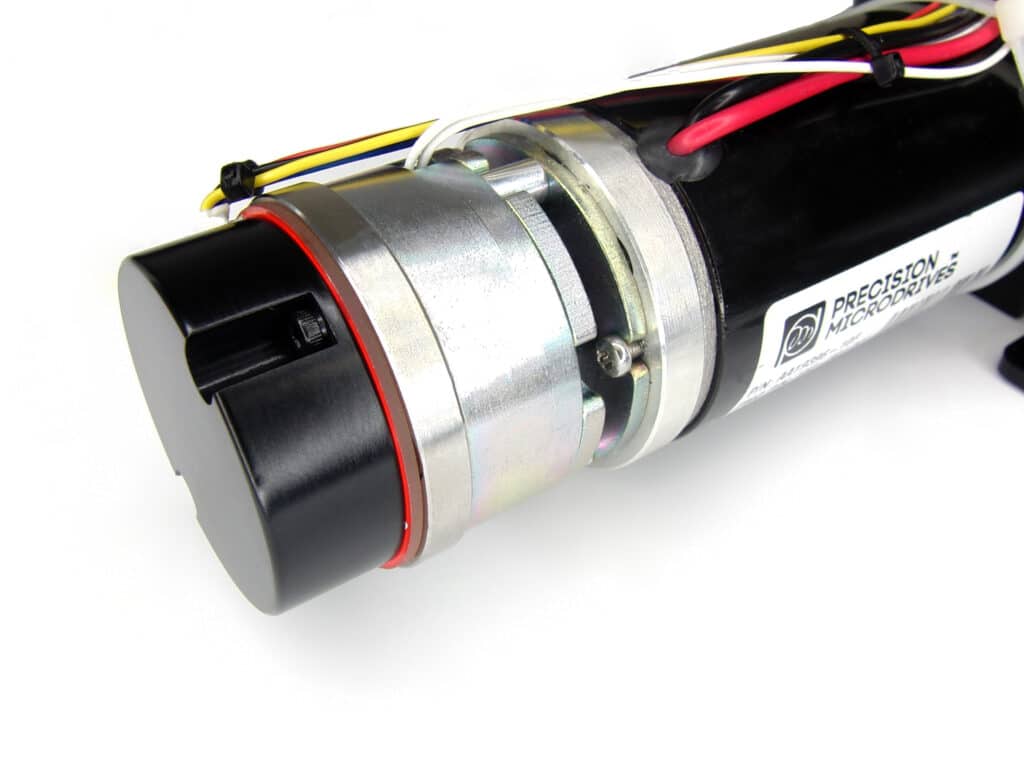
Clutches and mechanical brakes
Clutches can disengage the gearbox from the application. Mechanical brakes can lock the gearbox shaft in a ‘park’ position.
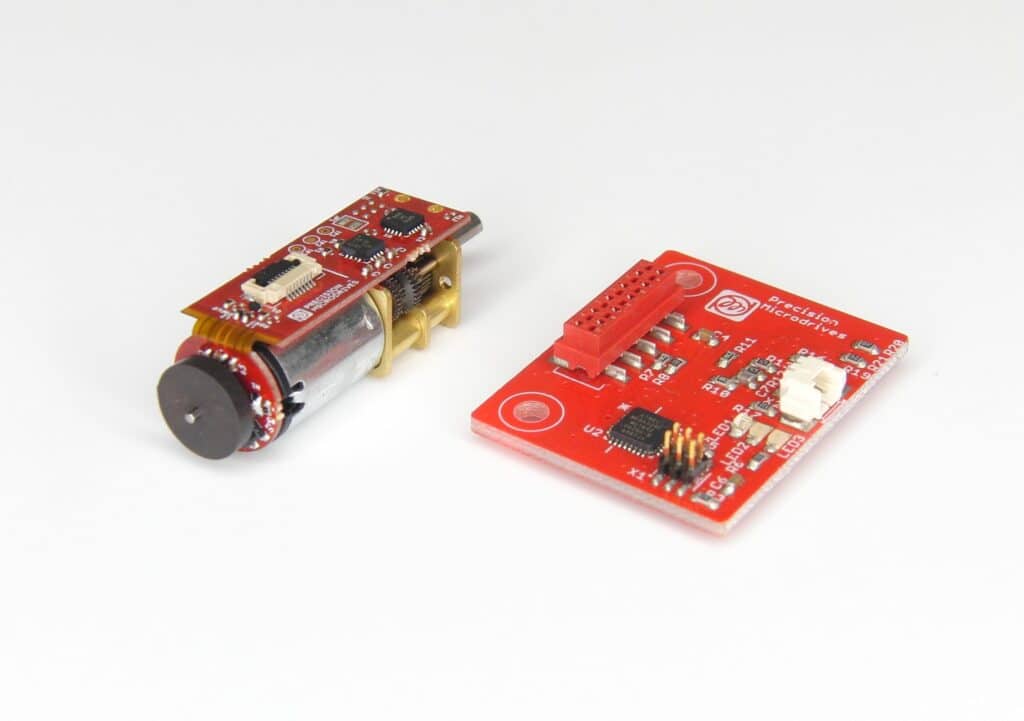
Advanced motion controllers
Precision movement is sometimes necessary, but motion controllers can also significantly extend gear motor service life.
Specialised engineering services and capabilities
Find out more about our capabilities
YOUR DC GEAR MOTOR ENGINEERING PARTNER
Why Precision Microdrives?
Trusted motors and mechanisms
Getting the core of your application correct, first time
Motors and mechanisms are likely one of the most expensive lines on your BOM and also the least likely to be noticed by your customers. Until they fail…
So, choose an engineering partner that has extensive domain expertise in mitigating the technical risks of these complex products.
Rely on a manufacturing partner with a presence on the ground, robust quality control processes, and a familiar approach to maximising your value-add.
Priced to deliver the best value
We engineer our products to be optimised for your application and delivered at a best value cost.
We don’t engineer our solutions to the highest possible standards, or the lowest possible costs.
That’s not the only way we help your profitability either.
Add a very technically experienced, cost effective addition to your development team. We will free up your internal resource to focus on more valuable R&D work, which will expedite your development cycles.
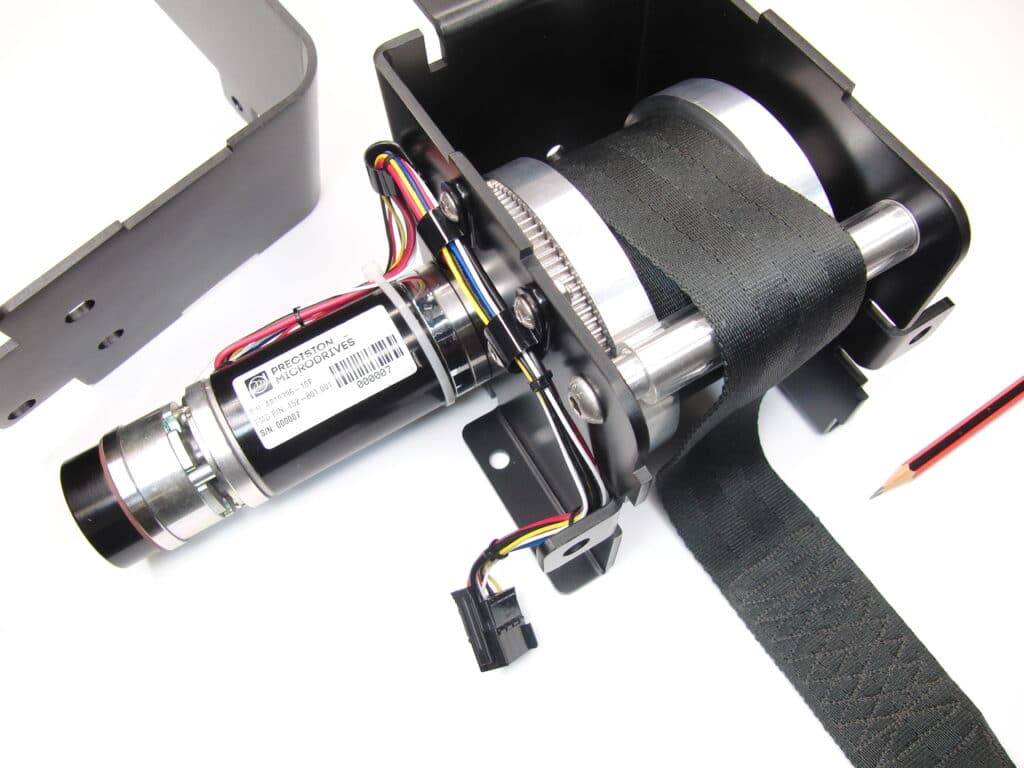
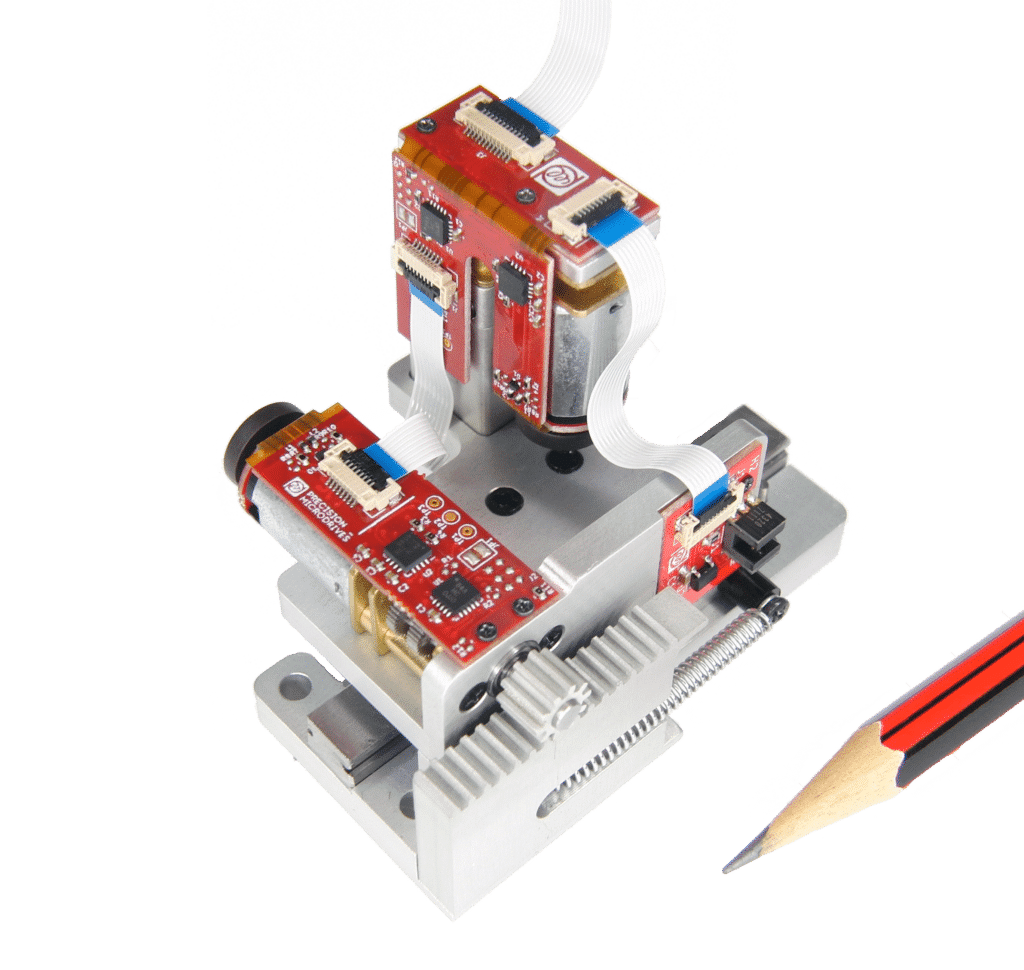
Working with Precision Microdrives
Manufacturable design
- We design solutions that are manufacturable and reliable.
- Tested and validated for longevity, performance and environment.
Technical expertise
- Absolute domain experts in motors and mechanisms.
- If we can help by sharing our expertise and experience, we will.
Robust quality controls
- Quality teams in Asia to control upstream component suppliers.
- QC methods developed specifically for motors and sub-components.
Precision manufacturing
- Uniquely (for Asia) co-locating design engineers and final assembly lines in Hong Kong.
- Specialisation in complex electromechanical assemblies.
- Motor / mechanism custom end-of-line testing.
Partnership
- We free up your resources and take away the pain of motor mechanisms for higher value R&D.
- Working as an extension of your business, at every stage.
- Pre and post sales support, in your time zone and language.
Managing your risk
- Unparalleled motor mechanism experience, enables us to predict problems and provide solutions.
- Competent skills and processes to mitigate risks from design through to mass production.
- A culture to get things right!
Key markets and applications
We provide motor and mechanism solutions to all sorts of industries, including:
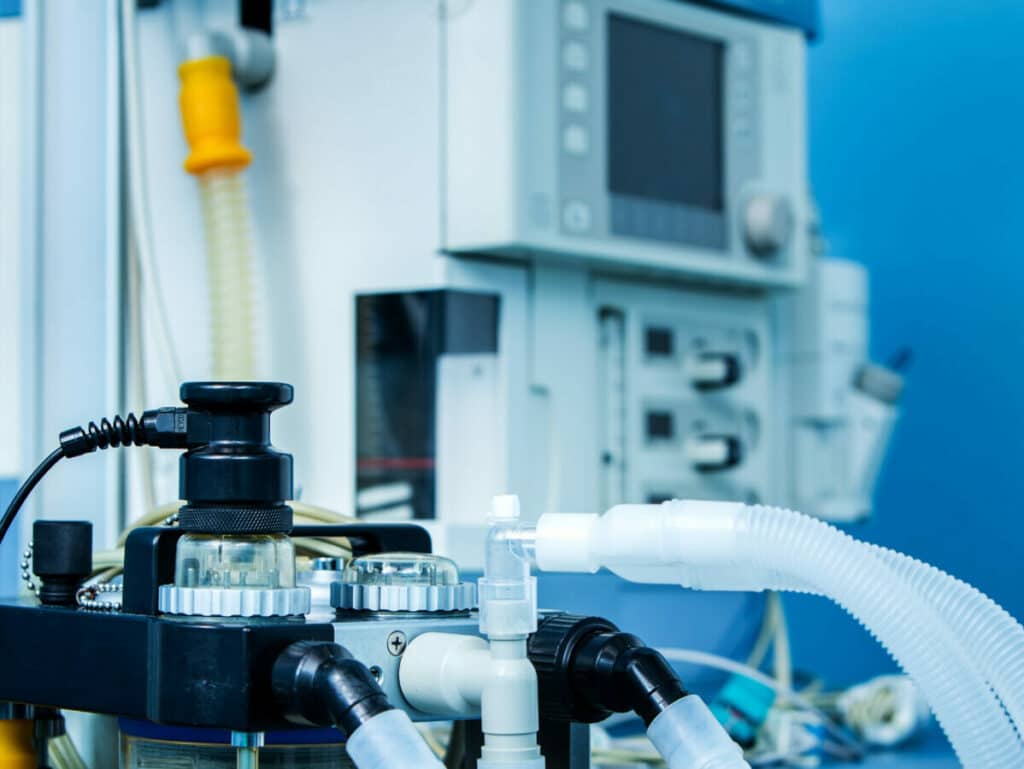
Medical
- Point of care machines
- Lab analysis and diagnostics equipment
- Drug dispensers
- Automated test platforms
- Pumps
- Surgically implanted devices
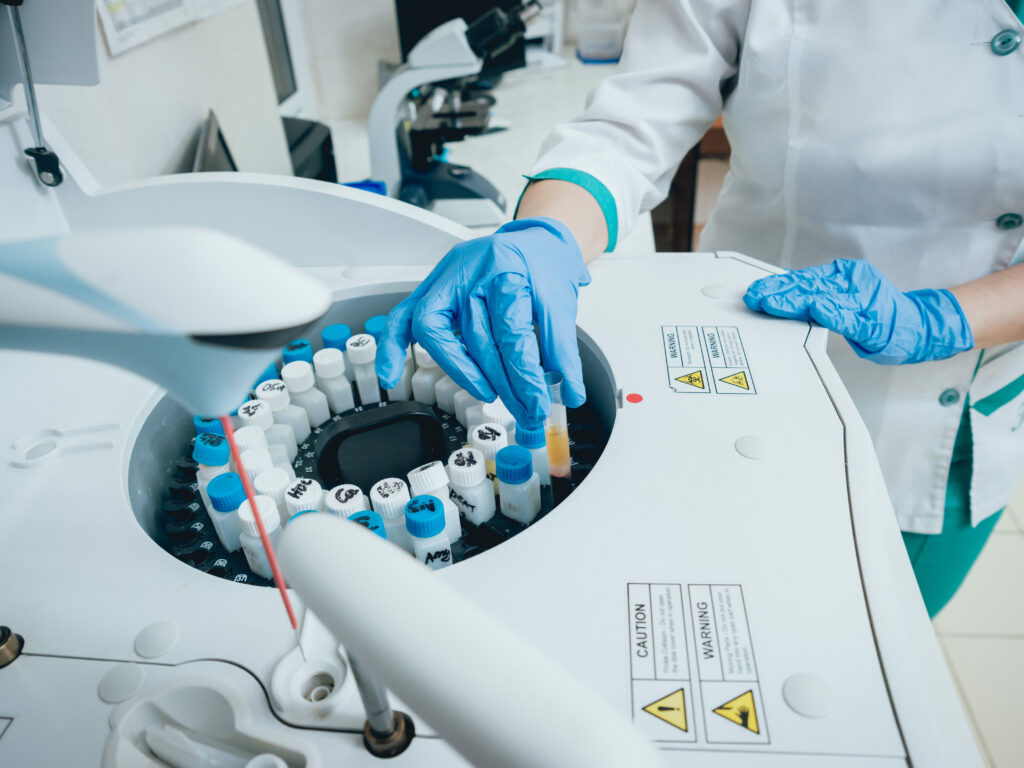
Instruments
- Monitoring and measuring devices
- Lab sample preparation equipment
- Diagnostics equipment
- Sensors and gauge testing
- Bench-top dispensary equipment
- Electronics test equipment
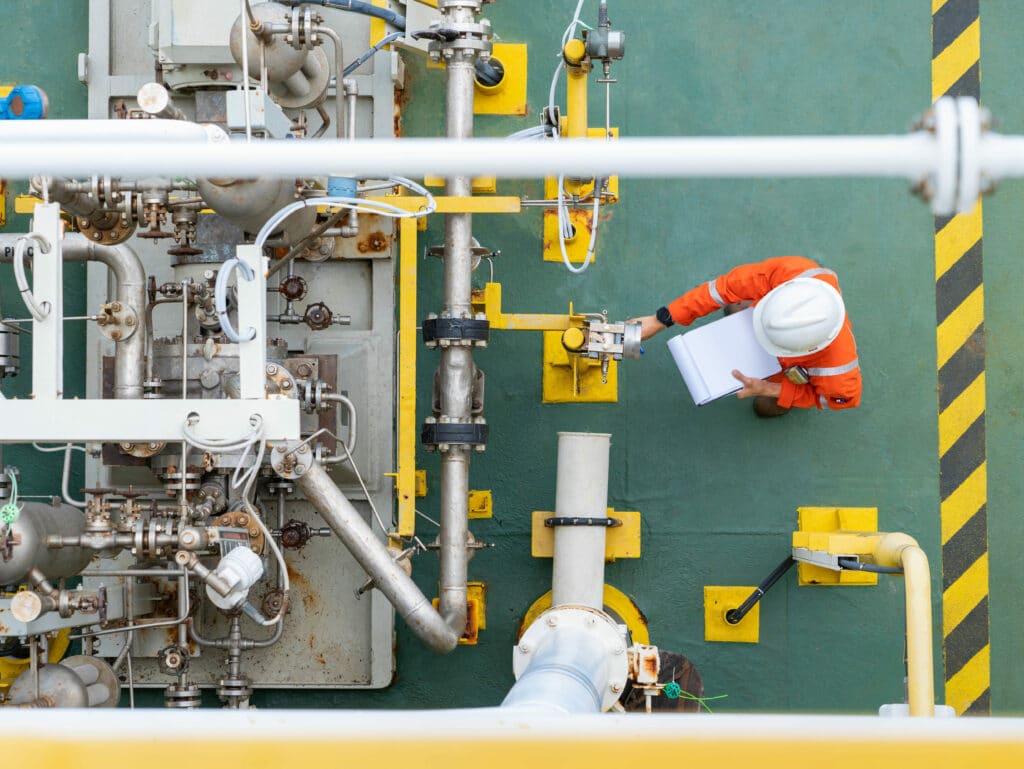
Industrial
- Emergency services equipment
- Analysis and monitoring devices
- Transport and logistics
- Controllers
- Ticket kiosks and ATM’s
- Robotics and artificial limbs
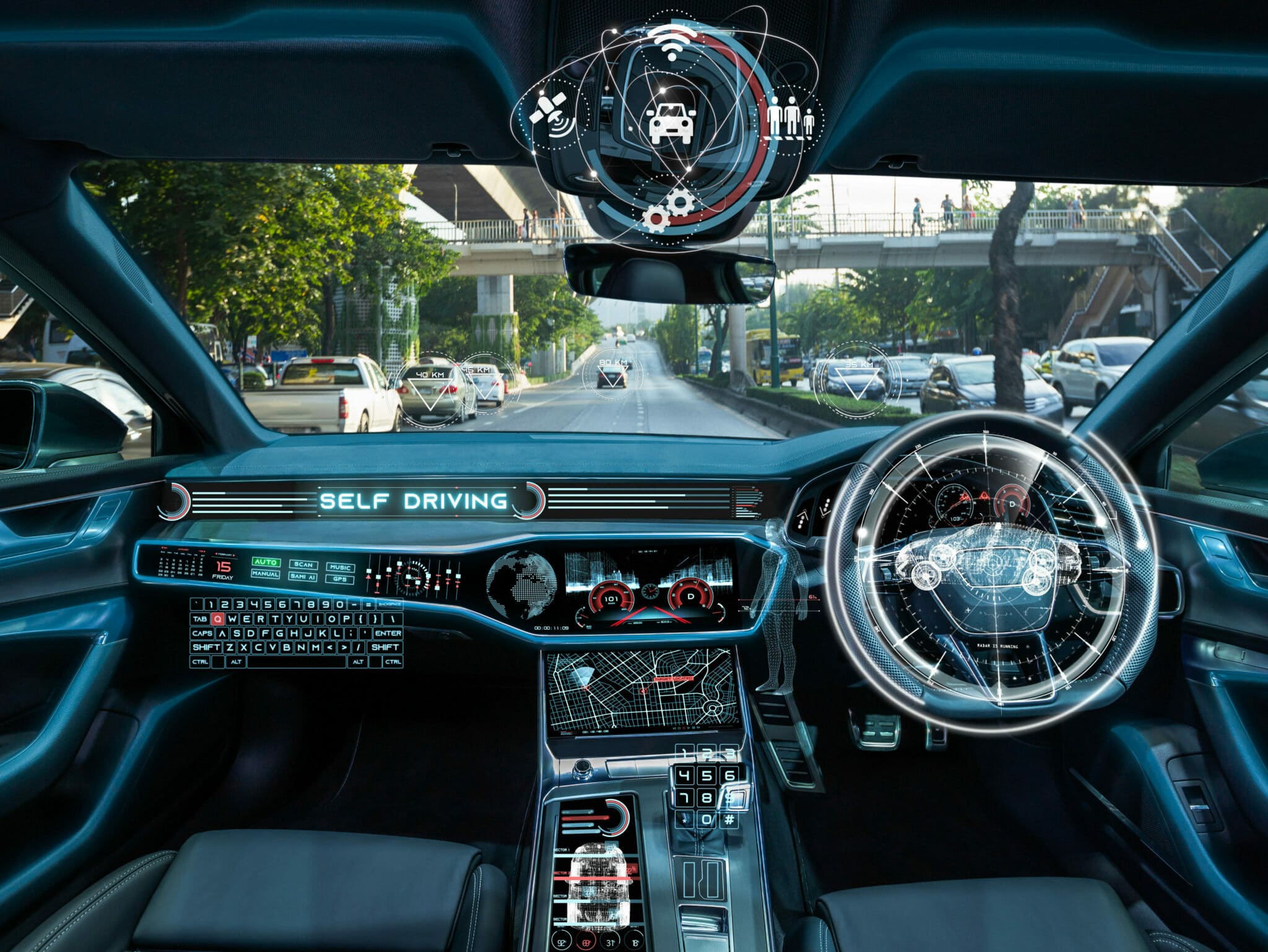
Consumer
- Touchscreens and smart devices
- Video games and controllers
- Smart homes
- Automotive dashboards
- E-bikes
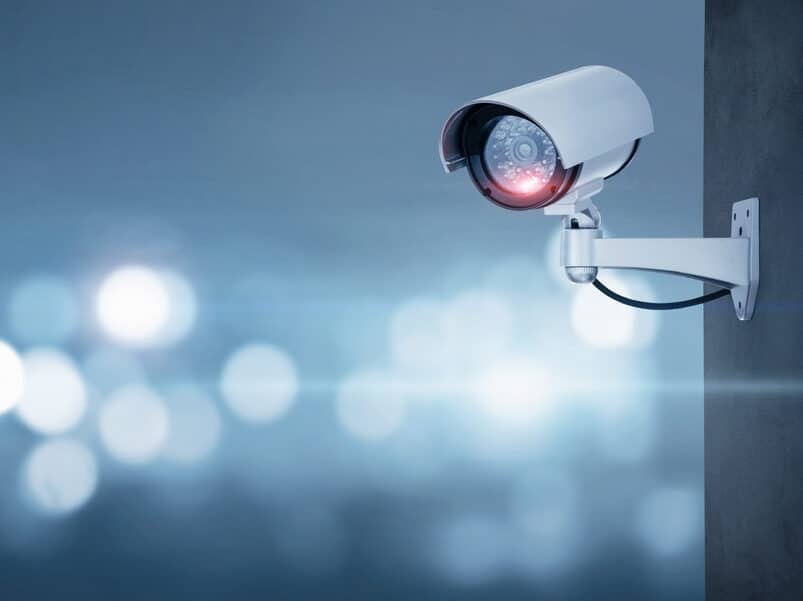
Security
- Sensors and alarms
- Handheld scanners
- Surveillance cameras and monitors
- Locks, security systems and safes
- Passport readers and ID scanners
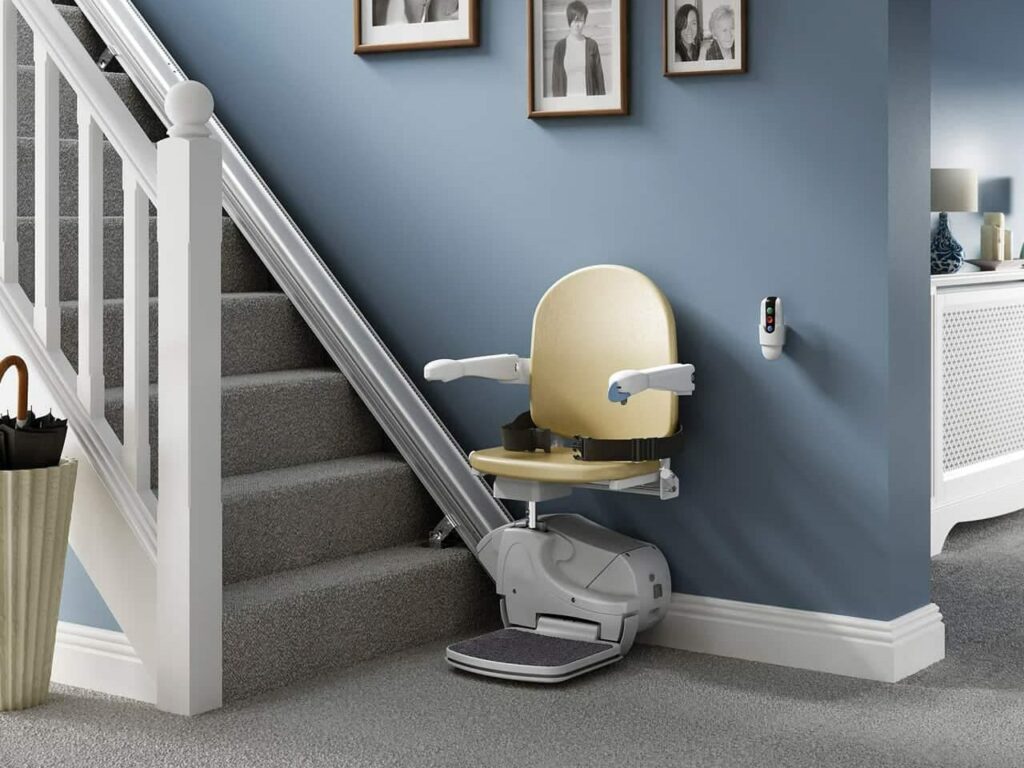
Healthcare
- At home health monitoring
- Rehabilitation accessories
- Fitness trackers and smart watches
- Oral drug dispensaries and vapes
- Stairlift and mobility solutions
Case studies
Our DC Gearmotors are used throughout many applications and industries. Here are some of our recent gearmotor projects
-
Smart home
Precision motors for solar-powered, smart-enabled motorised control access system for operating home devices like locks, windows and blinds.
View Case Study
-
Medical laboratory DNA testing equipment
DNA Benchtop medical diagnosis machine redesign to support new commercialisation model.
View Case Study
-
Medical inhaled medication delivery device
Intelligent medical inhaler device, which was FDA Class III approved, required a gear motor mechanism to provide precise dosage for all users.
View Case Study
-
Mobility stairlift
Mobility solution, an indoor stairlift, required a new gear motor mechanism.
View Case Study
-
Swarm robot research linear actuator
Challenging technical and unique application for swarm robotics for a European robotic research Institution.
View Case Study