AB-023
Miniature Motor Driver Resource
What Are Linear Resonance Actuators?
Welcome to our Motor Driver Resource section. Here we have suggested some chips that are suitable for driving our motors and linear resonant actuators. Please note this is a simple guide and you should always refer to the product’s datasheet for accurate ratings and design advice.
Whilst most DC motors are essentially driven by the same principle (by applying a DC voltage), these chips boast a host of different features. Some accept analogue inputs, others PWM or I2C, H-bridges will enable you to easily change the direction of rotation and haptic drivers are specially designed for haptic feedback applications. We’ve split our guide into the following categories:
- Transistors
- H-Bridges
- Vibration Motor Drivers
- Haptic Feedback Drivers
- Brushless Motor Drivers
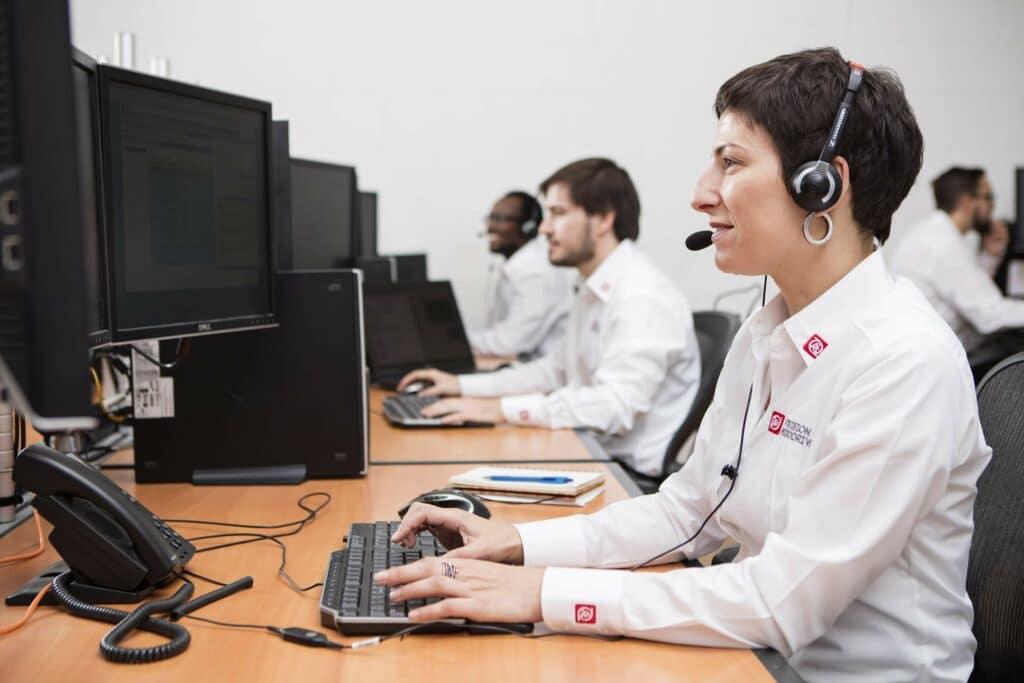
Get in touch
Speak to a member of our team.
Motor catalogue
Looking for our products?
Reliable, cost-effective miniature mechanisms and motors that meet your application demands.
Transistors
Transistors act like an electrical switch, enabling a low current or low voltage source (like a microcontroller) to drive a motor. By closing the switch the transistor can connect the motor to a suitable power supply where it has access to sufficient voltage and current. They can also be used with PWM signals to vary the level of voltage.
There are different types of transistor, here we suggest two MOSFETs; one n-channel (switch closed with high voltage at the base) and on p-channel (switch closed with low voltage at the base). Thousands of different devices exist, far too many to list here. We have previously used the ones below in-house.
Manufacturer | Product Code | Type | Output Range | Link |
---|---|---|---|---|
ON Semiconductor | MGSF1N02L | n-channel | 20 V, 750 mA | ON Semiconductor Website |
ON Semiconductor | NTR4101 | p-channel | 20 V, 3.2 A | ON Semiconductor Website |
H-Bridges
Built using 4 transistors, H-bridges enable you to easily reverse the polarity of the applied voltage to change the rotation direction. This makes them great for gearmotor applications, or anything where you might want need to rotate the motor both ways.
You can either build it yourself using the MOSFETs above with a reference circuit or purchase a single discrete chip.
There are many different types of design, including ‘half bridges’ and ‘dual H-bridges’. The chips below are all full H-bridges and a couple are ‘dual’ (can drive two motors). Again, there are many more available.
Manufacturer | Product Code | Type | Output Range | Link |
---|---|---|---|---|
STMicroelectronics | L298 | Dual Full Bridge Driver | 46 V, 4 A | STMicroelectronics Website |
STMicroelectronics | L6201 | DMOS Full Bridge Driver | 60 V, 5A | STMicroelectronics Website |
Texas Instruments | DRV8837 ( / 38 / 39) | Full Bridge Driver | 11 V, 1.8 A | TI Website |
Texas Instruments | DRV8832 ( / 30 / 33) | Full Bridge Driver | 6.8 V, 1 A | TI Website |
Texas Instruments | DRV8800 | Full Bridge Driver | 36 V, 2.8 A | TI Website |
Freescale | MC33886 | Full Bridge Driver | 40 V, 5.2 A | Freescale Website |
Allegro MicroSystems | A3908 | Full Bridge Driver | 5.5 V, 500 mA | Allegro Website |
Allegro MicroSystems | A4973 | Full Bridge Driver | 50 V, 1.5 A | Allegro Website |
Vibration Motor Driver IC
There is a small selection of components that are specifically designed to operate vibration motors with a simple on/off drive pattern. They operate in a similar method to the transistor chips above, but provide a different output voltage to the supply voltage – much like low-dropout voltage regulator (worth researching).
When using batteries, the supply voltage will vary depending upon the battery’s level of charge – when using a transistor this results in a varying performance from the vibration motor. These ICs will enable you to achieve consistent vibration motor performance across the entire battery range.
Some are fixed and some are adjustable, but most can be controlled by PWM to vary the speed.
These can, of course, be used to drive normal DC and gearmotors too as they output a DC voltage, however, some of them are specifically branded for the vibration motor market. Some users will get better performance from the H-bridges listed above or Haptic Feedback Chips, so be sure to check these other lists.
Manufacturer | Product Code | Type | Output Range | Link |
---|---|---|---|---|
ON Semiconductor | NCP5426 | TSOP-5 | 2 V, 150 mA | ON Semiconductor Website |
Maxim | MAX1749 | SOT23 | 6.5 V, 120 mA | Maxim Website |
Haptic Feedback Chips
These are the most complex chips in this section. Many of them are able to drive both eccentric rotating mass vibration motors and linear resonant actuators, have a variety of drive methods, include a range of impressive additional features and some even store haptic waveforms – all on a single component.
For top-end haptic feedback performance, you will need one of these devices along with a high-performance haptic actuator.
Manufacturer | Product Code | Type | Output Range | Link |
---|---|---|---|---|
Texas Instruments | DRV8601 | ERM / LRA | 5.5 V, 400 mA | TI Website |
Texas Instruments | DRV2603 | ERM / LRA | 5.5 V | TI Website |
Texas Instruments | DRV2604L | ERM / LRA | 5.5 V | TI Website |
Texas Instruments | DRV2605 | ERM / LRA | 5.5 V | TI Website |
Fairchild Semiconductor | FAH4820 | ERM | 3.6 V, 500 mA | Fairchild Website |
Fairchild Semiconductor | FAH4830 | ERM | 3 V, 500 mA | Fairchild Website |
Fairchild Semiconductor | FAH4840 | LRA | 2 V, 200 mA | Fairchild Website |
Brushless Motor Driver
Our brushless motors (vibration and normal) are more difficult to drive compared to the brushed DC varieties above. They are electrically commutated, which means the driver activates the different internal coils depending upon the position of the motor to maintain a constant direction of rotation. Of course, the benefit is a greatly improved lifetime as the precious metal brushes (which wear out) are removed.
All of the chips below are sensorless brushless vibration motor drivers and may require some external components, typically 3 resistors between the driver outputs and motor terminals.
Manufacturer | Product Code | Type | Output Range | Link |
---|---|---|---|---|
Texas Instruments | DRV11873 | Sensorless | 12 V, 1.5 A | TI Website |
Texas Instruments | DRV10866 | Sensorless | 5 V, 680 mA | TI Website |
NXP | TDF5140A | Sensorless | 20 V, 800 mA | NXP Website |
Newsletter
Sign up to receive new blogs, case studies and resources – directly to your inbox.

Sign up
Discover more
Resources and guides
Discover our product application notes, design guides, news and case studies.
Case studies
Explore our collection of case studies, examples of our products in a range of applications.
Precision Microdrives
Whether you need a motor component, or a fully validated and tested complex mechanism – we’re here to help. Find out more about our company.